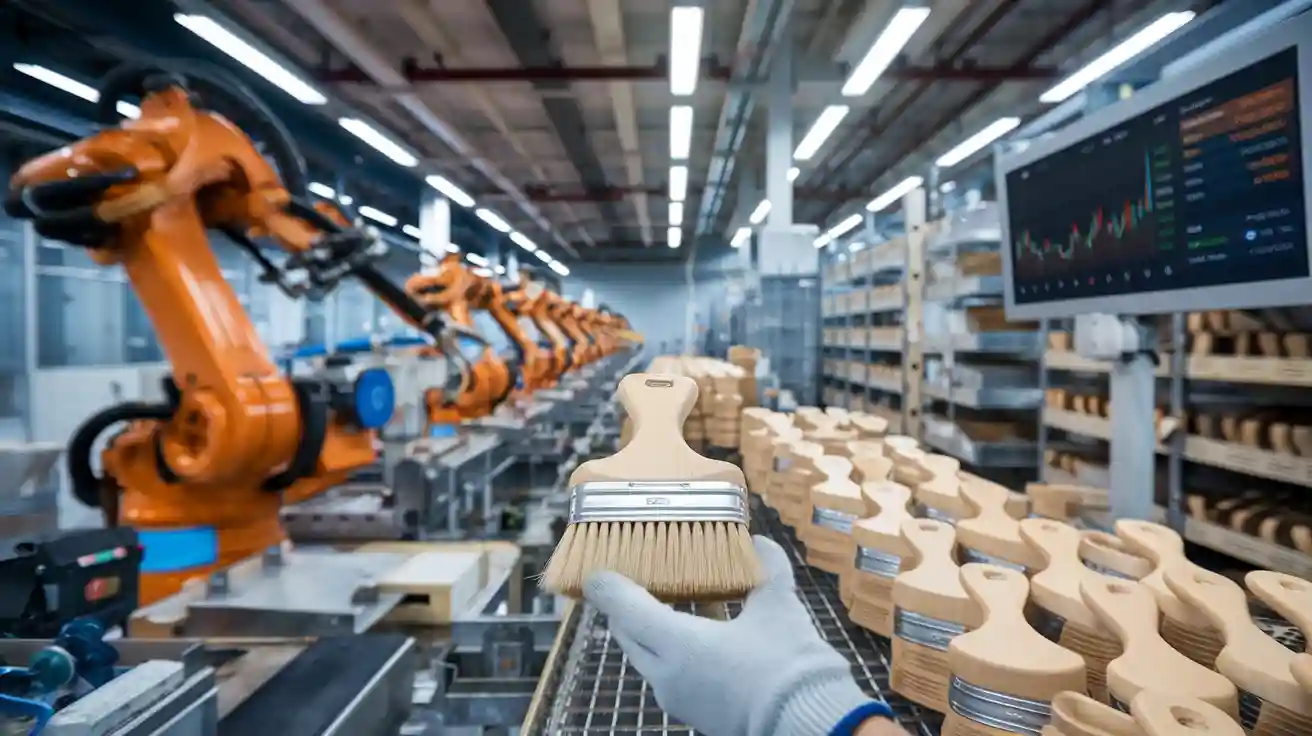
When making wooden paint brush handles, Supply Chain Management is crucial. It’s not just about moving materials from place to place; it’s about using good wood, staying eco-friendly, and working smart. However, 2025 presents new challenges to address. How can we meet growing needs while remaining green? I believe that new ideas are the solution. By improving Supply Chain Management, we can create better handles without sacrificing quality or harming the planet.
Key Takeaways
Use eco-friendly materials. Certified wood and green methods attract eco-conscious buyers.
Create good supplier relationships. Trust and talking openly improve quality and delivery times.
Use technology to work faster. Inventory tools track supplies and stop shortages.
Try Just-in-Time inventory. Order materials only when needed to cut waste and costs.
Check your supply chain often. Regular checks find problems early and keep quality high.
Current Supply Chain Challenges for Paintbrush Handle Makers
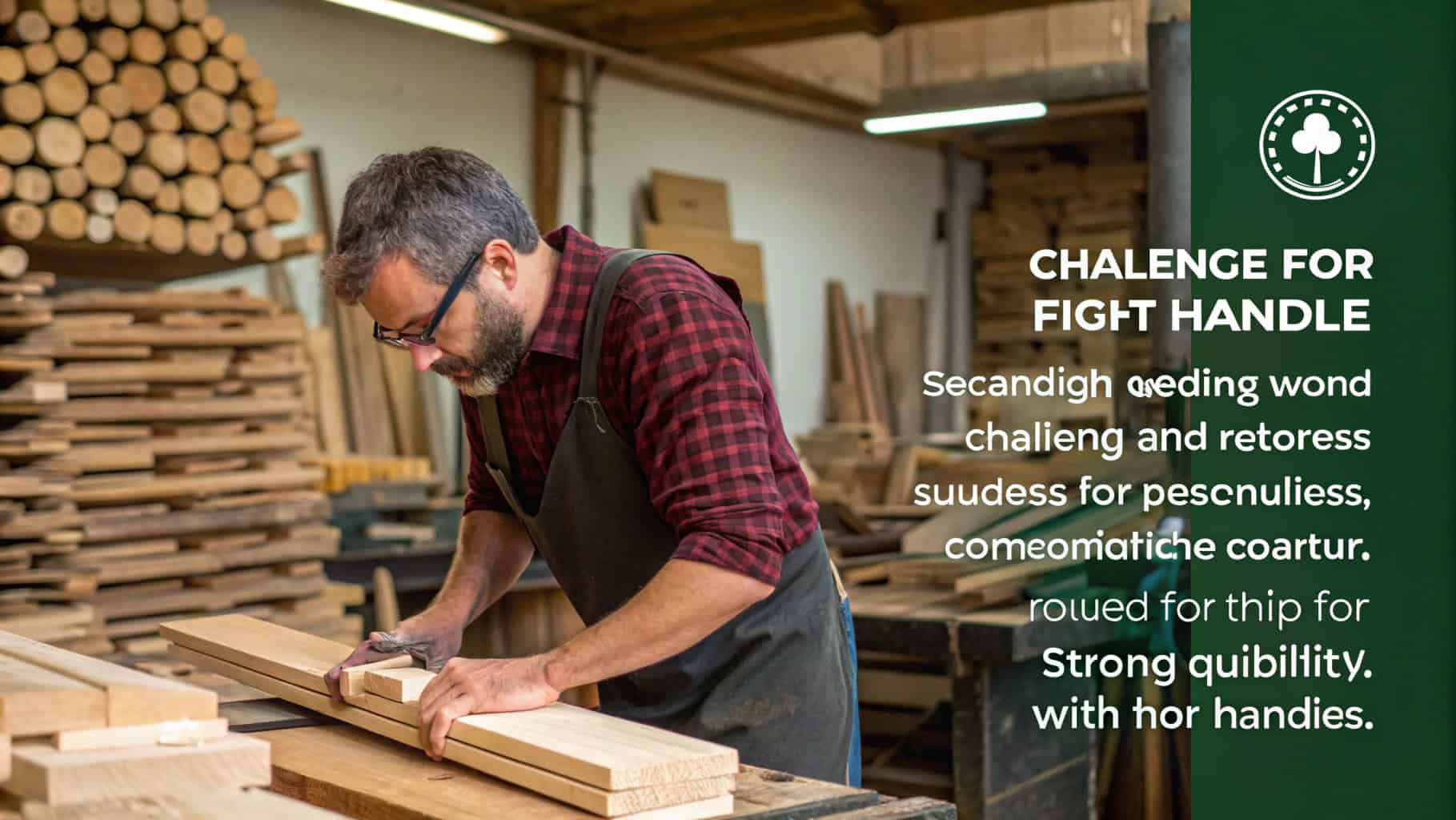
Finding Good, Eco-Friendly Wood for Handles
Getting the right wood for handles isn’t easy. Makers need wood that’s strong, light, and good for the planet. But with fewer forests and more demand, finding eco-friendly wood is tough. Suppliers often can’t keep up, causing delays or lower quality.
Supply chain numbers, like defect rates and delivery times, show these problems. For instance, a high defect rate means the wood isn’t good enough. Long delivery times can mess up schedules, making it hard to meet orders.
Keeping Production Steady
Making sure production runs smoothly is another big problem. If suppliers are late or send bad materials, everything slows down. Costs rise, and customers might get bad products.
A table of supply chain numbers can help spot issues early:
Metric | What It Means |
---|---|
Defect Rate | Shows how often products fail quality checks. |
On-Time Delivery Rate | Tracks if suppliers deliver when they promise. |
Lead Time | Measures how long materials take to arrive after ordering. |
Cost Variance | Points out unexpected cost increases in the process. |
Incident Frequency | Counts how often problems like delays or shortages happen. |
Responsiveness | Shows how quickly suppliers handle changes or questions. |
Dealing with Environmental and Rule Changes
Rules about the environment are getting stricter every year. Companies now have to cut waste and use less energy. This means they need to find better wood or cleaner ways to make handles.
Also, supply chain problems make getting materials harder. When wood runs low, companies must choose: delay work or pay more. Both choices hurt profits.
🌱 Tip: To stay ahead, work closely with suppliers and watch for new rules.
Controlling Costs and Preventing Supply Chain Disruptions
Managing costs and avoiding problems can be tricky. Even small issues can cause big trouble. But don’t worry—there are ways to handle this.
First, watch your spending carefully. Do you know where your money goes? Check every step of the supply chain for waste. For example, are shipping or storage costs too high? Cutting extra expenses can save money over time.
Next, build strong ties with suppliers. Good relationships mean they’ll care about your needs. Talking often with them can stop delays or mistakes. Also, having backup suppliers is very helpful. If your main supplier runs out of wood, a backup keeps work going.
💡 Pro Tip: Use tools like software to track your supply chain. These tools can warn you about problems early.
Being flexible is also important. If wood prices rise, try using a different type of wood. Changing how you make things can also help. Flexibility keeps costs low and avoids big problems.
Lastly, plan for surprises. Things like bad weather, shipping delays, or new rules can happen anytime. A backup plan helps you stay ready for anything.
By staying smart and prepared, you can save money and avoid problems. It’s all about being ready and able to adjust when needed.
Best Practices to Improve Paintbrush Handle Supply Chains
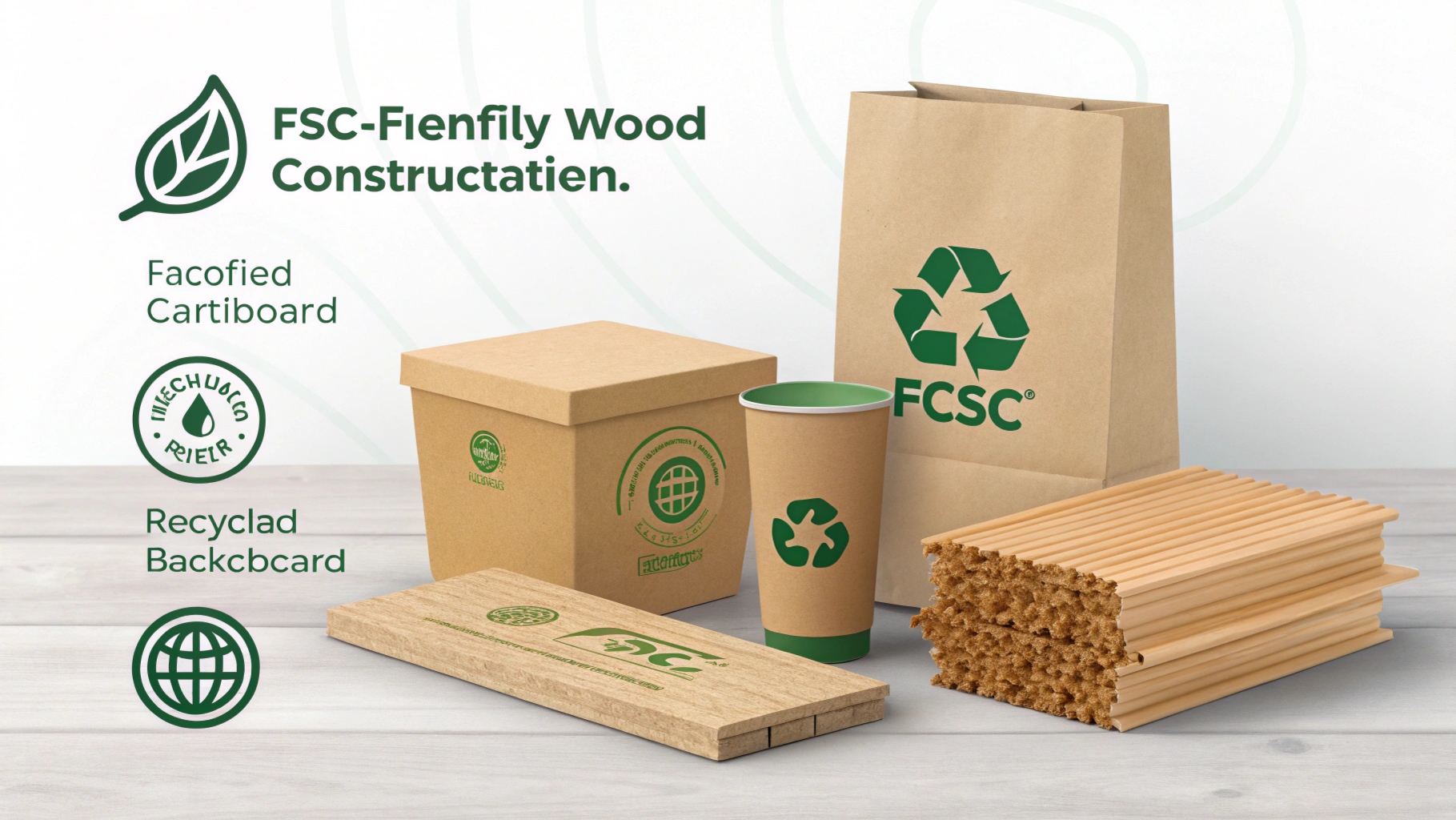
Choosing Eco-Friendly Materials and Packaging
Using eco-friendly materials is not just popular—it’s important. Picking certified wood, like FSC-certified, is strong and planet-friendly. It’s good for business and the Earth. Also, using recycled cardboard or biodegradable wraps for packaging helps a lot. Customers notice these changes and trust your brand more.
Here’s a tip: Work with suppliers who care about the planet. Ask them questions about their eco-friendly actions. Do they plant trees to replace the ones they cut? Do they reduce waste when making products? These questions help you find suppliers who value quality and the environment.
🌍 Note: Eco-friendly choices help the Earth and attract green-minded buyers.
Using Technology to Improve Inventory and Shipping
Technology makes supply chains better. Tools like inventory software track materials live. This helps avoid delays and plan better. For example, alerts can tell you when stock is low, so you’re ready.
Shipping tools are also helpful. They find faster routes, saving time and money. Imagine knowing exactly when your wood will arrive. That’s less stress, right? These tools also reduce mistakes, keeping quality high in every batch.
💡 Pro Tip: Start small. Even simple tools can improve your supply chain.
Building Stronger Supplier Relationships
Good supplier relationships lead to better results. Talking openly with suppliers is very important. Regular updates and clear needs prevent problems. When suppliers know what you want, they deliver better materials on time.
Some companies, like Orkla House Care, use advanced systems to work better with suppliers. These systems improve teamwork, leading to better products and happier customers. Investing in these tools helps businesses share ideas and improve together.
🤝 Tip: Treat suppliers like partners, not just sellers. Strong teamwork helps everyone.
Streamlining with Just-in-Time Inventory Practices
Let me tell you, Just-in-Time (JIT) inventory practices can be a game-changer for paintbrush handle manufacturers. It’s all about getting materials exactly when you need them—no earlier, no later. This approach keeps storage costs low and reduces waste. But how do you make it work? Let’s dive in.
First, you need to know your production schedule inside and out. When you understand how much wood you need and when you need it, you can order materials at just the right time. This avoids overstocking and keeps your warehouse clutter-free. Plus, it saves money. Why pay for storage space you don’t need?
💡 Tip: Use inventory management software to track your stock levels in real time. It’s like having a crystal ball for your supply chain.
Next, build strong relationships with your suppliers. When you trust your suppliers, you can rely on them to deliver materials on time. Regular communication helps them understand your needs and adjust to changes quickly. For example, if you suddenly get a big order, a good supplier can step up and deliver extra wood without delay.
Here’s another thing: JIT works best when your production process is smooth. Delays or bottlenecks can throw everything off. That’s why it’s important to keep your equipment in top shape and train your team to handle unexpected issues.
🚀 Pro Tip: Combine JIT with predictive analytics. This helps you forecast demand and plan your orders more accurately.
By adopting JIT practices, you can cut costs, reduce waste, and keep your operations running like a well-oiled machine. It’s all about working smarter, not harder. Ready to give it a try?
Innovations in Wooden Paintbrush Handle Design and Production
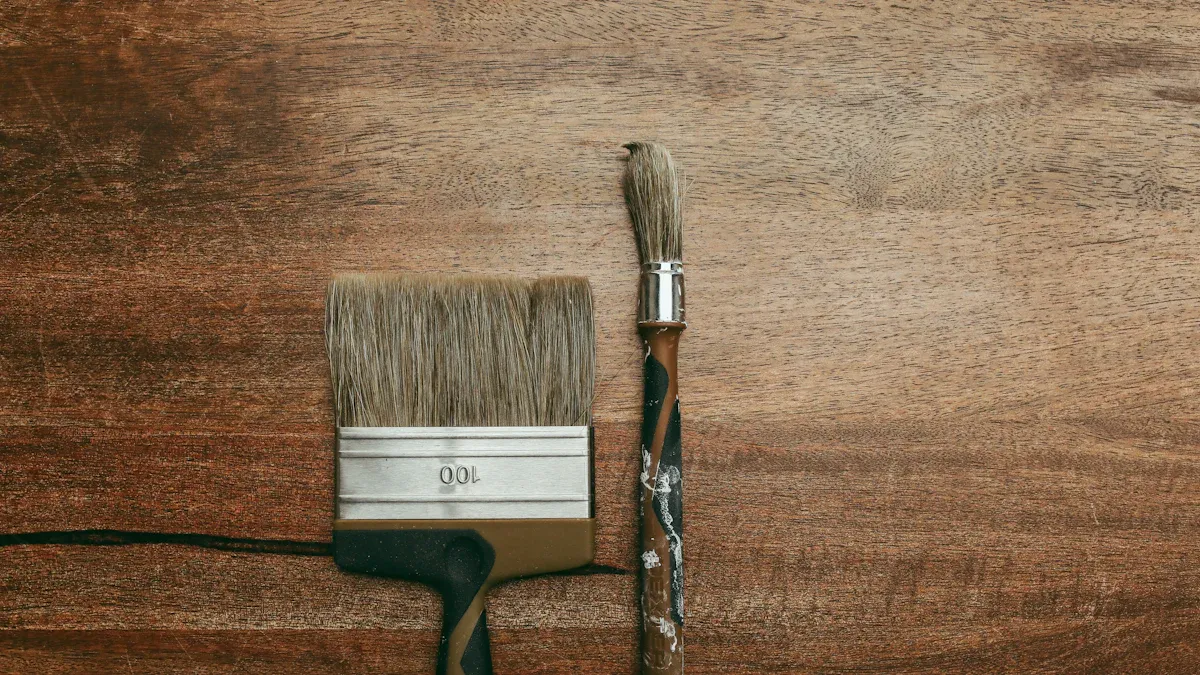
Trying Lightweight and Strong Wood Options
Have you thought about how wood type affects handles? Lightweight woods like bamboo and balsa are now popular. They are easy to hold and don’t tire your hands. Artists like them because they feel comfortable and precise. These woods are also strong, so handles last longer even with heavy use.
Manufacturers care about the environment too. Many use recycled wood or certified sustainable timber. This helps the planet and gives handles a high-quality look. Customers notice and appreciate this effort. It’s good for everyone.
Using Machines for Faster and Better Production
Automation is changing how paintbrush handles are made. Machines now cut, shape, and finish handles quickly and perfectly. This means fewer mistakes and better products. Here are some benefits:
Machines make production faster, meeting tight schedules.
They shape handles consistently, so all handles look the same.
Automation reduces waste and saves money by using materials wisely.
I’ve seen factories with automation, and it’s amazing. Everything runs smoothly and efficiently, like clockwork.
Reducing Waste with Smart Manufacturing
Waste is a big issue, but circular practices help a lot. Companies like Da Vinci recycle materials, like old boxes, for packaging. They also use local energy sources to lower pollution.
What’s great is how they handle harmful waste. They sort and dispose of it responsibly, showing care for the planet. Circular manufacturing cuts waste and makes the process cleaner. When combined with high-quality handles, it’s clear this is the future of production.
Designing Ergonomic and Stylish Paintbrush Handles
Have you ever picked up a paintbrush and thought, "Wow, this feels perfect in my hand"? That’s the magic of ergonomic design. When handles are designed to fit comfortably in your hand, painting becomes a breeze. You don’t have to deal with hand cramps or awkward grips. Instead, you can focus on creating your masterpiece.
Here’s what makes ergonomic handles so special:
They’re shaped to reduce strain on your hand and wrist.
Soft grips make them comfortable to hold, even for long painting sessions.
Lightweight materials keep your hand from getting tired too quickly.
I’ve noticed that when people use these kinds of handles, they paint longer and enjoy the process more. It’s like the brush becomes an extension of their hand. And let’s not forget about style! A sleek, modern handle doesn’t just look good—it also makes the brush stand out on the shelf. Customers love tools that feel premium and look great.
Some companies are even taking things to the next level with smart handles. These have sensors that give feedback while you paint. They can help you improve your technique or avoid hand pain. It’s a cool feature that tech-savvy painters really appreciate.
🎨 Tip: If you’re designing paintbrush handles, think about both comfort and style. A handle that feels good and looks amazing will always win over customers.
By focusing on ergonomic and stylish designs, manufacturers can create brushes that people love to use. It’s all about making painting easier, more enjoyable, and a little more fun. Who wouldn’t want that?
Actionable Steps for Paintbrush Handle Manufacturers
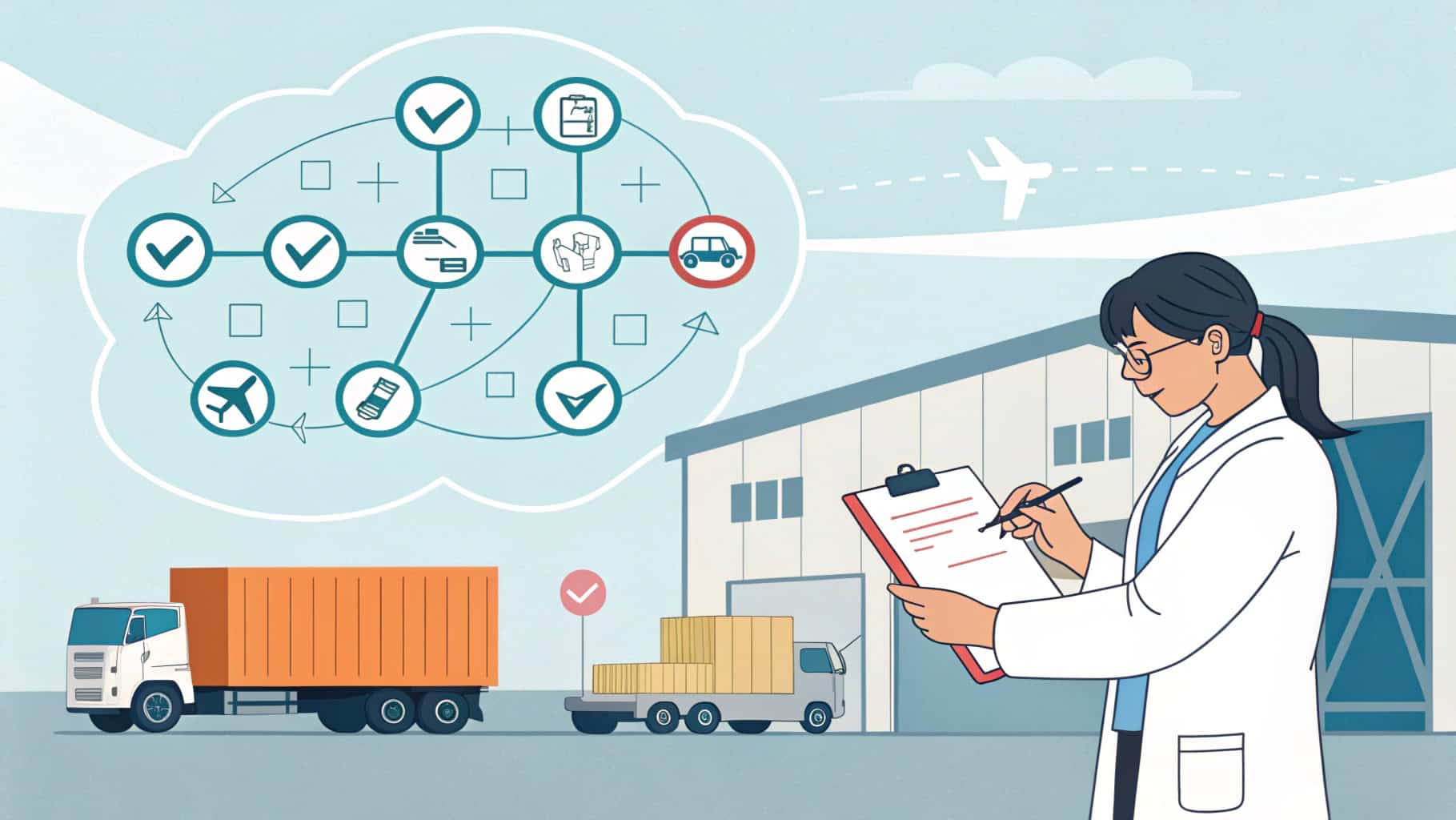
Checking Supply Chains Regularly
Think of supply chain checks like a doctor visit. They help find problems early and keep things working well. These checks aren’t just about numbers—they make sure everything is high-quality, fast, and follows rules.
Here’s what to check during audits:
Compliance Certifications: Make sure suppliers follow safety and quality rules.
Operational Capacity: See if suppliers can handle orders on time.
Performance Optimization: Watch numbers like delivery times and product accuracy.
This table shows how certifications help:
Certification Type | What It Ensures |
---|---|
Proves suppliers follow strict quality systems. | |
Retail Certification Programs | Shows they meet store rules and lower audit costs. |
Check your supply chain every three months. For example, aim for a 98.5% on-time delivery rate to stay efficient. Also, try to waste less—keeping scrap rates under 3% saves money and helps the planet.
🛠️ Tip: Audits build trust with suppliers. They’ll focus more on quality when they know you care.
Teaching Suppliers for Better Results
Training suppliers is a smart way to improve work. When they know what you need, they make fewer mistakes. I’ve seen how training makes everything better.
Focus on these areas:
Regular Training: Teach new skills often to keep everyone sharp.
Cross-Training: Show workers different tasks for more flexibility.
Lean Manufacturing: Help suppliers cut waste and stay efficient.
Numbers like delivery times and defect rates show how training helps. For example, tracking lead time changes shows if deliveries are steady. Here’s a quick guide:
Metric | What It Means |
---|---|
Tracks how often orders arrive on time. | |
Defect Rate | Shows the percentage of bad items received. |
Supplier Corrective Action Rate | Counts how often suppliers fix material problems. |
📈 Pro Tip: Work with suppliers to create training plans. When they feel supported, they’ll try harder to meet your needs.
Using Data to Predict Needs
Using data tools can help you plan better. These tools look at past orders to predict future needs. I’ve found this helps avoid running out of materials or having too much.
For example, predictive tools can tell you how much wood to order. This keeps your stock just right—no waste or shortages. It also ensures materials are fresh, helping paint stick better.
These tools also help control costs. They show wood price trends so you can budget better. Plus, they help match your stock to what customers want.
🔮 Note: Start small with data tools. Even simple ones can improve your supply chain.
By combining audits, training, and data tools, you can build a supply chain that’s strong, reliable, and ready for anything.
Making Supply Chains Eco-Friendly
Being eco-friendly is no longer optional—it’s a must. Helping the planet also helps your business grow. But how can you make your supply chain greener? Let’s break it into simple steps.
First, find out what’s causing waste or harm. Are there parts of your process that hurt the environment? Fixing these problems can save money and improve your company’s image. Start by setting clear eco-friendly goals. Knowing your purpose makes it easier to stick to changes.
Next, talk with your suppliers and partners. They need to understand your goals and work with you. For example, if you want to use FSC-certified wood, explain why it’s important. Show them how they can help you reach this goal.
Setting goals and deadlines is also very important. Think of it like planning a trip. You need to know where you’re going and how to get there. Clear goals make the process easier. Tracking progress keeps everyone focused and excited.
Here’s a simple checklist to follow:
Decide your eco-friendly goals.
Work with suppliers and partners.
Create clear goals and deadlines.
Review and update your plans often.
Share new ideas with your team.
Some companies go further by creating rules for suppliers. They check if suppliers follow these rules through audits. This builds trust and ensures everyone is doing their part.
Making your supply chain eco-friendly helps the planet and your business. 🌱 It’s a smart choice with many benefits.
Key Trends Shaping Wooden Paintbrush Handle Manufacturing in 2025
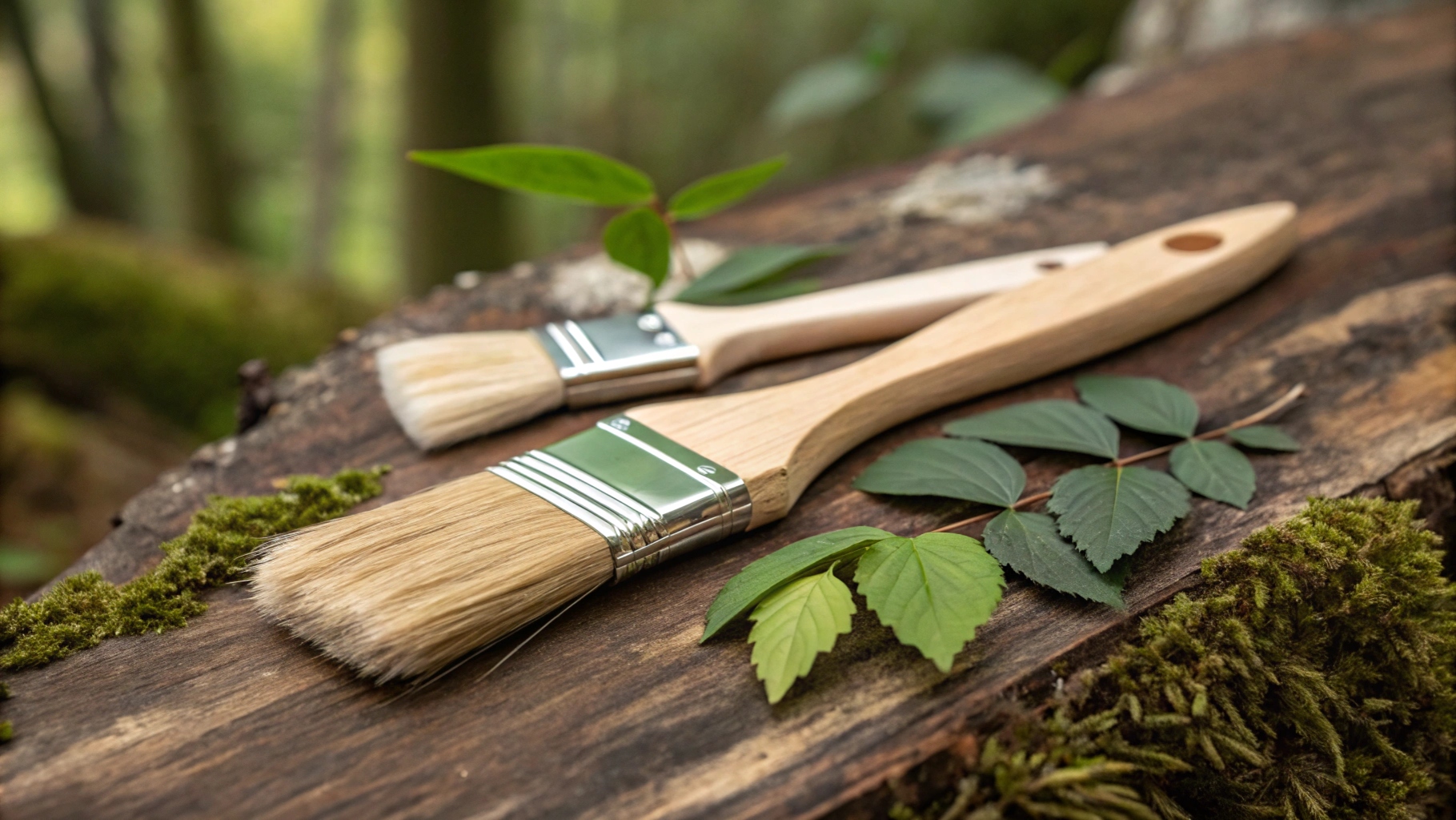
Growing Need for Eco-Friendly Paintbrush Handles
Have you noticed people care more about the planet now? Eco-friendly products are not just popular—they’re important. Wooden paintbrush handles are a great choice. They’re natural, recyclable, and good for the Earth. This change isn’t just about feeling good; it’s about being smart.
The demand for eco-friendly handles is rising quickly. More buyers want brushes with biodegradable bristles and recyclable handles. This connects to the global push for saving the environment. Many manufacturers say customers care about how products are made. They want tools that don’t harm nature.
If you make paintbrushes, now is the time to go green. Use certified wood and eco-friendly finishes to stand out. Customers notice these efforts and will choose your brushes over others.
How Global Wood Prices Affect Costs
Let’s talk about wood prices—they can change a lot. This makes it hard for paintbrush makers to keep costs steady. But there are ways to handle this challenge.
Some companies solve this by using different wood suppliers. Instead of depending on one, they work with many. This helps avoid sudden price jumps. Others switch to cheaper woods like bamboo, which are still strong and durable.
Technology can also help. Tools that predict price changes let you plan ahead. Staying flexible is important. If one wood type gets too pricey, you can switch to another without slowing production.
Meeting Customization Demands from Paintbrush Brands
In 2025, brands want unique paintbrush handles. They ask for special shapes, colors, or finishes to match their style.
I’ve seen companies succeed by saying yes to these requests. They use advanced machines to make custom designs fast. This keeps brands happy and builds trust.
It’s not just about looks, though. Brands also want handles that make painting easier. Lightweight and ergonomic designs are very popular. When you offer these features, you’re solving problems, not just selling brushes.
To adapt, start by asking your clients what they need. Find ways to deliver what they want. Customization isn’t just a trend—it’s a chance to grow your business.
Using Smart Materials for Better Paintbrush Handles
Have you ever wondered if technology could improve paintbrush handles? Smart materials can make this possible. They are not just cool—they solve real problems for users and makers.
Smart materials, like shape-memory metals or heat-sensitive plastics, are amazing. Imagine a handle that changes to fit your hand while painting. Sounds awesome, right? This makes painting easier and less tiring. It feels like the brush is helping you.
Another great idea is water-resistant coatings. Wooden handles often soak up water, causing cracks or swelling. Smart coatings protect the wood, even in wet weather. This means brushes last longer, making customers happy.
💡 Fun Fact: Some smart materials change color with heat. This could make paintbrushes fun and interactive!
For makers, smart materials save time and money. They cut waste during production. For example, self-healing materials fix small scratches by themselves. This means fewer broken handles and lower costs.
Here’s how smart materials can improve paintbrush handles:
Comfort: Handles that fit your hand perfectly.
Strength: Coatings that stop water damage.
Style: Finishes that change color or texture.
Eco-Friendly: Less waste during production.
Using smart materials isn’t just a new idea—it’s the future. These materials make brushes better, stronger, and greener. If you make paintbrush handles, now is the time to try them. Who wouldn’t want to create the next big thing in painting tools?
Building a Strong Supply Chain for Paintbrush Handles
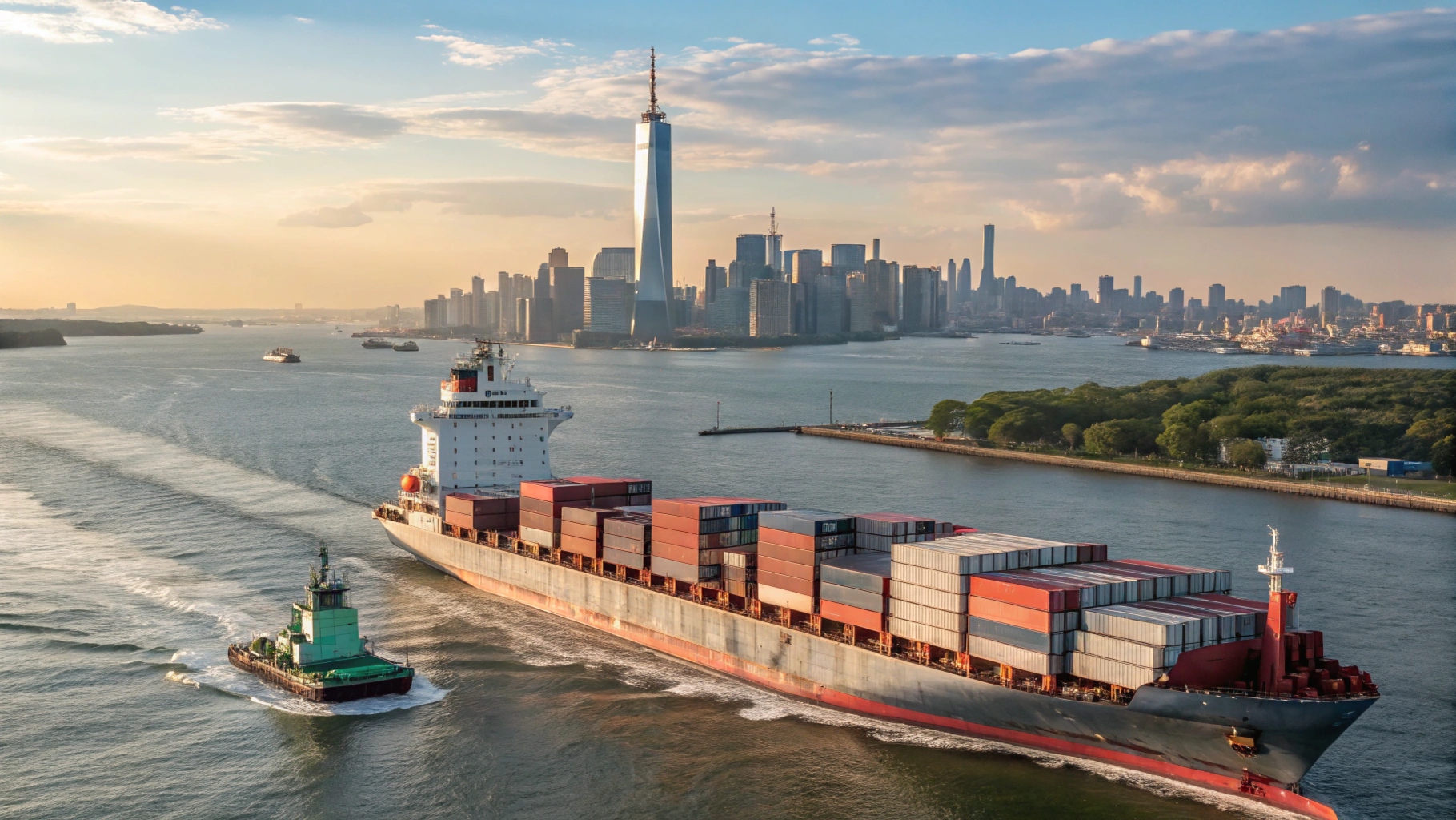
Getting Ready for Shipping Problems
Shipping delays can mess up your plans. Even small delays can cause big problems. That’s why it’s smart to prepare for them.
You can track shipments with GPS or software. These tools show where your materials are. This helps you plan better and avoid surprises. Another idea is to work with more than one shipping company. If one has delays, another can step in.
🚢 Pro Tip: Keep extra materials in stock. A small backup can help when shipments are late.
Stay informed about global news. Things like storms or strikes can slow shipping. Knowing early gives you time to change your plans.
Using Many Wood Suppliers for Safety
Depending on one supplier is risky. If they run out of wood or raise prices, you’re stuck. It’s better to work with several suppliers. This spreads the risk and keeps things steady.
Find suppliers in different places. If one area has a shortage, another might not. Use both local and international suppliers. Local ones are faster, and international ones might cost less.
🌍 Note: Good relationships with suppliers mean they’ll help you first during tough times.
Planning Ahead for Material Shortages
Sometimes, materials run out. Having a plan makes it easier to handle. Start by finding other materials you can use. For example, if your usual wood isn’t available, could bamboo work instead?
Make a list of backup suppliers. Keep their contact info ready so you can call them quickly. It’s also smart to store a little extra material. This gives you time to find a solution.
🛠️ Tip: Test new materials before you need them. This way, you know they’re good enough.
By planning ahead, you can keep making products even when problems happen.
Building Strong Local Supplier Connections
Making your supply chain stronger is easier with local suppliers. Nearby suppliers help you save time and support your community. Meeting them in person builds trust and solves problems faster. Let’s see why this works and how to do it well.
First, using local suppliers lowers shipping costs. Short trips mean fewer delays and less fuel use. This also helps the environment 🌍. Many businesses save lots of money by choosing local suppliers.
Another benefit is better communication. When suppliers are close, you can visit them or invite them over. This helps you find and fix problems quickly. For example, if wood isn’t good enough, you can sort it out fast without waiting weeks.
💡 Tip: Meet your local suppliers often. Even a short chat can build trust.
To make these connections stronger, focus on three things:
Honesty: Share your needs and challenges with suppliers. This helps them provide better materials.
Fair Pay: Pay suppliers fairly so they prioritize your orders.
Teamwork: Work together on green projects like planting trees or cutting waste.
Using local suppliers doesn’t just improve your supply chain—it helps your community too. It’s a smart choice that benefits everyone. Why not start today? 😊
How Wooden Handles Make Paintbrushes More Competitive
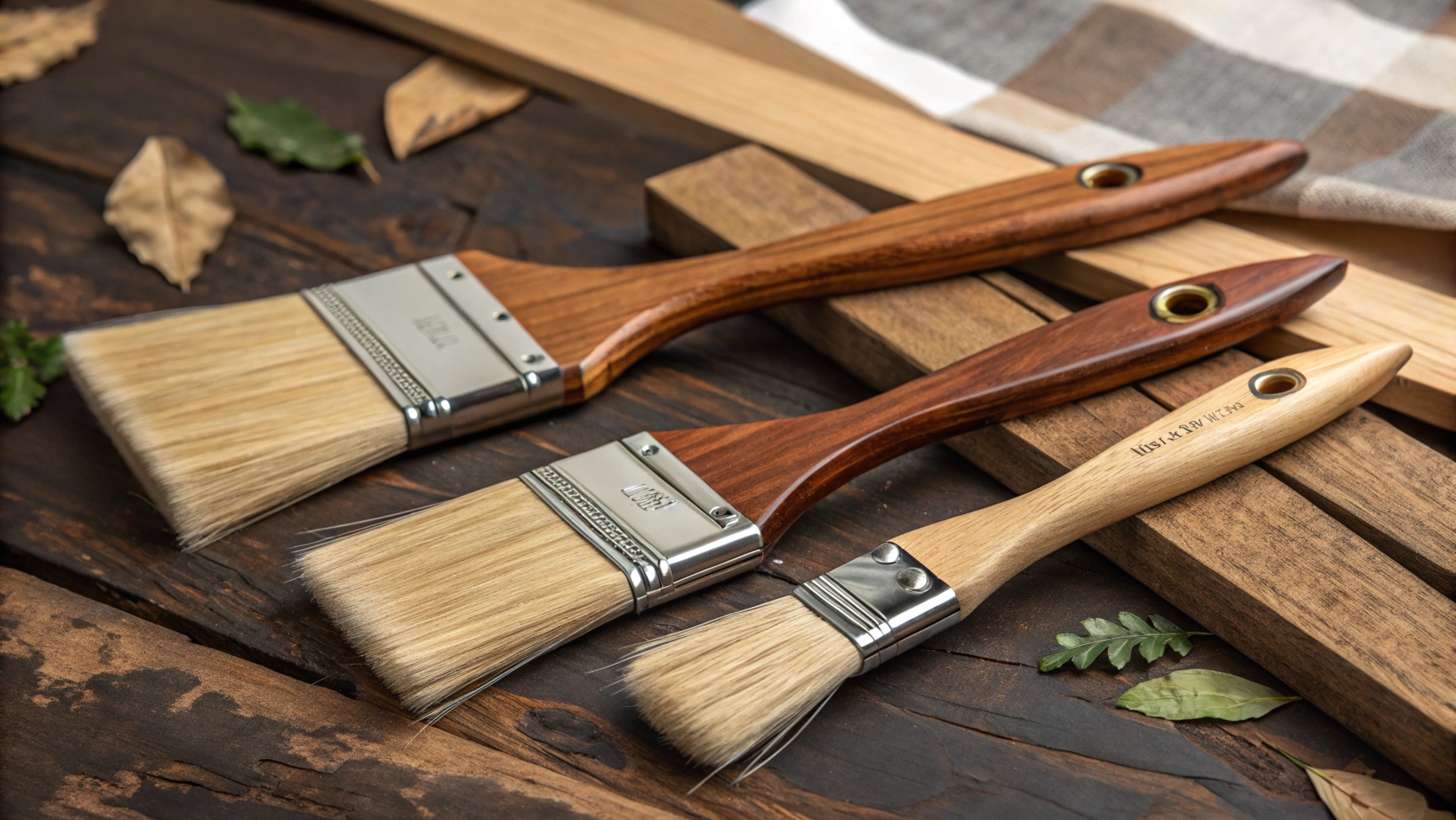
Standing Out with High-Quality Wood Finishes
Premium wood finishes make paintbrushes look and feel special. Smooth, shiny handles seem professional and high-end. People really like that. But it’s not just about looks. A good finish also protects the wood, helping it last longer. This is great for users and better for the planet.
More people now care about the quality of wooden handles. This is because they’re learning how to take care of wood. Also, the growing construction industry needs tools that last. By using top-quality finishes, companies can attract buyers who want stylish and durable brushes.
Making Brushes Strong and Comfortable
Strong handles are super important for painters. Nobody wants a handle that breaks or wears out fast. Well-made wooden handles can handle tough jobs and last for years. They give painters confidence to work on any project.
Comfort matters too. A handle that feels nice makes painting easier and more fun. Lightweight wooden handles with comfy designs stop hands from getting tired. This mix of strength and comfort keeps people coming back. It’s all about making brushes people trust and love.
Showing Care for the Planet with Wood Choices
Caring for the planet is more than just talk. Picking the right wood shows brands care about the Earth. Some companies use FSC-certified wood to prove they’re serious about being green. This helps forests and builds trust with eco-friendly buyers.
Using sustainable wood matches the rising demand for green products. When brands share their eco-friendly choices, they attract people who want tools that last without hurting nature. It’s a smart way to stay ahead while helping the planet.
Balancing Cost and Quality for Market Advantage
Finding the right balance between cost and quality is tricky. If you cut costs too much, quality drops. But focusing only on quality can make products too pricey. So, how can you balance both? Let’s explore some simple ideas.
First, know your materials well. Good wood doesn’t have to cost a lot. For example, bamboo or reclaimed wood is strong and affordable. These options save money and attract eco-friendly buyers.
💡 Tip: Talk to suppliers about cheaper materials with good quality. You might find great options you didn’t know about.
Next, improve how you make your products. Better production methods reduce waste and save money. For example, using machines for repetitive tasks makes work faster and more consistent. This way, you can make more handles without lowering quality.
Another idea is to offer different product levels. Not everyone needs a fancy paintbrush handle. Create basic, mid-range, and premium options to fit different budgets. This way, you can sell to more people while keeping your brand strong.
Here’s how product levels can look:
Product Level | Features | Price Range |
---|---|---|
Basic | Simple but durable design | Low |
Mid-Range | Comfortable and stylish | Medium |
Premium | Top-quality wood, fancy finish | High |
Lastly, listen to what your customers say. Their opinions help you decide where to save money and where to focus on quality. When you balance both well, you save money and earn customer trust. That’s a win for everyone!
Making supply chains better for wooden paintbrush handles isn’t just fixing problems—it’s finding new chances to grow. Facing challenges directly helps things run smoothly, improves products, and makes customers happy. Using eco-friendly methods and smart tools can really help.
🌟 Tip: Even small changes now can lead to big success later.
Let’s stay ahead by trying new ideas and planning wisely. The paintbrush business is changing, and with the right moves, we can make 2025 greener, smarter, and more efficient. Are you ready to start?
FAQ
Why is FSC-certified wood good for paintbrush handles?
FSC-certified wood comes from forests managed responsibly. It helps protect nature and supports eco-friendly practices. Customers like brands that use certified wood because it shows care for the planet. It also helps you stay green while keeping quality high.
🌱 Tip: Always check if your supplier has FSC certification for proof.
How can I cut down waste when making paintbrush handles?
Check your production steps for wasted materials, like scraps or packaging. Try recycling leftover wood or reusing scraps in new ways. Using machines can also help by making fewer mistakes and saving materials.
♻️ Pro Tip: Work with local recycling groups to handle extra materials properly.
What should I do if there’s not enough wood?
Work with more than one supplier to lower risks. Keep a list of backup suppliers and try other materials like bamboo or recycled wood. Store a small amount of extra wood for emergencies. Planning ahead keeps your work running smoothly.
🛠️ Note: Check how well your suppliers are doing to avoid problems.
Why are ergonomic paintbrush handles important?
Ergonomic handles make painting easier and more comfortable. They fit your hand naturally, so your hand doesn’t get tired. People love tools that feel good to use, which makes them happy and loyal to your brand.
🎨 Fun Fact: Ergonomic handles can also help artists paint more precisely.
How can technology help my supply chain?
Technology helps track inventory, shipments, and future needs. Tools like inventory software stop you from running out of materials or having too much. Shipping tools find faster routes, saving time and money. These tools make your supply chain better and easier to manage.
💡 Tip: Start with basic tools and add more as your business grows.