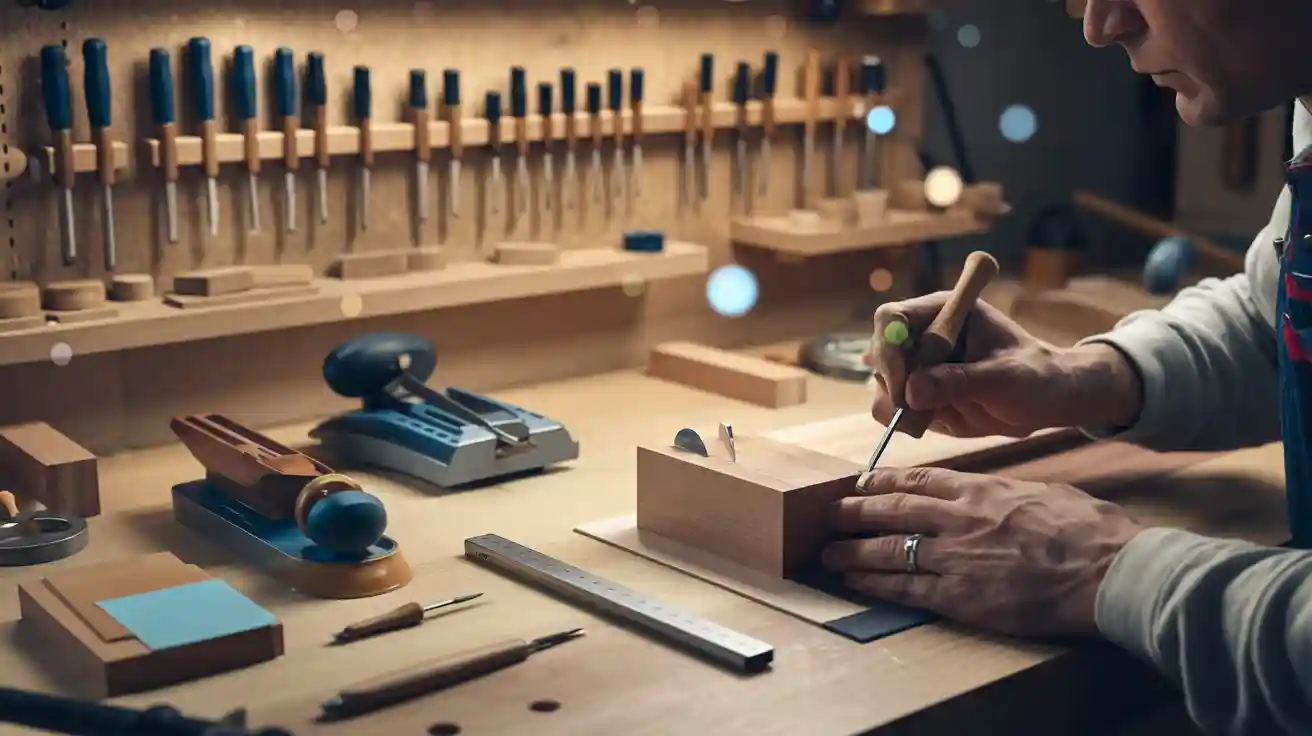
Have you ever thought about why some wood blocks are better? It’s all about being precise. Precision Processing Techniques in carving ensure that every cut and curve fits perfectly. This attention to detail makes the wood stronger and helps it last longer. When I think of making wood products, I see how careful techniques transform plain wood into art. For example, new carving methods have improved the [email protected] score by 3.5%. They also raised the [email protected]:0.95 score by 5.8%. These numbers demonstrate how being accurate through precision processing techniques leads to better designs and details. Whether using hardwood or softwood, selecting the right tool is crucial. The right gouge aids in adding fine details and achieving smooth finishes. With good tools and precision processing techniques, even small mistakes can be corrected, resulting in strong and high-quality wood blocks.
Key Takeaways
Careful processing makes wood blocks stronger and look better.
High-tech tools like lasers and CNC machines cut wood precisely.
Checking wood moisture with sensors stops cracks and bending.
Machines that find and sort defects save time and improve quality.
Using eco-friendly methods, like reusing wood chips, helps nature and work.
Mastering Precision Wood Processing for OEM Excellence
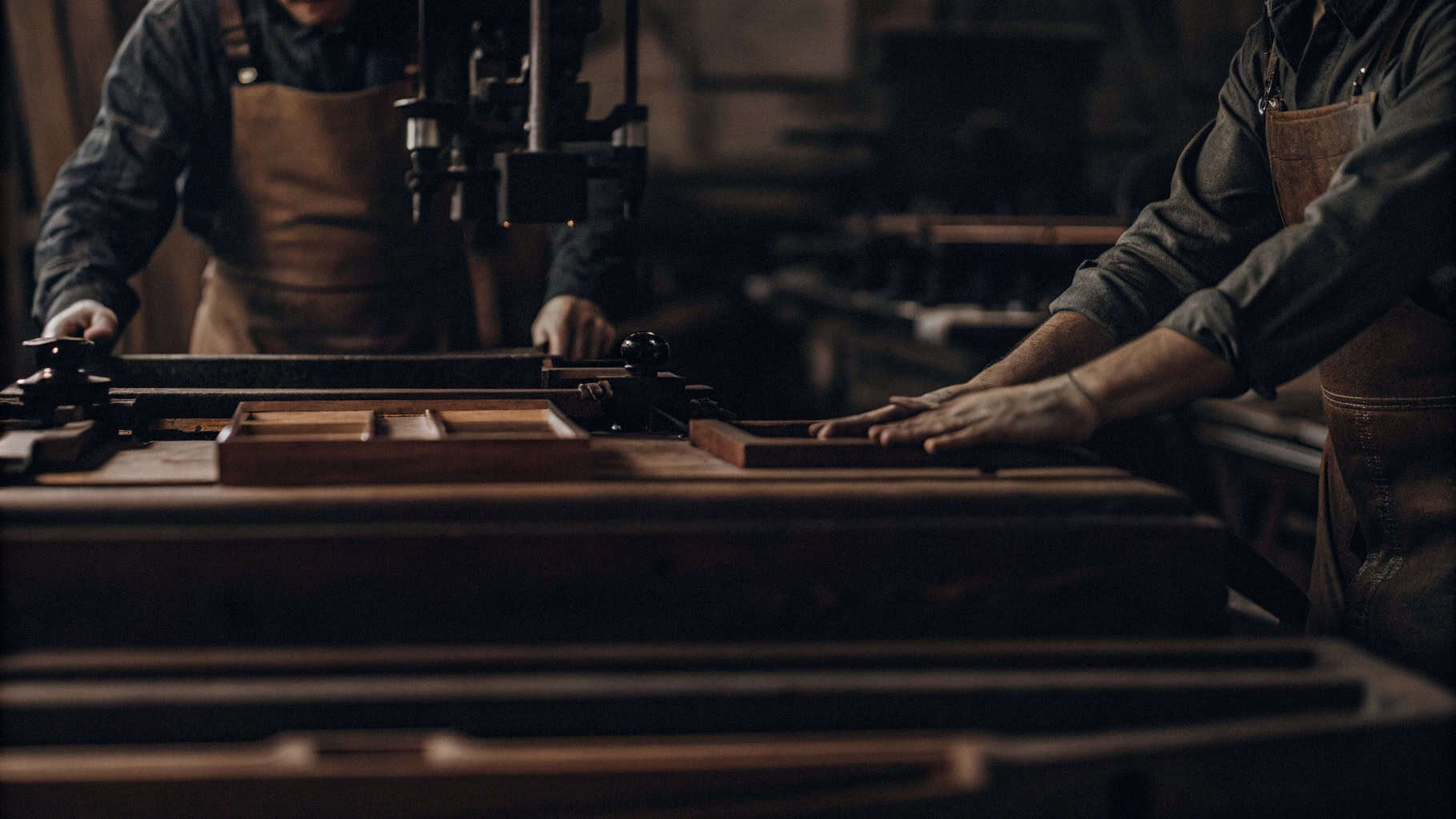
Nanosecond Laser Calibration Standards
Nanosecond lasers are a big help in wood carving. They make tools super accurate, so every cut is perfect. These lasers check and adjust tools with great precision. Imagine cutting wood and knowing it will fit perfectly every time. That’s what these lasers do. They also lower mistakes, saving materials and reducing waste. This means better products, less time wasted, and lower costs. It’s like having a magic tool for woodworking.
Multi-Axis CNC Programming Protocols
Multi-axis CNC machines are great for making detailed designs. These machines move in many directions to create complex patterns. I’ve used them to carve amazing designs on wood blocks. They are fast and very accurate. By programming them, I can place every cut exactly where it belongs. These machines also check quality automatically, making the process smoother. It’s exciting to see how they turn ideas into real designs with such detail.
Thermal Deformation Compensation Algorithms
Wood changes shape with temperature, which can cause problems. Thermal deformation algorithms fix this by predicting and adjusting for changes. This is very helpful for big projects where small errors matter. These algorithms keep the wood’s shape and quality steady, no matter the conditions. They ensure the final product looks and works as planned.
Here’s a simple table showing how precision woodworking helps OEM work:
How It Helps OEM Work | What It Does |
---|---|
Makes sure wooden items are precise and high-quality. | |
Automatic Quality Checks | Adds checks during production to save time. |
Faster Production | Speeds up making and delivering products. |
Saves Money | Cuts costs by setting up tools precisely. |
Less Waste | Uses materials wisely from the start. |
Automated Grain Pattern Recognition
Have you seen how wood grain affects designs? Knowing the grain is important for making great carvings. That’s why automated grain pattern recognition is so useful. It’s like having a tool that finds the best grain spots.
This technology scans wood blocks using special imaging systems. It shows the grain direction, density, and hidden flaws. I like it because it removes the guesswork from carving. Instead of guessing, the system tells me where to carve. It’s like having a guide saying, “Carve here for the best results.”
The system also works well with carving tools. For example, when I use gouges, the grain direction matters for smooth cuts. This technology helps me carve in the right direction every time. It saves time and stops the wood from splitting.
Here’s a tip: Use this tool with good-quality gouges. Together, they make carving easier and more accurate. They help me create designs that look amazing. Whether I’m making detailed patterns or simple shapes, this tool is a big help.
In the end, this technology isn’t just about easier carving. It makes the final product better. By understanding the grain, I can show the wood’s natural beauty and make something special.
Industrial-Grade Precision Cutting Systems
5-Axis Waterjet Cutting Configurations
The first time I used a 5-axis waterjet cutting system, I was amazed. It can cut curves easily, making it great for detailed designs. The best thing is it doesn’t make dust or pollution. There’s also no heat damage, so the wood stays perfect. The thin kerf, about 0.5 to 1.0 mm, reduces waste. This makes it both cost-saving and eco-friendly.
Here’s a simple table showing why this system works so well:
Feature | Description |
---|---|
Curve Cutting | Cuts curves smoothly and easily. |
Notch Quality | Makes clean notches without dust or mess. |
Cutting Force | Uses low force, keeping wood stress-free. |
Kerf Width | Thin kerf saves more material. |
Programmable Z Axis | Moves up between cuts for better results. |
Drive System | High-speed drive for accurate cutting. |
Sealed Driver System | Stays safe from water, dust, and dirt. |
This system has changed how I carve wood. It’s quick, exact, and dependable, making it a must-have for quality woodworking.
AI-Driven Kerf Width Optimization
I’ve always thought being precise is important in carving. AI-driven kerf width optimization makes this even better. It uses smart algorithms to find the best kerf width for each cut. This helps use wood wisely, saving money and reducing waste. I’ve seen how it makes cuts smoother and more even.
What’s even cooler is how it follows Lean Manufacturing ideas. It reduces waste and boosts productivity, using every piece of wood well. The built-in measuring tools also save time by skipping repeated measuring. This keeps the workspace safer and more organized.
Vacuum Clamping Pressure Formulas
Have you ever had trouble keeping wood steady while carving? I used to, but vacuum clamping fixed that. It uses exact pressure to hold wood firmly without harming it. This is great for delicate designs or detailed carving with gouges.
The best part? It works with other carving tools too. Whether I’m doing fine details or big cuts, the vacuum clamp keeps the wood still. This lets me focus on carving without worrying about slipping.
Tip: Adjust the pressure based on the wood type. Softer woods need less pressure, while harder woods need more.
These precision cutting systems have changed how I work with wood. They make carving faster, safer, and better, while giving amazing results.
Real-Time Moisture Content Monitoring
When I first started working with wood, I didn’t realize how much moisture could affect the final product. Over time, I learned that monitoring moisture levels is one of the most important carving techniques. It’s not just about keeping the wood dry; it’s about finding the right balance. Too much moisture can make the wood swell, while too little can cause cracks. That’s where real-time moisture content monitoring comes in.
This technology has completely changed how I approach wood carving. It uses sensors to measure the moisture inside the wood blocks. These sensors give instant readings, so I know exactly when the wood is ready for carving. I don’t have to guess anymore, which saves me a lot of time and effort.
Here’s how it works:
The sensors scan the wood and detect moisture levels.
The data gets displayed on a screen or app.
I adjust my carving techniques based on the readings.
For example, if the wood is too wet, I let it dry a bit longer. If it’s too dry, I might add a little humidity to make it easier to carve. This precision helps me create high-quality designs without worrying about cracks or warping.
I’ve also noticed that this system works great with wood carving gouges. When the moisture is just right, the gouges glide smoothly, making the carving process much easier. It’s amazing how something as simple as monitoring moisture can improve the quality of my work.
Tip: Always check the moisture levels before starting. It’s a small step that makes a big difference in the final product.
Real-time moisture content monitoring isn’t just a tool; it’s a game-changer. It ensures that every piece of wood I work with is in perfect condition, helping me achieve the best results every time.
High-Yield Material Utilization Strategies
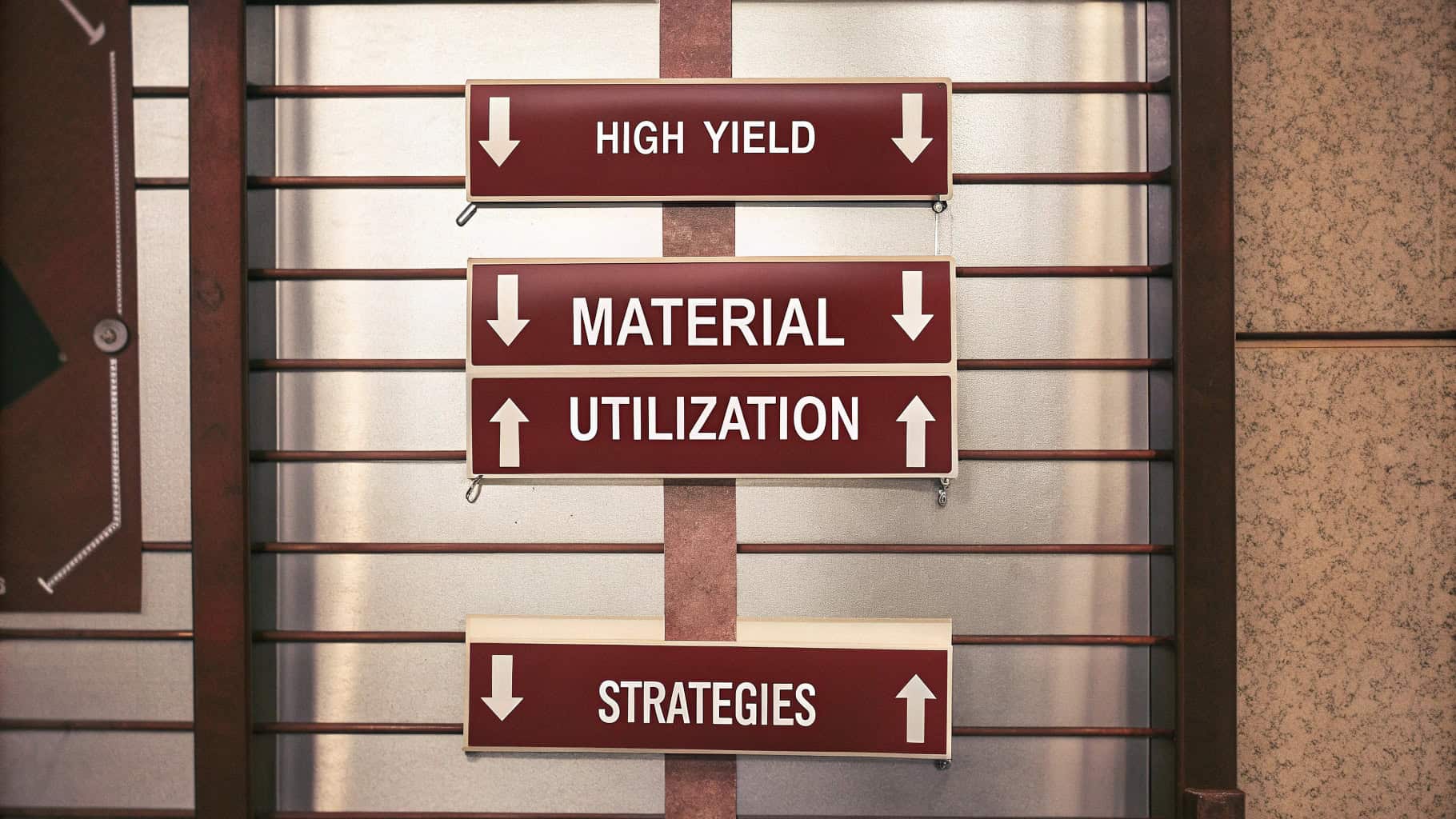
3D Nesting Software Efficiency Models
When I first started working with wood blocks, I often struggled to make the most out of each piece. That’s when I discovered 3D nesting software. It’s like a puzzle solver for wood carving. This software arranges shapes on a block to use as much material as possible. It’s amazing how it reduces waste and saves money.
The software works by analyzing the dimensions of the wood and the designs I want to carve. Then, it calculates the best way to fit everything together. I’ve noticed that it’s especially helpful when I’m working on intricate designs with gouges. It ensures I don’t waste any wood, which is great for both my budget and the environment.
Here’s a table showing how much value and volume yield can improve with high-yield strategies like 3D nesting:
Study | Value Yield Increase | Volume Yield Improvement |
---|---|---|
Chang & Gazo (2009) | 46% | N/A |
Lundahl & Grönlund (2010) | 22% | 4.5% |
Rais et al. (2017) | 4-20% | N/A |
Stängle et al. (2015) | 13-24% | 24% |
Fredriksson (2014) | 21% | 13% |
This data shows how much more efficient wood carving can be with the right tools and techniques.
Waste Chip Reclamation Processes
I used to throw away wood chips without a second thought. Then I learned about waste chip reclamation. It’s a process that turns leftover chips into something useful, like particleboard or even fuel. Now, I see those chips as a resource instead of waste.
The process is simple. After carving, I collect the chips and send them to a reclamation facility. They’re compressed and treated to create new materials. It’s a win-win. I reduce waste and contribute to sustainable practices. Plus, it feels good knowing I’m making the most out of every block.
Defect Mapping Integration Techniques
Defects in wood can ruin a project. That’s why I rely on defect mapping. This technique uses technology to find flaws in the wood before I start carving. It’s like having a magnifying glass that spots every crack and knot.
The system scans the wood and creates a map of defects. I use this map to plan my carving techniques. It helps me avoid weak spots and focus on the best areas. For example, when I use wood carving gouges, I know exactly where to carve for smooth results.
Here are some real-world benefits of defect mapping:
An automotive company reduced defects by 36% using defect concentration diagrams.
This saved them $2 million annually, showing how much waste can be avoided.
Defect mapping has transformed how I work with wood. It ensures every piece I carve is high-quality and free from flaws.
Batch-Specific Cutting Parameter Databases
When I began carving wood, I didn’t know small changes mattered. Over time, I learned every batch of wood is different. Things like density, grain, and moisture can change. That’s why batch-specific cutting parameter databases are so helpful. They’re like a guide for carving wood better and faster.
Here’s how they work. The database stores details from past projects. It saves the best speed, pressure, and tool angles for each wood type. When I start carving, I check the database for advice. For example, softwood might need less pressure and sharper gouges. Hardwood might need slower speeds and stronger tools.
This system works great with wood carving gouges. It helps me pick the right gouge for each job. It also stops me from using too much force on fragile wood. This saves time and reduces waste. I can use every piece of wood wisely.
Tip: Update your database often. Each project adds new info to improve future carvings.
Batch-specific cutting parameter databases have changed how I carve wood. They make carving easier and more accurate. Whether I’m making detailed patterns or simple shapes, this tool helps me get great results every time.
Global Quality Certification Pathways
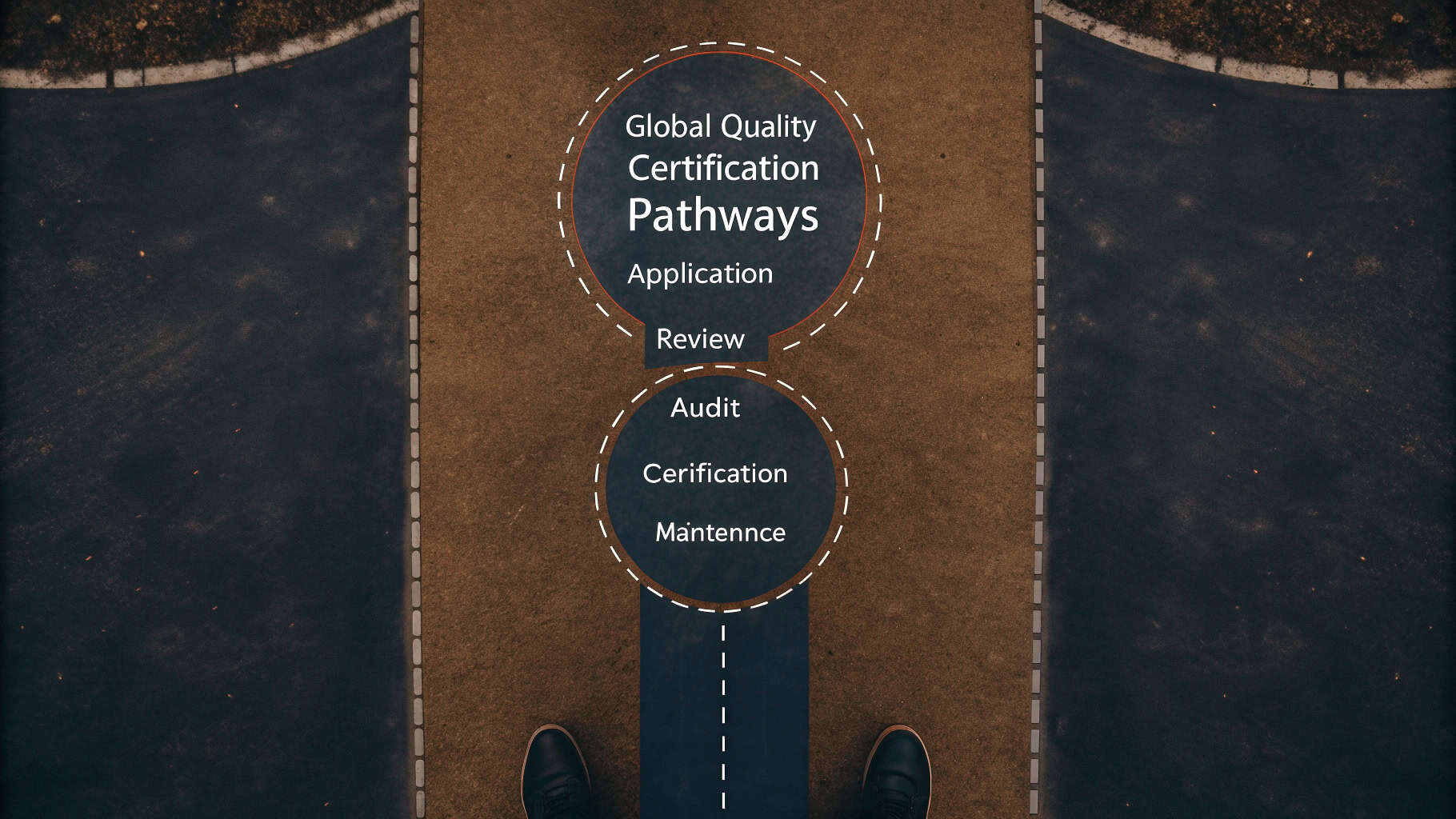
JAS/FSC Compliance Automation Kits
At first, I thought JAS and FSC certifications were just labels. But they actually ensure wood products are sustainable and high-quality. To simplify things, I started using compliance automation kits. These kits handle paperwork and tracking for me. They save time and prevent mistakes, which is helpful when managing many projects.
The coolest part? These kits work with my tools. For instance, while carving wood blocks, the system logs the materials I use. It also checks if the wood meets certification rules. This lets me focus on carving instead of worrying about rules. It’s like having a helper for all the boring tasks.
Wood Movement Coefficient Testing
Wood changes with temperature and humidity. This movement can ruin carvings if not managed. That’s why I use wood movement coefficient testing. It measures how much wood moves in different conditions. This helps me plan better carving techniques.
Here’s how it works. I test a small wood sample in a machine. The machine gives a report on how the wood will move. With this info, I adjust my carving to avoid cracks or warping. It’s a simple step that improves the final product.
VOC Emission Control Frameworks
Have you smelled strong odors while working with wood or finishes? Those come from VOCs (volatile organic compounds). VOCs can harm health and the environment. To fix this, I use VOC emission control frameworks. These systems monitor and lower VOC levels during carving.
For example, when I carve treated wood with gouges, the system filters the air. It keeps my workspace safe and ensures my projects meet environmental rules. It’s good for me and the planet.
Tip: Check VOC levels in your materials before starting. It’s a small step that helps a lot.
Cross-Border Certification Reciprocity
When I started working on global projects, certifications felt confusing. Every country has different rules for wood products. It was hard to keep up. Then, I discovered cross-border certification reciprocity. It’s like a passport for wood, making global standards easier to follow.
Here’s how it helps. If a product is certified in one country, reciprocity agreements let other countries accept it too. For example, if my wood blocks are FSC-certified in the U.S., they might also meet European rules without extra tests. This saves time and lets me focus on carving.
This is super useful when I use wood carving gouges for detailed work. Knowing my materials meet global standards makes me feel confident. It also shows clients they’re getting top-quality products. Plus, it helps me sell in new markets, which is exciting.
I’ve learned to keep all my documents neat and ready. Reciprocity often needs proof of compliance. I use digital tools to track wood types and carving methods. This makes exporting products much easier.
Tip: Check each country’s rules carefully. Reciprocity helps, but some places have special requirements.
Cross-border certification reciprocity has made my work simpler and faster. It’s a great tool for anyone growing their woodworking business worldwide.
Smart Factory Integration Solutions
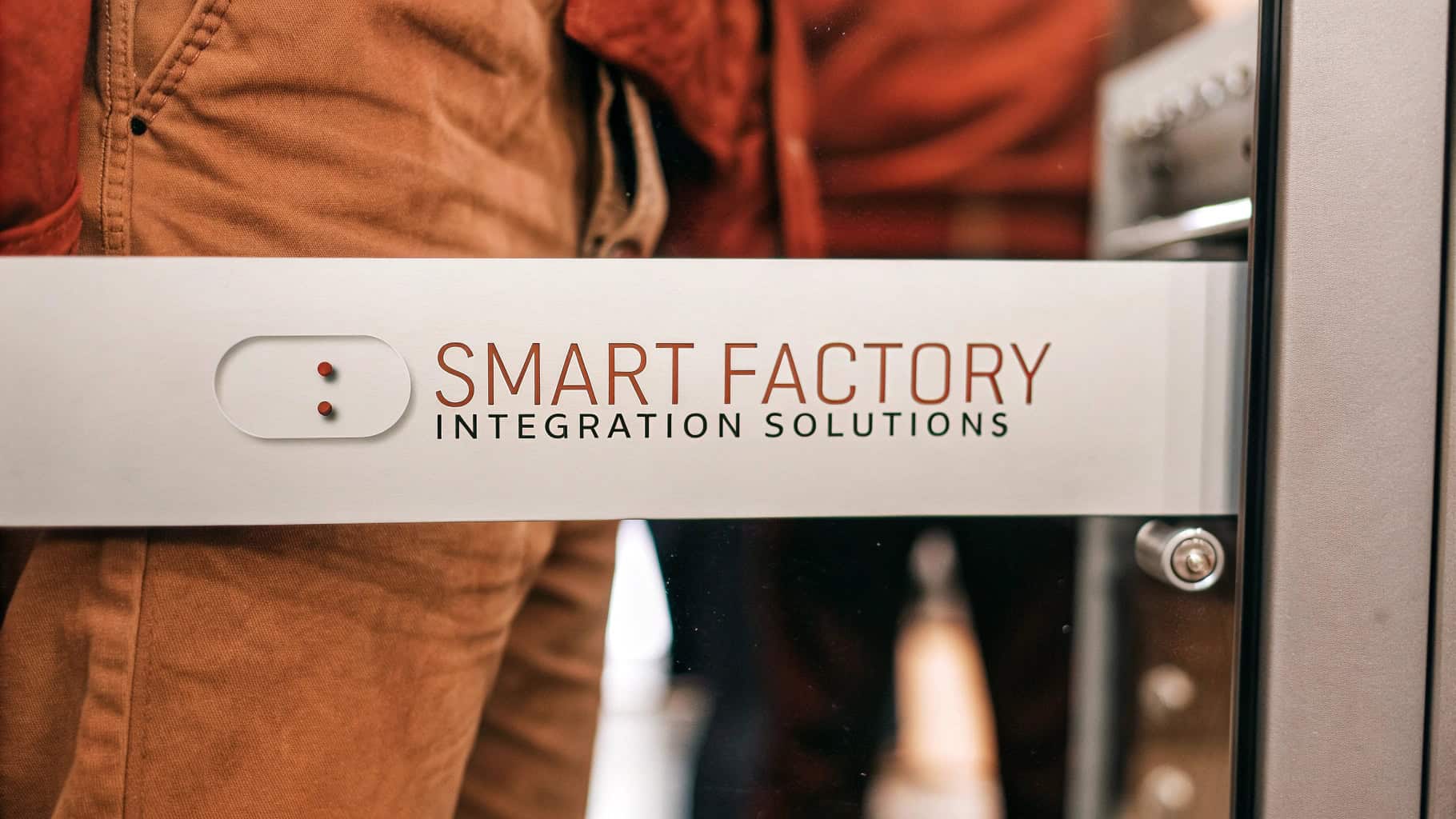
IoT-Enabled Humidity Control Systems
Humidity is very important for wood carving projects. Keeping the air just right helps prevent cracks and warping. That’s why I use IoT-enabled humidity control systems. These systems have smart sensors that check and adjust air moisture. It’s like having a weather helper in my workshop.
Here’s how it works. Sensors measure the air’s humidity and send data to a system. If the air is too dry or too wet, the system fixes it automatically. This keeps the wood ready for carving. When the air is perfect, my gouges move smoothly, and the wood stays strong.
These systems also save me time. I don’t need to check the air myself anymore. Instead, I can focus on carving and making great designs. This small change has made my work much better.
Machine Learning Predictive Maintenance
I used to worry about tools breaking during projects. Now, I use machine learning predictive maintenance to avoid this. This technology predicts when tools might need fixing. It’s like having a tool expert in my workshop.
For example, the system tracks how often I use my gouges. It studies this data and tells me when to do maintenance. This stops sudden breakdowns and saves repair costs. It also helps my tools last longer, which is great.
Here’s how predictive maintenance helps:
Metric | What It Does |
---|---|
Stops surprise failures, saving money and time. | |
Longer Tool Life | Regular care makes tools last longer. |
Better Productivity | Fewer problems mean more time for carving. |
With fewer tool issues, I can focus on carving. My projects are now smoother and faster.
Digital Twin Process Simulation
Imagine testing your carving ideas without wasting wood. That’s what digital twin process simulation does. It creates a virtual copy of my workshop and tools. I use it to try new carving methods before using real wood.
The simulation shows how tools like gouges will work on the wood. It even predicts how the wood will react. This helps me avoid mistakes and save materials. It’s like practicing on a digital block first.
Digital twins also improve my workflow. I can test different setups to find the best one. This has made my carving faster and more efficient. It’s a great tool for anyone serious about woodworking.
Tip: Try new designs with digital twins. It’s a safe way to experiment without wasting wood.
RFID-Embedded Material Tracking
Have you ever wondered how to keep track of wood blocks during carving projects? I used to struggle with this, especially when working on multiple pieces at once. That’s when I discovered RFID-embedded material tracking. It’s like having a digital assistant that keeps tabs on every block in my workshop.
RFID (Radio Frequency Identification) tags are tiny chips that store information about the wood. These tags attach to each block and send data to a reader. The system shows me details like the type of wood, its moisture level, and even its grain pattern. This makes carving so much easier because I always know what I’m working with.
Here’s why I love this system:
No more guesswork: The RFID tags tell me everything I need to know about the wood before I start carving.
Better organization: I can sort blocks by size, type, or even carving techniques.
Time saver: Instead of flipping through notes or labels, I just scan the tag and get instant info.
One time, I was working on a batch of wood carving gouges for a custom project. The RFID system helped me match each gouge to the right block. It even flagged a piece of wood that wasn’t ready for carving because its moisture level was too high. That saved me from ruining the design and wasting time.
Tip: Use RFID tracking with carving techniques that require precision. It helps you avoid mistakes and keeps your workflow smooth.
This technology isn’t just about convenience. It’s about improving the quality of your work. By knowing the exact details of each block, I can plan my carving techniques better and create designs that stand out. Whether I’m working on intricate patterns or simple shapes, RFID tracking has become an essential part of my process.
Cost-Optimized Surface Treatment Systems
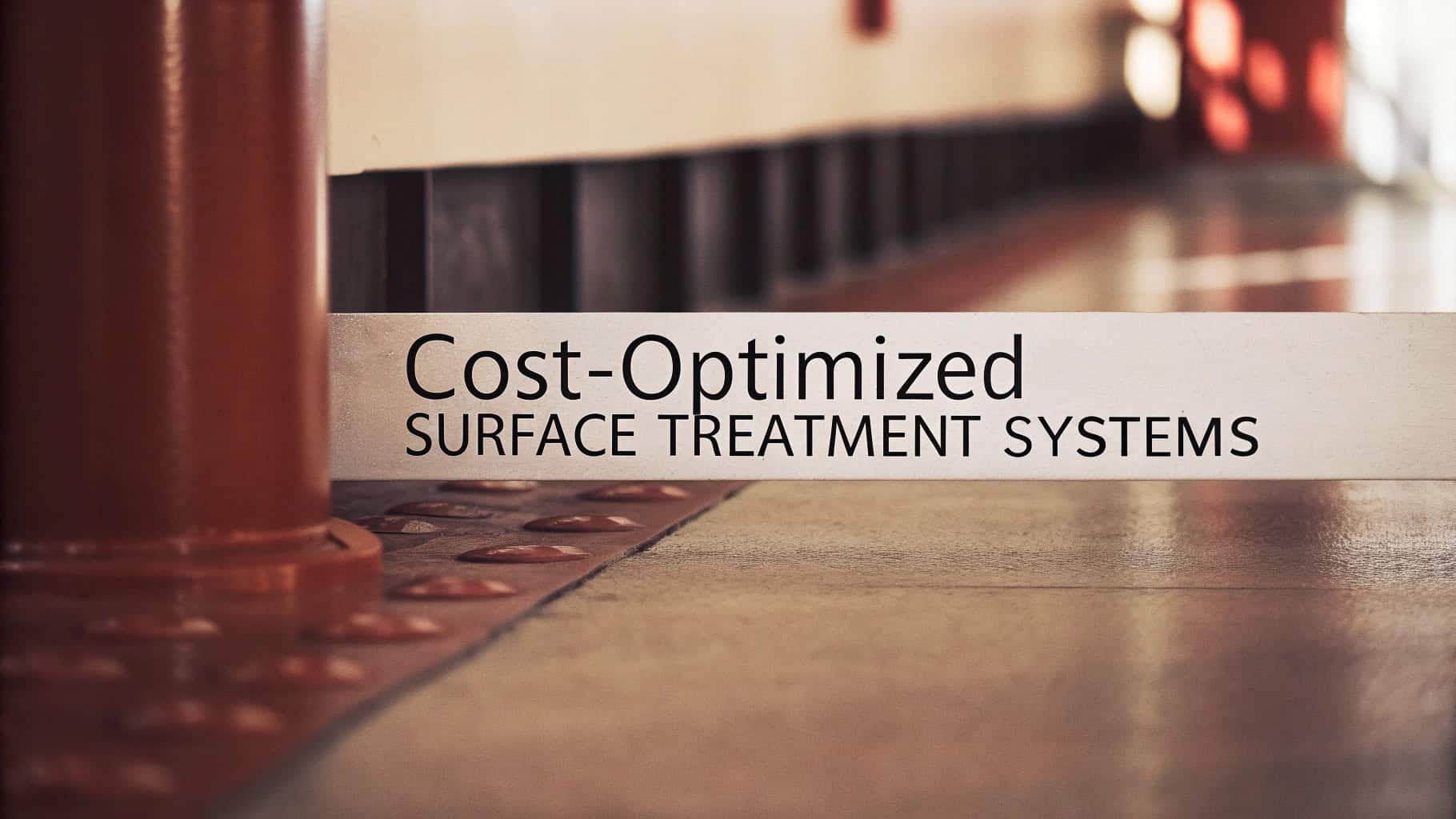
UV-Cured Coating ROI Calculators
I didn’t know UV-cured coatings could save so much money. These coatings dry super fast under UV light, speeding up projects. The best part? ROI calculators show how much I save. They help me see the benefits clearly.
Here’s what I’ve learned:
Labor costs are lower because drying is quick.
They work for both small and big projects, giving options.
The quality of my work has also improved. These coatings make wood surfaces smooth and strong. They highlight the wood’s natural beauty, whether it’s a simple block or a detailed design. The calculators also help me plan better, showing when I’ll get my money back.
Automated Sanding Grit Transition
Sanding used to be my least favorite task. Changing sandpaper grits felt boring, and I worried about skipping steps. Then I found automated sanding systems. These machines switch grits for me, making sanding easy.
Here’s how it works: The system changes the grit based on the wood’s surface. It knows when to go from rough to fine grit, leaving a smooth finish. This makes carving easier because my gouges glide smoothly over the wood.
I also save time. I don’t stop to change sandpaper anymore. Instead, I focus on creating designs. It’s amazing how this simple tool makes a big difference.
Electrostatic Spray Efficiency Models
Applying finishes used to feel tricky. I worried about wasting materials or uneven coverage. That changed with electrostatic spray systems. These sprays use charged particles to stick finishes evenly to wood.
The best part? They’re super efficient. The spray wraps around the wood, covering all sides without wasting material. This is great for detailed projects where every inch matters. The finishes also dry faster, keeping my work on schedule.
Tip: Use electrostatic sprays for detailed carvings. They save time and give perfect results.
These surface treatment tools have changed how I work. They save time, cut waste, and improve my projects. Whether I’m carving or finishing, these tools make every step easier.
Micro-Pore Sealing Pressure Formulas
At first, micro-pore sealing seemed tricky to understand. But after trying it, I saw how much it helps wood carving. This method uses exact pressure to close tiny pores in the wood. It’s like adding a hidden layer of protection, making the surface smoother and stronger.
Here’s how it works. The process calculates the right pressure for each wood type. Softer woods need gentle pressure, while harder ones need more. Using the right pressure makes carving easier and improves the finish. My gouges move smoothly, leaving neat and detailed cuts.
What I like most is how it highlights the wood’s natural beauty. Sealing the pores makes the grain patterns stand out more. It’s great for detailed designs. The sealed surface also blocks moisture, stopping the wood from bending or warping over time.
Tip: Test the pressure on a small wood piece first. This avoids over-sealing, which can make carving harder.
Micro-pore sealing works well with other carving methods. After sealing, I use wood carving gouges to add fine details. The sealed wood stays strong, even with repeated carving. This simple step really improves the final design.
If you enjoy wood carving, try this technique. It helps create durable and high-quality designs.
Crisis-Resistant Production Frameworks
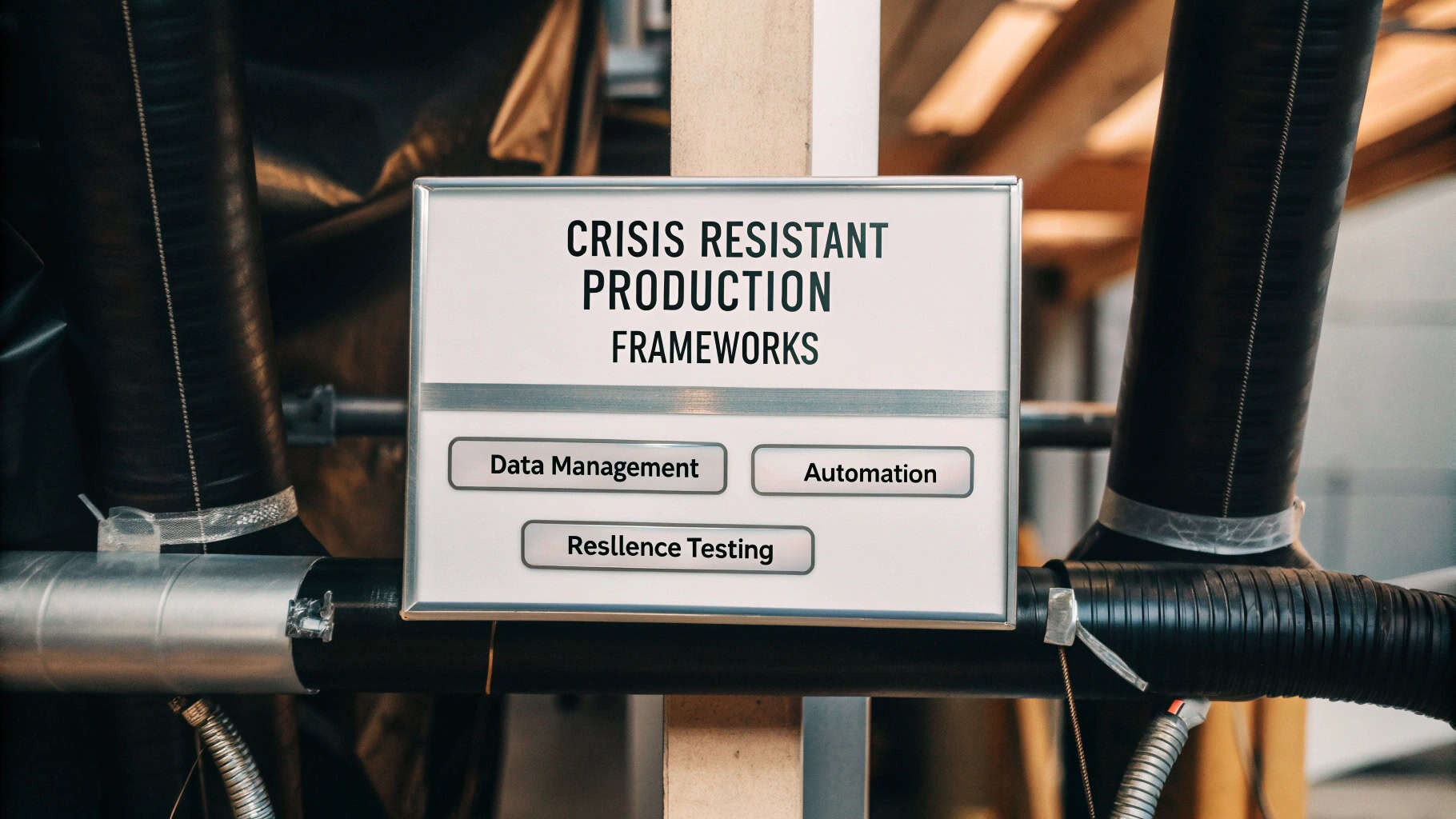
Dual-Source Material Buffer Models
Relying on one supplier can be risky. Delays or shortages can ruin plans. That’s why I use dual-source material buffer models. This means having two suppliers for the same material. It’s like having a backup to keep things steady.
Here’s how it works. I split my orders between two suppliers. If one has problems, the other fills in. This also helps me get better prices since suppliers compete. For example, when I buy wood blocks, I ensure both suppliers meet the same quality. This way, the materials are always consistent.
Dual sourcing also protects against climate or market changes. Studies show that increasing harvests can store more carbon. This helps the environment and ensures a steady wood supply. Check this table for details:
Measure | Annual Mitigation Potential (kt CO2/year) | Total Sequestered Carbon (Mt CO2 eq) by 2050 |
---|---|---|
Without increased harvest | 721 | 20.9 |
With increased harvest | 1.5 | 42.7 |
This strategy keeps my projects on track, even during tough times.
Automated Supplier Switch Protocols
Switching suppliers used to be hard. Now, automated supplier switch protocols make it simple. These systems shift orders to another supplier if one fails. It’s like having a safety net for materials.
For example, if one supplier runs out of gouges, the system orders from the backup. This saves time and avoids delays. It works best with dual sourcing. Together, they handle supply chain problems well.
Tip: Keep supplier details updated in the system. It makes switching faster.
Energy Consumption Optimization
Energy costs can rise fast, especially in woodworking. That’s why I focus on energy consumption optimization. Automated systems help me cut energy use. For example, reinforcement learning can lower energy use by 35% to 40%. Here’s a quick look:
Reduction Method | Energy Consumption Reduction |
---|---|
Reinforcement Learning | 35%-40% reduction |
This saves money and helps the planet by cutting emissions. I’ve also noticed my tools, like gouges, last longer with efficient energy use. Small changes can make a big impact.
Note: Check your tools often for energy efficiency. Small fixes save big.
Rapid Tooling Changeover Systems
Switching tools used to take too much time. I often struggled with setups, especially for detailed wood carving projects. Then I found rapid tooling changeover systems. These systems make tool swapping quick and simple, saving time and keeping work smooth.
Here’s how they work. The system has a modular design for fast tool changes. I can switch gouges in seconds without recalibrating. It feels like pressing a button to swap tools. This is great for designs needing different gouges for fine details or bigger cuts.
One thing I like is how it reduces downtime. For example, while carving wood blocks, I can switch tools without losing focus. This keeps the process fast and helps me finish projects sooner. It also ensures my carving stays consistent, which is key for good results.
Another plus is better safety. Before using these systems, securing tools was tricky and could cause accidents. Now, tools lock firmly in place, making work safer. This small improvement makes a big difference in my workshop.
Tip: Organize your tools ahead of time. It speeds up tool changes even more.
Rapid tooling changeover systems have changed how I carve wood. They save time, boost safety, and help me focus on making great designs. If you love woodworking, these systems are worth trying.
Customized Precision Tooling Solutions
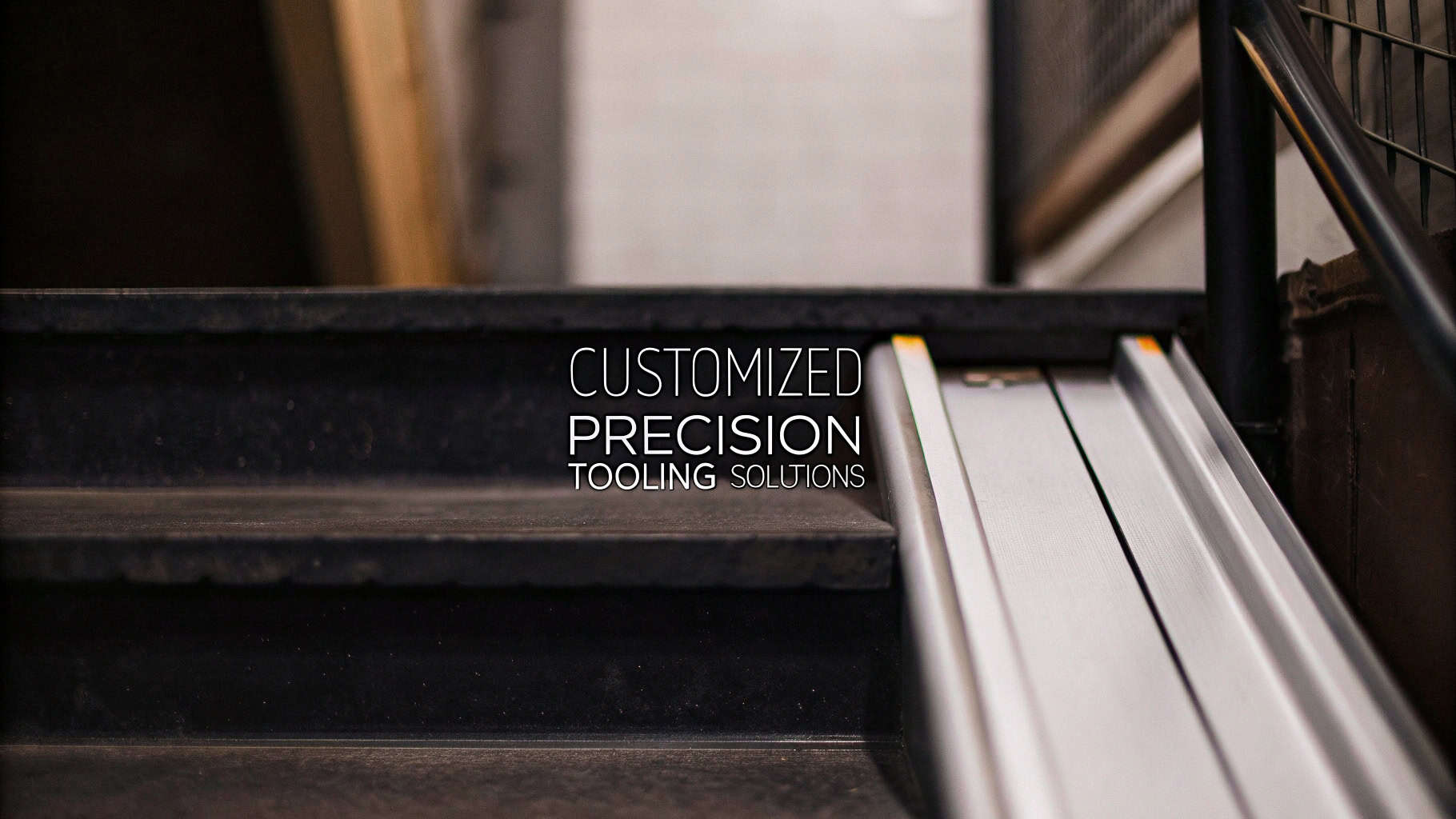
Diamond-Coated Bit Lifecycle Analysis
When I began using diamond-coated bits, I didn’t know how helpful they were. These bits last longer and cut better than regular ones. Tracking their use has helped me save money and reduce waste. By knowing when to replace them, I keep my work smooth.
I’ve noticed these bits stay sharp even on hard wood. This means I don’t stop carving often to change tools. Their sharpness also helps me make detailed designs with my gouges.
Tip: Write down how often you use your diamond-coated bits. This helps you know when to replace them before they wear out.
Carbide Insert Regeneration Processes
I use carbide inserts for precise carving. Instead of tossing them when dull, I now regenerate them. This process makes them sharp again and saves money. It’s like giving them a second chance.
The process is easy. I send the inserts to a service that sharpens and re-coats them. When they return, they work like new. This reduces downtime and helps me reuse materials, which is better for the environment.
Note: Not all carbide inserts can be regenerated. Ask your supplier if yours can be reused.
Tool Wear Prediction Algorithms
Knowing when tools will wear out is hard. That’s why I use tool wear prediction algorithms. These systems track how I use tools and predict when they’ll need fixing. It’s like having a tool expert in my workshop.
For example, the system checks how often I use gouges and how much pressure I apply. It tells me when they might dull, so I can plan ahead. Regular maintenance keeps my carving smooth and my designs perfect.
Here’s a table showing why proactive maintenance is helpful:
Benefit | Description |
---|---|
Keeps Quality Consistent | |
Extends Tool Life | Maintenance makes tools last longer, saving money. |
Stops Unexpected Delays | Fixing tools early prevents sudden issues and keeps projects on time. |
Tip: Use these algorithms with a cutting parameter database. Together, they make carving easier and more efficient.
Customized precision tooling has improved my woodworking. From diamond-coated bits to smart algorithms, these tools help me work faster and better. They save time, reduce waste, and make sure every wood block turns out great.
Modular Fixture Design Libraries
When I started carving wood, keeping blocks steady was hard. They often moved while I used gouges for detailed designs. Then I found modular fixture design libraries, and they made carving much easier.
These libraries have fixtures ready to use. The fixtures can adjust to fit different wood sizes and shapes. I pick one, change it to match my project, and start carving. This saves setup time and lets me focus on my work.
The fixtures are very flexible. For example, they hold wood tightly without causing damage. This is helpful for carving patterns with gouges. They also keep larger blocks steady for big cuts. It feels like having extra hands to help.
Tip: Use modular fixtures for precise carving. They stop slips and keep designs neat. They’re also easy to store and reuse, making them worth having.
These fixtures have improved my carving process. Whether I’m making simple shapes or detailed designs, they help me create great pieces every time.
Note: Modular fixtures are more than tools—they solve problems. They make carving smoother and give better results.
AI-Powered Defect Recognition Systems
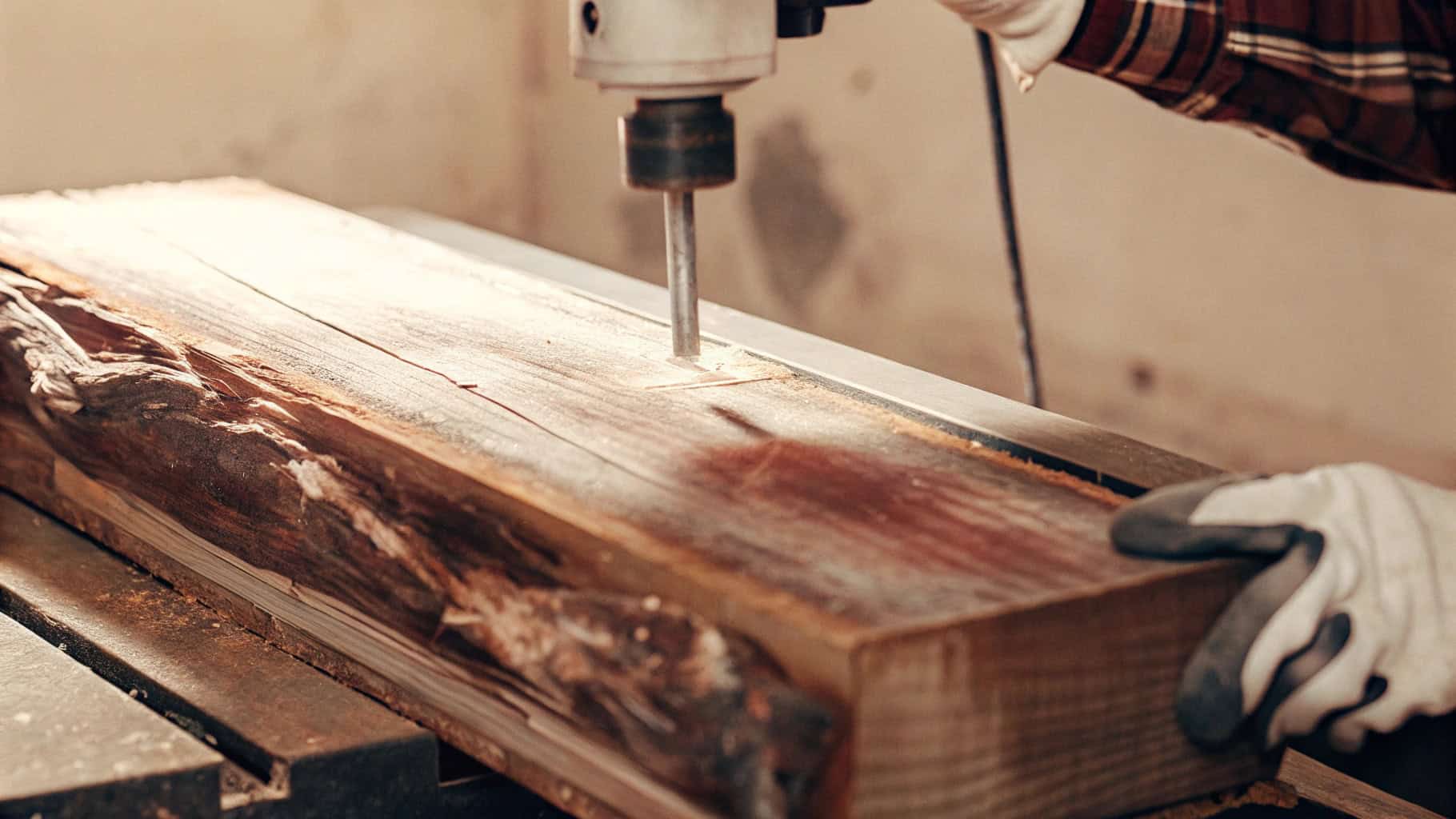
Hyperspectral Imaging Analysis
At first, hyperspectral imaging seemed too advanced for woodworking. But after trying it, I saw how useful it is. This technology uses special cameras to scan wood and find hidden defects. It’s like having X-ray vision for wood. The system spots cracks, knots, and flaws inside the wood, helping me avoid weak areas.
The best part is how fast it works. The system scans entire wood blocks in seconds. It gives me a detailed map showing the wood’s condition. This helps me plan my carving better and avoid wasting time on bad pieces. It’s especially helpful when I use gouges for detailed designs. Knowing where to carve makes my work easier and more accurate.
Here’s a simple table showing how different technologies help find defects:
Technology | Benefits |
---|---|
Machine Vision | Speeds up inspections; ensures accuracy and reduces downtime. |
X-ray Inspection | Quickly checks large batches; finds hidden flaws for better wood quality. |
AI Learning | Learns from past mistakes; improves defect detection over time. |
Automated Sorting | Spots defects early; organizes wood for higher-quality results. |
Hyperspectral imaging has become one of my favorite tools. It saves time, reduces waste, and helps me make better designs.
Knot Detection Neural Networks
Knots in wood can be tricky. They look nice but can cause carving problems. Knot detection neural networks solve this issue. These systems use AI to find and classify knots in wood. They are very accurate, even with complex patterns.
I’ve noticed the system works best with clear, high-quality images. Blurry images can lower accuracy, but using features like texture and color improves results. For example:
Misclassified knot images were 13%-14% smaller than correctly classified ones.
Combining features like GLCM and LBP improved accuracy.
Artificial neural networks (ANN) worked best with optimized settings.
This technology makes carving easier. It helps me avoid weak spots and focus on areas that highlight the wood’s beauty. My gouges move smoothly, even around knots, thanks to the system’s guidance.
Automated Sorting Conveyor Logic
Sorting wood by hand used to take forever. Now, automated sorting conveyor systems do it for me. These systems use sensors and AI to scan wood on a conveyor belt. They find defects and sort the wood into groups automatically.
This saves me so much time. I can spend more time carving instead of sorting. The system also ensures only the best wood reaches my workshop. It’s like having a helper that never gets tired. Plus, it’s very accurate. It catches even tiny flaws, so I don’t get surprises while carving.
Tip: Use automated sorting for big batches of wood. It saves time and improves your projects.
These tools have made my work faster and better. Whether I’m carving detailed patterns or simple shapes, they make every step easier.
Blockchain-Enabled Traceability Solutions
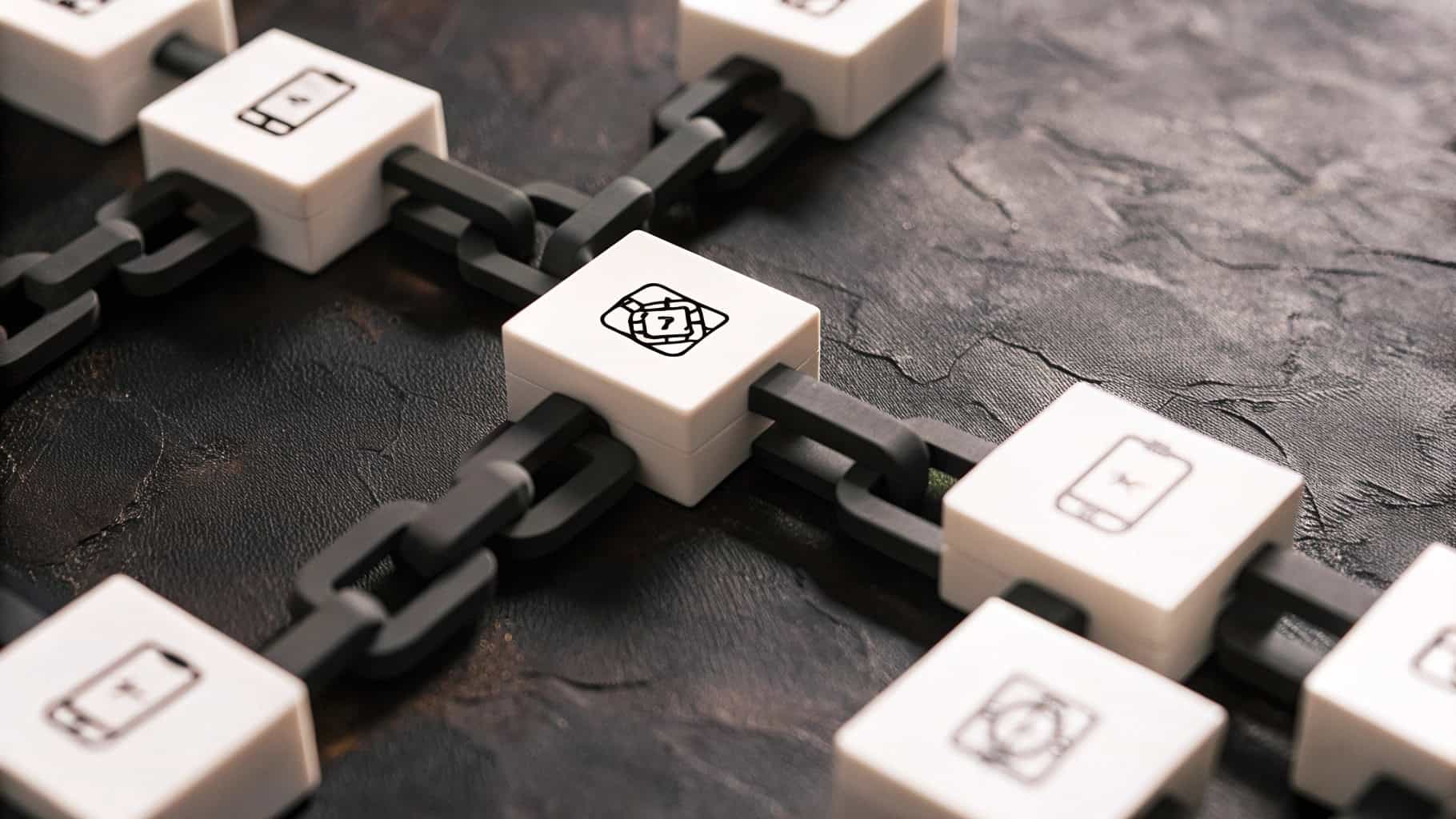
Origin-to-Customer Chain Verification
When I first heard about blockchain for woodworking, I wasn’t sure how it could help. Then I tried it, and wow—it’s like having a digital map for every piece of wood. Blockchain tracks each block from the forest to the customer. It records every step, like harvesting, processing, and shipping. This makes it easy to prove the wood’s origin and quality.
Here’s why I love it. Customers can scan a code and see the entire journey of their wood carving. It builds trust and shows that the materials are sustainable. For me, it’s also a time-saver. I don’t have to dig through paperwork to prove where my wood came from. The blockchain does it for me.
Tip: Use blockchain for custom projects. It helps clients feel confident about the materials you’re using.
Smart Contract Quality Assurance
Smart contracts are like digital agreements that run themselves. They check if the wood meets quality standards before moving to the next step. For example, when I carve wood blocks, the contract verifies the moisture level and grain pattern. If something’s off, it flags the issue right away.
This technology keeps my carving techniques consistent. It also saves me from wasting time on wood that doesn’t meet the mark. Plus, it’s super easy to use. Once the contract is set up, it works automatically. I can focus on carving while it handles the details.
Note: Smart contracts are great for large projects. They ensure every block meets the same high standards.
Real-Time Customs Data Sharing
Shipping wood carving gouges and finished pieces across borders used to be a hassle. Customs paperwork slowed everything down. Blockchain fixed that. It shares data with customs in real time, speeding up the process. Now, I can ship my carvings faster and with fewer delays.
Here’s how it works. The blockchain stores all the details about the wood and tools. Customs officials access this data instantly, so there’s no waiting for forms. It’s like having a fast pass for international shipping.
This system also helps me keep track of my shipments. I know exactly where my gouges and carvings are at all times. It’s a small change that makes a big difference in my workflow.
Tip: Use blockchain for international orders. It saves time and keeps your projects on schedule.
Sustainable Forestry Compliance Protocols
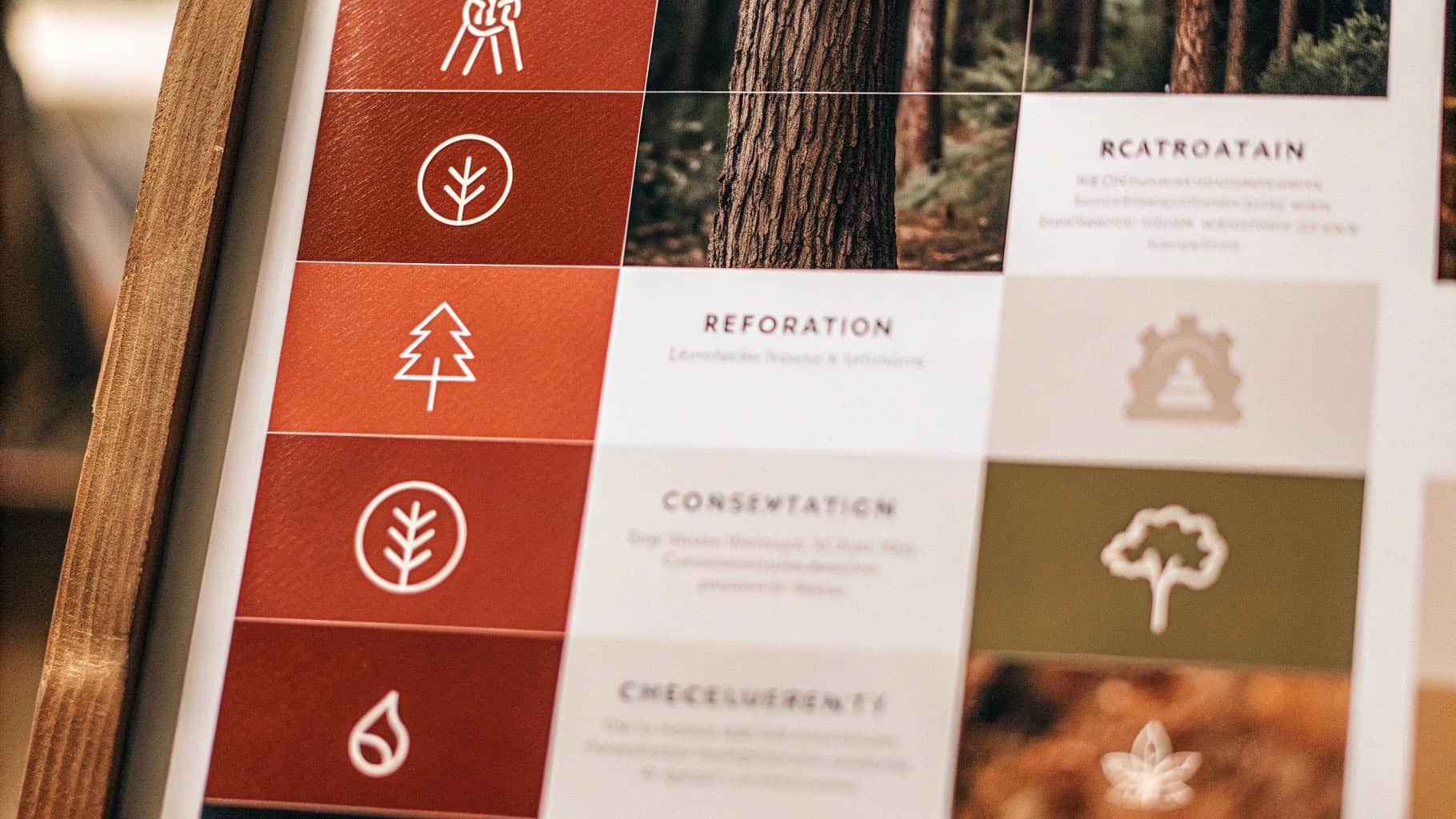
Satellite-Based Stock Verification
Technology helps forests stay healthy. Satellite-based stock verification uses satellite pictures to check forest wood supplies. It shows how much wood is available without visiting the forest. It’s like seeing everything from above.
This tool stops overharvesting. It shows which areas can be harvested and which need time to grow. This keeps forests strong and ensures wood for future projects. The data is very accurate, so I can plan carving projects responsibly.
Chain-of-Custody Digital Ledgers
Tracking wood origins used to be hard. Chain-of-custody digital ledgers make it easy. These ledgers record every step, from forest to product. It’s like a digital journal for each wood block. I can see its full journey and confirm it meets sustainability rules.
Here’s why these ledgers are helpful:
Digital Product Passports (DPPs) show wood’s source and environmental effects.
RFID and geolocation tools securely track wood movement.
FSC-certified wood tokens allow precise tracking of certified materials.
These tools give confidence. When I carve with gouges, I know the wood is sustainable. Customers also love seeing the story behind their carvings. It builds trust and shows care for the planet.
Biodiversity Offset Management
Forests are homes for plants and animals, not just wood. Biodiversity offset management keeps ecosystems balanced when trees are cut. For every tree removed, new ones are planted, and habitats are restored.
I choose suppliers who follow these practices. They plant trees and protect wildlife, keeping forests healthy. This makes me proud of my work. I’m not just carving wood; I’m helping nature too.
Tip: Pick suppliers who care about biodiversity. It helps forests and the planet.
Multi-Material Processing Innovations
Wood-Plastic Composite Formulations
Wood-plastic composites mix wood fibers with plastic. This creates a strong and flexible material. They are great for projects needing durability. These composites resist water and don’t bend like regular wood. I use them for outdoor carvings or furniture.
Making these composites is interesting. Wood fibers are blended with melted plastic. Then, they are shaped into blocks or sheets. Carving them with gouges feels different. The surface is smooth, and tools slide easily. It’s perfect for a polished look with little effort.
Tip: Keep your gouges sharp when carving wood-plastic composites. Sharp tools make cleaner cuts and better designs.
Cross-Laminated Timber Techniques
Cross-laminated timber (CLT) is very strong and stable. It’s made by layering wood panels in opposite directions. I use CLT for big projects, like carving detailed designs on structural pieces. It doesn’t crack or bend under pressure.
CLT combines old wood methods with new ideas. The layers stop it from bending, even in wet weather. When I carve CLT with gouges, the material stays steady. This lets me focus on my designs without worrying about splits.
Fire-Retardant Impregnation Methods
Safety is key when working with wood. Fire-retardant treatments make wood safer by slowing burning. This is important for carvings in homes or public spaces.
The treated wood feels heavier when carving. But my gouges still work well on it. Knowing the wood is fire-safe makes me feel better about my projects.
Note: Check if fire-retardant treatments affect your tools. Some treatments can make gouges dull faster.
Acoustic Damping Layer Integration
At first, I didn’t think acoustic damping layers would matter in woodworking. But after using them, I saw how they improve sound in wood projects. These layers reduce vibrations and noise, making them great for musical instruments or furniture.
Here’s what I do. I pick the right material for the damping layer. Some materials work better with certain woods. Then, I place the layer between wood pieces, like a sandwich. This helps absorb sound. It’s simple, but the results are impressive.
Carving wood with damping layers feels different. The layers make the wood steadier, so carving is smoother. This lets me focus on details without worrying about vibrations or movement.
Tip: Keep your gouges sharp when carving with damping layers. Sharp tools make cleaner cuts and easier carving.
One of my best projects was carving wooden speaker blocks with damping layers. The sound was clear and rich, like the music came alive. The layers didn’t just improve sound—they made the blocks stronger too.
If you enjoy wood carving, try acoustic damping layers. They’re easy to use and make projects better. Whether it’s instruments, furniture, or decorations, these layers add a professional finish.
Precision Finishing Technology Packages
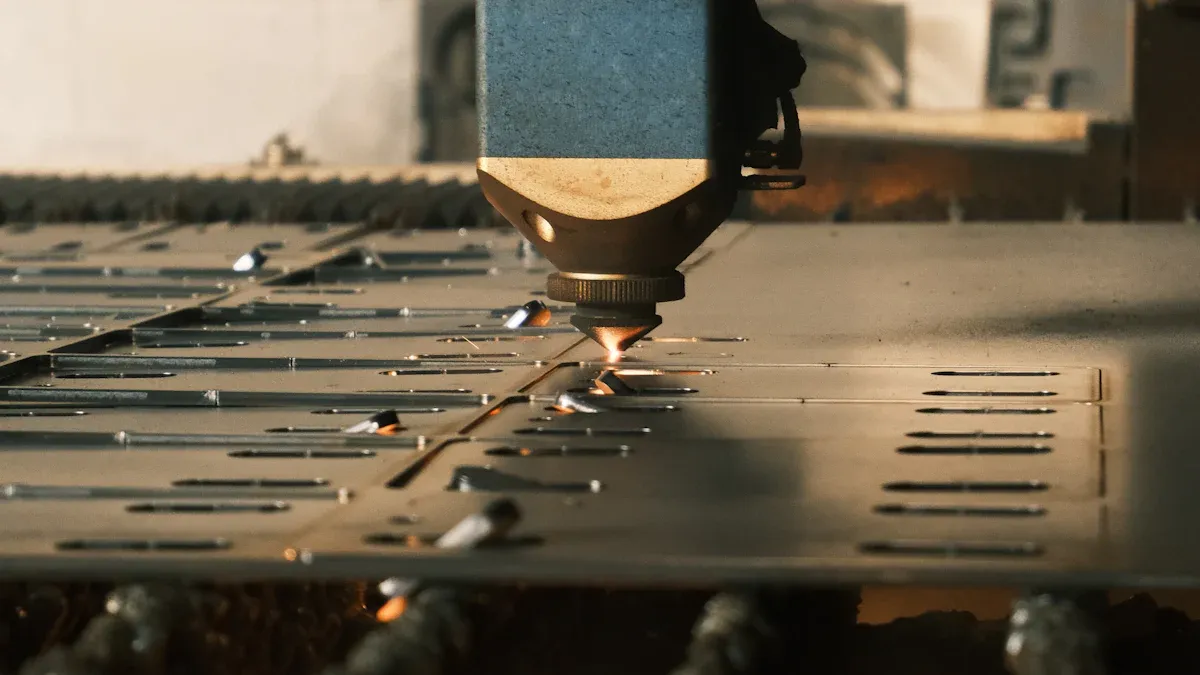
Robotic Arm Edge-Breaking Systems
Smoothing wood edges by hand used to take forever. It was tiring, and the edges didn’t always look even. Then I found robotic arm edge-breaking systems. These machines make smoothing edges fast and perfect. The robotic arm moves smoothly over the wood, leaving flawless edges every time.
The best part is how adjustable they are. I can set the arm’s pressure and angle for different wood types. This helps a lot when I’m carving detailed designs with gouges. The system makes sure the edges match the rest of the carving perfectly. It’s like having a helper that never gets tired or makes mistakes.
Tip: Use robotic arms for tasks you repeat often. They save time and improve accuracy.
Micro-Texture Replication Processes
Adding textures to wood carvings by hand was hard and slow. Micro-texture replication processes made it much easier. These systems copy patterns onto wood surfaces with amazing detail. The results look professional and consistent.
Here’s how it works. The system scans a texture, like wood grain, and copies it onto the wood. I’ve used it to add fine details that are hard to do by hand. It works great with gouges, making the design stand out even more. Plus, it’s quick, so every piece looks polished and neat.
Climate-Adaptive Coating Formulas
Wood carvings can get damaged in bad weather. That’s why I use climate-adaptive coating formulas. These coatings protect wood from cracking or bending in heat or cold. They’re perfect for outdoor projects.
Applying the coating is easy. I brush or spray it evenly on the wood. Once dry, it forms a layer that adjusts to the weather. Carvings with this coating last longer and look better. The coating also brings out the wood’s natural beauty.
Note: Test the coating on a small spot first. This ensures it works well with your wood.
Automated Gloss Measurement
When I began carving wood, I didn’t think much about gloss. I thought shiny finishes were just for looks. Later, I learned gloss makes carvings stand out more. Automated gloss measurement systems made this process easier and faster for me.
Here’s how they work. Sensors check how light reflects off the wood’s surface. They give instant results, showing if the gloss is too shiny or dull. This helps me adjust my work to get the best finish. For example, when I carve detailed designs with gouges, the gloss highlights every curve and line perfectly.
What I like most is how simple these systems are. I place the wood under the sensor, and it measures everything quickly. It’s reliable and saves time, especially when I’m working on many pieces. The readings also help me pick the right polish or coating for each project.
Tip: Use these systems for detailed carvings. They make sure the gloss improves the design without being too much.
These systems work with all kinds of carving methods. Whether I’m smoothing edges or adding patterns, the gloss measurement ensures the final piece looks polished and professional. It’s surprising how much this small tool improves my work.
If you love wood carving, try automated gloss measurement. It’s an easy way to make your carvings look even better.
Precision processing methods have changed how I work with wood. They help make wood blocks stronger, more accurate, and better looking. For example, CNC machines can cut within ±0.005 inches for perfect fits. Using tools like gouges with LiDAR defect detection makes carving easier and faster. These techniques not only add fine details but also show off the beauty of hardwoods. As woodworking improves, smart quality systems and eco-friendly methods will keep making wood blocks better. Let’s use these new ideas to improve our skills!
Callout: Choosing the right gouge helps add fine details and smooth finishes.
FAQ
What are gouges, and why are they important in wood carving?
Gouges are specialized tools with curved blades. They help create smooth, detailed cuts in wood. I use them for everything from shaping blocks to adding intricate designs. Their versatility makes them essential for carving techniques, whether you're a beginner or an expert.
How do I choose the right gouge for my project?
I pick gouges based on the design and wood type. For fine details, I use smaller gouges. Larger ones work better for removing more material. Testing a few options helps me find the perfect fit for each carving project.
Can I use the same carving techniques on all types of wood?
Not really. Different woods need different approaches. Softer woods are easier to carve but can split. Hardwoods require sharper gouges and more effort. I always adjust my carving techniques to match the wood's texture and grain.
How do I prevent wood blocks from cracking during carving?
I monitor the wood's moisture levels. Real-time sensors help me know when it's ready. If it's too dry, I add humidity. If it's too wet, I let it dry. This balance keeps the blocks stable and prevents cracks while carving.
What’s the best way to maintain gouges?
I clean and sharpen my gouges regularly. A sharp blade makes carving smoother and safer. I also store them in a dry place to avoid rust. Proper care extends their life and keeps them ready for any project.