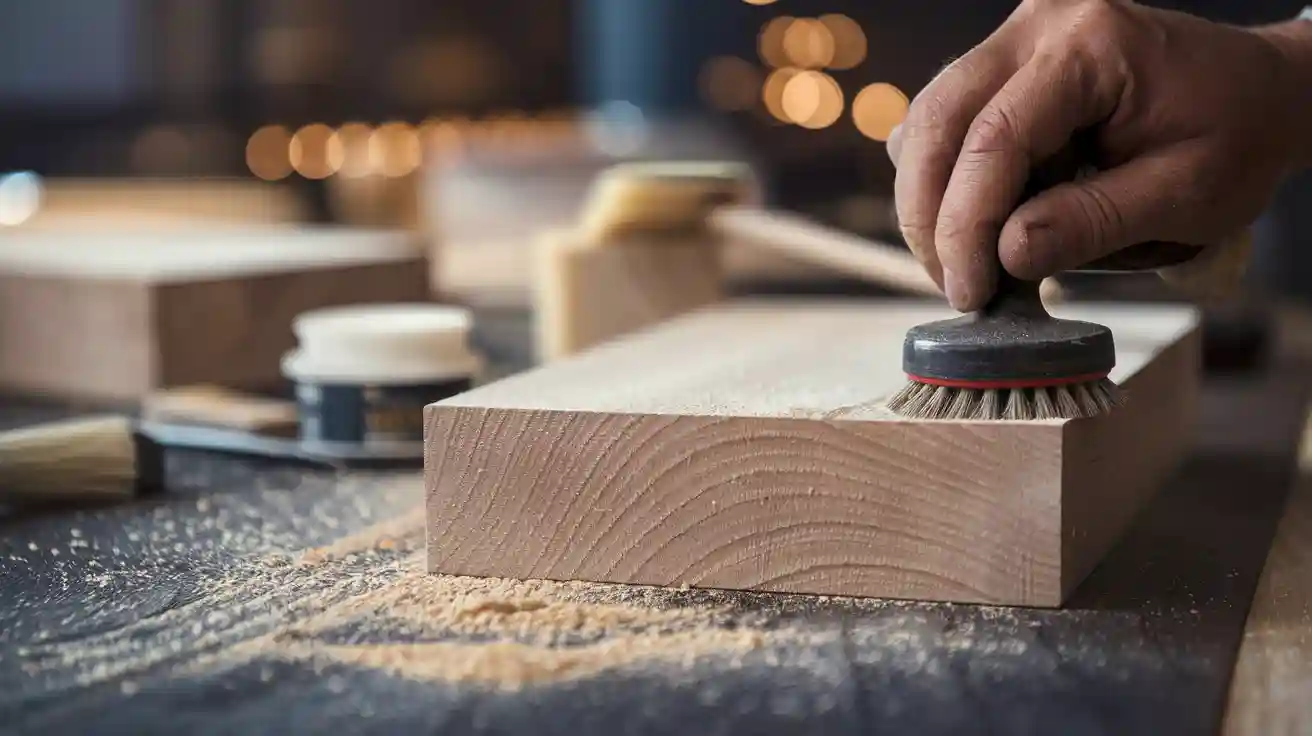
Have you ever thought about why some wood lasts so long while other wood falls apart quickly? The secret is how you effectively surface treat the wood. Treating wood isn’t just about making it look nice; it’s about protecting it so it stays strong over time. When you treat wood correctly, you keep it safe, enhance its appearance, and help it last longer.
I’ve seen what happens when wood isn’t treated. It can crack, bend, or even grow mold. By cleaning the wood well and using the right finish, you can stop these problems. For example, a study showed that pressure-treated wood lasts much longer than other types, like Siberian larch. This is because treatments make wood stronger and better for the environment.
If you want to finish wood the right way, start by cleaning it. Clean the wood to get rid of dirt or grease. Then, add a finish like oil or varnish. Whether you’re cleaning a butcher block or outdoor furniture, using the right method to effectively surface treat the wood is very important.
Key Takeaways
Clean the wood well to get rid of dirt and grease. This helps the finish stick better and last longer.
Pick wood with the right moisture level. Use 6-8% for indoor wood and 9-14% for outdoor wood to avoid problems with the finish.
Try using machines for sanding and oiling. This saves time, spreads the finish evenly, and lowers work costs.
Use safe, FDA-approved finishes for butcher blocks. This is important for food-related items to stay safe and follow rules.
Take care of the wood regularly, like recoating once a year. This keeps it looking nice and makes it last longer.
Essential Wood Surface Treatment Techniques for Manufacturers
Comparing Hardwood vs. Softwood for Industrial Use
Picking between hardwood and softwood can be confusing. I’ve used both types, and each has its benefits. Hardwood, like oak or maple, is strong and lasts longer. It’s perfect for projects that need durability. Softwood, like pine or cedar, is lighter and easier to handle. It’s better for projects where weight matters more than strength.
Here’s what I’ve noticed about durability:
Hardwood breaks down slower than softwood, especially with proper treatment.
Treating wood, like oiling hardwood, makes it even stronger.
Durability tests vary, so results depend on the wood type and finish.
For strong, long-lasting projects, hardwood is a good choice. For lighter, easier projects, softwood can save time and effort.
Optimal Moisture Content for Pre-Treatment Processing
Before treating wood, the moisture level must be just right. Too much or too little moisture can ruin the finish. The best moisture level depends on where the wood will be used. For indoor wood, aim for 6-8% moisture. For construction wood, 9-14% works best.
Here’s a simple guide:
Humidity of the in-use location | EMC of the in-use location | Corresponding MC the wood will attain at this location |
---|---|---|
19-25% | 5% | 5% |
26-32% | 6% | 6% |
33-39% | 7% | 7% |
40-46% | 8% | 8% |
47-52% | 9% | 9% |
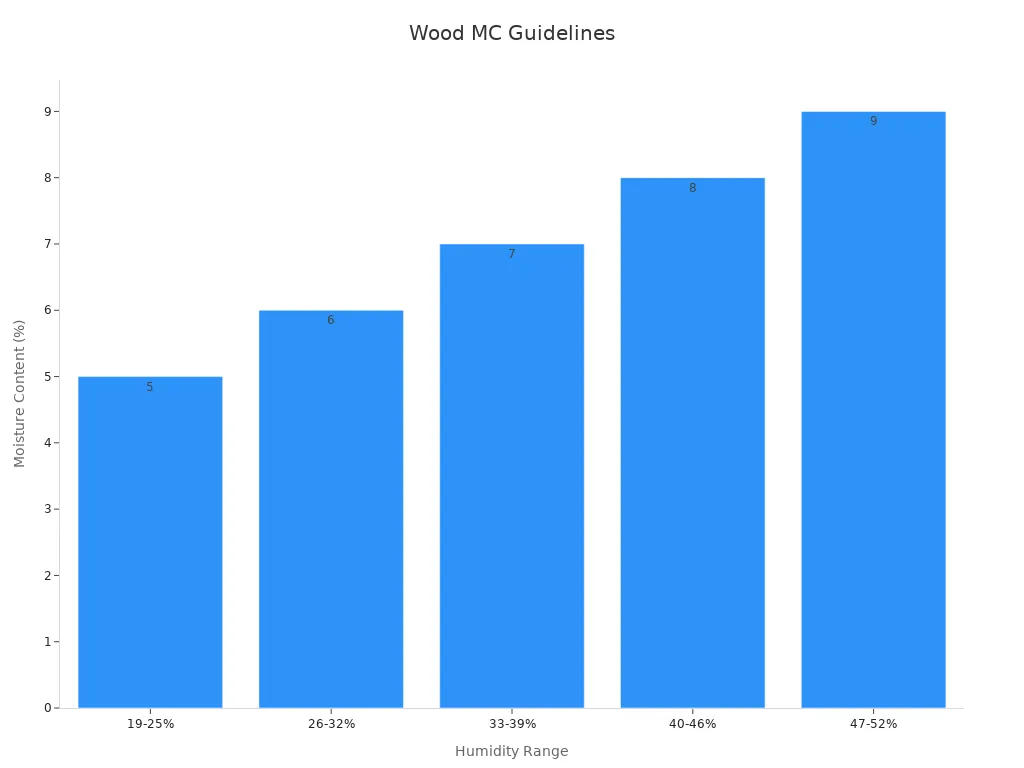
If you’re unsure, match the moisture level to the wood’s environment. This helps the finish stick well and last longer.
Automated Sanding Systems for Batch Production
Sanding is a key step for wood projects. Automated sanding systems make this process faster and better. These systems save time and create smooth surfaces for finishes like oil or varnish.
Automated systems also lower labor costs and reduce waste. They follow environmental rules and work well for large orders. If you handle big batches, these systems improve speed and cut costs. They also prepare wood perfectly for the next steps, like oiling or finishing.
Cost-Effective Oiling Methods for Bulk Orders
Treating lots of wood with oil is cheap and easy. It works well and can be done for big orders. Over time, I’ve found ways to save even more money.
First, buy oil in large amounts. Many sellers give discounts for bulk purchases. Contact local suppliers to ask for better prices. You’d be surprised how much you can save by asking.
Next, use machines to apply the oil. These machines spread oil evenly on the wood. This saves time and avoids wasting oil. Hand oiling can leave uneven spots and waste product. Machines make sure every piece looks the same.
Also, reuse leftover oil. After oiling, filter and save extra oil for later. This cuts costs and reduces waste, which is great for the environment.
Finally, pick the right oil for your project. Cheaper oils like linseed or tung oil work for most wood. For special projects, you might need pricier oils. Always choose oil based on how the wood will be used.
By using these tips, you can treat wood well without spending too much. Whether it’s a small or large order, these ideas help save money and keep quality high.
Professional-Grade Chopping Block Finishing Solutions
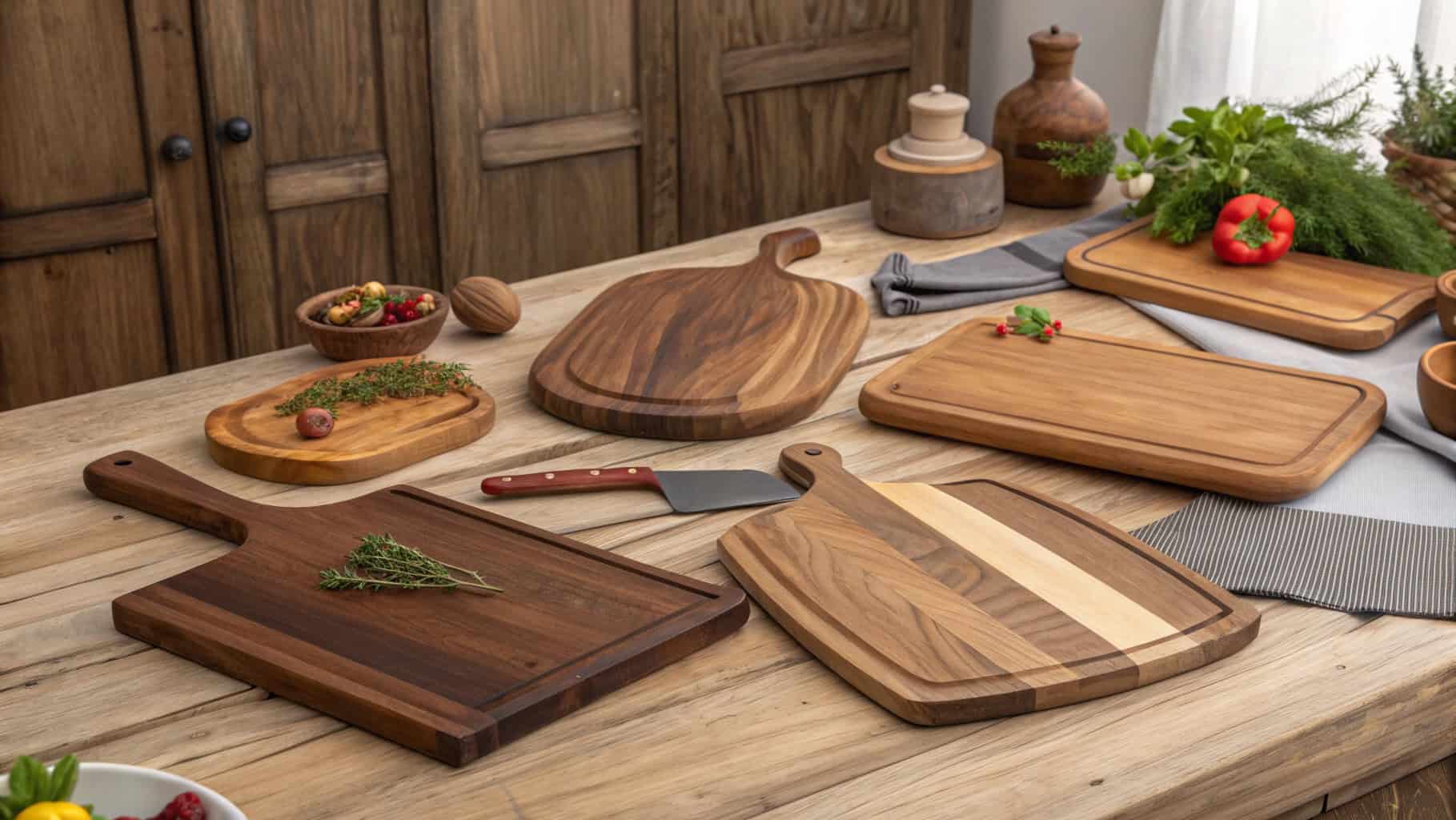
FDA-Approved Food-Safe Finishes for Export Markets
Safety is key when working with chopping block surfaces. I always pick FDA-approved food-safe finishes. These finishes stop bacteria and meet strict rules. They are perfect for export markets where safety is required.
Here’s why they are great:
They use special polymers to stop contamination during food prep.
Many are blue, making them easy to spot visually.
They resist heat, chemicals, and wear, which is perfect for heavy use.
These finishes also seal the wood, keeping out moisture and damage. I apply several coats to make the surface strong and long-lasting. This process improves the surface and stops bacteria, which is very important for food use.
High-Speed Curing Techniques for Factory Output
Finishing butcher blocks quickly is important for big orders. High-speed curing methods, like laser curing, are very helpful. They cut curing time from minutes to just 30 seconds. This saves energy and increases factory production.
I’ve seen how this method lets me finish quickly without losing quality. It’s great for large jobs where time is valuable. Fast curing also makes sure the sealant sets evenly. This creates a smooth and tough surface.
Custom Stain Formulations for Brand Differentiation
Custom stains are my favorite for unique chopping block designs. I enjoy trying different finishes to match a brand’s style. Custom stains show off the wood’s natural grain and add personality.
To get the best look, I layer the stain for depth and color. This makes the wood look better and protects it from damage. Light stains give a simple look, while dark stains feel rustic. Custom stains help chopping blocks stand out in busy markets.
Scratch-Resistant Nanocoatings for Premium Lines
Scratches can ruin the look of premium wood products. That’s why scratch-resistant nanocoatings are a great choice. These coatings act like a shield, protecting wood from damage. They keep the surface smooth and looking new.
What makes nanocoatings unique? They use tiny particles you can’t see. These particles create a thin, clear layer on the wood. This layer is strong and stops scratches from keys or tools. It protects the wood without changing its natural look or feel.
Here’s why nanocoatings are amazing for premium wood:
Durability: They last much longer than regular finishes.
Transparency: They show off the wood’s natural grain.
Ease of Maintenance: Dirt doesn’t stick, so cleaning is simple.
Pro Tip: Test the coating on a small spot first. This ensures it looks right.
People who buy premium wood want it to stand out. Nanocoatings help by adding protection and a touch of luxury. They are also eco-friendly, which is great for the planet.
For high-end projects, nanocoatings are worth trying. They protect wood and keep it looking perfect for years.
Industrial Wood Treatment Equipment Guide
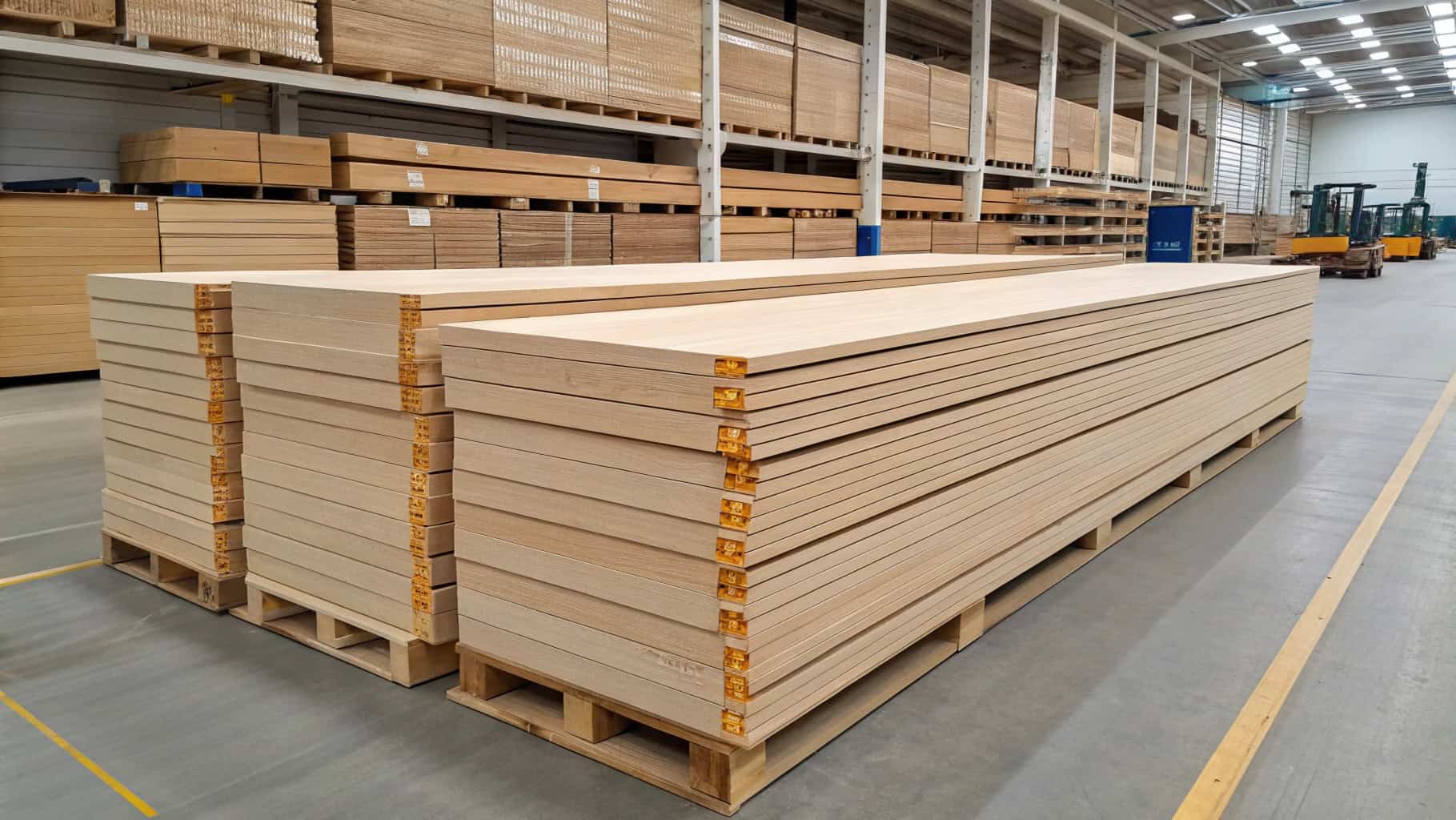
UV Curing Systems for Fast-Drying Finishes
When I need to work faster without losing quality, I use UV curing systems. These systems dry finishes in just seconds. They are great for projects with tight deadlines. Traditional drying takes hours, but UV curing is much quicker. It’s like giving your workshop a speed boost!
Here’s why UV curing systems are so effective:
Advantage | Description |
---|---|
Faster Curing Times | Dries finishes in seconds, making production faster. |
Meeting Deadlines | Helps finish projects on time and keeps customers happy. |
Material Waste | Cuts waste by reducing extra material, supporting eco-friendly practices. |
These systems also make production smoother. They let other steps happen right after curing, saving time. If you want to work faster and smarter, UV curing systems are a great choice.
Spray Booth Configurations for Even Coating
Getting a smooth finish on wood can be hard, but spray booths help a lot. The right setup makes painting easier and better. Special filters in the booth remove dust from the air. This keeps the paint job clean and professional-looking.
Automated spray guns are also very helpful. They spray paint evenly, so every piece looks the same. Filters in the booth catch extra paint, keeping the area clean and protecting the tools. With these features, spray booths make sure your work looks perfect every time.
Pro Tip: Clean the filters often to keep the booth working well and avoid dirt in the paint.
Dust Extraction Solutions for Workshop Safety
Dust isn’t just messy—it’s harmful. That’s why I always use dust extraction systems in my workshop. These systems clean the air and keep workers safe from dangerous particles.
Modern systems use smart technology to remove dust quickly. For example:
EtherCAT tech works in less than 1 millisecond, improving speed.
XFC tech responds in under 100 microseconds, making processes faster.
These systems don’t just make the air safer; they also help you work better. Clean air means fewer breaks and more focus. If you want a safer and more productive workshop, dust extraction systems are a must-have.
ROI Analysis of Automated Oil Application Machines
At first, I wasn’t sure if automated oil machines were worth it. But after checking the numbers, I saw they are a big help for large wood projects. Let me explain why.
How Automated Machines Save Money
Manual oiling takes a lot of time and effort. Workers often struggle to apply oil evenly, causing mistakes. Automated machines fix this issue. They spread oil evenly, wasting less and making each piece look great. Over time, this saves money by avoiding mistakes and wasted materials.
Here’s a simple comparison:
Manual Oiling | Automated Oiling |
---|---|
Hard work needed | Little labor needed |
Uneven oil application | Smooth, even application |
More oil wasted | Less oil used |
Improving Productivity
These machines also work faster. One machine can do the job of many workers. This helps finish orders quickly and take on more jobs. Faster work keeps customers happy and brings in more money.
Pro Tip: Track how long manual oiling takes. Compare it to the speed of an automated machine. The difference will surprise you.
Long-Term Benefits
The upfront cost may seem high, but the savings are huge. You’ll spend less on labor, waste fewer materials, and get more done. These machines last for years if cared for properly. It’s like having a worker who never gets tired.
If you want to grow your wood business, automated oil machines are a smart choice. They save time, cut costs, and improve results. That’s a win-win for everyone.
Export-Ready Wood Surface Preparation Standards
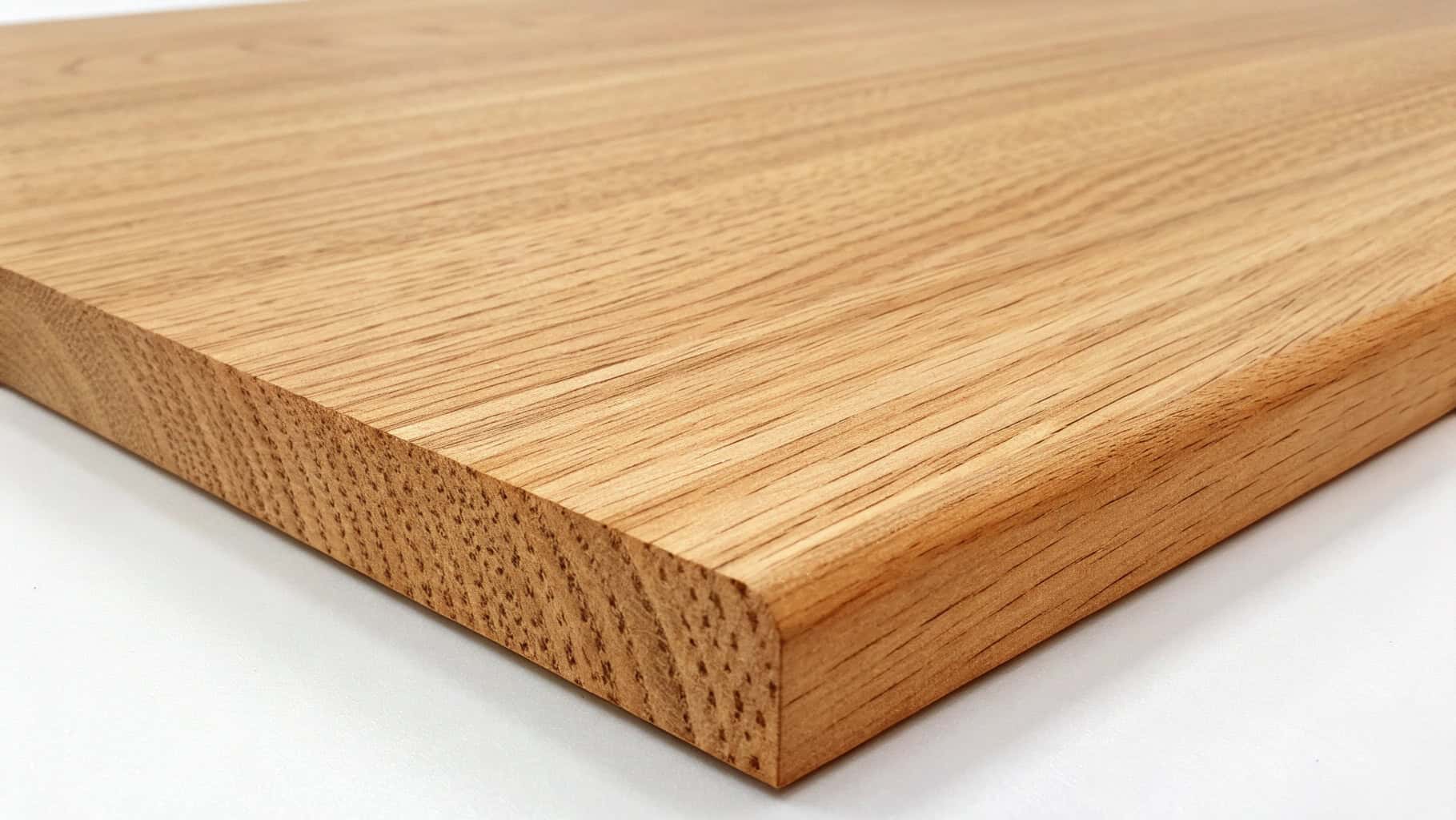
Meeting EU REACH Chemical Compliance
When exporting wood, following EU REACH rules is essential. These rules ensure products are safe for people and nature. One important rule limits formaldehyde emissions. By August 2026, the limit will drop to 0.05 ppm. That’s half of today’s allowed amount!
To meet these rules, I use low-emission finishes and adhesives. These products keep formaldehyde levels safe. I also test the wood often to ensure it meets the standards. This isn’t just about rules—it’s about making safer, better products for buyers.
Tip: Ask suppliers for certifications. It’s the easiest way to check if materials meet EU rules.
Humidity-Resistant Treatments for Tropical Markets
Shipping wood to tropical areas can be tough. High humidity can cause swelling, warping, or mold. Humidity-resistant treatments help protect the wood. They seal it, keeping moisture out and surfaces smooth.
For tropical markets, I use water-repellent finishes. These finishes block moisture and protect the wood. I also suggest kiln-dried wood. It has less moisture, so it stays stable in humid places.
Pro Tip: Use anti-mold additives in your finish. They’re great for humid areas.
Pallet-Free Packaging for Finished Block Transport
Pallet-free packaging is great for shipping wood blocks. It saves space and lowers shipping costs. I use shrink wrap or custom cardboard to secure the blocks. These materials protect the wood without needing heavy pallets.
This method also meets global shipping rules. Many countries like pallet-free options because they’re easier to handle and eco-friendly. It’s also a good way to show customers you care about the planet.
Note: Label packages clearly. This avoids delays at customs.
Documentation Needs for Shipping Wood Blocks Abroad
Sending wood blocks to other countries can seem tricky. But having the right papers makes it simpler. Missing documents can cause delays or fines. I always check everything carefully before shipping. Here are the main papers you’ll need:
1. Commercial Invoice
This is like a receipt for your shipment. It shows details like buyer, seller, product info, amount, and cost. Customs use it to figure out taxes, so it must be correct.
2. Packing List
This is a list of what’s in the shipment. It includes weight, size, and packaging info. A clear list helps avoid problems during checks.
3. Certificate of Origin (COO)
Some places need proof of where the wood blocks were made. A COO shows the origin and may lower tariffs. I get mine from the local chamber of commerce.
4. Export License
You might need this depending on the country. It proves your shipment follows export rules. I always check the rules for the destination.
5. Bill of Lading (BOL)
This is an agreement with the shipping company. It proves they got your goods and lists transport terms. I keep a copy in case of issues.
Pro Tip: Label papers clearly and save digital copies. It helps if something gets lost.
By organizing these papers, you’ll avoid delays and ship smoothly. It’s worth the effort!
Durable Outdoor Wood Block Treatments
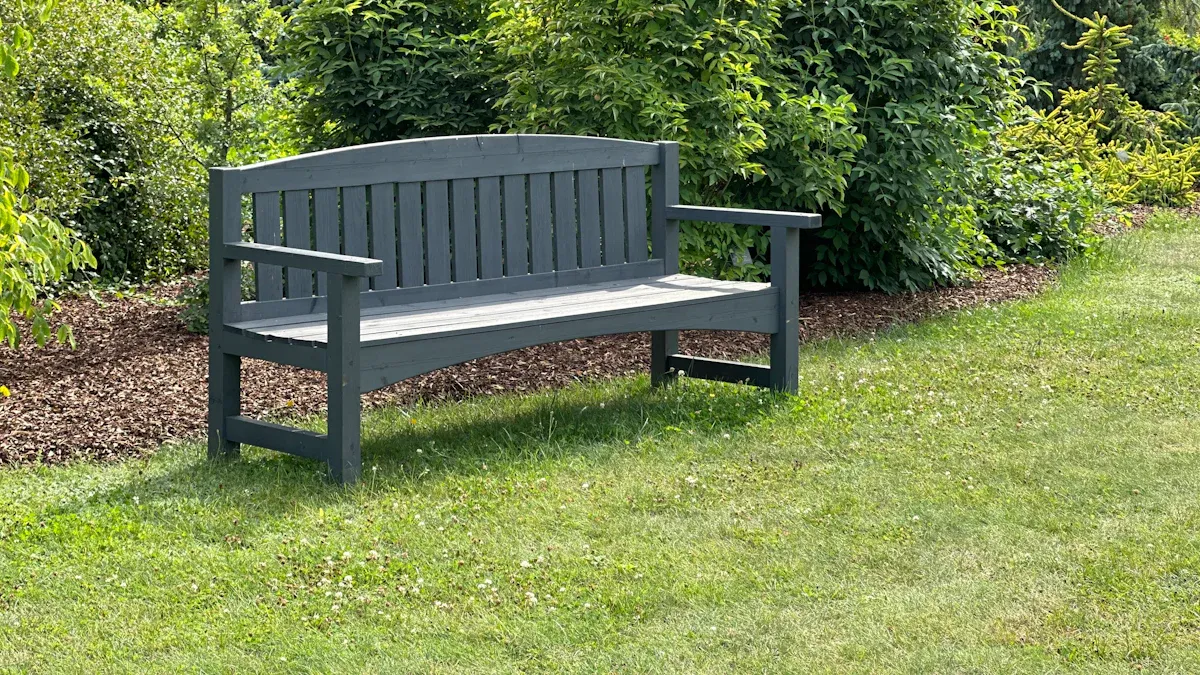
Marine-Grade Epoxy for Waterfront Applications
For wood near water, I use marine-grade epoxy. It’s like armor for outdoor wood. This epoxy makes a strong, waterproof shield. It protects wood from water, salt, and sunlight. I’ve used it on docks, benches, and shore decorations. It stops wood from swelling or cracking.
Using marine-grade epoxy is easy. First, clean and dry the wood. Dirt or grease can stop the epoxy from sticking. Next, mix the epoxy and brush it on evenly. It dries fast and leaves a shiny, clear layer. This layer seals the wood and makes it look better.
If you’re working with wood near water, try marine-grade epoxy. It’s tough, simple to use, and keeps wood looking great for years.
UV-Stabilized Pigments for Color Retention
Sunlight can fade outdoor wood over time. That’s why I use UV-stabilized pigments. These pigments protect the wood’s color and keep it bright. They’re great for furniture, fences, or any wood in the sun.
Here’s how they help:
UV Absorbers (UVAs): They soak up harmful UV rays and turn them into heat.
Hindered Amine Light Stabilizers (HALS): They stop fading by trapping harmful radicals.
Lignin Stabilizer: It keeps lignin, a part of wood, from breaking down and losing color.
I’ve seen how these pigments work. Without them, wood fades and looks old. With them, the color stays fresh and bright for years. For outdoor wood, UV-stabilized pigments are a smart choice.
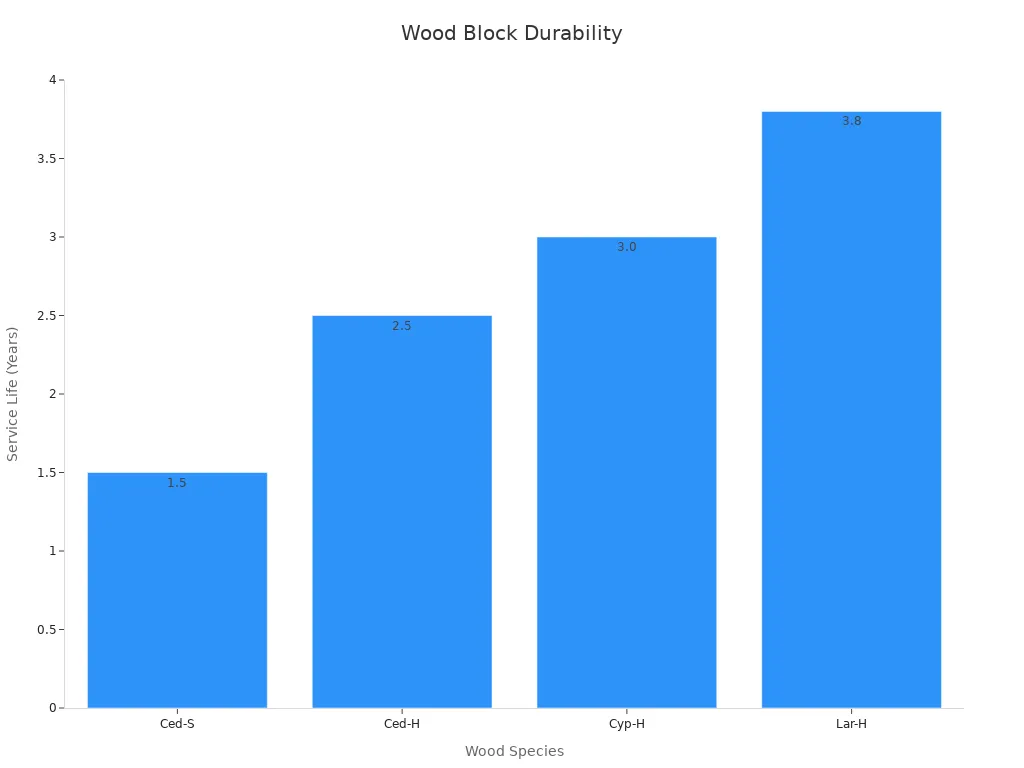
Anti-Mold Additives for High-Humidity Regions
Humidity can ruin outdoor wood by causing mold. Mold makes wood look bad and weakens it. To stop this, I add anti-mold treatments to finishes. These treatments block mold and keep wood strong.
I’ve used them in tropical areas with high humidity. They create a layer that stops moisture and mold spores. For the best results, I pair anti-mold treatments with water-repellent finishes. This double layer keeps wood safe in any weather.
If you’re treating wood for humid places, don’t skip this step. It’s easy and makes a big difference.
Load-Bearing Surface Coatings for Heavy Use
If wood needs to hold heavy weight, use special coatings. These coatings make wood stronger and protect it from damage. They are great for things like pallets, workbenches, or outdoor decks.
Why Use Load-Bearing Coatings?
Wood used for heavy tasks faces pressure and friction. Without protection, it can crack or wear out fast. I’ve seen untreated wood break, and it’s not good. Load-bearing coatings make wood tougher and last longer, even in hard conditions.
Choosing the Right Coating
Not all coatings work the same. For heavy use, pick coatings with these features:
High Abrasion Resistance: Stops scratches and surface damage.
Impact Resistance: Protects from dents caused by heavy items.
Waterproofing: Blocks moisture that weakens wood.
Non-Slip Properties: Keeps surfaces safe in busy areas.
Pro Tip: I prefer polyurethane coatings. They are strong, last long, and easy to use.
Application Tips
Applying coatings is simple but needs care. First, sand the wood to make it smooth. Clean off dust or dirt. Use a brush or roller to spread the coating evenly. Let it dry before adding more layers. Two or three coats work best.
With the right coating, wood can handle heavy use easily. It’s a small effort for big results!
Sustainable Surface Treatment Alternatives
Plant-Based Polymer Finishes for Eco-Certification
Plant-based polymer finishes are great for eco-friendly wood treatment. They come from renewable materials like soy or linseed oil. These finishes help businesses earn eco-certifications and lower harmful emissions. They’re safe for the planet and protect the wood.
These finishes make wood look natural and smooth. They also create a strong, biodegradable layer. To use them, first clean the wood to remove dirt or grease. Then, apply the finish evenly with a brush or cloth. It dries fast and leaves a shiny, natural look.
If you want a green option, try plant-based finishes. They protect wood and show your business cares about the environment.
Low-VOC Compliance for North American Markets
Low-VOC finishes are important for North American rules. VOCs, or volatile organic compounds, harm air quality. Low-VOC products are safer for workers and better for the earth.
Before applying, clean the wood well to remove any residue. Then, use a roller or sprayer to spread the finish evenly. These finishes are just as strong and shiny as regular ones but without harmful chemicals.
For exporting wood to North America, low-VOC finishes are a must. They meet rules and help protect the environment.
Waste Oil Recycling in Production Facilities
Recycling leftover oil is a smart way to cut waste. Instead of throwing it away, you can clean and reuse it. This saves money and helps the environment.
Here’s how it works. After oiling wood, collect the extra oil in a container. Filter it to remove dirt or debris. Then, store it for later use. This method is great for big production facilities. It reduces costs and ensures no oil is wasted.
Recycling oil is simple and effective. It’s good for the planet, saves money, and is easy to do in any workshop.
Carbon-Neutral Treatment Process Auditing
When I first learned about carbon-neutral processes, I wondered, "What does that mean?" Later, I found out it’s about lowering carbon emissions and being eco-friendly. Auditing helps make this possible.
Start by checking how much energy you use. This includes machine electricity and fuel for transport. I use tools like energy trackers and fuel logs to monitor this. Once you know your emissions, you can find ways to reduce them.
Pro Tip: Use solar or wind power in your workshop. It cuts emissions a lot.
Next, review the materials you use. Some treatments release harmful chemicals. I now use low-VOC and plant-based products. They are safer for the planet and can earn eco-certifications. These certifications are great for selling to eco-conscious buyers.
Here’s a simple checklist I follow during audits:
✅ Track energy use and find areas with high consumption.
✅ Check the carbon footprint of materials.
✅ Reduce waste, like reusing leftover oil.
✅ Offset emissions by buying carbon credits.
Auditing may seem hard, but it’s helpful. It saves money, attracts green customers, and helps the planet. If you haven’t tried it, start now. You’ll feel proud knowing your process is eco-friendly. 🌱
Quality Control in Wood Surface Finishing
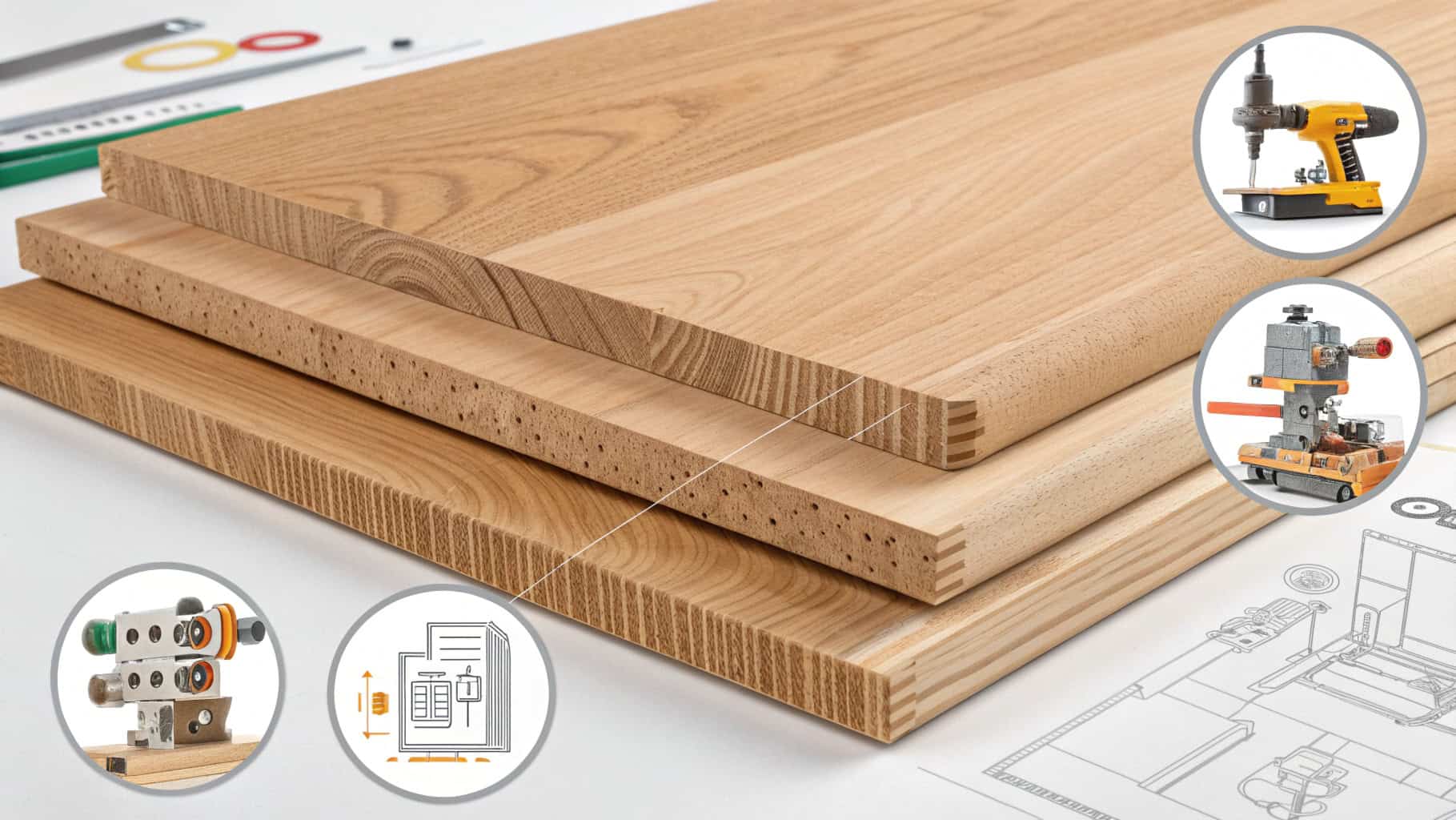
Laser Thickness Measurement for Coating Uniformity
To get a smooth finish, I use laser tools. These tools check if the coating is even on the wood. Uneven coatings can make wood look bad and wear out faster. Lasers help me find and fix these problems quickly.
Experts say even finishes are very important. Tools like profilometers measure coating thickness well. They make sure the finish looks good and protects the wood. I’ve seen that even coatings help wood last longer and stay strong.
Pro Tip: Check the coating after each layer dries. This keeps it smooth and even.
Salt Spray Testing for Coastal Market Durability
Wood near the coast faces salty air, which can harm finishes. To test this, I use salt spray testing. This test shows how well the finish can handle tough coastal weather.
Testing is key for wood in harsh places. It helps me pick the best finishes for protection. Finishes with strong moisture barriers work best. They stop salt damage and keep wood looking great.
If you’re making wood for coastal areas, always do this test. It helps ensure quality and durability.
Microscope Inspection of Wood Grain Penetration
To see how well a finish soaks into wood, I use a microscope. This tool shows if the finish has gone deep into the grain. Deep penetration means better protection and a longer-lasting finish.
Checking the surface closely is important for good results. It helps improve the process and ensures high-quality products. I’ve found that finishes that soak in well protect wood from moisture and damage while making it look better.
Note: Test a small piece first before treating all the wood. This saves time and avoids mistakes.
Batch Traceability Systems for Defect Management
Have you ever had a customer complain about a defect in your wood products and struggled to figure out where things went wrong? I’ve been there, and trust me, it’s frustrating. That’s where batch traceability systems come in. They’re like a detective for your production line, helping you track every step of the process.
Here’s how they work. A batch traceability system assigns a unique code to each batch of wood products. This code links to detailed records, like the type of wood, the treatments used, and even the equipment settings during production. If a defect pops up, you can trace it back to its source in no time.
Pro Tip: Always label batches clearly and store records digitally. It saves time and avoids confusion.
Why are these systems so important? First, they help you fix problems faster. Let’s say a batch of wood blocks has uneven finishes. With traceability, you can pinpoint whether the issue came from a faulty machine, a bad batch of oil, or something else. Second, they improve quality control. By analyzing data from past batches, you can spot patterns and prevent future defects.
Here’s what I love most: these systems build trust with customers. When you can quickly address issues and show them you’re on top of things, they’ll feel more confident in your products.
If you’re not using a batch traceability system yet, now’s the time to start. It’s a game-changer for managing defects and keeping your production line running smoothly.
Cost-Reduction Strategies for Bulk Treatment
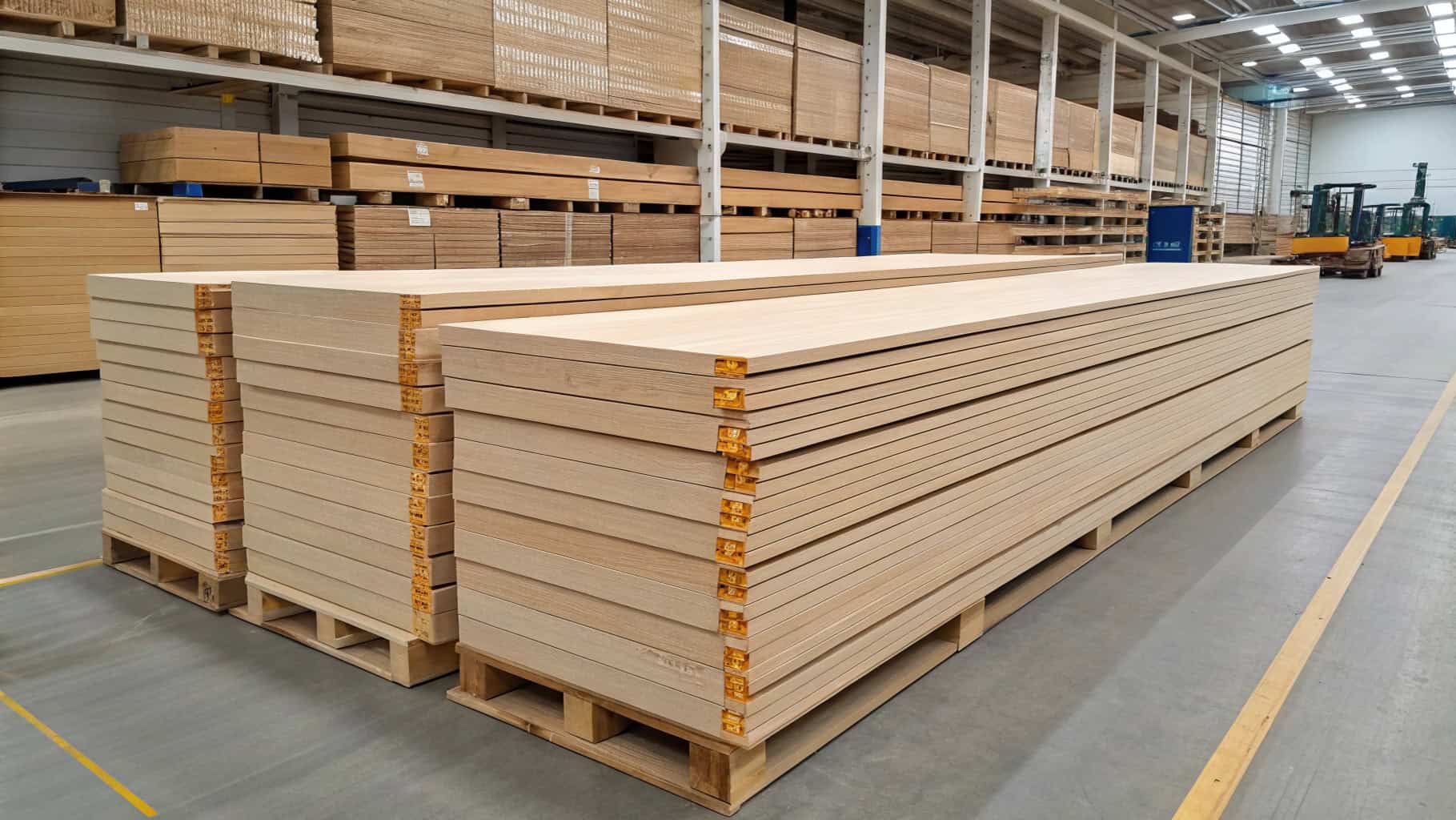
Bulk Purchasing Discounts on Food-Grade Oils
Buying food-grade oils in large amounts saves a lot of money. When you buy more, the price per unit gets cheaper. It’s like getting a discount just for ordering bigger quantities.
I’ve experienced this myself. Once, a supplier gave me 15% off for ordering a larger batch. That saved me hundreds of dollars in one go. Plus, it meant I didn’t have to reorder as often, which saved time too.
Here’s an idea: talk to local suppliers and ask about discounts for bulk orders. Many will lower prices if you buy more. It helps you save money, and they get a bigger sale.
Pro Tip: Keep bulk oil in a cool, dry place. Use airtight containers to stop it from spoiling.
Energy-Efficient Drying Tunnel Designs
Drying tunnels are important for treating wood, but they use a lot of energy. Switching to energy-saving designs has helped me cut costs. These tunnels dry wood faster while using less power.
One design I like uses zoned heating. It heats only the parts of the tunnel that need it, saving energy. Another feature is automated temperature control. It adjusts the heat based on how wet the wood is, which saves even more power.
If you’re upgrading your tools, pick drying tunnels with these features. They’ll save you money and are better for the planet.
Multi-Stage Filtration for Oil Reuse
Reusing oil is a great way to save money. After treating wood, I collect leftover oil and clean it with a multi-stage filtration system. This system removes dirt and other stuff, making the oil good to use again.
Here’s how it works:
Primary Filter: Takes out big pieces like wood chips.
Secondary Filter: Removes smaller bits like dust.
Final Stage: Cleans the oil completely so it’s ready to reuse.
This method saves money and cuts down on waste. I’ve reused oil many times without losing quality. It’s an easy way to make your workshop greener and more cost-effective.
Tip: Use good-quality filters. They last longer and clean oil better.
Labor-Saving Jigs for Hand-Finishing Steps
Hand-finishing wood can be time-consuming, especially when you’re working on multiple pieces. That’s where labor-saving jigs come in. These tools have been a game-changer for me. They simplify repetitive tasks, save time, and make sure every piece looks consistent. If you’ve ever struggled to sand edges evenly or apply finishes without streaks, jigs might be your new best friend.
One jig I use often is a sanding block guide. It holds the sandpaper at the perfect angle, so I don’t have to guess. This makes sanding edges or corners much faster and more precise. Another favorite is my finishing rack. It lets me coat multiple pieces at once without worrying about smudging the finish. I just rotate the rack, and everything dries evenly.
Pro Tip: Build your own jigs using scrap wood. It’s cheap, and you can customize them for your projects.
Here’s a quick list of jigs that can make your life easier:
Edge Sanding Jigs: Keep edges straight and smooth.
Clamping Jigs: Hold pieces steady while you work.
Finishing Stands: Prevent smudges and speed up drying.
Template Jigs: Ensure uniform shapes and cuts.
Using jigs doesn’t just save time. It also reduces strain on your hands and wrists. After long hours in the workshop, that’s a big deal. Plus, they help you avoid mistakes, which means less wasted material.
If you’re not using jigs yet, give them a try. Start with simple ones and see how much easier your projects become. Trust me, once you start, you’ll wonder how you ever worked without them! 😊
Customized Finishing for OEM Partnerships
Private Label Packaging for Distributors
Private label packaging helps distributors stand out. It lets them control their brand, prices, and product choices. This makes their products unique and more appealing to customers.
Why is private label packaging useful?
Distributors can create their own brand image.
They can set prices to fit their audience.
Custom designs make their products different from others.
I’ve seen distributors use private label packaging to grow their business. It helped them attract more buyers and compete better. If you work with OEMs, private label packaging is a smart option.
Color-Matching Services for Brand Consistency
Matching colors perfectly is very important for brands. Even small color differences can change how people see a product. I use special tools to make sure colors are always accurate.
Feature | Explanation |
---|---|
Color Pigments | Pigments are organic or inorganic and dissolve in water. |
Instrumental Analysis | Tools like spectrophotometers measure color for exact matches. |
Color Control Standards | Light, reflection, and opacity need strict rules for consistency. |
Monitoring Color Changes | Spectrophotometers catch tiny shifts in color during production. |
Acceptance Testing | Accurate color checks ensure quality before approval. |
Specific Color Limits | Controlled lighting and viewing keep colors within exact limits. |
These tools help keep colors the same across all batches. Customers notice when colors don’t match, so it’s important to get it right every time.
On-Site Treatment Training for Procurement Teams
Training procurement teams improves wood treatment quality. I’ve taught teams how to apply finishes, spot problems, and keep results consistent. These lessons make a big difference.
During training, teams practice using tools and applying finishes. They also learn to find defects early, which saves money and time. By the end, they feel ready to handle the process well.
Pro Tip: Train teams every year to keep skills fresh and learn new methods.
On-site training isn’t just about teaching—it builds trust. Skilled teams help everyone succeed.
Small-Batch Pilot Production for Market Testing
When I first started testing new wood finishes, I didn’t jump straight into full-scale production. Instead, I used small-batch pilot production. It’s a smart way to test the waters without risking too much. If you’re trying out a new finish, design, or treatment, this approach can save you time, money, and headaches.
Here’s why small-batch production works so well:
It’s low-risk: You’re not committing to a large order, so mistakes won’t cost you much.
It’s flexible: You can tweak the process as you go.
It gives real-world feedback: You’ll see how the product performs before scaling up.
I usually start by selecting a small number of wood blocks—just enough to represent the variety in a larger batch. Then, I apply the new treatment or finish. This lets me test how it looks, feels, and holds up under different conditions. For example, I once tested a new stain on 20 blocks. Half went through regular use, while the other half stayed in storage. This helped me see how the finish aged over time.
Pro Tip: Keep detailed notes during testing. Write down what works and what doesn’t. This will save you from repeating mistakes later.
Small-batch production also helps with market testing. I’ve sent samples to a few trusted customers to get their opinions. Their feedback has been invaluable. Sometimes, they’ve pointed out issues I hadn’t noticed. Other times, they’ve loved the product so much that it became a bestseller.
If you’re launching something new, don’t skip this step. It’s like a dress rehearsal for your product. You’ll feel more confident when it’s time to go big. 😊
Long-Term Maintenance Programs for Buyers
Annual Recoating Service Contracts
To keep wood surfaces looking good, regular care is needed. That’s why I suggest yearly recoating service contracts. These contracts make sure wood stays protected and looks great all year. Professionals handle everything, so you don’t have to worry about missing a recoat or using the wrong products.
Outdoor wood needs recoating the most. Weather and use can wear down protective layers over time. A good contract includes cleaning, checking, and adding a new finish coat. This keeps the wood lasting longer and avoids expensive repairs later.
Here’s how regular care helps wood last longer:
Maintenance Task | How Long It Lasts |
---|---|
Use WRP on rough or old wood | |
Reapply every 2 to 4 years after even color | 2 to 4 years |
By following a schedule, your wood will stay strong and look great for many years.
Instructional Video Libraries for End Users
Some buyers like to take care of wood themselves. Instructional video libraries are perfect for this. Clear, step-by-step videos make learning easy. They show how to clean, finish, or check wood for water beading.
For example, one video might teach how to clean wood before adding a finish. Another could show how to test if wood needs retreating by checking water beading. These small steps make a big difference in keeping wood in good shape. Plus, you can watch the videos anytime for a reminder.
Pro Tip: Find videos that focus on tasks like removing mildew or using water-repellent finishes. They’re super helpful when you’re unsure what to do next.
Refinishing Kit Bundles with Purchase Orders
For buyers who want an all-in-one solution, refinishing kits are great. These kits include everything needed to care for wood, like cleaning products and finishes. They’re ideal for DIY buyers who want professional results.
A good refinishing kit should have:
A cleaner to remove dirt and mildew.
Sandpaper or a sanding block to smooth the wood.
A high-quality finish for protection and shine.
These kits save time by giving you all the tools in one package. They also make it easier to stick to a care routine. When everything is ready to use, maintaining wood becomes simple.
Note: Always follow the kit’s instructions for the best results. This ensures your wood stays in top condition.
AI-Powered Wear Prediction for Proactive Care
Have you ever wanted to know when your wood might wear out? AI-powered wear prediction can help! It’s like a smart tool that predicts when wood needs care. This technology uses data to spot wear and tear early, so you can fix problems before they get worse.
Here’s how it works. AI looks at how the wood is used, the environment, and the type of finish. It uses this information to tell you when maintenance is needed. For example, if a butcher block is used daily, AI might suggest recoating it sooner than one used less often. Pretty cool, right?
Pro Tip: Use AI with sensors that check humidity or temperature. This makes predictions even better.
This tool saves time and money by catching small problems early. Fixing issues before they grow keeps wood looking nice and lasting longer. It’s also great for businesses with lots of wood products. Imagine knowing exactly when each piece needs care—no more guessing or wasting materials.
Here’s why AI-powered wear prediction is awesome:
Efficiency: It plans maintenance only when it’s really needed.
Cost Savings: It avoids costly repairs by spotting problems early.
Sustainability: It helps wood last longer, reducing waste.
If you want to take better care of your wood, try this technology. It’s simple to use and makes a big difference. Once you start, you’ll wonder how you managed without it! 😊
Surface treating wood blocks doesn’t have to be complicated. Start by cleaning the surface, ensuring the moisture content is right, and applying the proper finish. Whether it’s oiling, staining, or adding protective coatings, each step adds durability and beauty to the wood.
Remember: Treated wood lasts longer, looks better, and resists damage from wear and weather.
If you’ve been waiting to start your project, now’s the time! Follow these steps, and you’ll create something that stands the test of time. Trust me, you’ve got this! 😊
FAQ
What’s the best way to clean wood before treating it?
I always start by wiping the wood with a damp cloth to remove dust. For greasy spots, I use a mild soap solution. Afterward, I let the wood dry completely. This ensures the finish sticks properly and lasts longer.
How do I know if the wood is ready for finishing?
It’s simple! I check the moisture content using a moisture meter. If it’s between 6-8% for indoor wood or 9-14% for outdoor wood, it’s good to go. Too much moisture can ruin the finish.
Can I use the same finish for indoor and outdoor wood?
Not really. Indoor wood works well with oils or stains. Outdoor wood needs tougher finishes like marine-grade epoxy or UV-stabilized coatings. These protect against weather and sunlight. Always pick a finish based on where the wood will be used.
How often should I recoat treated wood?
It depends on the wood’s use. For outdoor wood, I recommend recoating every 1-2 years. Indoor wood, like butcher blocks, might need a touch-up every 6-12 months. Regular maintenance keeps the wood looking great and protected.
What’s the easiest way to apply oil evenly?
I use a lint-free cloth or a foam brush. First, I pour a small amount of oil and spread it in the direction of the grain. Then, I wipe off any excess. This method avoids streaks and ensures a smooth finish.