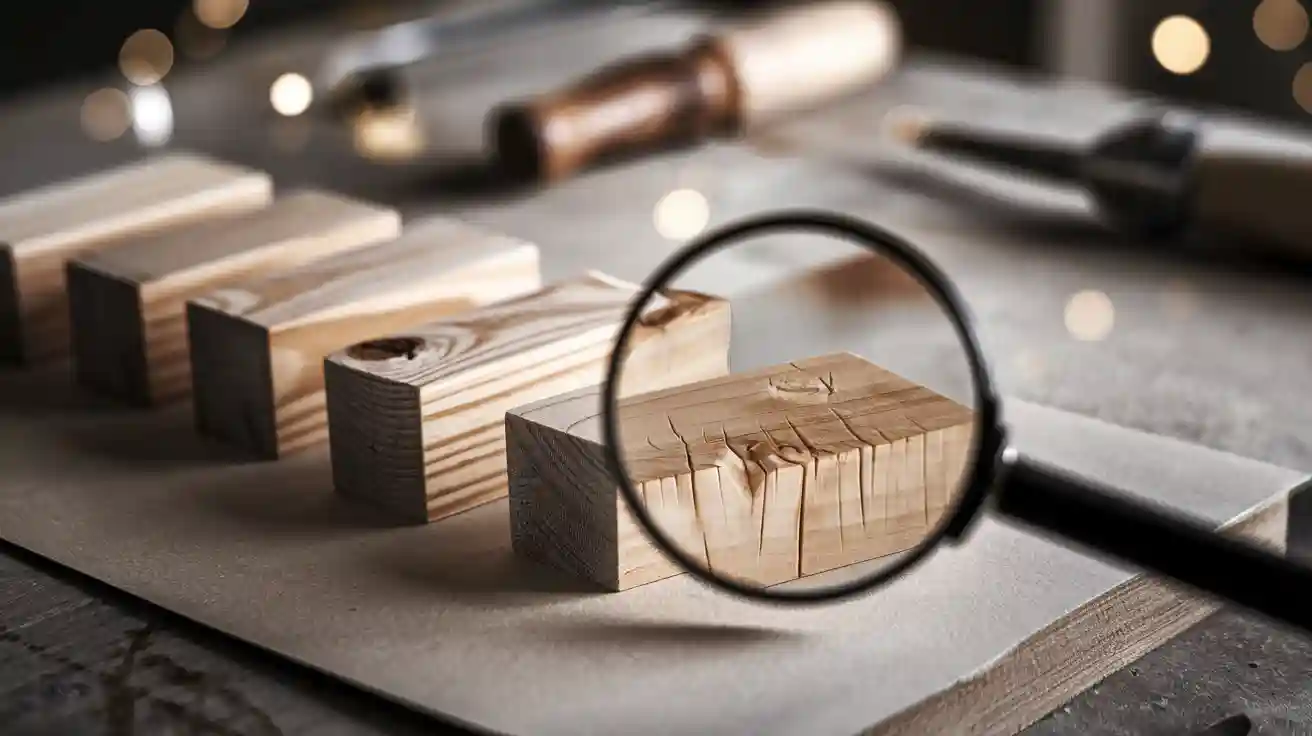
Have you ever wondered why it’s so important to recognize quality defects in wood blocks? Let me tell you—it’s not just about looks. Defects can weaken a block, making it unsafe and less durable. They can ruin a project, whether it’s a sturdy board for construction or a decorative piece. But when you identify a good wood board block, you’re setting yourself up for success. Good quality wood lasts longer, handles stress better, and gives you peace of mind. It’s all about knowing what to look for and making the right choice.
Key Takeaways
Look at and feel wood to spot flaws like cracks or bumps.
Use tools like moisture meters to check wood's water levels. Keep it at the right level for strength and stability.
Use machines to find defects faster and more accurately.
Try advanced tools like AI or sound waves to check wood better.
Create a scorecard to rate and pick good wood suppliers.
10 Ways to Spot Defects in Wood Blocks
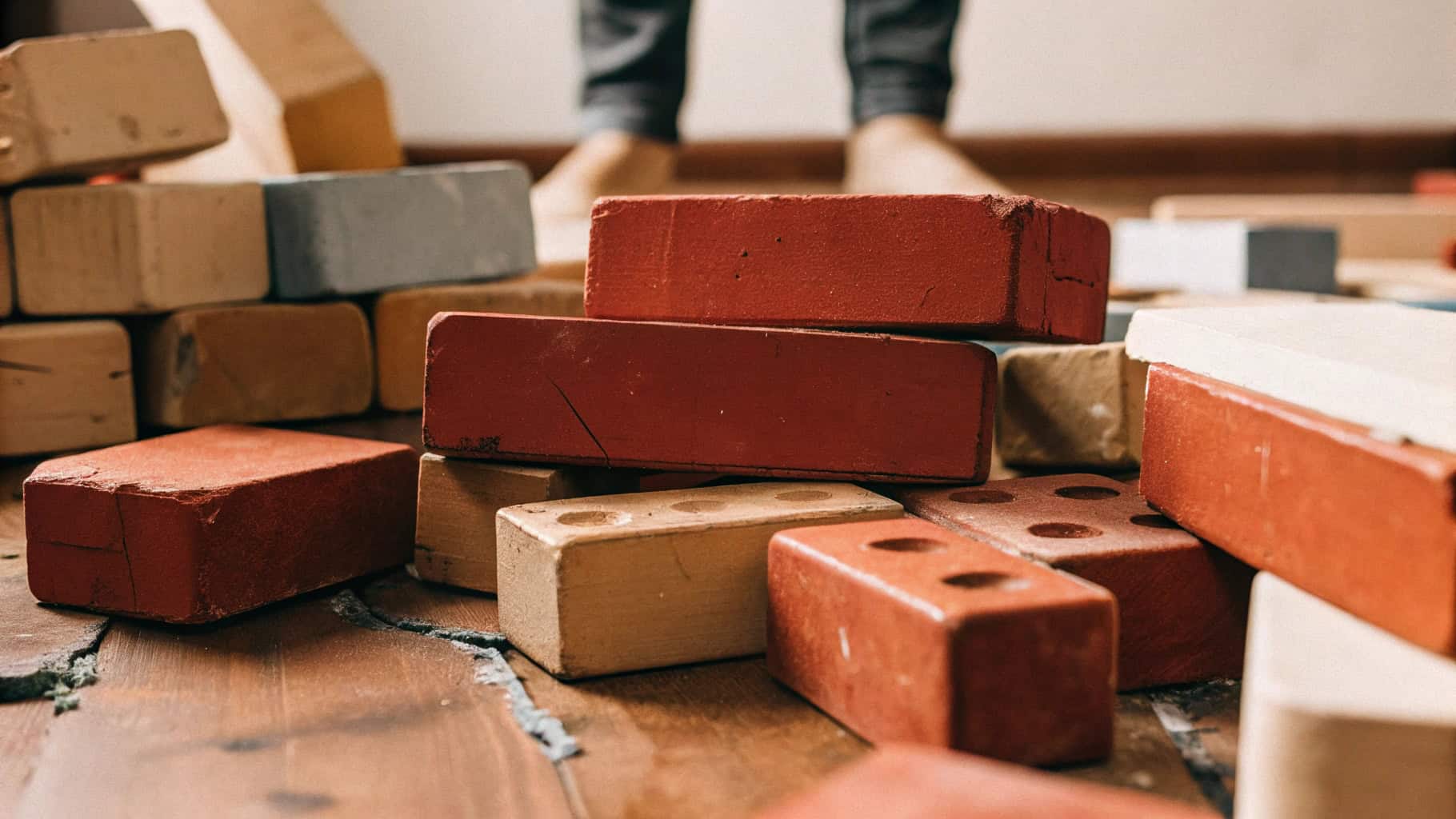
Simple Steps to Check Wood Surfaces
When I check a wood block, I start by looking at its surface. Checking with your eyes is the easiest way to find problems. I also feel the edges for damage or rough spots. Running your hand over the wood helps find bumps or uneven areas you might not see. Small flaws like these can cause big issues later, especially in building projects.
Another thing to watch for is strange colors or patterns. These might mean the wood is cracking or starting to rot. A quick look can stop you from using bad wood that could ruin your project.
How to Find Knots and Cracks in Wood
Knots and cracks are common problems in wood, but they make it weaker. Checking raw wood before using it is very important. Knots may seem fine, but big or badly placed ones can cause trouble. Cracks show the wood has been stressed and might break.
To find these issues, hold the wood up to the light. This helps you see cracks better. You can also tap the wood lightly and listen. A dull sound might mean there’s a crack or empty space inside.
Using Lasers to Check Veneer Quality
For thin wood sheets, laser tools are very helpful. These tools find flaws that are hard to see with your eyes. Studies show that deep learning methods, like U-NET, make it easier to check veneer for problems.
In the past, people used dye and microscopes to check veneer, which took a lot of time. New tools, like SMOF, give clear pictures of veneer edges, making checks faster and more accurate.
If you work with veneer, laser tools can save time and improve quality.
Automated Warping Measurement Systems Implementation
Have you ever seen a wood block that isn’t straight? That’s called warping, and it can mess up projects. Automated warping measurement systems help find these problems early. They use smart tools to spot small bends or twists in wood. Let me tell you how they work and why they’re helpful.
These systems use cameras and sensors to scan the wood. They make a 3D model showing where the wood is bent. This is much better than just looking at it yourself. These tools save time and cut down on waste. You don’t need to check each piece by hand anymore.
Here’s why these systems are great:
Speed: They check hundreds of blocks in just minutes.
Accuracy: They find tiny flaws you might not see.
Efficiency: They sort out bad pieces before the next step.
Tip: For big projects, these systems save money over time. They stop warped wood from causing expensive fixes later.
Some systems even predict how wood might warp in the future. Isn’t that cool? This helps you pick the strongest wood for tough jobs. If you care about quality, these systems are a smart choice. They make everything easier and more dependable.
Structural Integrity Verification for Commercial Lumber
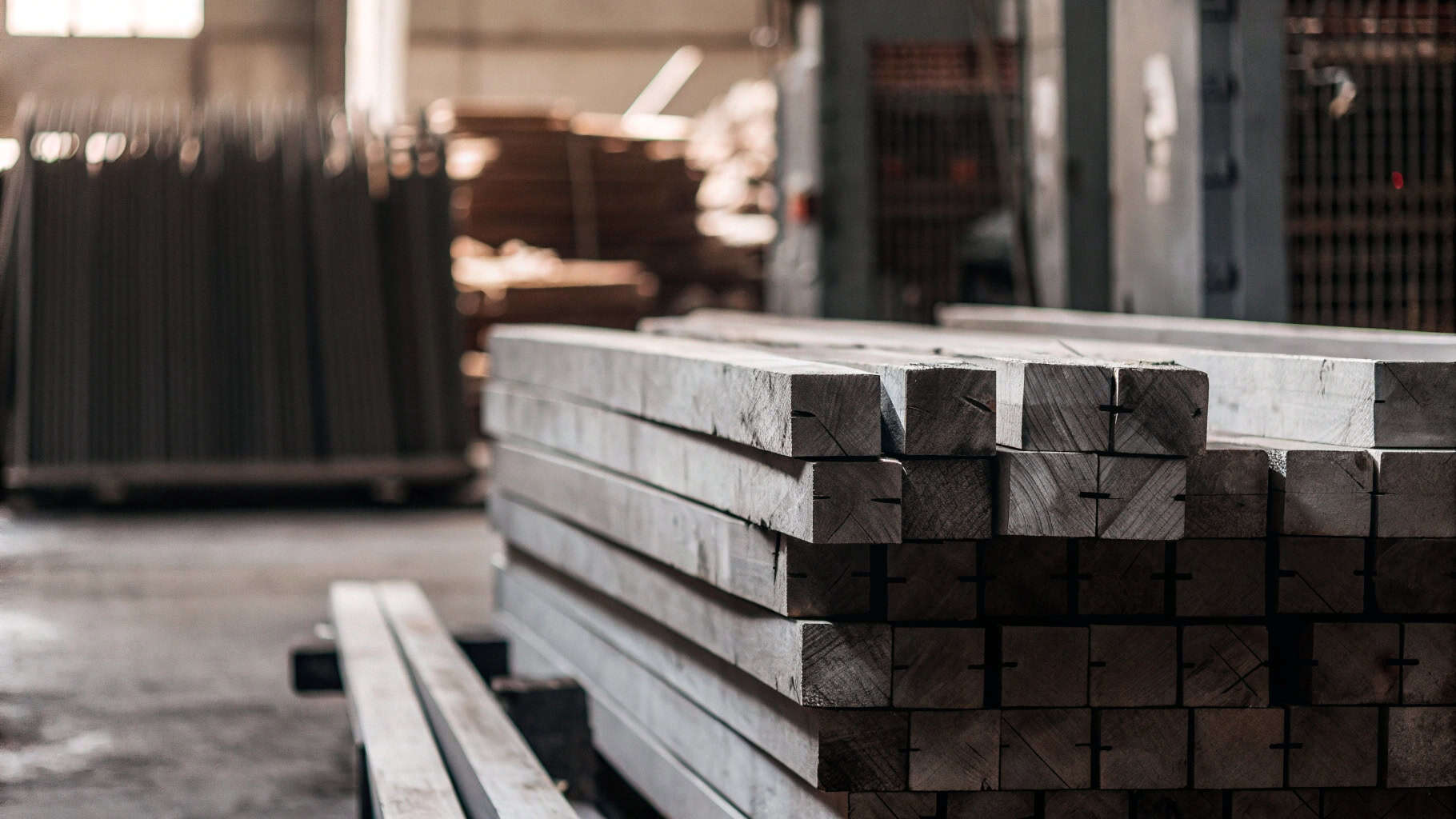
3D Scanning for Warp/Twist Deformation Analysis
When I work with lumber, one of the first things I check is whether the boards are straight. Warping and twisting are common movement defects that can ruin a project. That’s where 3D scanning comes in handy. This technology creates a detailed map of the wood’s surface, showing even the smallest bends or twists. It’s like having X-ray vision for your boards!
I’ve found that 3D scanning is super accurate. It catches defects that I might miss with just my eyes. Plus, it’s fast. You can scan multiple boards in minutes, saving time and effort. If you’re serious about quality, this tool is a game-changer.
Ultrasonic Testing for Internal Crack Detection
Have you ever wondered if a piece of wood has hidden cracks? I know I have. That’s why I love ultrasonic testing. This method sends sound waves through the wood to detect internal defects. If there’s a crack, the sound waves bounce back differently, revealing the problem.
This technique is especially useful for commercial lumber. It ensures the wood is strong and safe to use. I’ve seen it catch issues that would’ve gone unnoticed otherwise. It’s like giving the wood a health check-up before using it.
Load-Bearing Capacity Simulation Techniques
Not all wood is created equal. Some boards can handle more weight than others. That’s why I use load-bearing capacity simulations. These tests show how much stress a piece of wood can take before it breaks. It’s a great way to ensure safety, especially for construction projects.
The simulation mimics real-world conditions, like heavy loads or pressure. It helps me pick the right wood for the job. Knowing the limits of each board gives me peace of mind and keeps my projects safe and sturdy.
Moisture Content Impact on Structural Stability
When I work with wood, one of the first things I check is its moisture content. Why? Because moisture can make or break a project—literally! Wood is like a sponge. It absorbs and releases water depending on the environment. This constant movement can cause big problems if you’re not careful.
Here’s what happens when moisture levels are off:
Too much moisture: The wood swells, becomes soft, and loses strength. It might even start to rot.
Too little moisture: The wood shrinks, cracks, or warps. This weakens its structure and makes it unreliable.
I always aim for a balance. The ideal moisture content depends on where the wood will be used. For indoor projects, I look for wood with 6-8% moisture. Outdoor wood can handle a bit more, around 10-12%.
Tip: Use a moisture meter to check the wood before starting your project. It’s a small tool, but it saves you from big headaches later.
Moisture doesn’t just affect the wood itself. It also impacts how the wood interacts with other materials. For example, if you’re building furniture, wood with high moisture might loosen screws or glue joints over time. That’s why I always double-check before assembly.
Here’s a quick table to help you understand the effects of moisture:
Moisture Level (%) | Common Issues | Best Use Cases |
---|---|---|
Below 6% | Cracking, brittleness | Dry climates, indoor use |
6-12% | Stable, minimal movement | Most projects |
Above 12% | Swelling, rot, instability | Outdoor use (treated) |
Keeping moisture in check is key to strong, long-lasting wood. Trust me, it’s worth the extra effort!
Acoustic Quality Control Solutions for Wood Products
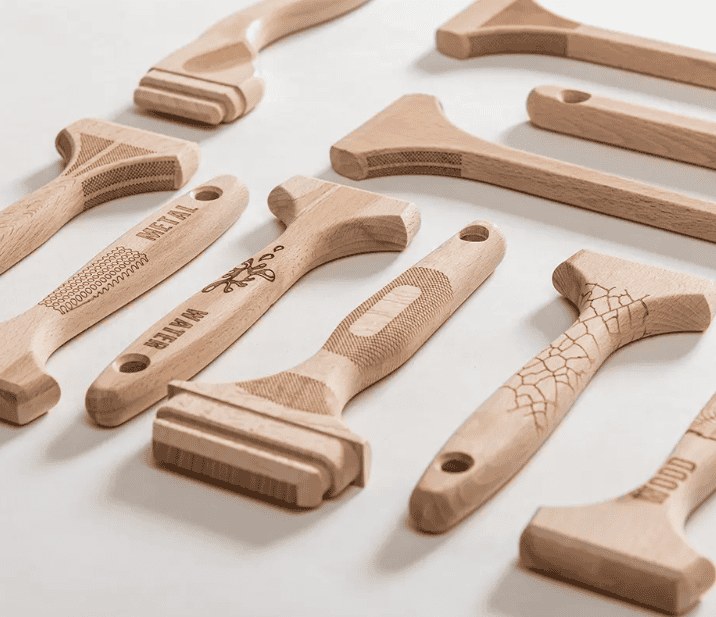
AI-Powered Knock Test Analysis Systems
Have you ever tapped on wood to hear its sound? I do this often to find hidden problems. Now, AI-powered knock test systems make this even better. These systems listen to the sound when you tap the wood. They can find cracks or empty spaces you might not notice.
Here’s how they work: The system records the sound and checks it against a database. If the sound is different from solid wood, it flags an issue. It’s like having a smart helper to find defects. This is great for checking many wood pieces quickly and correctly.
Sound Frequency Pattern Recognition Technology
Sound can tell you a lot about wood. With special tools, you can understand it better. Sound frequency pattern recognition finds weak spots in wood by studying vibrations. When I use this, I can locate cracks or uneven areas.
This works by sending sound waves through the wood and measuring them. Different sounds show different problems. For example, a sudden change might mean a crack or knot. It’s amazing how much sound can reveal!
Internal Void Detection Through Resonance Testing
Resonance testing is a simple way to find hidden voids in wood. I use this to check for empty spaces that weaken boards. You tap the wood and listen to the sound it makes. A hollow or strange sound often means there’s a problem inside.
What’s cool about resonance testing is how easy it is. You don’t need fancy tools—just practice and a good ear. Advanced tools can make it even better. They measure sound waves and give detailed results. This helps you choose the best wood for your project.
Tip: Use these sound tests with visual checks for the best results. Together, they show the full quality of the wood.
Portable Acoustic Inspection Device Applications
When I began working with wood, I used simple tools to find flaws. But portable acoustic inspection devices have made this much easier. These small gadgets are light, easy to use, and great at spotting hidden problems in wood. Let me explain how they work and why I like them.
These devices send sound waves into the wood to find cracks, voids, or weak areas. You place the device on the wood, and it sends a sound signal. The device checks how the sound moves through the wood. If there’s an issue, like a crack inside, the sound changes, and the device alerts you. It’s like carrying a tiny lab in your hand!
Here’s why they’re so helpful:
Portability: You can bring them anywhere, like job sites or workshops.
Ease of Use: No special skills are needed. Just follow the steps.
Accuracy: They find even tiny flaws you might miss by looking.
Tip: Combine these devices with visual checks for the best results. Together, they show the full quality of the wood.
I’ve used these devices to check everything from raw wood to finished furniture. They save time and make inspections easier. If you work with wood, getting one of these tools is a smart idea. Trust me, it’s worth it!
Blockchain-Enabled Timber Traceability Systems
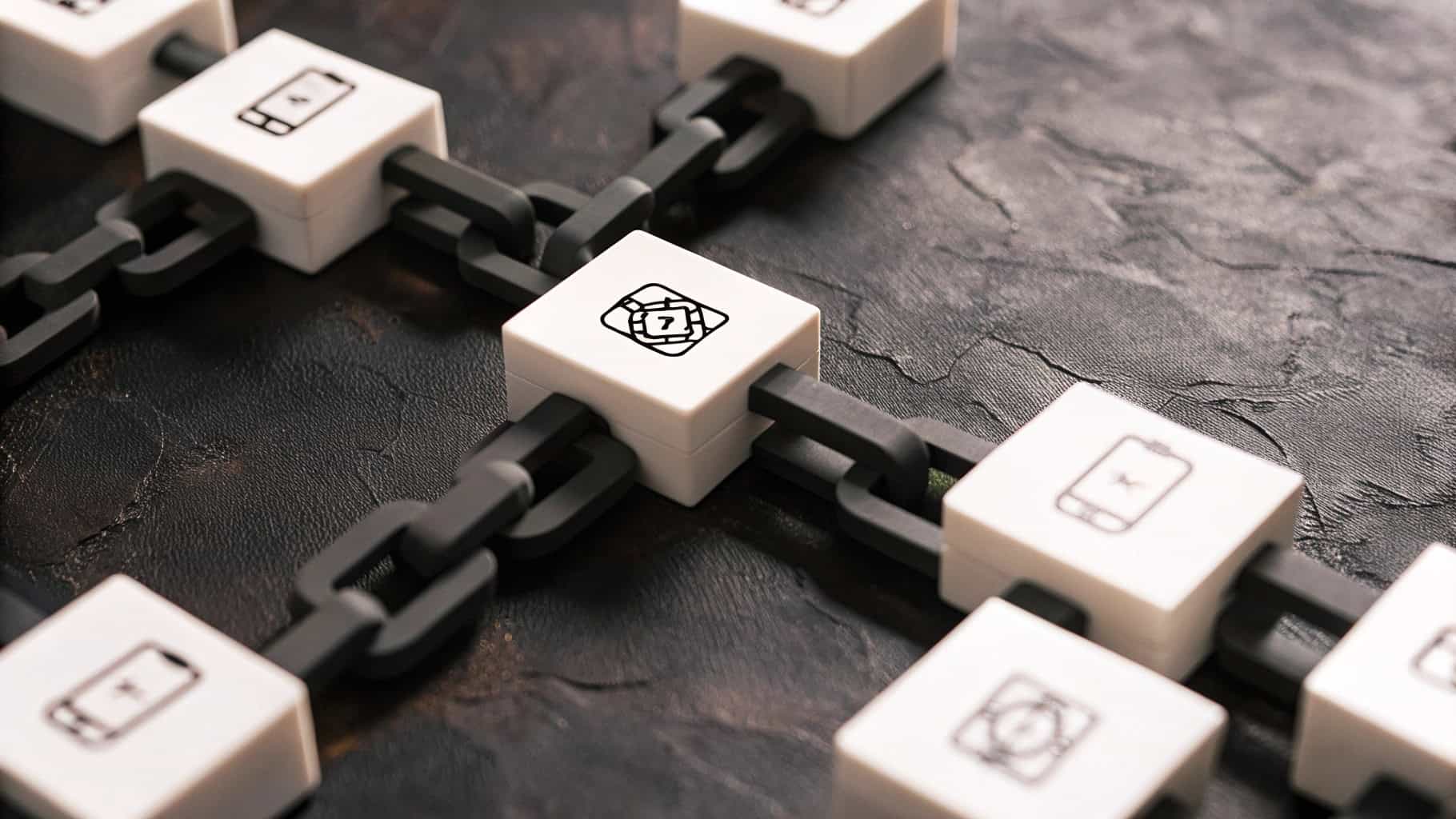
When I first heard about blockchain for tracking timber, it seemed tricky. But after learning more, I saw how it helps ensure good quality and sustainability. Let me explain it simply.
Digitized Wood Origin Certification Processes
Do you know where your wood comes from? With digital certification, it’s easy to check. Blockchain keeps a secure record of the wood’s journey—from the forest to the final product. This ensures every piece meets rules like the European Union Deforestation Regulation (EUDR).
Why is this important?
It makes the timber supply chain clear and honest.
It stops illegal logging by confirming the source.
It builds trust between buyers and sellers.
I’ve seen how this technology helps keep wood sustainable. It’s like giving each piece of wood a digital ID. You can trust it’s responsibly sourced.
Smart Contract Compliance Verification
Smart contracts are another great part of blockchain. These are automatic agreements that make sure everyone follows the rules. For example, if a supplier promises perfect wood, the smart contract checks the data. If something is wrong, it sends an alert.
This makes things faster and more accurate. No more waiting for manual checks or worrying about mistakes. I like how it keeps everyone honest and simplifies the process. It’s like having a digital judge for wood deals.
Real-Time Supply Chain Monitoring Solutions
Imagine tracking your wood at every step. Blockchain makes this possible. You can see where it is, who handled it, and how it was stored. This helps prevent damage during shipping.
I’ve used systems like this to watch shipments. It’s so helpful to catch problems early, like delays or bad handling. Plus, it ensures the wood arrives in great shape, ready to use.
Tip: For big projects, ask your supplier about blockchain tracking. It’s a smart way to ensure quality and sustainability.
Anti-Counterfeiting Technology Integration
Have you ever worried about whether the wood you’re buying is the real deal? I know I have. Counterfeit wood products are a growing problem, and they can lead to poor quality and even legal trouble. That’s why I’m a big fan of anti-counterfeiting technology. It’s like having a secret weapon to ensure you’re getting authentic, high-quality wood.
One of the coolest tools I’ve seen is QR code tagging. Each piece of wood gets a unique QR code that you can scan with your phone. This code tells you everything—where the wood came from, how it was processed, and even if it meets sustainability standards. It’s quick, easy, and super reliable.
Another method I’ve come across is DNA marking. Yes, you read that right—DNA! Scientists add a special marker to the wood that acts like a fingerprint. It’s impossible to fake, so you can trust the wood’s origin. This is especially useful for high-value timber, like teak or mahogany.
Tip: Always ask your supplier if they use anti-counterfeiting measures. It’s a simple way to protect yourself and your projects.
I’ve also seen blockchain systems play a role here. They create a digital record of the wood’s journey, from forest to store. This makes it nearly impossible for counterfeit products to slip through the cracks.
These technologies give me peace of mind. They ensure I’m working with genuine, high-quality wood. If you care about quality and sustainability, these tools are worth exploring. Trust me, they make a big difference!
Predictive Maintenance for Wood Processing Equipment
Vibration Analysis for Saw Blade Wear Detection
Keeping saw blades sharp is very important. Worn blades can cause bad cuts, waste wood, and be unsafe. That’s why I use vibration analysis to check them. It’s like a health check for your saw.
This method watches how the blade moves while cutting. If the movement changes, the blade might be worn or not straight. I’ve found this tool great for spotting problems early.
Studies also show how helpful this is. Research like "Experimental studies on band saw blade vibration" by Tanaka et al. (1981) and "Vibration control of band saws: Theory and experiment" by Yang and Mote (1990) proves it works. Small vibration changes can show wear, helping you fix issues fast.
Tip: Check for strange vibrations often. It saves time and money later.
Thermal Imaging for Machinery Health Monitoring
Have you ever felt a machine that’s too hot? That’s a warning sign. I use thermal imaging to find heat problems before they get worse.
Thermal cameras show heat patterns on machines. They help me see if a motor is too hot or a part isn’t cooling. It’s like a heat map for your tools. I’ve used it to find problems like stuck vents or worn-out parts.
Thermal imaging is quick and easy. Just scan the machine, and it shows hot spots right away. It’s a fast way to keep machines working well.
Note: Overheating can harm machines and ruin wood quality. Fixing it early helps a lot.
Automated Lubrication System Optimization
Machines need lubrication to work smoothly. Without it, parts rub together and wear out. I’ve seen machines fail because they weren’t oiled enough. That’s why I trust automated lubrication systems.
These systems add the right amount of oil to each part. They adjust based on how hard the machine is working. This saves oil and reduces wear.
I’ve noticed machines run much better with these systems. They stop overheating and reduce friction, so there are fewer breakdowns. Plus, they save time since you don’t have to oil parts by hand.
Tip: Want your machines to last longer? Try automated lubrication systems. They’re a big help for maintenance.
Production Line Downtime Prediction Models
Have you ever had a machine break down right in the middle of a project? I have, and let me tell you, it’s frustrating. That’s why I rely on production line downtime prediction models. These tools help me avoid unexpected stops by predicting when equipment might fail. It’s like having a crystal ball for your machines!
Here’s how it works. These models use data from sensors on the equipment. They track things like temperature, vibration, and speed. Then, they analyze this data to spot patterns that might signal a problem. For example, if a motor starts running hotter than usual, the model might flag it as a potential issue. This gives me time to fix it before it breaks down.
Tip: Always keep your sensors clean and calibrated. Accurate data makes these models more reliable.
I’ve noticed three big benefits from using these models:
Fewer surprises: Knowing about problems early means I can plan repairs instead of dealing with sudden breakdowns.
Lower costs: Fixing small issues is cheaper than replacing entire machines.
Better productivity: When machines run smoothly, projects stay on schedule.
One time, a downtime prediction model saved me from a major headache. It flagged unusual vibrations in a saw. I checked it out and found a loose bolt. Tightening it took five minutes, but it saved me hours of downtime.
If you’re serious about keeping your production line running smoothly, these models are a must-have. They’re easy to set up and can save you a ton of time and money. Trust me, once you try them, you’ll wonder how you ever managed without them!
Cost-Effective Defect Prevention Strategies
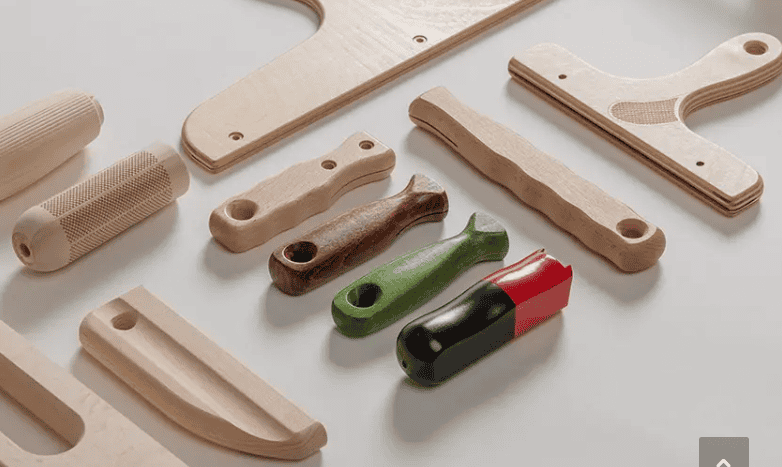
AI-Driven Defect Pattern Recognition Software
At first, I doubted AI could help with wood inspections. But after using it, I saw how much better it made things. AI software checks wood for defects quickly and accurately. It uses cameras and sensors to find cracks, knots, or warping. This saves time and ensures higher-quality wood for projects.
What I like most is how simple it is to use. You don’t need special skills—just set it up, and it works. It’s like having extra eyes that never get tired. Plus, it catches problems early, reducing waste. This means fewer bad pieces and more usable wood.
Tip: Want better wood quality? Try investing in AI tools.
Lean Manufacturing Waste Reduction Techniques
I always try to use every piece of wood wisely. Lean manufacturing helps me do this by cutting waste at every step. For example, I now use leftover wood pieces to make smaller items. It’s surprising how much material you can save this way.
Another method I use is planning cuts carefully. This reduces scraps and saves money while helping the environment. Lean techniques make everything smoother, from getting wood to finishing products.
Note: Small changes can save a lot. Start by finding where waste happens most.
Automated Grading System ROI Analysis
Buying an automated grading system seemed like a big choice. But after seeing the savings, I knew it was worth it. These systems check wood quality and sort out bad pieces automatically. This ensures only good wood moves forward.
These systems save money over time. They lower labor costs, speed up checks, and improve product quality. I’ve noticed happier customers and fewer complaints since using one. It’s a win-win for everyone.
Tip: Track your savings after installing a grading system. The results will amaze you.
Supplier Quality Scorecard Development
When I began working with wood suppliers, I saw tracking them was key. A supplier quality scorecard became my favorite tool for this. It’s like grading suppliers to see if they meet my needs. Let me explain how I make one and why it’s useful.
First, I pick what matters most for my projects. Quality is always number one for me. I also check delivery speed, prices, and eco-friendly practices. These are the main parts of my scorecard.
Here’s an example of how I set it up:
Category | Weight (%) | Supplier A | Supplier B |
---|---|---|---|
Quality of Materials | 40% | 9/10 | 8/10 |
On-Time Delivery | 30% | 10/10 | 7/10 |
Pricing | 20% | 8/10 | 9/10 |
Sustainability | 10% | 7/10 | 10/10 |
I rate each supplier based on how they perform in these areas. Then, I add up the scores to find the best match for my needs.
Tip: Keep your scorecard simple. Focus on what matters most for your projects.
Using a scorecard has saved me time and headaches. It helps me find dependable suppliers and avoid ones that might cause problems. It’s also great for talking with suppliers. If their score drops, I can show them where to improve.
If you don’t use a supplier scorecard yet, you should try it. It’s an easy way to stay organized and pick the best suppliers. Trust me, it makes a big difference!
Customized Quality Assurance Protocols Development
Species-Specific Defect Threshold Configuration
Different wood types have unique features and problems. Some woods, like oak, can handle small knots without losing strength. Softer woods, like pine, are weaker and need stricter checks. I set defect limits based on the wood type I’m using. This helps me decide what’s acceptable for each project.
To make things simple, I use a chart. It lists wood types and their allowed defects. This chart helps me quickly check if a piece of wood is good enough. Having clear rules saves time and keeps quality consistent.
Tip: Make your own chart for the wood you use most. It’s super helpful!
Climate-Adaptive Storage Condition Controls
Wood changes with the weather. If it’s too humid, wood swells. If it’s too dry, it cracks. That’s why I adjust storage to match the local climate. In wet areas, I use dehumidifiers to keep the air dry. In dry places, I use humidifiers to add moisture.
I also stack wood with spaces in between for airflow. This stops uneven drying, which can cause warping. Tools like hygrometers help me check humidity levels. They make it easy to keep storage conditions just right.
Note: Good storage doesn’t just stop damage. It also makes wood last longer.
Automated Rejection System Calibration
Sorting bad wood by hand takes a lot of time. That’s why I use automated systems to do it. These machines scan wood and reject pieces with defects. But they need to be set up correctly to work well.
I test the system with sample wood to adjust its settings. This ensures it catches bad wood and keeps good pieces. Regular maintenance also helps the system stay accurate. It takes some effort, but it saves time and reduces waste later.
Tip: Test your system with different wood types to make sure it works for all of them.
Continuous Improvement Feedback Loops
To keep wood products high-quality, I use feedback loops. These loops help me check and improve my work regularly. Let me explain how they make everything better.
First, I gather data after each project. I write down details about wood quality, machines, or delivery times. This helps me find patterns. For instance, if a supplier often sends bad wood, I know to talk to them or switch suppliers.
Tip: Use a notebook or spreadsheet to track problems. It doesn’t need to be fancy, just consistent.
Next, I involve my team. We meet to discuss what worked and what didn’t. Everyone shares ideas, and we solve problems together. This improves our work and builds teamwork. When people feel heard, they work harder.
Here’s how I use feedback loops:
Step 1: Find the problem (e.g., wood warping in storage).
Step 2: Figure out why (e.g., bad humidity control).
Step 3: Fix it (e.g., add a dehumidifier).
Step 4: Watch the results and adjust if needed.
Note: Feedback loops aren’t just for fixing mistakes. They help you learn and improve every time.
Since using feedback loops, I’ve seen big improvements in quality and speed. They’re simple but very effective. Once you try them, you’ll wonder how you managed without them!
Global Timber Quality Standards Compliance Guide
FSC Certification Audit Preparation Checklist
Getting ready for an FSC (Forest Stewardship Council) audit can seem hard. But with the right steps, it’s easier than you think. First, I check the FSC rules that apply to my work. These rules make sure the wood comes from well-managed forests.
Then, I gather important papers like purchase records and supplier certifications. Keeping these in order saves time during the audit. I also teach my team about FSC rules. Everyone needs to know how to help stay compliant.
One trick I use is doing a practice audit. It’s like a test run to find problems before the real audit. This step has saved me from surprises many times.
Tip: Always check if your supplier is FSC-certified. If they’re not, it could cause problems during your audit.
ISO 38200 Implementation Roadmap
ISO 38200 is about tracking wood and wood-based products. When I started using it, I broke it into small steps. First, I made a map of my supply chain. This showed where the wood comes from and how it moves.
Next, I set up a tracking system using barcodes and digital records. This made it easy to trace each piece of wood back to its source. I also trained my team to use the tools and understand why tracking is important.
Finally, I checked the system often to make sure it worked. These checks helped me find problems early, like missing labels or wrong records.
Note: ISO 38200 isn’t just about following rules. It also helps build trust with customers who care about the environment.
Customs Compliance Documentation Best Practices
Dealing with customs can be tricky, especially for international shipments. But following some simple steps makes it easier.
Make sure your wood packaging provider follows ISPM 15 rules.
Share ISPM 15 rules with your exporter so they understand them.
Add ISPM 15 compliance rules to your contracts.
Check wood packaging for pests or damage before shipping.
Teach exporters about the costs of breaking the rules, like fines or delays.
These steps have saved me from big mistakes. For example, I once found packaging that didn’t follow the rules. Fixing it before shipping saved me from delays and fines.
Tip: Always check your packaging materials when they arrive. This small step can stop big problems later.
International Grading System Cross-Reference
When I began working with wood, grading systems confused me. Different countries use different ways to grade wood. Over time, I learned to compare these systems. It made my work much easier. Let me explain how.
Why Cross-Referencing is Important
Grading systems check if wood meets certain standards. But grades don’t always match between countries. For example, “Select” in the U.S. isn’t the same as “Prime” in Europe. Knowing these differences helps you avoid mistakes. It also ensures you get the quality you need.
Common Grading Systems
Here’s a simple table of popular grading systems:
Grading System | Region | Focus |
---|---|---|
NHLA (National Hardwood Lumber Association) | United States | Hardwood quality and defects |
BS EN 942 | Europe | Appearance and structural use |
JAS (Japanese Agricultural Standard) | Japan | Strength and moisture content |
AS/NZS 4787 | Australia/New Zealand | Timber grading for structural use |
My Tips for Comparing Grades
Ask for Papers: Always get grading details from suppliers.
Use Comparison Charts: These help match grades between systems.
Test Small Batches: Unsure? Test a few pieces to check quality.
Tip: Keep a grading guide nearby. It saves time and helps with international orders.
Learning to cross-reference grades takes practice but is worth it. It ensures you pick the right wood for your projects. Once you understand it, you’ll feel more confident in your choices.
Emerging Technologies in Wood Defect Detection
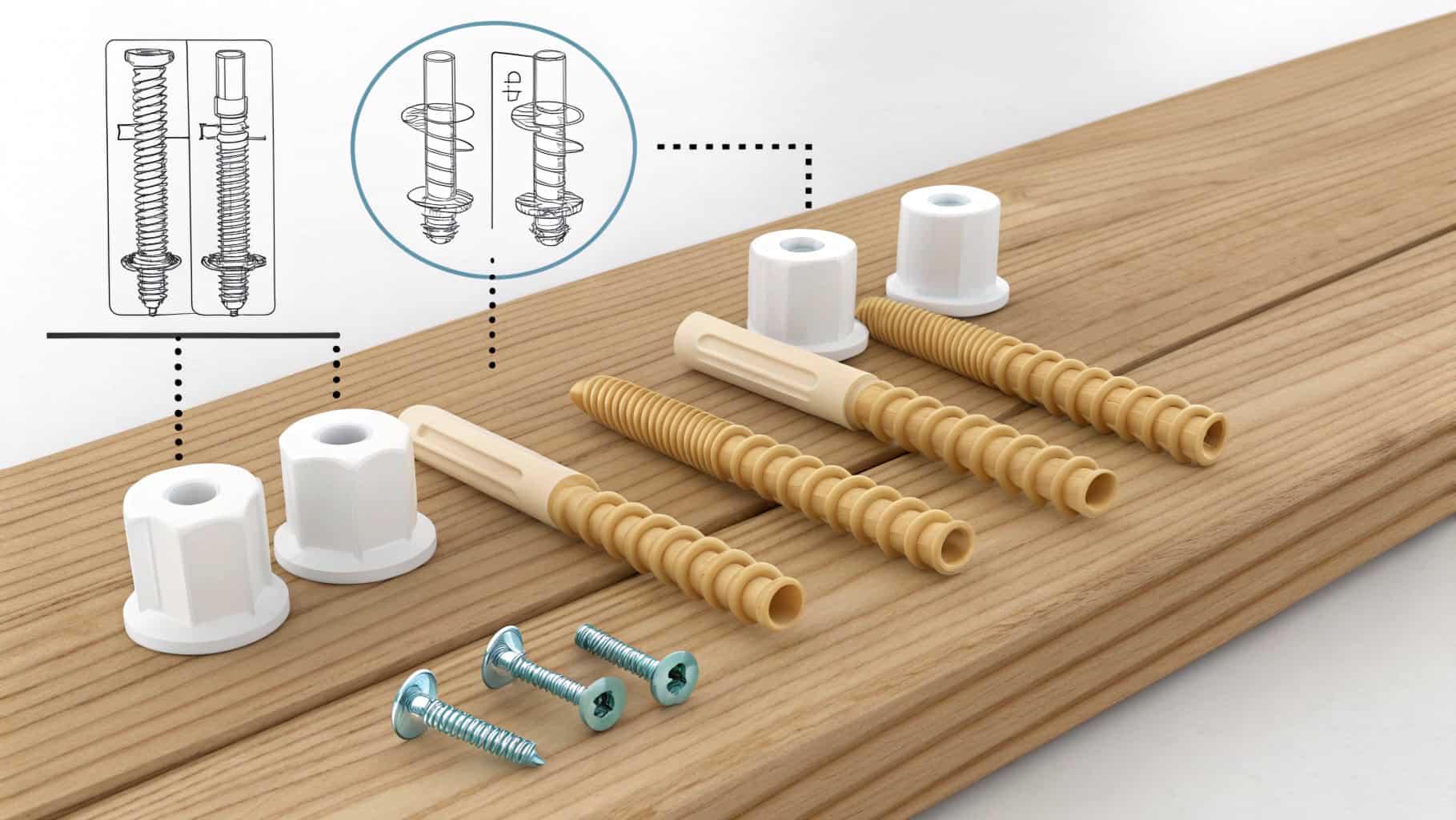
Hyperspectral Imaging for Early Decay Identification
Wouldn’t it be great to spot wood decay early? Hyperspectral imaging makes this possible. It uses light to find changes in wood that you can’t see. It’s like having special vision to catch decay before it spreads!
I’ve seen this tool in action. It scans the wood and notices tiny color or texture changes. These changes often mean decay or hidden problems. The best part? It works quickly and doesn’t harm the wood.
This technology is perfect for expensive projects. It ensures the wood is strong and problem-free. If you’re using costly lumber, hyperspectral imaging can save you from big mistakes.
Tip: Combine hyperspectral imaging with other tools for better results. It helps catch issues early and keeps your work on track.
X-Ray Tomography for 3D Internal Mapping
Some wood problems are hidden inside where you can’t see them. That’s why X-ray tomography is so useful. It creates a 3D image of the wood’s inside, showing cracks or empty spaces.
Here’s how it works. The X-ray scans the wood and makes a detailed picture of its structure. You can see everything, from small cracks to big gaps. It’s like looking inside the wood without cutting it open.
I’ve used this for projects where safety matters, like furniture or supports. Knowing the wood is solid inside gives me confidence. It also saves time and materials by avoiding bad pieces.
Note: X-ray tomography is great for wood that needs to hold heavy weight. It ensures the wood is strong and dependable.
Machine Learning-Based Defect Prediction
Machine learning has changed how I check wood. It helps predict defects before they appear. It’s like having a tool that sees the future of wood quality!
The software learns from past inspections to spot problems. Then, it scans new wood and flags possible defects. It’s fast, accurate, and perfect for big projects.
Here’s a quick look at studies showing how well it works:
Study | Methodology | Findings |
---|---|---|
Xie (2013) | Image recognition with digital image processing | Good algorithms improve defect detection accuracy. |
Zhang et al. (2015) | Principal Component Analysis (PCA) | PCA combines wood surface features effectively. |
Luo (2019) | Neural network comparison | CNN and SVM models are better than BP neural networks. |
Urbonas et al. (2019) | R-CNN | Achieved 96.1% accuracy in finding wood surface defects. |
Shi et al. (2020) | Mask R-CNN | Improved speed and accuracy for defect detection. |
One study showed a 7 to 22% improvement over older methods. That’s a big step forward!
Tip: For large lumber projects, machine learning tools save time and money. They’re a huge help for quality checks.
Robotics-Assisted Quality Control Workflows
Robots checking wood quality? It sounds like science fiction, but it’s real! These robots are changing how we inspect wood. They’re fast, accurate, and super dependable. Let me explain how they work and why they’re so useful.
First, robots are great at doing the same task over and over. They can check hundreds of wood pieces without getting tired. I’ve seen robotic arms with cameras and sensors scan wood for cracks, knots, and warping. They find flaws that even experts might miss.
Tip: For big production jobs, robots save time and reduce mistakes.
Another cool thing is how robots learn. Advanced robots use machine learning to improve. They study past inspections and get better at spotting problems. It’s like having a smart helper that never needs a break.
Here’s what makes robotics amazing:
Speed: Check hundreds of wood pieces in just minutes.
Consistency: Always deliver the same great results.
Safety: Keep people away from dangerous inspection tasks.
Robots also help cut waste. They catch bad wood early, so it doesn’t go further in production. This saves materials and lowers costs.
Note: Robots may cost a lot at first, but they save money over time by improving efficiency and reducing waste.
Robotics-assisted systems are a game-changer. If you care about quality and saving time, these tools are a must-have. Once you see them work, you’ll wonder how you managed without them!
Wood Density Measurement Certification
When picking a wood supplier, I always check the wood’s density. Why? Because density shows how strong and durable the wood is. Denser wood can handle more weight and lasts longer. That’s why I ask for a wood density measurement certification. It’s like a quality report for the wood.
Suppliers use tools like densitometers to measure density. This tool compares the wood’s weight to its size. If the numbers are off, it might mean the wood has hidden problems or wasn’t dried right. Trusting this certification helps me avoid weak wood in my projects.
Tip: Make sure the certification matches the wood type you’re buying. It’s an easy way to ensure good quality.
Sustainable Harvesting Practice Verification
I care about where my wood comes from. That’s why I check if suppliers follow sustainable harvesting rules. This means they cut trees carefully so forests can grow back. It’s good for the planet and ensures better wood quality.
I ask for certifications like FSC (Forest Stewardship Council) or PEFC (Program for the Endorsement of Forest Certification). These prove the supplier follows strict sustainability rules. Sometimes, I visit their site or ask for photos of their work. Seeing their process makes me feel confident about their practices.
Note: Sustainable wood often has fewer flaws because it’s handled with care.
Mill Production Process Auditing
Before choosing a supplier, I check how their mill works. This means looking at how they cut and dry the wood. A good mill makes strong, reliable wood. A bad one can cause problems like cracks or warping.
During my check, I look at their machines and ask about quality checks. For example, do they use tools to find defects? Do they dry the wood properly? These things matter. A quick visit or video call can show if the supplier is dependable.
Tip: Ask lots of questions during your check. Good suppliers will gladly explain their process.
Transportation Damage Prevention Standards
When I first started transporting wood, I didn’t realize how much damage could happen on the way. A few dents or scratches might not seem like a big deal, but they can ruin the quality of the wood. Over time, I’ve learned some simple ways to keep wood safe during shipping. Let me share what works best for me.
Use Proper Packaging Materials
The right packaging makes all the difference. I always use sturdy materials like wooden crates or reinforced cardboard. For extra protection, I wrap each piece in foam or bubble wrap. This stops scratches and absorbs shocks during transit.
Tip: If you’re shipping large quantities, stack the wood neatly and secure it with straps. This keeps everything in place.
Protect Against Moisture
Moisture is a sneaky problem. It can cause wood to warp or rot before it even arrives. I always use waterproof covers or plastic sheeting to keep the wood dry. If I’m shipping over long distances, I add silica gel packets to absorb any extra moisture.
Choose Reliable Transport
Not all trucks or containers are the same. I pick ones with smooth interiors and proper ventilation. This prevents the wood from rubbing against rough surfaces or overheating.
Inspect Before and After Shipping
Before loading, I check the wood for any existing damage. After delivery, I inspect it again to make sure it arrived in good shape. This helps me spot problems early and avoid future mistakes.
Note: Keeping a record of inspections can help if you need to file a claim for damages.
By following these steps, I’ve saved time, money, and a lot of frustration. Protecting wood during transportation isn’t hard, but it does take some planning. Trust me, it’s worth the effort!
Finding quality defects in wood blocks is very important. It helps make projects safer, stronger, and more successful. I’ve explained simple ways to check wood, like looking at it, testing its strength, listening for problems, and checking where it came from. These steps help you find problems early and pick the best wood.
Try using these tips in your next project. They’ll save you effort, money, and stress. Trust me, good wood makes a big difference in your work.
Tip: Begin with a few pieces—practice before working on bigger projects!
FAQ
What are the most common defects in wood blocks?
Knots, cracks, warping, and discoloration are common problems. These can make wood weaker and look worse. Always check the surface and edges to find these early.
How can I check for hidden defects inside wood?
I use tools like sound testers or ultrasonic devices. These find cracks or empty spots inside without harming the wood. They’re fast and great for big projects needing high quality.
Does moisture content affect wood quality?
Yes! Too much water makes wood swell and rot. Too little causes cracks and bending. I use a moisture meter to check the wood before starting.
Are automated systems worth it for defect detection?
Yes, they save time and are very accurate. Tools like smart scanners or AI software find flaws you might miss. They’re helpful if you handle lots of wood.
How do I ensure my wood comes from sustainable sources?
Look for labels like FSC or PEFC. These show the wood was cut responsibly. You can also ask suppliers about their methods or visit their sites to check.