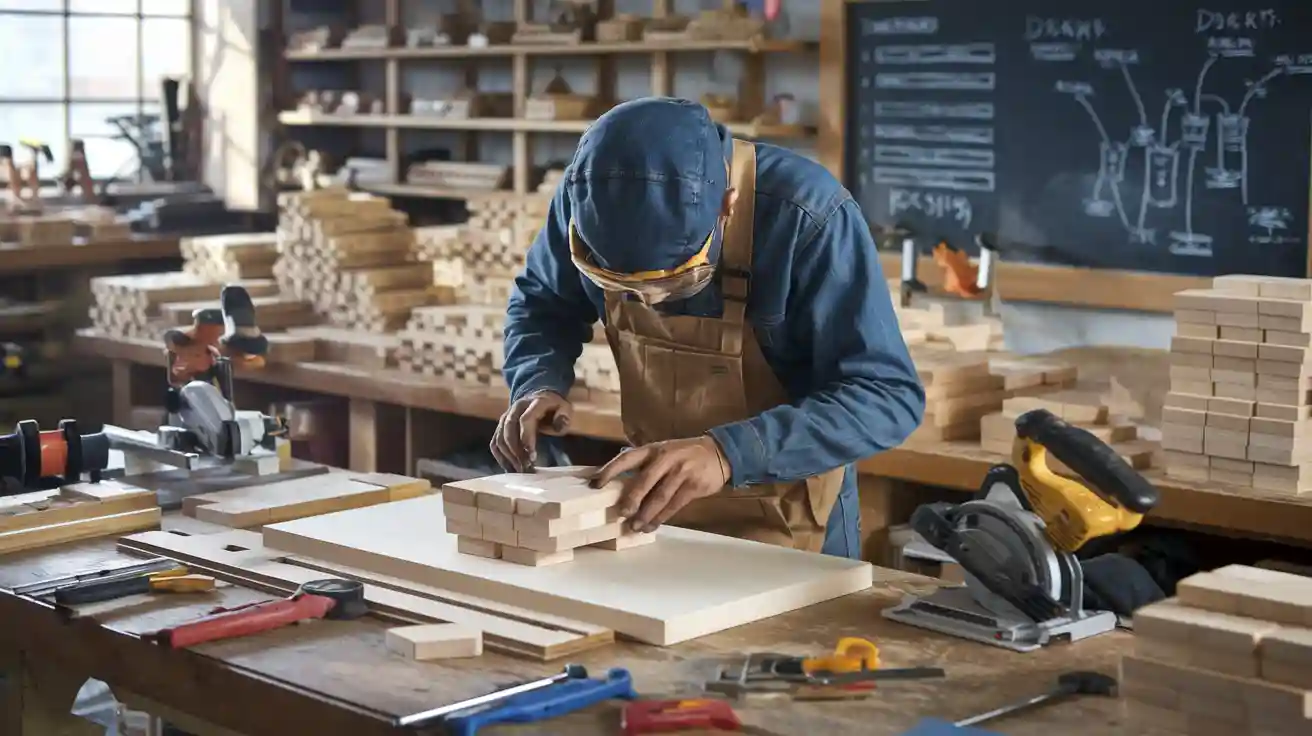
Reducing wood block production costs is very important today. It’s not only about saving money but also building a strong business. Using better materials can save up to $4.57 per pallet. These savings grow quickly, especially in big productions. By implementing the best strategies, such as cutting waste or controlling costs, we can handle high expenses directly. Saving money isn’t just a good idea; it’s key for lasting success.
Key Takeaways
Picking cheaper wood types can cut costs but keep quality.
Using smart production methods reduces waste and saves money.
Working well with suppliers can get discounts and lower prices.
Cutting Material Costs
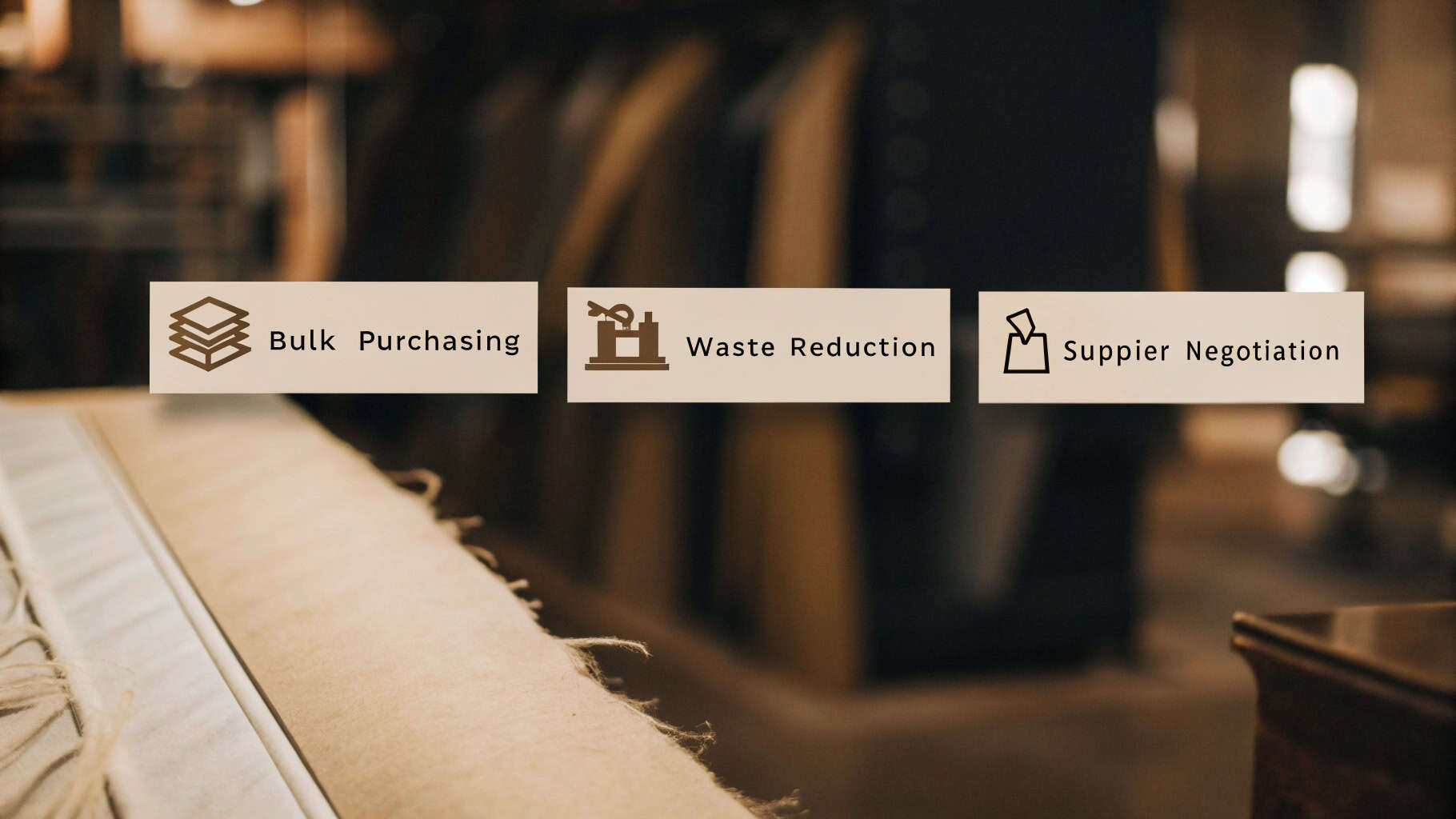
Lowering material costs is a smart way to save money. Here are some simple strategies to cut costs and improve production.
Picking cheaper wood options
The type of wood you use matters a lot. Some woods are cheaper but still work well for pallets. For example, creosote-treated wood costs $9.95 per foot, while concrete alternatives cost over $10.55. Check this table:
Material Type | Material Cost | Installed Cost |
---|---|---|
Creosote-Treated Wood (12#, 40-feet) | $9.95 | $15.60 /l.f. |
Concrete (Precast, Prestressed) | $10.55 | $16.28 /l.f. |
Choosing affordable wood helps save money without losing quality.
Using recycled and eco-friendly materials
Recycled materials save money and help the environment. Studies show they can cut costs by 10% to 20%. For example, recycling aluminum saves 95% of energy costs. These savings grow fast in big productions. Plus, using eco-friendly materials makes your brand look better.
Reducing waste during production
Wasting materials is like wasting money. Cutting smarter and reusing scraps can lower waste. Lean manufacturing removes extra steps, saving time and materials. This method cuts costs and improves how things run.
Buying in bulk with standard materials
Using the same materials makes buying easier and cheaper. Buying in bulk lowers costs and keeps inventory simple. The more you buy, the less each piece costs. Here’s why it works:
Aspect | Description |
---|---|
Economies of Scale | Bigger orders mean lower costs per item. |
Fixed Costs Distribution | Costs spread over more items, lowering the cost per unit. |
Profitability Increase | Lower costs per unit lead to higher profits. |
Standardizing materials and buying in bulk saves money and keeps production smooth.
Process Optimization for Cost Savings
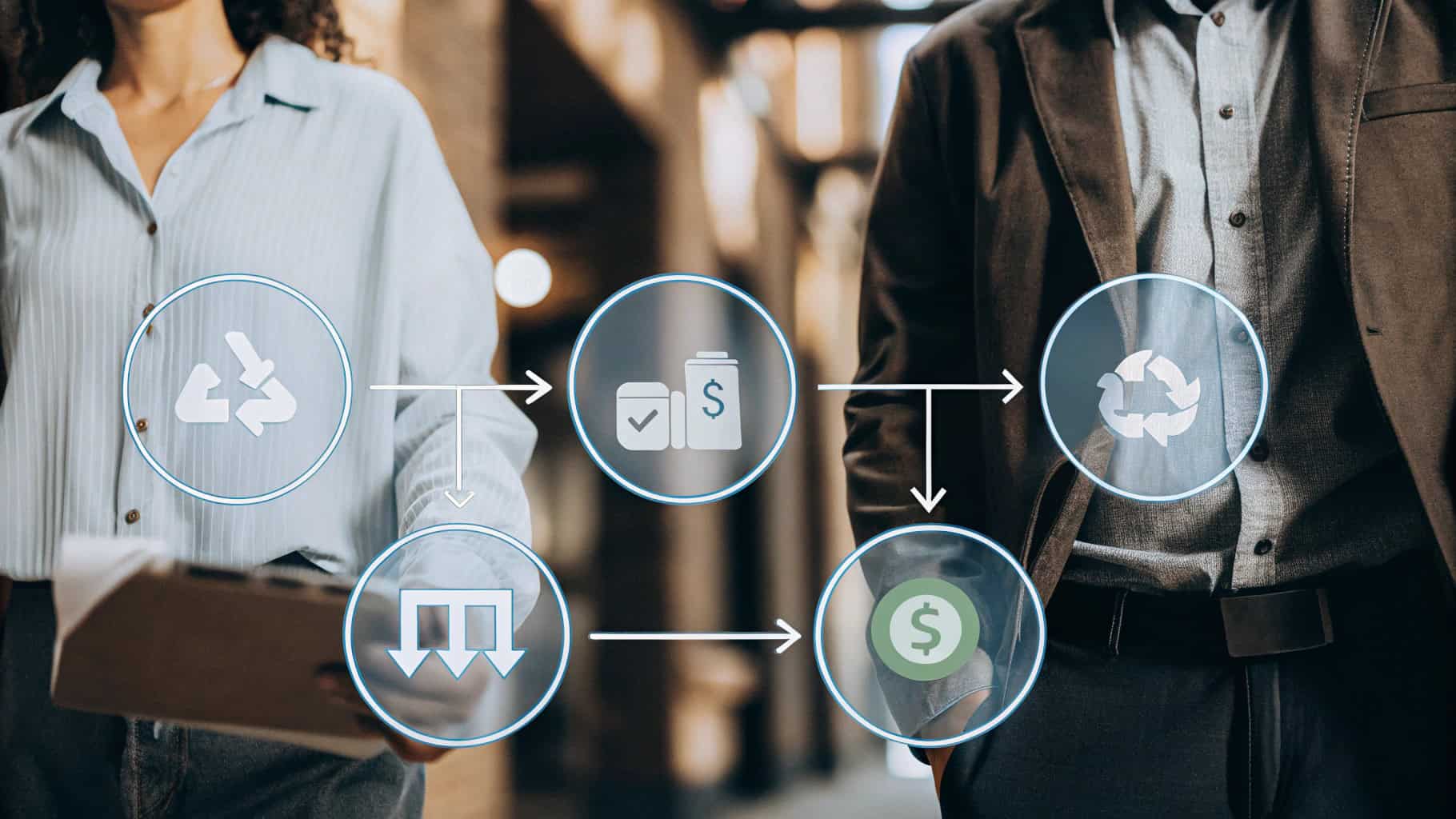
Cutting production costs can be easier with better processes. Here are some simple ways to improve efficiency and save money.
Using lean manufacturing methods
Lean manufacturing means doing more with fewer resources. It removes waste and focuses on useful tasks. Big companies like FedEx and cable makers have seen great results. Look at this:
Example | Before Lean Changes | After Lean Changes | Cost Savings |
---|---|---|---|
FedEx C-checks | 14 checks/year, 32,715 hours/check | 30 checks/year, 21,535 hours/check | Saved money by cutting work hours |
Cable Manufacturing | 5 hours/machine setup | 35 minutes/machine setup | More machine use, lower costs |
These examples show how lean methods save money and improve work.
Fixing cutting mistakes to save wood
Cutting mistakes waste wood and money. Training workers can lower mistakes by 25%. Digital tools also help reduce errors. Fewer mistakes mean saving materials and paying less for labor.
Making workflows smoother for better results
Improving workflows makes production faster and easier. A workflow check finds slow spots and extra steps. As one expert said:
"Checking workflows finds slow spots and shows where automation helps most."
Breaking tasks into smaller parts and automating saves time. It’s about working smarter, not harder.
Adjusting machines for better performance
Don’t forget about your machines. Adjusting their settings can save energy and improve work. Regular checks make sure machines run their best. This is a simple way to cut costs and boost efficiency.
Optimizing Supplier Relationships to Reduce Material Costs
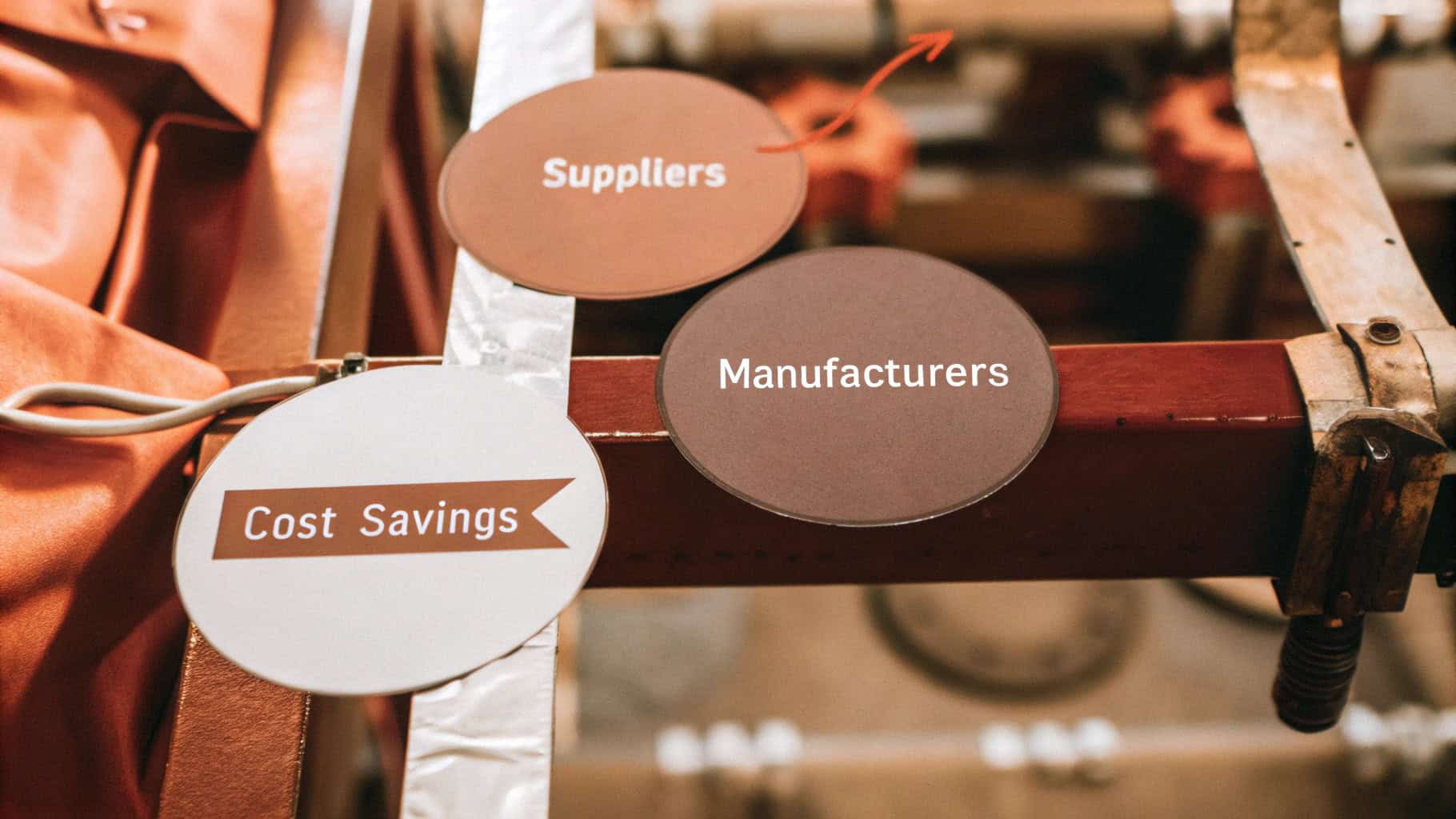
Building good relationships with suppliers helps lower production costs. Here are some simple strategies that work well.
Getting better prices from wood suppliers
Talking to suppliers can save money. Treat them as partners, not just sellers. Ask for discounts when buying more wood at once. This helps both sides and saves money over time. Suppliers like steady buyers and may offer better deals.
Buying wood in bulk during slow seasons
Buying wood at the right time saves money. During off-seasons, demand is lower, and prices drop. Buying a lot of wood then costs less. It also ensures you have enough materials to keep working. This trick has saved me money many times.
Using local wood suppliers to save on transport
Local suppliers can save money and help the environment. Here’s why:
Local suppliers mean lower transport costs.
Less shipping reduces expenses and pollution.
These small changes make production cheaper and greener.
Signing long-term contracts for steady prices
Long-term deals keep prices stable. They protect you from price changes. Suppliers often give better rates for long-term agreements. This helps plan costs and ensures materials are always available. Both sides benefit from trust and steady business.
Tip: Talk openly with your suppliers. Good communication leads to better deals and smoother work.
Leveraging Technology and Automation
Using machines to work faster and better
Buying automated machines has made a big difference for me. They don’t just make pallets faster; they also make them more accurate. These machines help avoid mistakes, saving materials and time. The money saved is huge. Check this table:
Metric | Value |
---|---|
Total system cost | $150,000 |
Current labor costs without robotics | $300,000 |
Anticipated labor costs with robotics | $75,000 |
Labor savings | $225,000 |
ROI in the first year | $75,000 |
Payback period | 2 years |
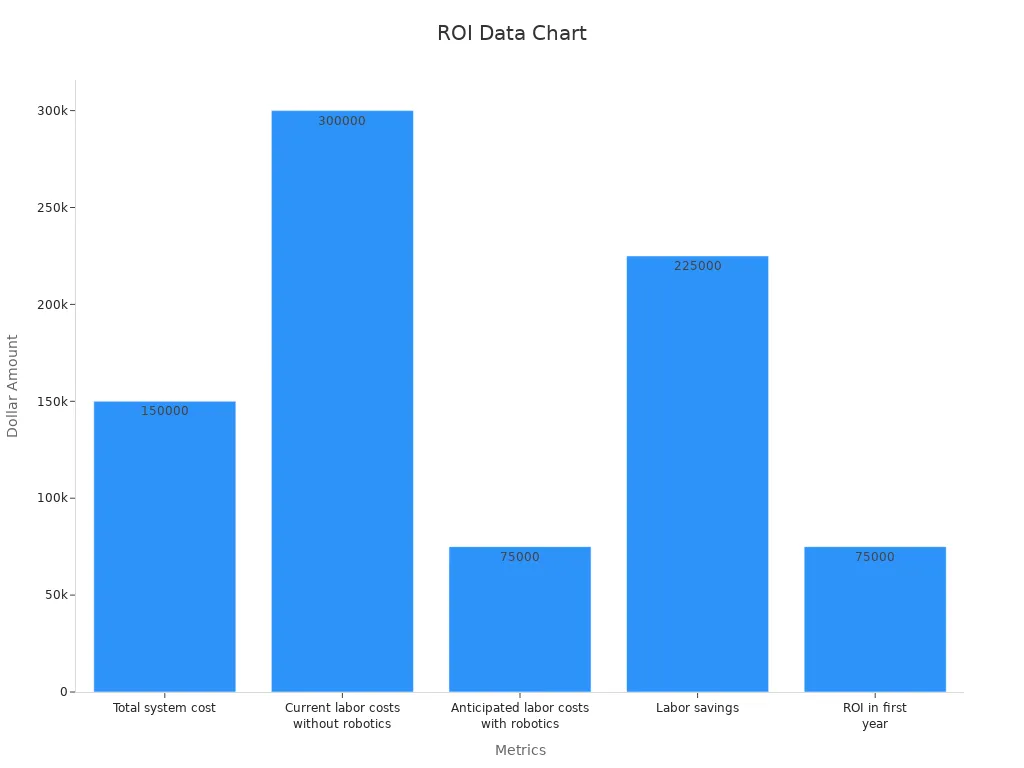
This shows how machines save money and improve production.
Using software to track and improve work
Software tools are like helpers for your factory. They watch machines, collect data, and find ways to work better. For example, they can spot problems early and fix them fast. Here’s what they do:
Feature | Benefit |
---|---|
Real-time data collection | Shows how machines are working right now. |
Overall Equipment Effectiveness (OEE) | Finds where time is being wasted. |
Actionable insights | Helps teams work together to fix problems. |
With these tools, I’ve saved money and made more products. It’s like having a guide to fix issues.
Trying new tools to save on labor
New tools save both time and money. Robotic arms can do simple jobs like stacking pallets. This lets workers focus on harder tasks. Tools like laser cutters also make cuts more exact, wasting less wood. These small changes save a lot of money over time.
Automating checks for better quality
Checking product quality is important but doesn’t need to cost much. Automated systems check for mistakes quickly. They make sure every pallet is good without needing people to inspect. I’ve seen how this saves time and keeps customers happy with great products.
Maintenance and Repairs to Reduce Costs
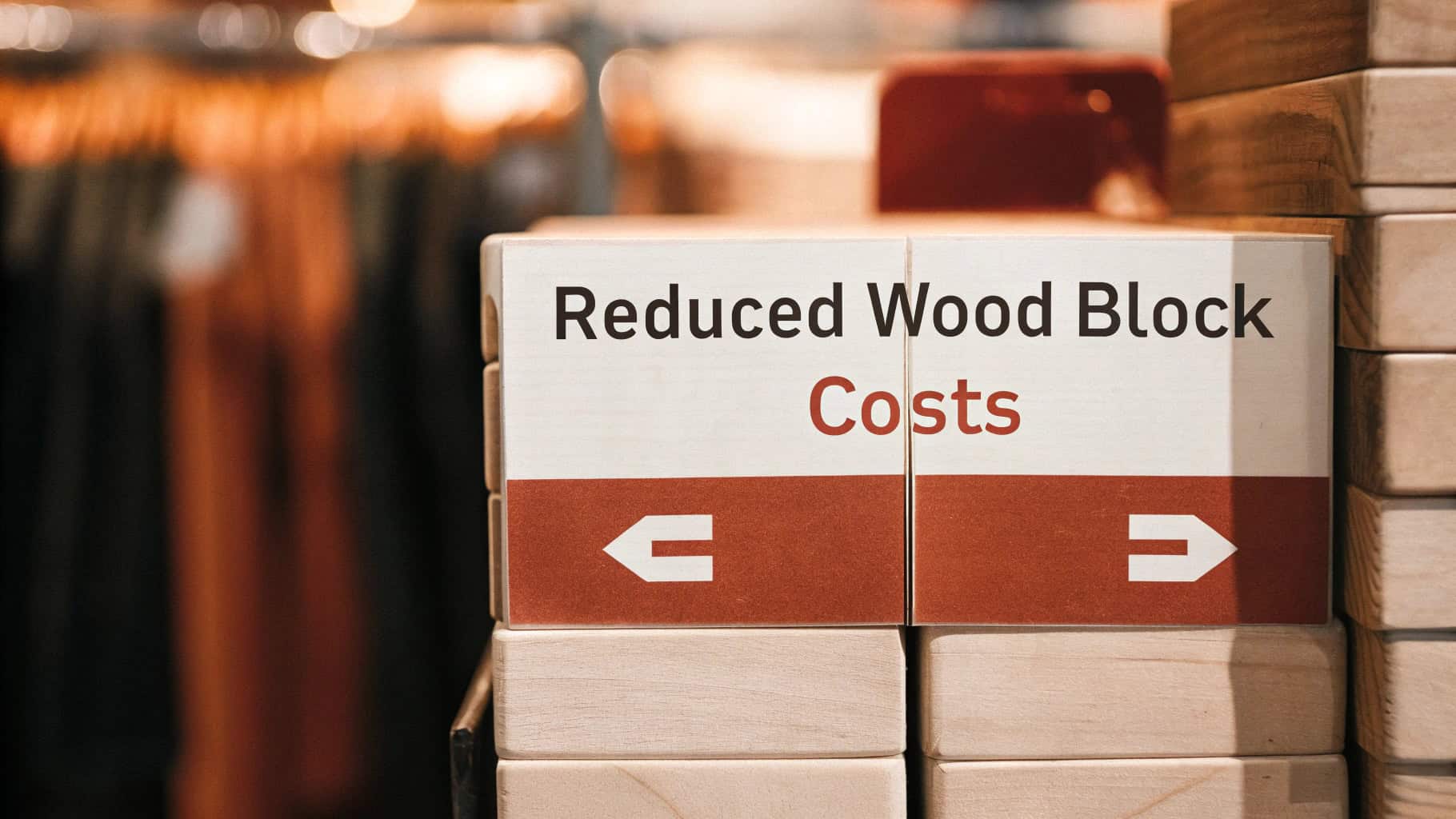
Regular maintenance to keep machines working longer
Taking care of machines is like giving them a check-up. It helps them run well and avoids costly breakdowns. For example, adding oil to moving parts lowers friction. This makes machines last longer and use less energy. Inspections also find small issues before they become big problems. Here’s how maintenance helps:
Benefit | How It Helps |
---|---|
Stops wear and tear | Fixes small problems early to make machines last longer. |
Regular checks | Finds tiny issues before they cause expensive repairs. |
Adding lubrication | Lowers friction, saves energy, and keeps machines running longer. |
Better performance | Makes machines work faster and saves time and materials. |
Following a maintenance plan has saved me money and kept work running smoothly.
Using smart tools to predict problems
Smart tools can tell when a machine might break. This has saved me a lot of money. Studies show it cuts repair costs by 10-40% and downtime by 50%. It also keeps machines ready to work. I’ve saved up to 25% on repairs by using this method. It’s like knowing the future for your machines!
Fixing old machines instead of buying new ones
Buying new machines is expensive. Fixing old ones costs much less. Refurbished machines work just as well as new ones. For example, I fixed a machine for half the price of a new one. It worked great and saved me thousands. Fixing old machines also helps the environment by reducing waste.
Teaching workers to do small repairs
Training workers to fix small problems saves time and money. Instead of waiting for help, they can fix things right away. This keeps work going and avoids delays. It also makes workers more confident and skilled. Spending money on training has been worth it for me.
Energy Efficiency in Production
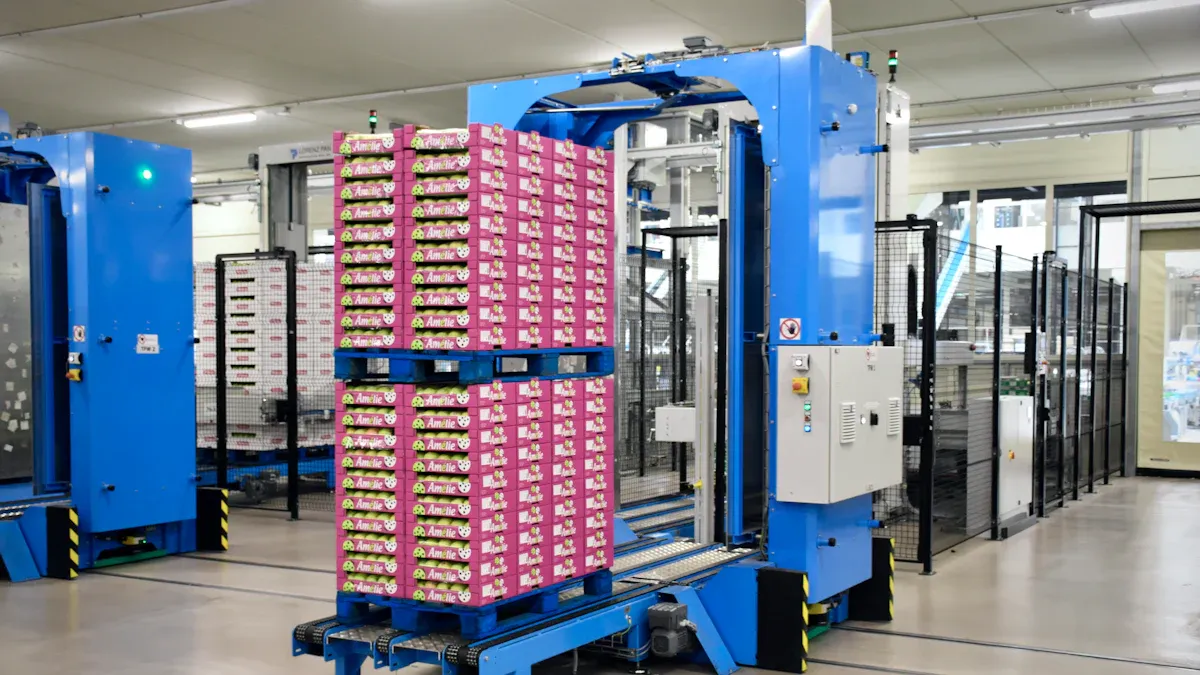
Saving energy during production is a smart way to cut costs. Here are some simple strategies that have worked well for me.
Using energy-saving machines
Switching to energy-saving machines has helped me a lot. These machines use less electricity, lowering power bills. They also break down less often, saving on repairs. Many governments give tax breaks for buying these machines. Here’s why they’re worth it:
Benefit Type | Description |
---|---|
Energy Savings | Cuts electricity bills by using less power. |
Lower Repair Costs | Fewer breakdowns mean less money spent on fixing them. |
Government Support | Tax breaks or grants for choosing energy-efficient machines. |
These machines may cost more upfront, but they save money over time.
Changing work times to save energy
Running machines at off-peak hours saves money on power. I’ve changed my work schedule to use cheaper electricity times. Grouping similar tasks together also helps machines work better. This saves both time and energy without slowing production.
Using systems to manage energy
Energy management systems (EnMS) are like helpers for tracking energy use. They find waste and suggest ways to save power. Studies show companies with EnMS use energy more efficiently. Here’s what the data shows:
Finding | Description |
---|---|
Positive Effect | |
Implementation Status | Companies with EnMS often have fewer chances to waste energy. |
Efficiency Measures | EnMS users are less likely to skip energy-saving steps. |
With EnMS, I’ve saved money by cutting wasted energy.
Trying renewable energy
Renewable energy is good for saving money and the planet. Solar power costs dropped 85% from 2010 to 2020. Wind energy prices also fell a lot during this time. These savings are too big to ignore. Using renewable energy has lowered my costs and made my work more efficient.
Tip: Start small with renewable energy. Even a few solar panels can save money over time.
Labor Cost Reduction Strategies
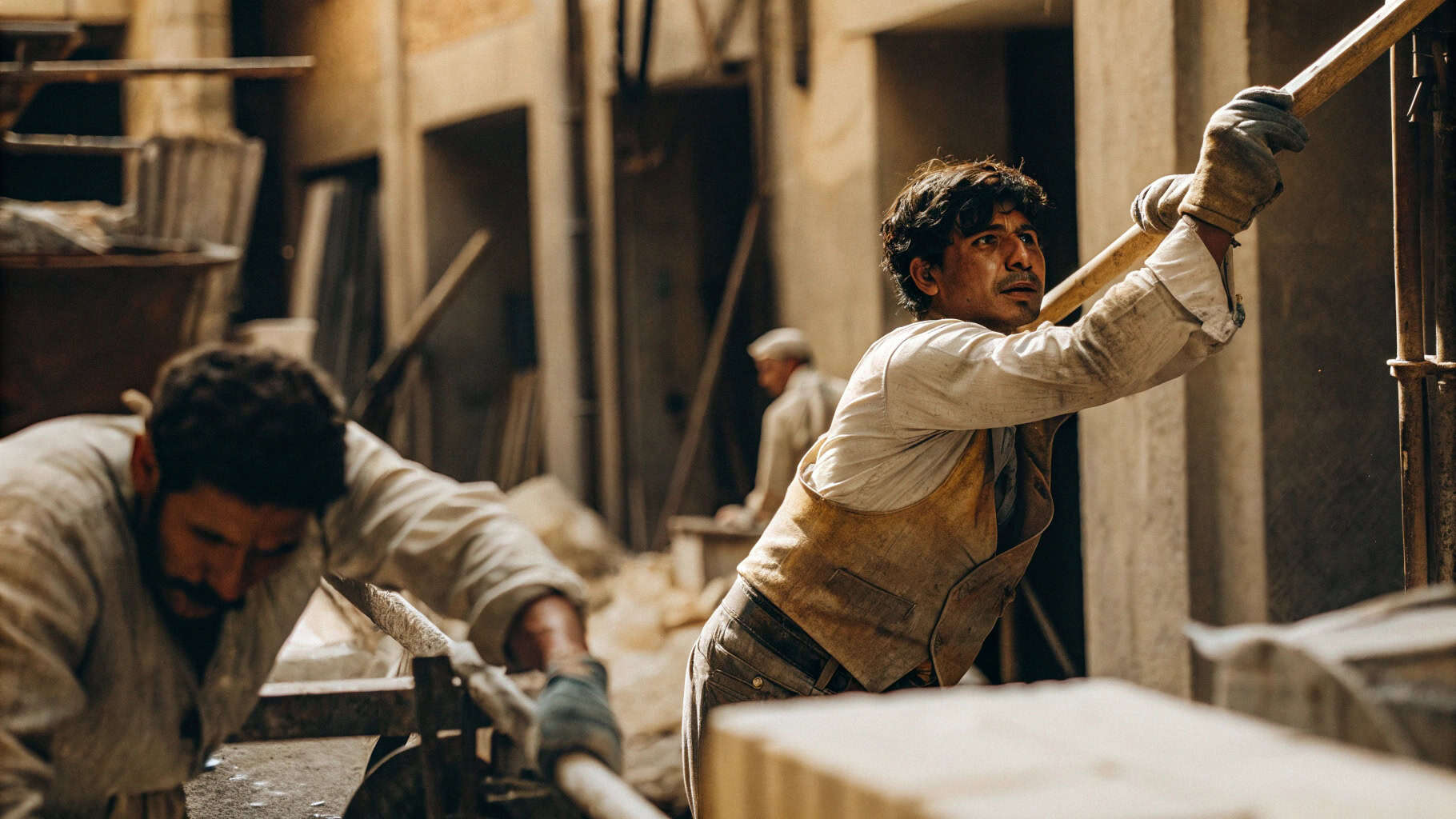
Cutting labor expenses is a smart way to save money. Here are some simple ideas to lower costs while keeping quality high.
Training workers to improve productivity
Teaching workers new skills is worth the effort. When workers know how to use tools well, they make fewer mistakes. They also finish tasks faster. After starting training programs, my team worked quicker without losing quality.
Studies show that skilled workers help companies use resources better. This means making more products without spending more on labor. It’s a win-win—better results and lower costs. Plus, trained workers feel confident, which keeps them happy and reduces quitting.
Using rewards to boost efficiency
Rewards make workers try harder. I started giving small prizes for meeting goals, and it worked great. Workers became more focused and got more done.
Here’s what research says about rewards:
Team rewards can increase work by 44%.
Tasks get done 15% faster with good motivation.
Workers improve by 27% when encouraged to meet goals.
These numbers show rewards aren’t just gifts—they help save money and improve work.
Outsourcing tasks to save time and money
Outsourcing has helped me a lot. By hiring experts for non-core tasks, I’ve saved both time and money. For example, outsourcing office work lets my team focus on production.
Here’s how outsourcing helps different industries:
Industry | Example Task Outsourced | Benefits |
---|---|---|
Technology Sector | Hired others to make computers. | Focused on software, boosting business value. |
Apparel Industry | Sent clothing production overseas. | Grew quickly and made more profit. |
Publishing | Outsourced editing and design work. | Cut costs and finished projects faster. |
Outsourcing lowers costs and makes work smoother.
Planning shifts to avoid overtime
Overtime costs a lot of money. I fixed this by planning shifts better. By checking production needs, I matched shifts to demand. This cut extra hours and saved money.
I also grouped tasks by importance and gave them to the right shifts. Workers stayed busy but didn’t feel overworked. This made production faster and easier. Smart planning beats working harder.
Tip: Use scheduling tools to track hours and stop overtime surprises. It’s an easy way to save money on labor.
Quality Control for Cost Reduction
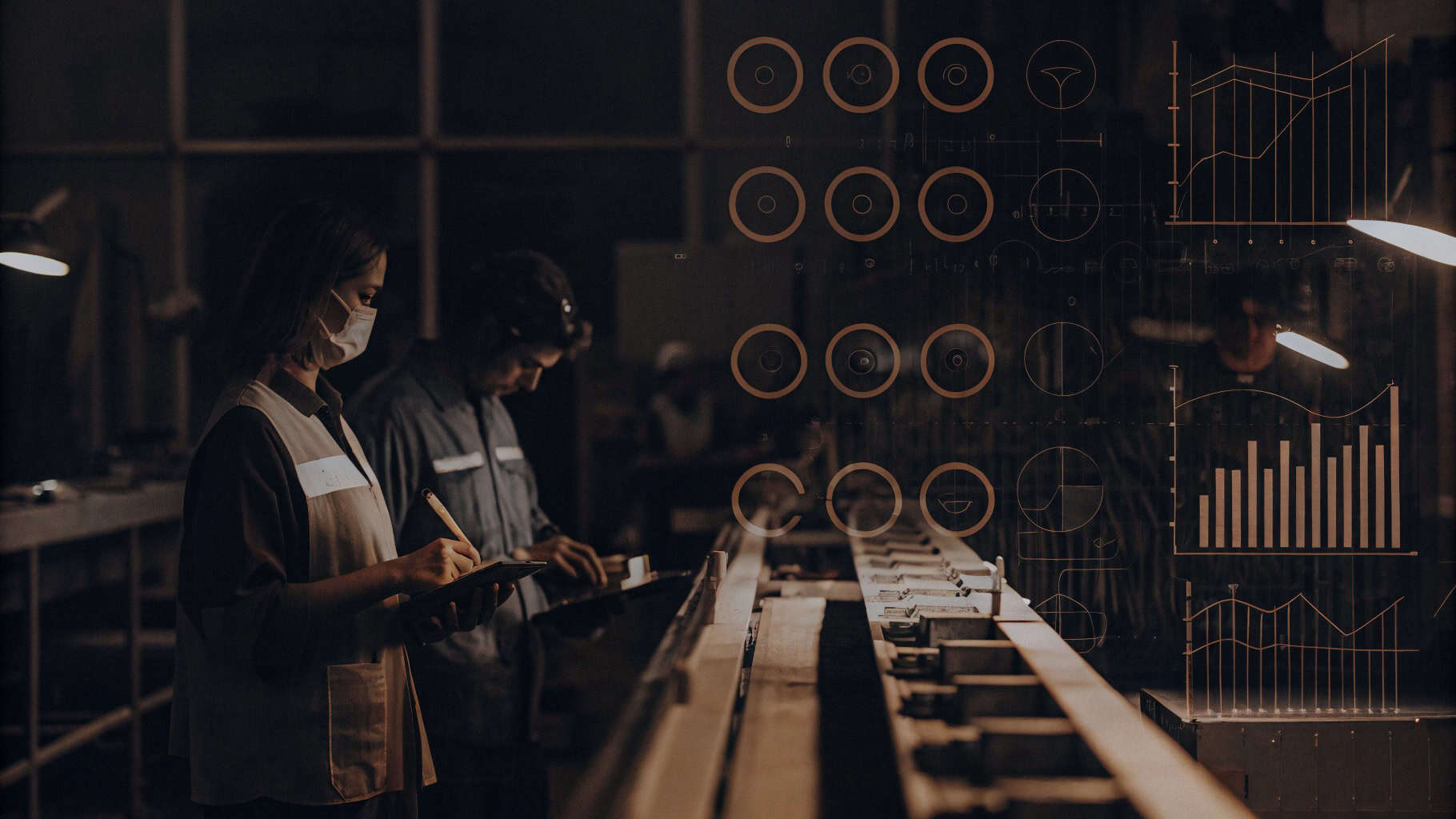
Cutting production costs starts with better quality control. High-quality products mean fewer mistakes and happier customers. Here are some strategies that worked for me.
Using statistical process control (SPC)
SPC is a helpful tool for tracking production. It spots problems early by monitoring processes in real time. For example, I used SPC to check machines and reduced defects by 15%. This method saves money by cutting waste and improving efficiency. Studies show fewer mistakes and happier customers after using SPC. Fixing issues early keeps production smooth and saves costs.
Teaching workers about quality standards
Workers are key to keeping quality high. Training them on standards lowers mistakes and improves results. After training, my team reduced errors by 20%. This saved materials and boosted morale. Workers felt confident, and production became more efficient. Clear expectations lead to better work and fewer errors.
Using automated tools for inspections
Technology makes checking quality faster and easier. Automated tools find defects that people might miss. I’ve used these tools to spot cracks or uneven cuts in wood blocks. The result? Fewer bad products and lower costs. Research shows that investing in these tools prevents failures and saves money. It’s a smart way to ensure every product meets standards.
Cutting rework with better process control
Rework wastes time and money. Improving process control has helped me avoid it. For example, I adjusted machine settings to make cuts consistent, reducing errors by 30%. This saved materials and labor costs. Finding and fixing problems early has been key. Better control improves efficiency and lowers expenses.
Tip: Preventing defects is cheaper than fixing them later. Focus on doing it right the first time.
Efficient Inventory Management
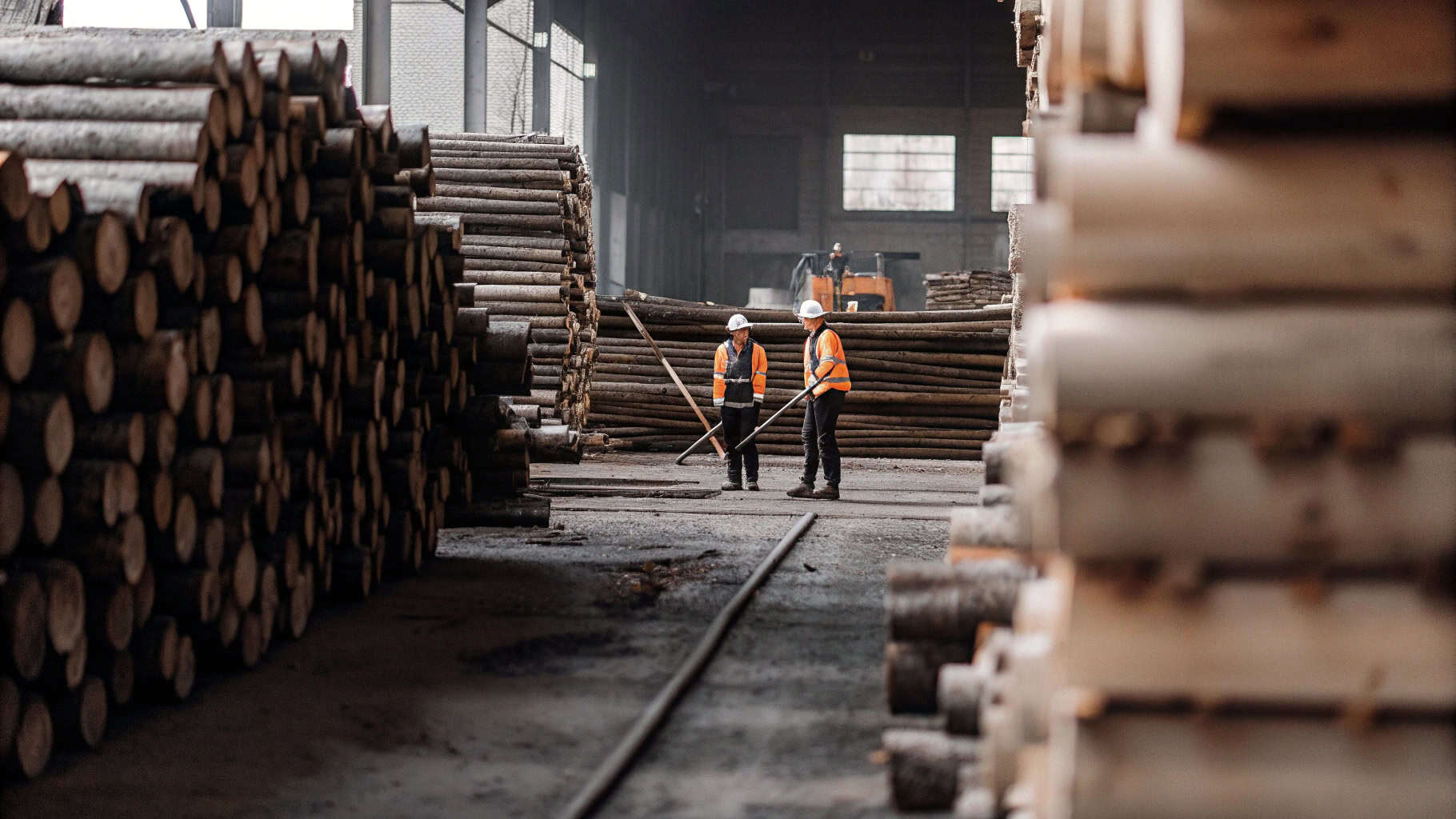
Managing inventory well has saved me money and stress. It’s not just about storing materials but keeping production smooth. Here are some strategies that worked for me.
Using just-in-time inventory systems
Just-in-time inventory has changed how I work. It means keeping only what’s needed when it’s needed. By matching production to orders, I’ve avoided extra stock and saved money. This system cuts waste in areas like:
Transport
Storage
Movement
Waiting
Overproduction
Overprocessing
Mistakes
Unused skills
When I started this, I saved money right away. Production runs better without piles of unused materials.
Switching to inventory software
Tracking inventory by hand was hard. Using software made it simple. These tools track stock, warn about shortages, and stop over-ordering. For example, the software tells me when to reorder materials. This saves time and cuts costs. Plus, having all data in one place helps me decide faster.
Avoiding waste with better forecasting
Forecasting helps me avoid wasting unused materials. By studying past trends and customer needs, I know what to order and when. This stops materials from sitting unused. Forecasting also prevents making too much, saving money. It’s a small step with big results.
Organizing the warehouse for speed
A tidy warehouse saves time and money. I rearranged mine to make supplies easy to find. For example, I put often-used items near the work area. This cut down on searching time. A good setup also reduces wasted movement, making work faster. Small changes made production much smoother.
Tip: Walk through your warehouse and spot areas where time is wasted. Simple fixes can save a lot of money.
Optimizing Transportation and Logistics
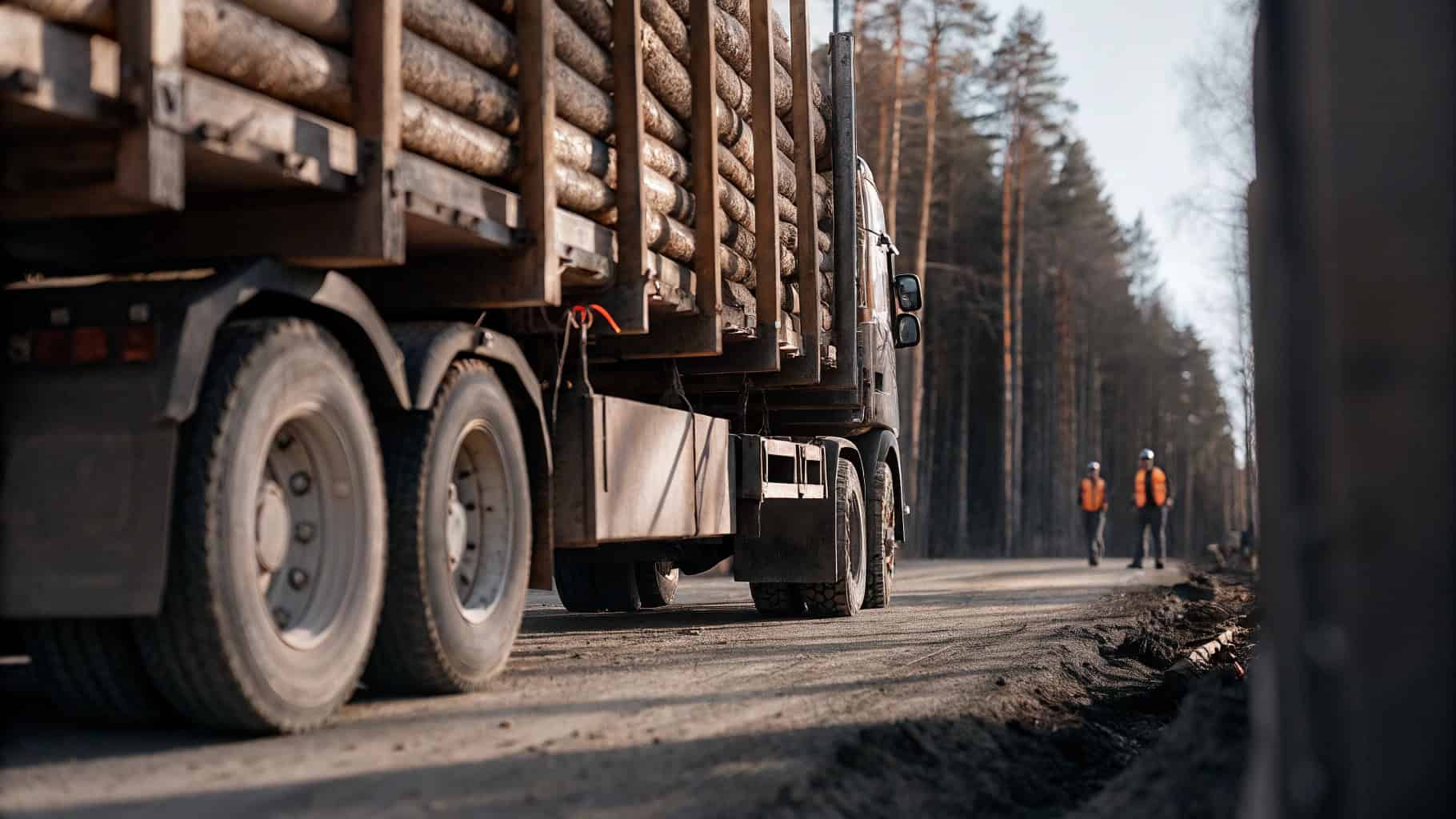
Cutting transportation costs is an easy way to save money. Even small changes in how goods are moved can make a big difference. Here are some strategies that have worked well for me.
Grouping shipments to save money
Sending bigger shipments instead of smaller ones saves money. I started combining weekly shipments into one larger load. This cut my shipping costs by 30%. Fewer trips also mean using less fuel, which helps the environment.
Asking carriers for better deals
Talking to shipping companies can lower costs. I built good relationships with carriers and asked for discounts. Since I ship regularly, they agreed, and I saved hundreds each month. Carriers like steady customers, so it’s worth asking.
Picking cheaper shipping options
Choosing the right shipping method helps save money. For short trips, I use local carriers. For long distances, I pick freight services with bulk discounts. This way, I balance cost and delivery speed.
Planning routes to save time and fuel
Good planning makes deliveries cheaper and faster. I use software to plan routes and schedules. Once, I improved my delivery routes and saved 15% on fuel. Careful planning avoids delays and keeps costs low.
Tip: Check your delivery plans often. Small changes can save a lot of money.
Cutting costs in making wood blocks has helped me a lot. Using smarter processes, better supplier deals, and energy-saving tools saved money. I suggest checking your methods and trying these ideas. Over time, you’ll spend less and save more, which is worth it.
FAQ
How can I reduce wood waste during production?
Reusing leftover pieces and planning cuts carefully helps a lot. Using lean manufacturing also removes extra steps and saves materials.
How do I get better deals from suppliers?
Build good relationships with your suppliers. Always ask for discounts when buying in bulk or signing long-term contracts. Reliable buyers often get lower prices.
Is automation useful for small businesses?
Yes, it is! Automation helps even small businesses by cutting mistakes, saving time, and working faster. Start with simple tools like automated cutters or quality check systems.
Tip: Try one automation tool first. Add more as you save money. Small changes can make a big difference!