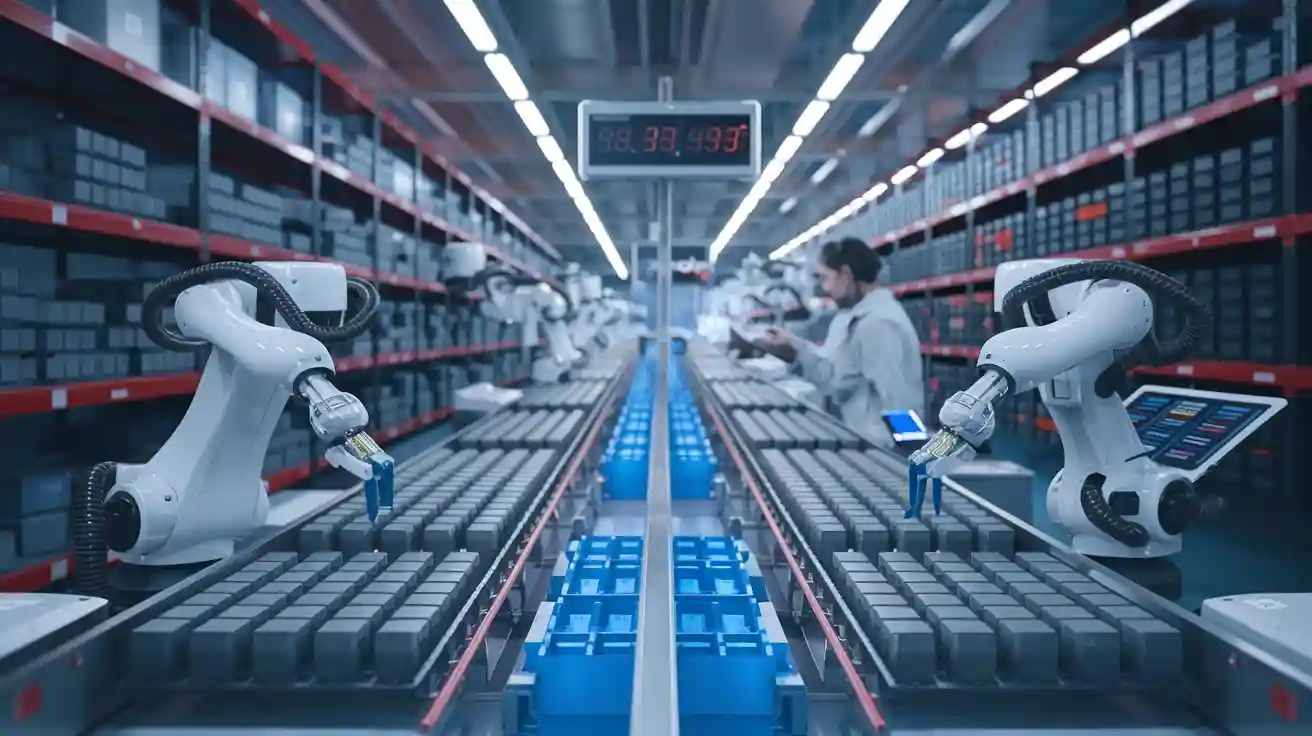
Cutting down lead times for paint block orders is crucial to shorten lead time effectively. Long lead times can slow supply chains, cause delays, and upset customers. To make lead times shorter, we should focus on four main areas:
Supplier Management: Good supplier relationships help improve lead times. Trustworthy suppliers act quickly and keep stock ready, which is essential to shorten lead time.
Process Optimization: Find and fix delays in production and delivery steps. This shortens lead times and makes orders faster, ultimately helping to shorten lead time.
Communication: Clear communication helps the supply chain work better. It’s important for planning inventory and tracking delivery times to ensure we can shorten lead time effectively.
Inventory Planning: Ordering smaller amounts more often lowers risks and speeds up the supply chain, contributing to our goal to shorten lead time.
When we follow these steps, shorter lead times are possible, and the whole supply chain benefits.
Key Takeaways
Create good relationships with suppliers. Reliable suppliers act fast and keep stock ready, helping to save time.
Use tools like smart contracts and AI. These tools make tasks easier, lower mistakes, and speed up orders.
Improve how you manage inventory. Check stock often and use data to guess needs, so you always have the right materials when needed.
Speeding Up Paint Block Delivery with Smart Contracts
Smart contracts are a big help in making paint block delivery faster. They handle tasks automatically, cut down mistakes, and keep things running smoothly. Here’s how they work:
Automating Purchase Orders with Blockchain
Purchase orders (POs) can slow things down. Manual work often causes delays. Blockchain fixes this by automating POs. It keeps everything clear and avoids human mistakes. For example, when a supplier confirms an order, the blockchain updates right away. This helps everyone stay informed and speeds up the process.
Using AI to Predict Demand
Guessing demand is hard, but AI makes it simple. AI tools study data to predict what’s needed. This helps us keep the right amount of stock. It also prevents running out or having too much. Did you know AI can cut product shortages by 65%? That means happier customers. Studies show AI reduces mistakes by 20-50%. This leads to fewer missed sales and quicker deliveries.
Linking Payments to Milestones
Payments can slow things down too. Smart contracts fix this by tying payments to progress. For example, when a shipment reaches a step, payment happens automatically. This keeps suppliers motivated and deliveries on time. Everyone benefits from this system.
Faster Quality Checks with Smart Contracts
Quality checks are important but take time. Smart contracts make this faster by automating checks. They confirm quality instantly, so we skip manual inspections. This ensures every batch is good before moving ahead.
Accurate Inventory Management Solutions
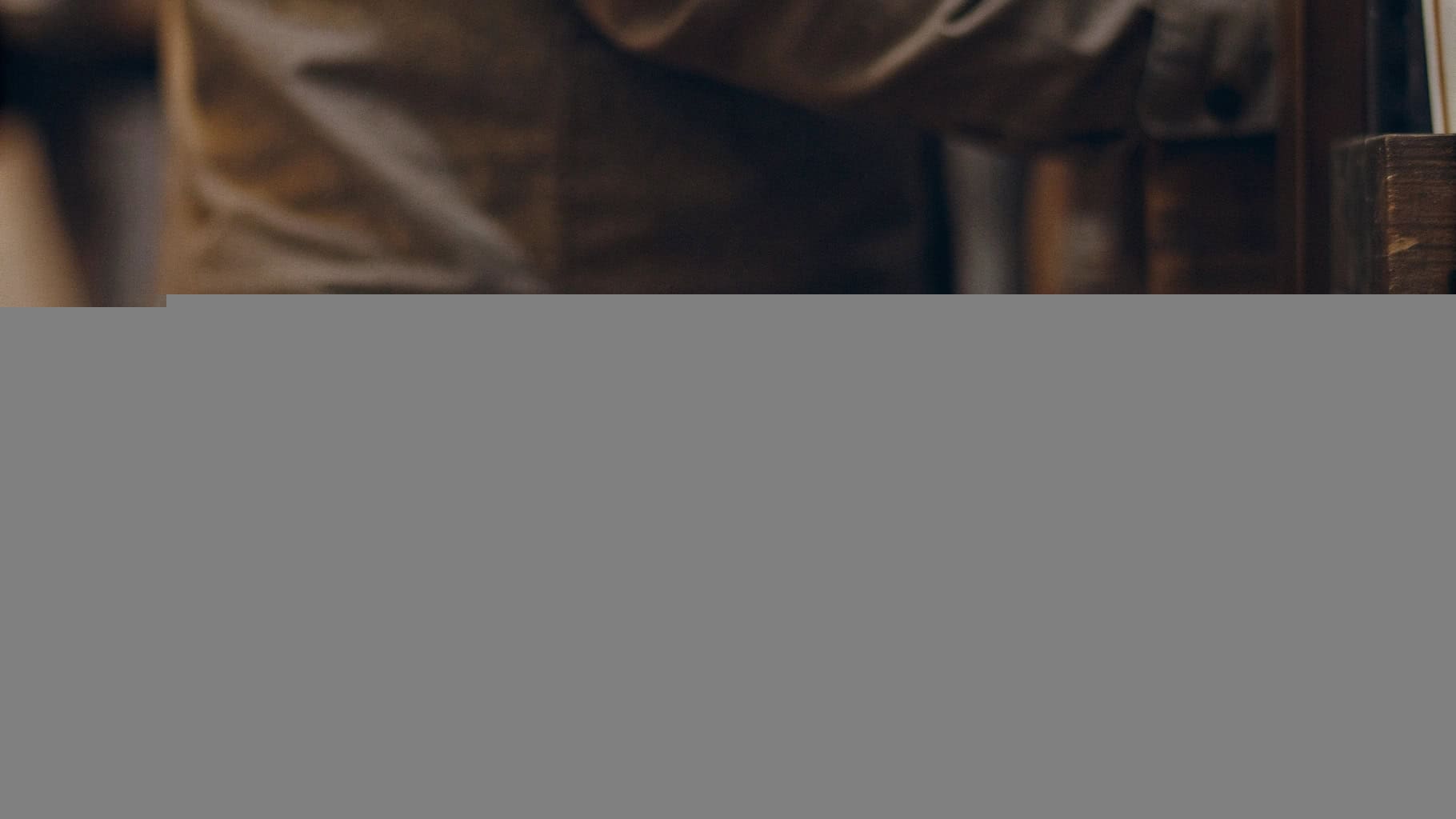
Managing inventory well means being precise. Small changes can make a big impact. Let’s explore some smart ideas to improve inventory management.
IoT Devices for Tracking Materials
Think about always knowing where your materials are. IoT devices make this possible. They use sensors to track materials live. No more waiting or guessing. If there’s a delay, you can act quickly. This also prevents running out of stock and keeps production steady.
Sharing Stock Between Plants
What if plants shared their supplies? It’s a smart idea. Sharing stock between plants helps when one runs low. This avoids delays and keeps orders on time. Companies using this method often deliver faster and use resources better.
AI Tools for Buffer Stock
Too much stock wastes money, but too little causes problems. AI tools fix this by finding the right stock levels. They study data to suggest how much to keep. This way, you’re ready without overstocking. It saves money and boosts efficiency.
Live Material Usage Tracking
Watching how materials are used in real time is helpful. Live tracking shows patterns and spots issues early. For instance, if something is used up too fast, you can reorder sooner. This keeps everything running smoothly.
Did you know automating inventory can cut lead times? Switching from manual to smart systems speeds up orders and improves supplier ties.
Multimodal Logistics Optimization Models
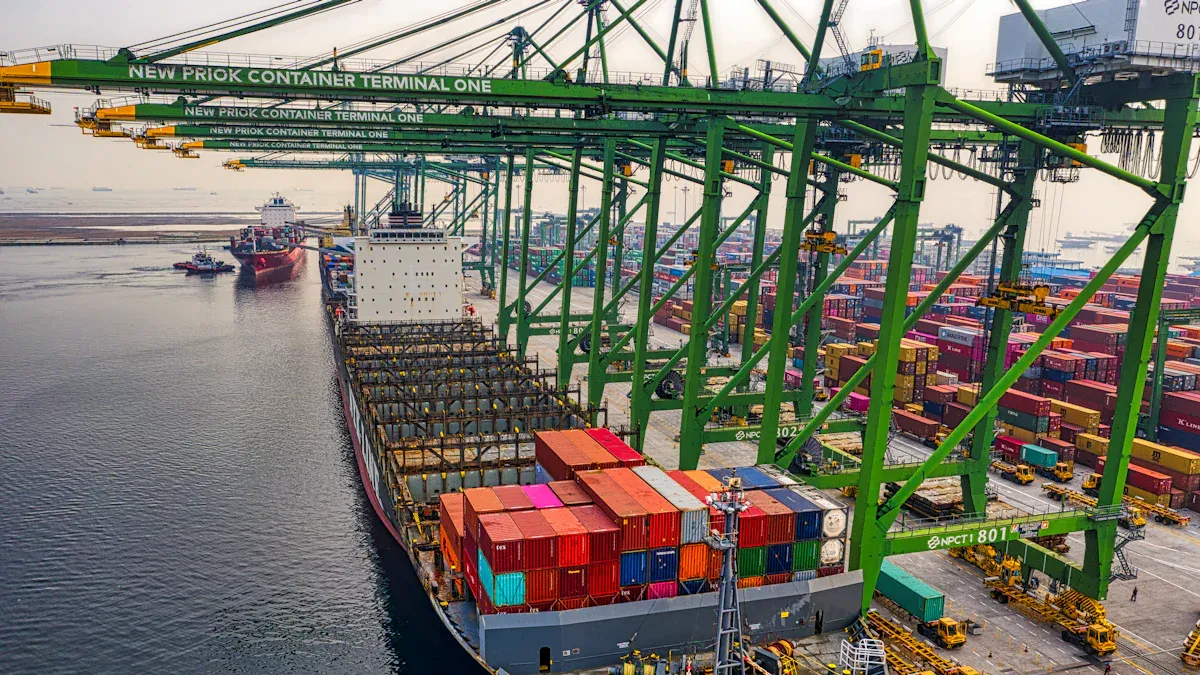
Logistics is key to faster deliveries. Better planning saves time and money. Here are some smart ways to improve logistics.
Predicting Port Delays with Algorithms
Shipments stuck at ports can be annoying. Predicting delays helps avoid this. Smart tools check traffic, weather, and schedules. They warn us about problems early. This way, we can change routes or plans. It’s like knowing the future of shipping!
Packing Containers Efficiently
Shipping containers need smart packing to save space. Bulk container optimization uses every inch wisely. This is useful when demand changes quickly. For smaller shipments, LCL shipping works well. Here’s a simple table:
Aspect | Details |
---|---|
Market Type | |
Key Insights | Saves money for smaller shipments |
Data Provided | Info by company, region, and type |
Market Trends | Tracks supply and demand changes |
Future Projections | Predicts market shares for 2025 |
Packing better lowers costs and speeds up shipping.
Analyzing Air Freight Costs
Air freight is fast but expensive. Cost analysis helps find cheaper options. Comparing routes and carriers saves money. This way, we meet deadlines without overspending.
Automating Customs Pre-Clearance
Customs can slow things down. Automation fixes this by submitting forms early. Digital systems reduce border delays and mistakes. This makes international shipping much faster.
Tip: Use these ideas together for better logistics. Faster shipping means happy customers and smoother operations.
AI-Optimized Production Scheduling Systems
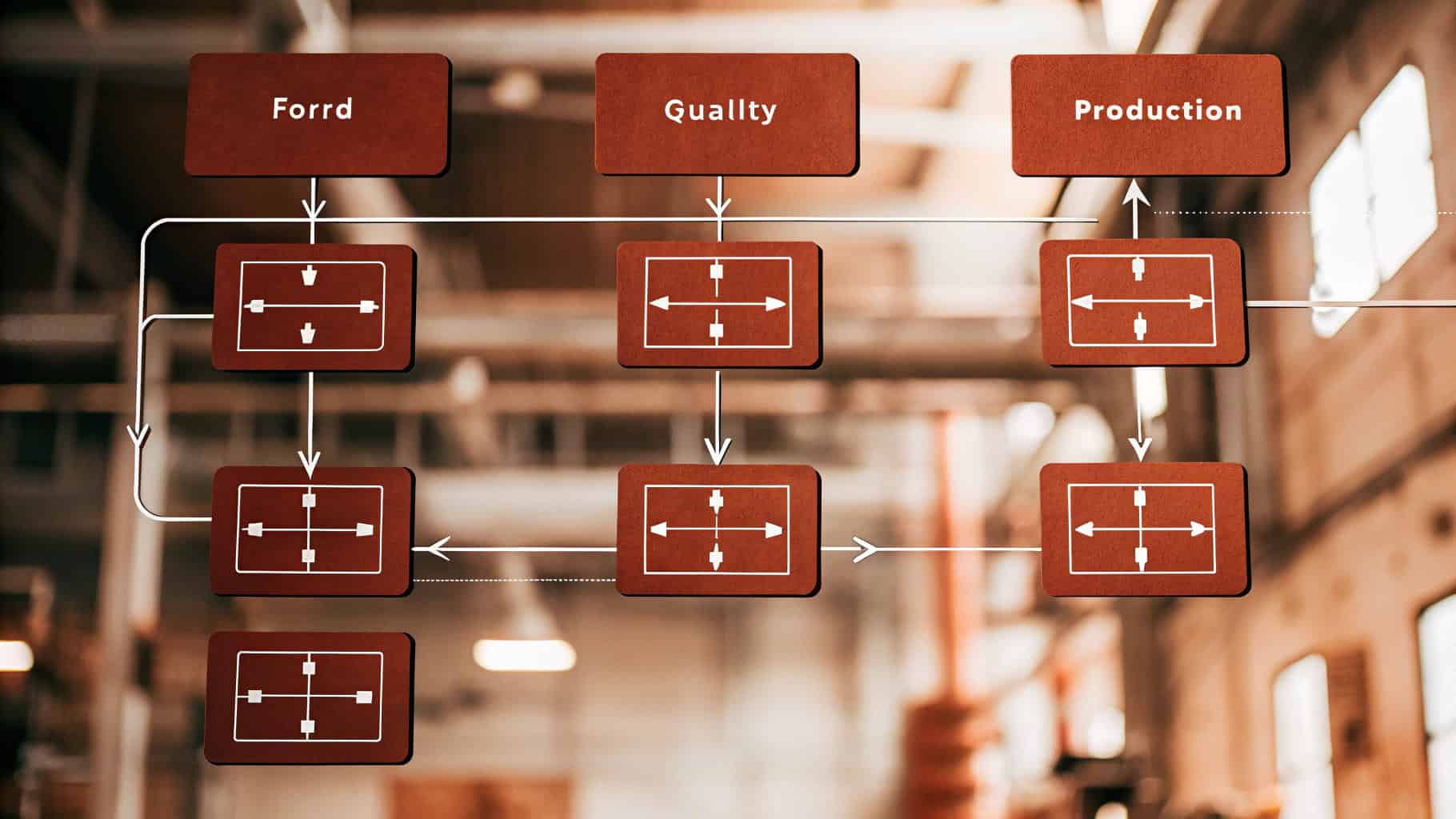
AI tools can make production faster and easier. They help plan better, reduce delays, and keep things running well. Let’s look at how AI improves production scheduling.
Machine Learning for Task Switching
Changing tasks during production can be hard. Machine learning studies past data to find quicker ways to switch tasks. It suggests the best order to save time. This means less waiting and more products ready faster.
Energy-Saving Batch Planning
Energy costs can be high. AI helps by grouping similar tasks to save energy. This lowers costs and makes production better for the environment. It’s good for both the planet and your wallet.
Live Machine Performance Tracking
Watching machines in real time is important. AI tools show how machines are working right now. They track things like how many items are made and how long machines run. Here’s what they measure:
Measure | What It Tracks |
---|---|
Items Made | How many products are created during a production run. |
Finished Products | The number of completed items from a machine or line. |
Machine Running Time | Minutes a machine works, showing any stops. |
Time Between Breakdowns | Average time between machine problems. |
Repair Time | How long it takes to fix or maintain equipment. |
These tools help make better products, reduce waste, and speed up production. They also keep customers happy and save money.
Predicting Repairs Before Problems Happen
Broken machines can cause big delays. AI predicts when repairs are needed before things break. It plans fixes during slow times, so work doesn’t stop. Studies show AI can cut surprise breakdowns by 50%. This saves time, money, and keeps machines working longer.
Tip: Use these AI tools together for faster and smoother production. It’s like having a smart helper for your factory!
Global Supplier Risk Management Plans
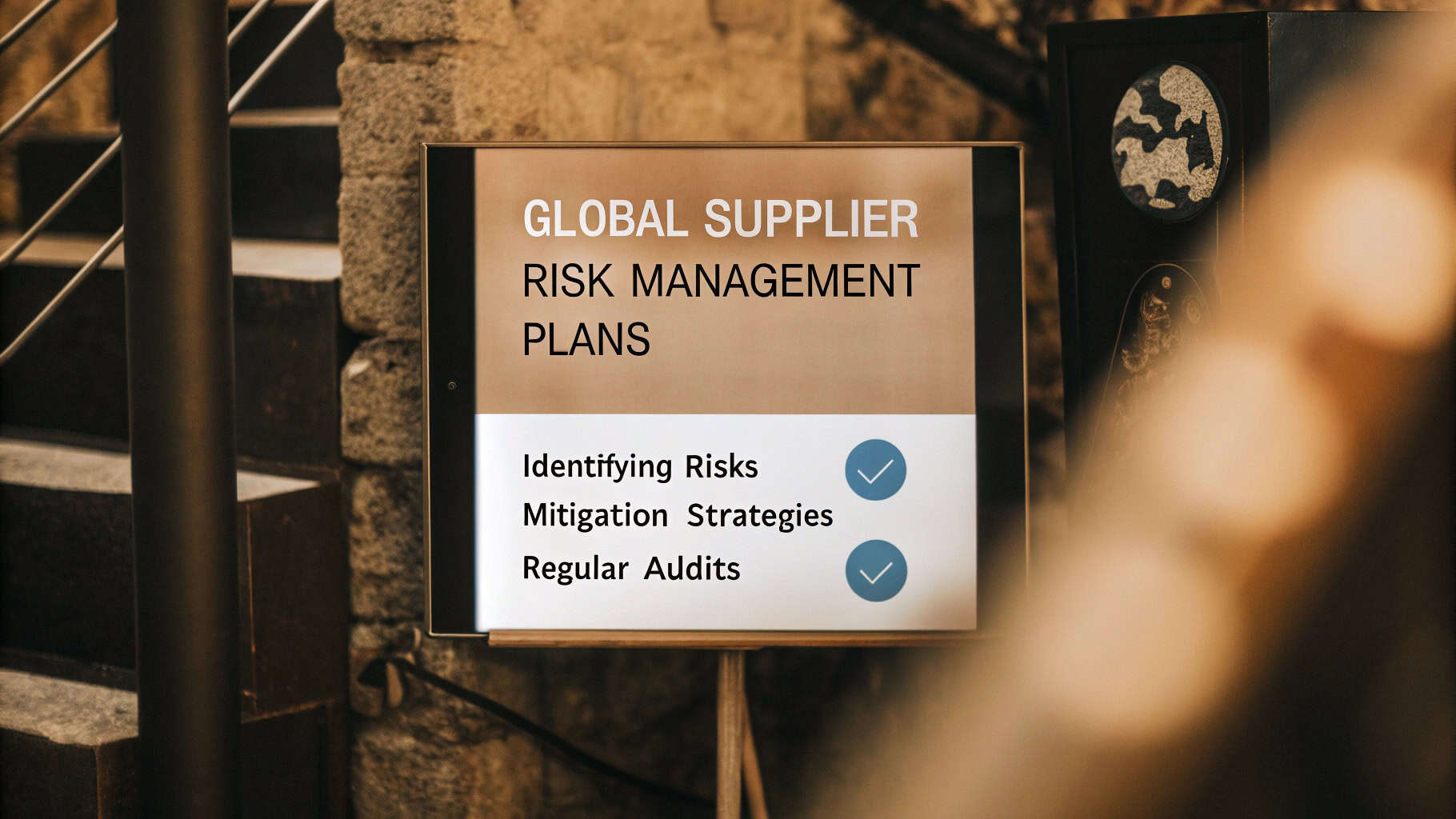
Managing supplier risks needs a strong plan. A good plan saves time and avoids problems. Here are some helpful strategies.
Checking Geopolitical Stability
World events can mess up supply chains. Stability tools check things like politics, trade, and money issues in supplier areas. These scores help decide if a supplier is safe to use or if we need a new one. It’s like a risk weather report for suppliers.
Having Backup Suppliers
Using only one supplier is risky. It’s better to have backups. This means finding another supplier for important materials. If one has delays, the other can help. This makes operations smoother and faster. Reliable suppliers handle surprises better.
Watching Supplier Finances
A supplier’s money situation shows how dependable they are. Dashboards track important numbers like profits and debts. Here’s a table of what I check:
Metric | What It Shows |
---|---|
Profitability Ratios | How well a supplier earns compared to sales or assets. |
Net Profit Margin | The percent of sales kept as profit after costs. |
Return on Assets (ROA) | How well a supplier uses assets to make money. |
Return on Equity (ROE) | How much profit comes from the owner’s investment. |
Solvency Ratios | If a supplier can handle long-term debts. |
Debt-to-Equity Ratio (D/E) | How much debt a supplier has compared to owner’s money. |
Debt-to-Assets Ratio | The part of assets paid for with debt. |
Interest Coverage Ratio | If a supplier can pay interest on debts with their profits. |
These numbers help spot problems early and avoid trouble.
Planning for Emergencies
Big problems like storms or strikes can stop work. Emergency plans help suppliers deal with these issues. These plans explain how to reduce delays and keep things moving. Being ready for surprises is key.
Tip: Use all these ideas together to cut supplier delays and work better.
Real-Time Supply Chain Visibility Platforms
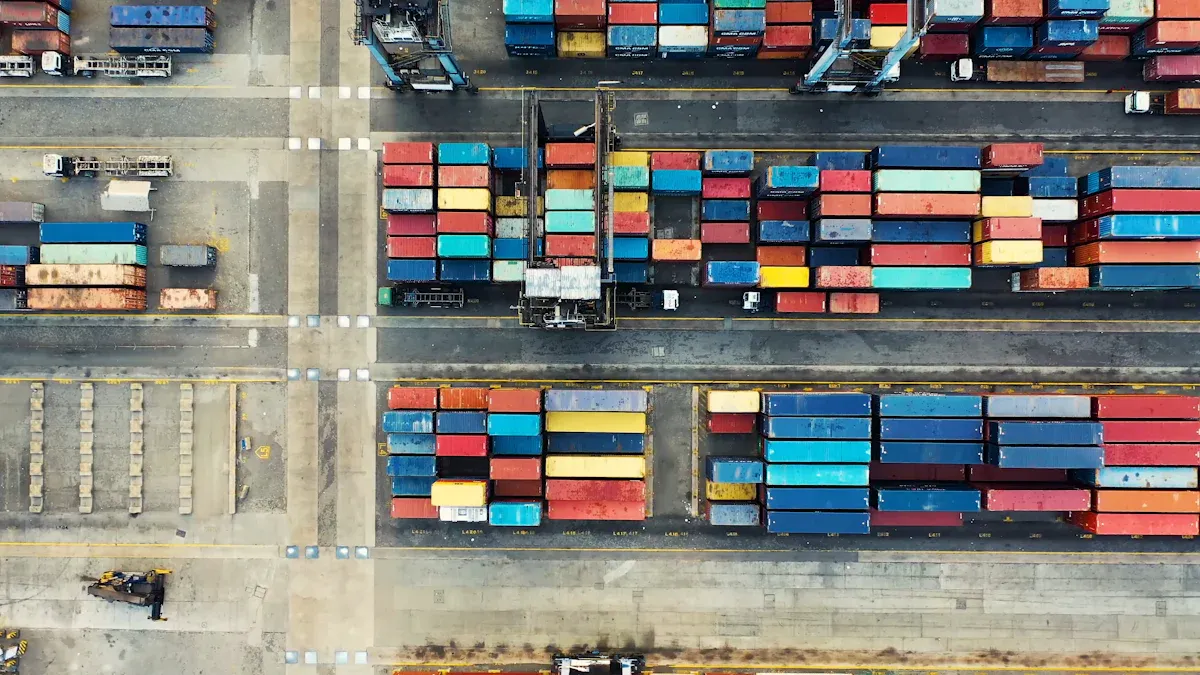
Tracking every part of the supply chain is like seeing everything from above. Real-time tools make this easy. They help find delays, work faster, and keep customers happy. Let’s look at some cool technologies.
Shipment GPS Heatmap Analytics
Do you ever wonder where your shipments are? GPS heatmaps show their exact location. They give live updates on trucks and loads. This helps us plan better. For example, brokers can see free trucks and change routes to avoid problems. Here’s what these tools do:
Feature/Benefit | Description |
---|---|
Updates constantly to show the latest truck locations. | |
Market Insights | Helps brokers understand truck demand and availability. |
Performance Metrics | Lets brokers compare their work to market averages. |
Resource Allocation | Shows where to focus, like finding more loads or carriers. |
These tools make the supply chain smoother and easier to manage.
Factory Floor IoT Data Streams
Imagine knowing what’s happening in a factory without being there. IoT devices make this possible. They collect live data from machines and workers. This helps us fix problems fast. For example, if a machine slows down, we can fix it right away. This keeps everything running smoothly.
Supplier Production Progress APIs
Guessing supplier progress is now a thing of the past. APIs give live updates on production timelines. This has changed how we work with suppliers. Here’s what’s improved:
No more overtime. Efficiency went up, and costs went down.
Workers are happier, and fewer people are leaving their jobs.
APIs make the supply chain faster and more dependable.
Customs Clearance Status Trackers
Customs delays used to be a mystery. Now, clearance trackers give live updates. They show where shipments are in the customs process. If there’s a delay, we know right away and can act fast. This saves time and keeps things moving.
Tip: Use all these tools together for a better supply chain. Real-time updates mean fewer problems and happier customers.
Green Ways to Speed Up Paint Block Orders
You can speed up paint block orders and still care for the planet. Here are some eco-friendly ideas to save time and help the Earth.
Natural Drying Boosters
Have you heard of natural drying boosters? They help paint dry faster without using harmful chemicals. Some companies have cut drying times by 30% with these. They’re safer for workers and better for the planet. It’s a smart and green choice!
Quick-Dry Low-VOC Paints
Waiting for paint to dry is no fun. Quick-dry low-VOC paints dry faster and release fewer bad fumes. These are great for reducing wait times and keeping the air clean. Customers like them because they’re safe indoors. Why not try them out?
Tools for Recycled Material Timing
Recycled materials are great but can cause delays. Timing tools help predict when recycled materials will arrive. These tools use data to avoid slowdowns and keep production steady. It’s like having a smart helper for your inventory.
Cleaner Shipping Routes
Shipping doesn’t have to harm the planet. Cleaner shipping routes use better fuels and reduce pollution. Companies using these routes often face fewer delays. It’s a green way to keep deliveries on time.
Tip: Use these ideas together for faster, eco-friendly deliveries. You can save time and help the planet too! 🌍
Predictive Quality Assurance Systems
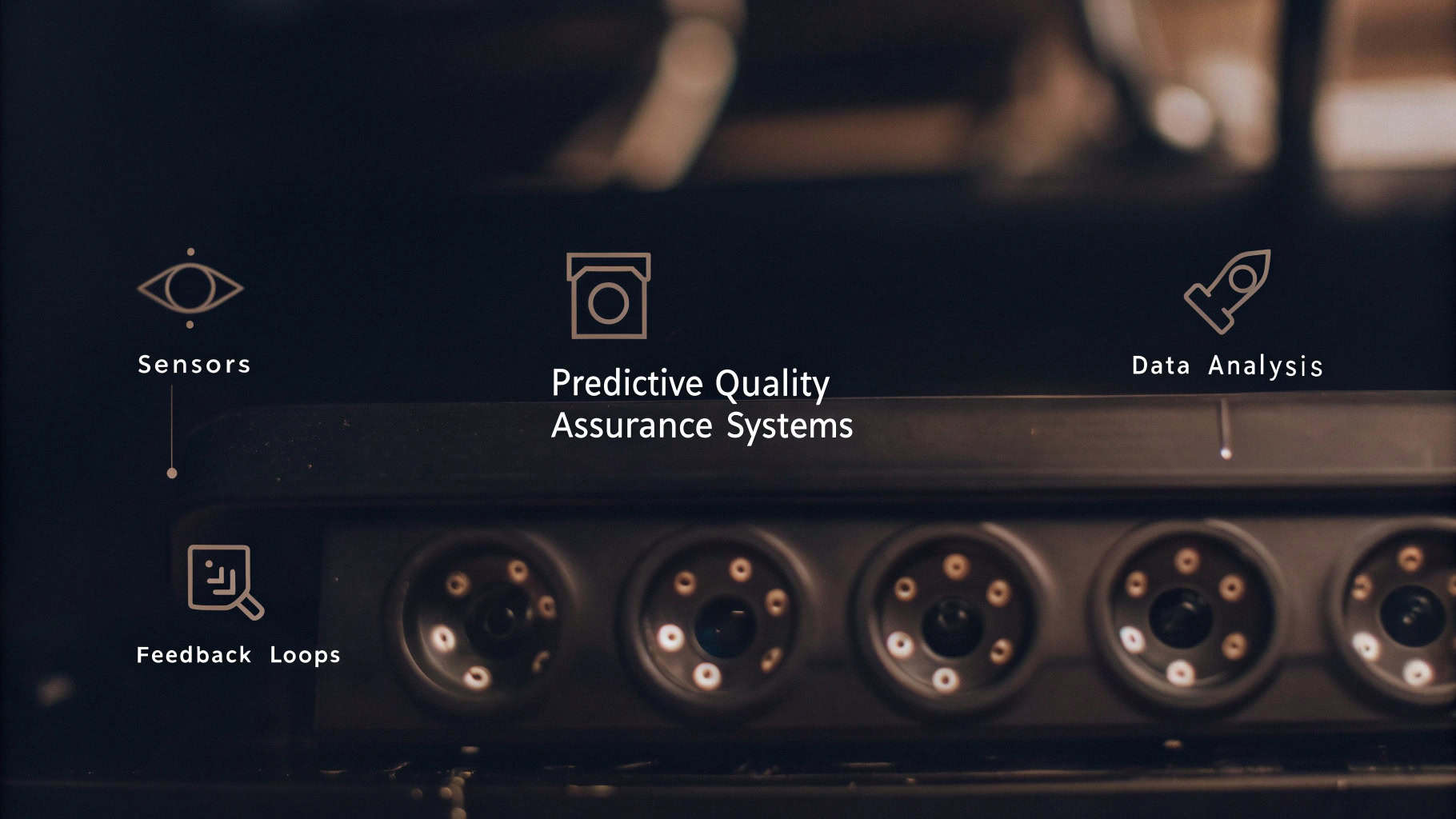
Predictive quality systems help improve product quality. They find problems early and fix them fast. Here are some tools that make this happen.
Spotting Defects with Light Scanners
How do we find tiny flaws in paint blocks? Light scanners use special technology to detect defects invisible to the human eye. This method works quickly and ensures products meet high standards. It saves time and improves accuracy. Think of it as a super tool for quality checks!
Robots for Batch Testing
Manual batch testing takes time and can miss mistakes. Robots handle this job better. They pick samples and test them with great precision. Robots don’t get tired or make errors. They speed up testing and let workers focus on other tasks.
AI Tools to Predict Rejection Rates
AI tools study past production data to predict rejection rates. They help adjust processes to avoid defective products. Real-Time Release Testing (RTRT) checks quality during production and catches issues instantly. This has reduced defective items in many factories.
Fixing Defects with Smart Algorithms
Fixing defective items can be tricky. Smart algorithms make it easier by finding the fastest way to repair them. They organize tasks and use resources wisely. This reduces delays and gets products ready faster. Everyone benefits from this system.
Predictive quality systems don’t just fix problems—they stop them before they start and ensure great products every time.
Collaborative Capacity Planning Networks
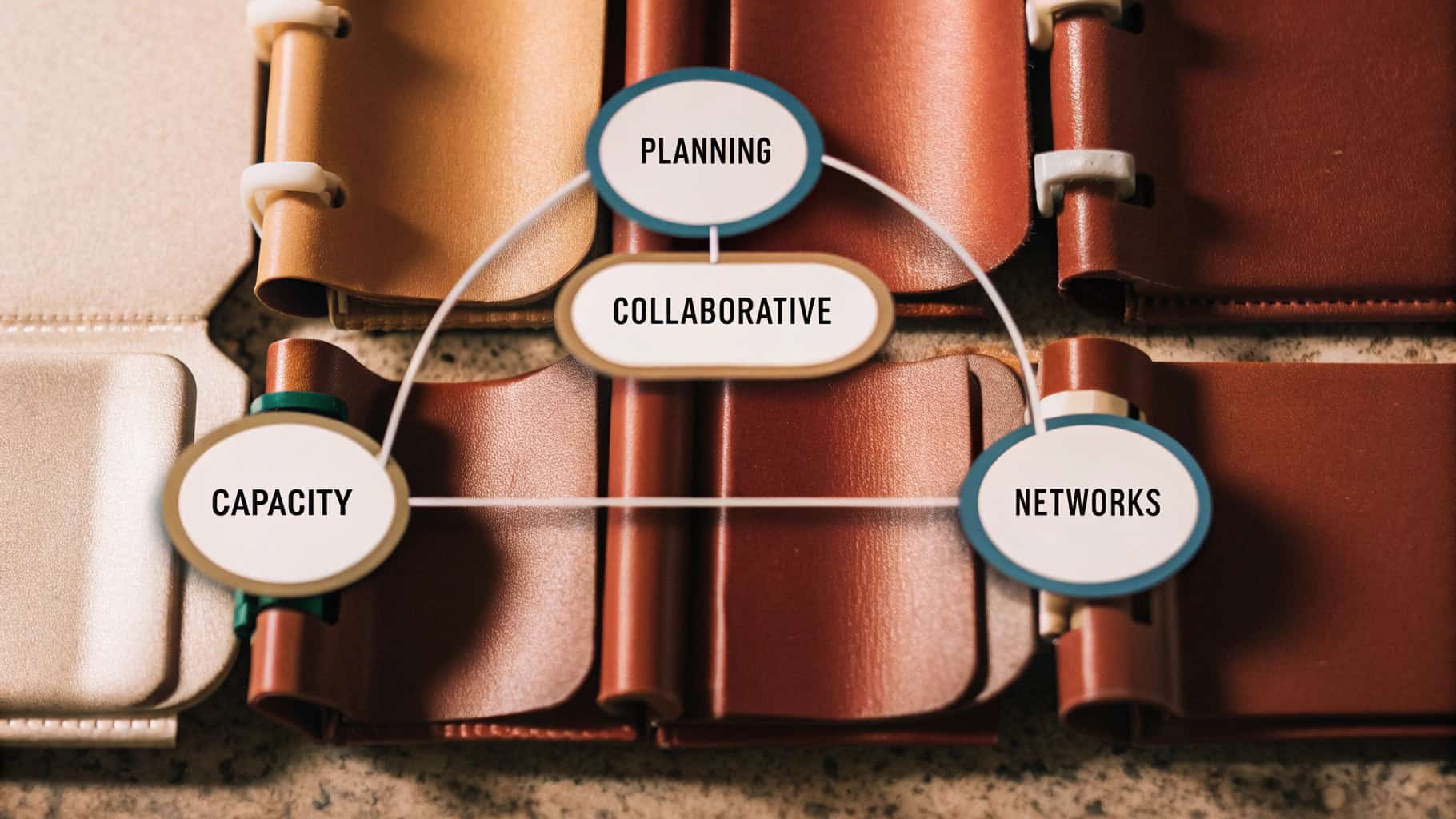
Working together can greatly improve how we manage production. By teaming up, we can share tools, avoid slowdowns, and keep things moving. Let’s explore some ways to make this happen.
Shared Production Calendar Platforms
Think of a shared calendar everyone can use. It shows production schedules for all teams. If one factory has free time, another can use it. This teamwork saves time and resources. It’s like everyone working in sync.
Capacity Swap Marketplaces
Sometimes, one factory has extra space while another is too busy. Capacity swap marketplaces let factories trade or share production time. This keeps everything balanced and avoids delays. Everyone benefits from this system.
Emergency Subcontractor Databases
Emergencies can happen, but being ready helps. A list of trusted subcontractors can solve problems fast. If a supplier fails, you can quickly find someone else. This keeps production steady and customers happy.
Joint Facility Investment Models
Sharing costs with other companies can be smart. Joint investments let businesses build shared warehouses or production lines. This saves money and improves efficiency. It’s a great way to work together.
Here’s how these ideas help production:
Report Type | What It Shows | Why It Helps |
---|---|---|
How well resources are being used. | Finds unused or overused resources for better planning. | |
Workload Capacity Report | Tracks work flow and resource use. | Helps make smarter choices to improve efficiency. |
Production Capacity Report | Shows the limits of production at different places. | Helps plan better schedules and use resources wisely. |
These reports show how teamwork makes production better. Sharing tools and planning together saves time and effort.
Tip: Start by sharing schedules or trading capacity. You’ll see how teamwork pays off quickly!
Data-Driven Order Fulfillment Architecture
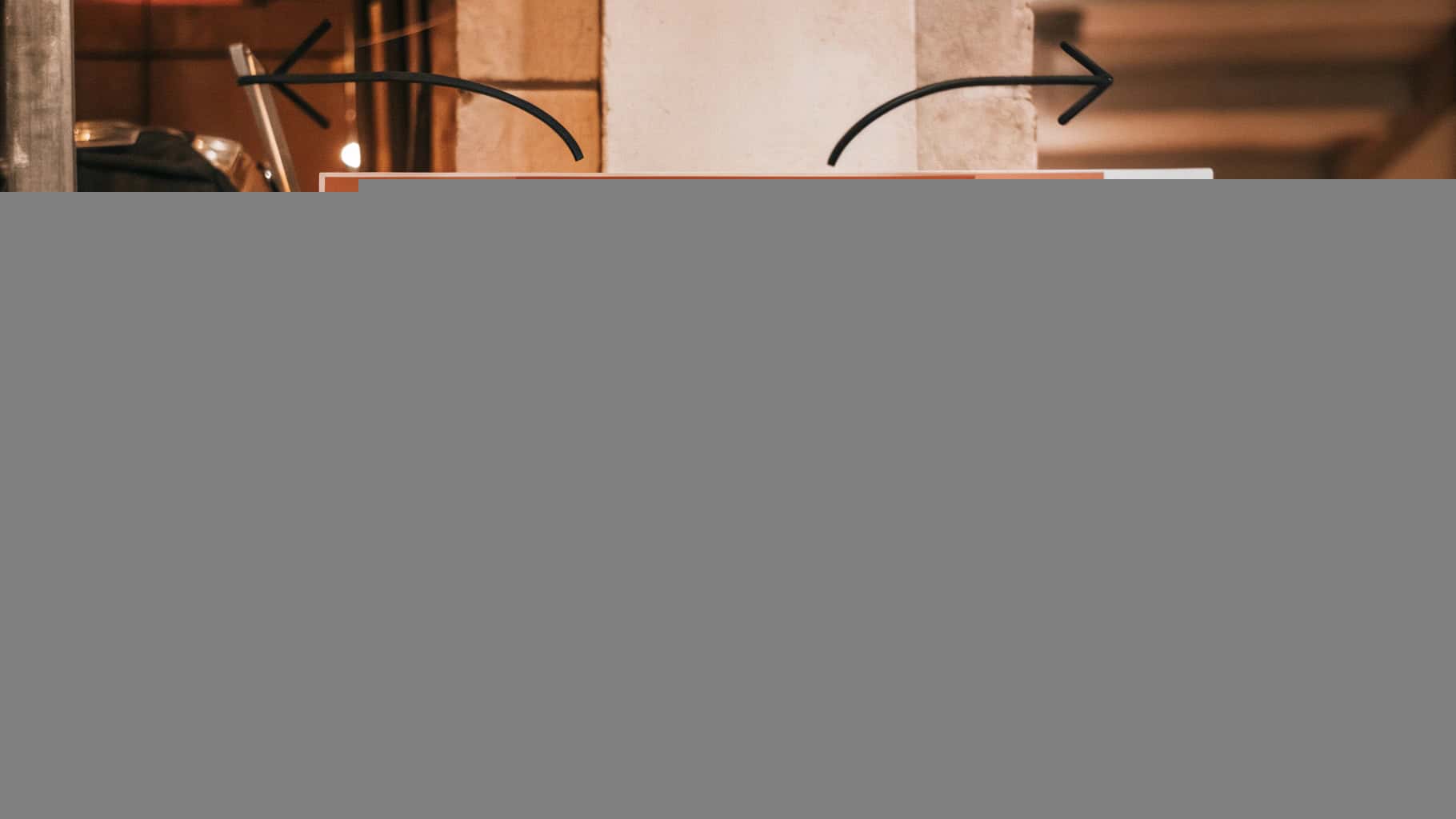
ERP-WMS Integration Blueprints
Combining ERP and WMS systems is a smart move. It’s like two minds working together for faster orders. Automation helps save money and boosts efficiency. Here’s what happens when companies switch:
Picking and processing costs drop by over 65%.
Manual packing costs $0.50 per order, but automation cuts it to $0.15. That’s a 70% savings!
Automated sorting boosts productivity by 600%.
These results show how ERP-WMS integration makes order fulfillment much better.
Automated Backorder Prioritization
Backorders can be tricky, but automation makes them easier. Using data to prioritize backorders reduces delays and keeps customers happy. Here are some key metrics that show its impact:
KPI | What It Tracks |
---|---|
Backorder Rate | The number of backorders compared to total orders. |
Fulfillment Accuracy Rate | How many orders are correctly completed from start to finish. |
On-Time Shipping Rate | How often shipments are delivered on time. |
Fulfillment Cost | The total cost to complete and deliver customer orders. |
Backorder Duration | How long items stay on backorder before being fulfilled. |
These numbers prove automation improves efficiency and reduces backorder problems.
Dynamic Carrier Selection Engines
Picking the right carrier for shipments can be tough. Dynamic carrier selection tools make it easy. They check routes, costs, and delivery times to choose the best option. Companies save money and meet deadlines with these tools. It’s like having a logistics helper.
ETA Machine Learning Refiners
Ever wonder how delivery times are so accurate? Machine learning tools are the answer. They study traffic, weather, and carrier performance to predict ETAs. These tools get smarter over time. The result? Fewer surprises and happier customers.
Making paint block orders faster isn’t only about speed. It’s about making things work better and easier. By improving supplier relationships, fixing delays, talking clearly, and planning inventory well, we can make orders quicker. Faster deliveries lead to happier customers and a better business. Why not begin now?
FAQ
How can I quickly shorten lead times for paint block orders?
Build strong supplier connections and use automation. These two steps help the most. They really make a big impact! 🚀
How does AI improve inventory management?
AI guesses what you’ll need and watches stock levels. It keeps things just right, so you don’t run out or have too much. Pretty cool, huh?
Are these tips useful for small businesses?
Yes, they are! These ideas work for any business size. Start with one small change, like automating a task, and grow from there. 😊