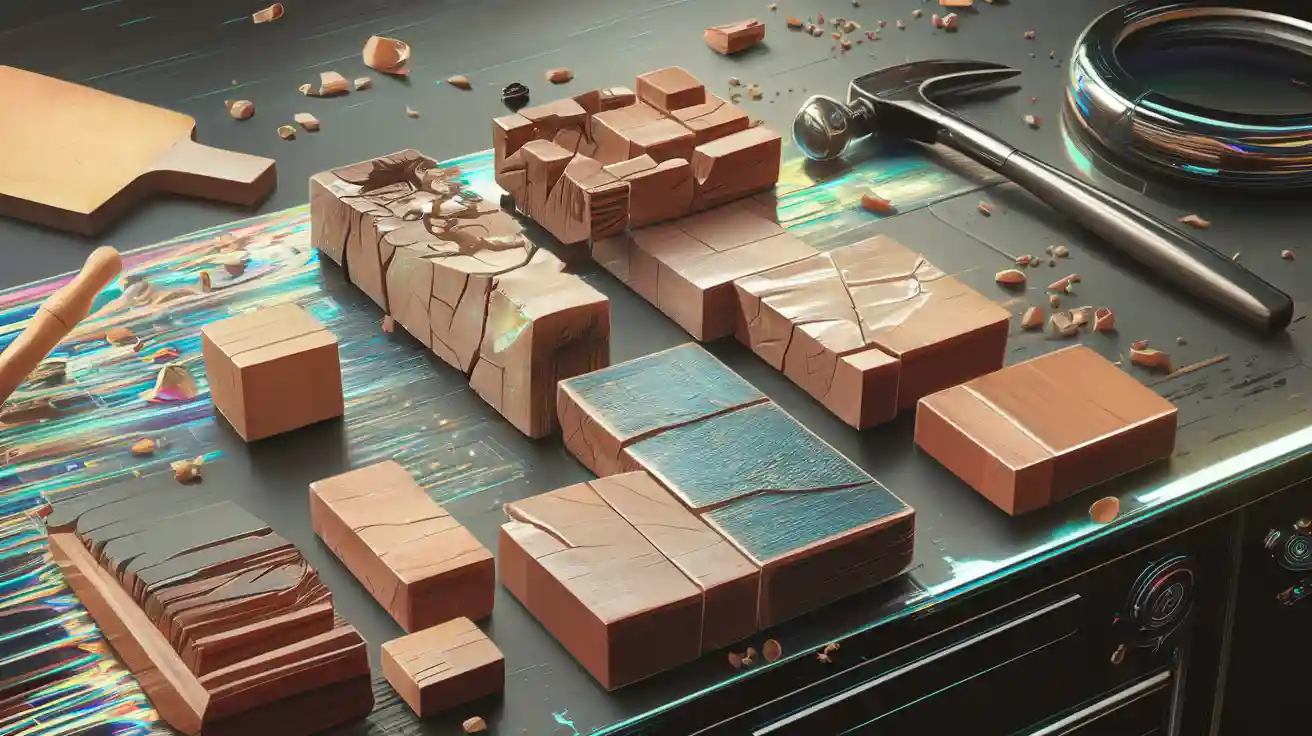
Have you ever seen how defects in wood blocks can ruin them? Problems like scratches, dents, or cracks can weaken wood and make it look bad. In factories, these defects in wood blocks waste materials and cost more money. For example, good wood should have no scratches or dents, dirt under 250 pixels, and stains smaller than 1000 pixels. Following these rules helps the wood work properly.
If you ignore these defects in wood blocks, they get worse. Cracks grow bigger, stains spread, and the wood might become useless. That’s why fixing wood defects quickly is so important. Luckily, JDW remedies make fixing wood problems easier and faster. Their smart tools and methods help fix wood, saving time and money.
Key Takeaways
Spot wood problems early, like knots or cracks, to stop bigger issues later.
Use JDW fixes, like laser tools and steam repair, to fix wood problems quickly and save money.
Store wood in climate-controlled areas to prevent bending or rotting.
Check wood often for water levels and bugs to meet shipping rules and avoid customs trouble.
Use smart tools like AI scanners and X-rays to find defects and make wood better.
10 Critical Wood Block Defects Impacting Manufacturing Quality
Structural Weakness from Knots & Shakes
Knots and shakes are some of the most common types of wood defects I’ve come across. Knots happen when branches grow out of the tree trunk, leaving circular patterns in the wood. They might look interesting, but they weaken the wood’s structure. Shakes, on the other hand, are cracks that form inside the tree while it’s still growing. These natural wood defects can make the wood less reliable for construction or furniture.
When I see knots or shakes, I know they can cause trouble. For example, a knot might fall out, leaving a hole in the wood. Shakes can split the wood apart under pressure. These defects make the wood harder to work with and can lead to wasted materials. That’s why it’s so important to spot them early.
Costly Warping Patterns in Industrial Processing
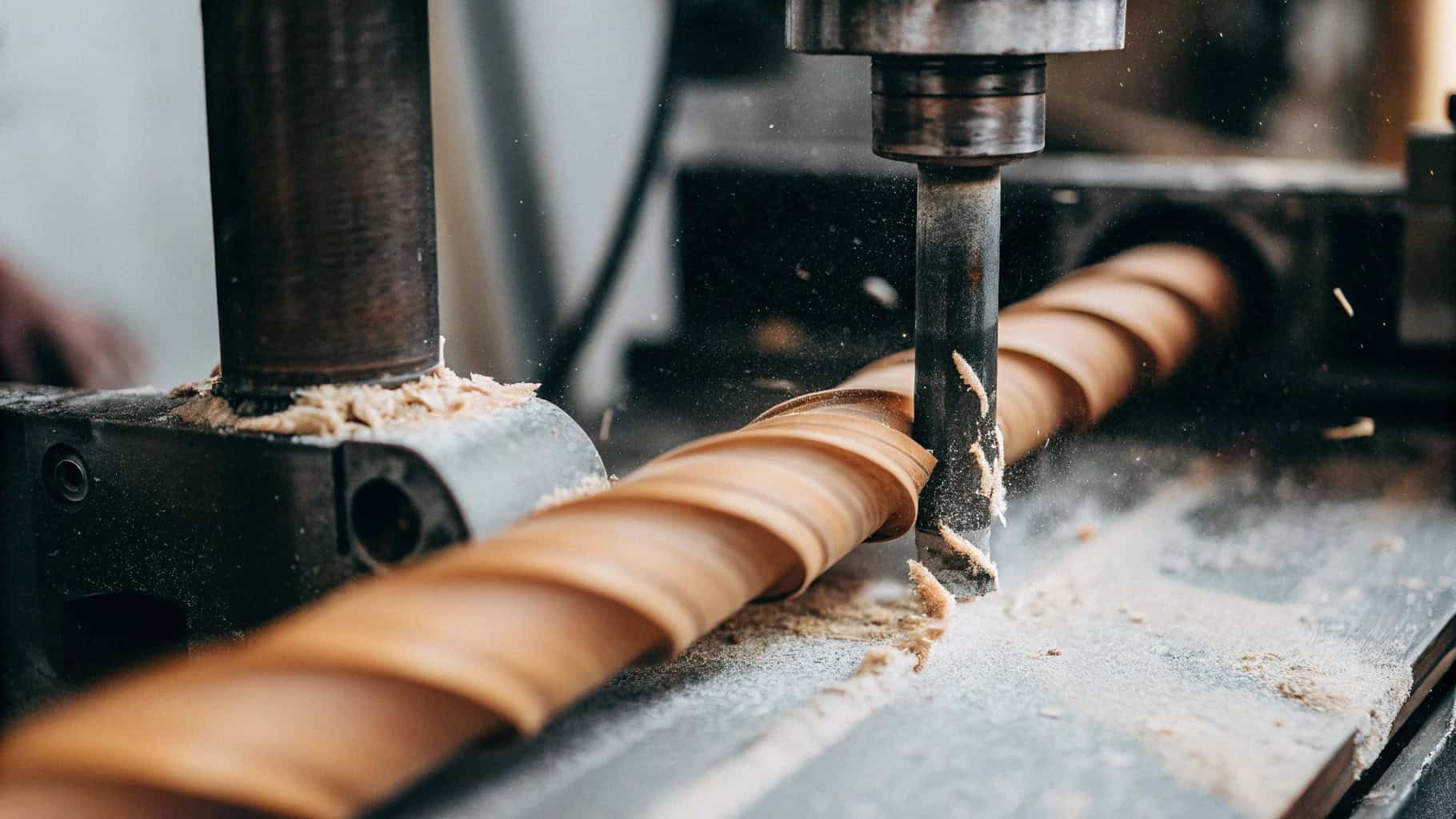
Warping is another issue I’ve noticed, especially during industrial processing. It happens when wood bends or twists out of shape. This can occur because of uneven drying or changes in moisture levels. Warping isn’t just annoying—it’s expensive. It can ruin entire batches of wood, making them unusable for precise projects.
I’ve learned that both natural wood defects and unnatural wood defects can lead to warping. For instance, uneven grain patterns (a natural defect) or improper storage (an unnatural defect) can cause the wood to warp. Fixing warped wood takes time and money, so preventing it is always the better option.
Hidden Risks of Surface Cracks in Raw Materials
Surface cracks might seem small, but they can cause big problems. These cracks often form during drying or because of poor handling. I’ve seen how they can weaken the wood and make it prone to breaking. What’s worse, these cracks aren’t always visible right away. They can hide under the surface, only to show up later when it’s too late to fix them.
These types of wood defects can lead to costly repairs or replacements. That’s why I always recommend inspecting raw materials carefully. Catching surface cracks early can save a lot of trouble down the line.
Decay Problems in Large Shipments
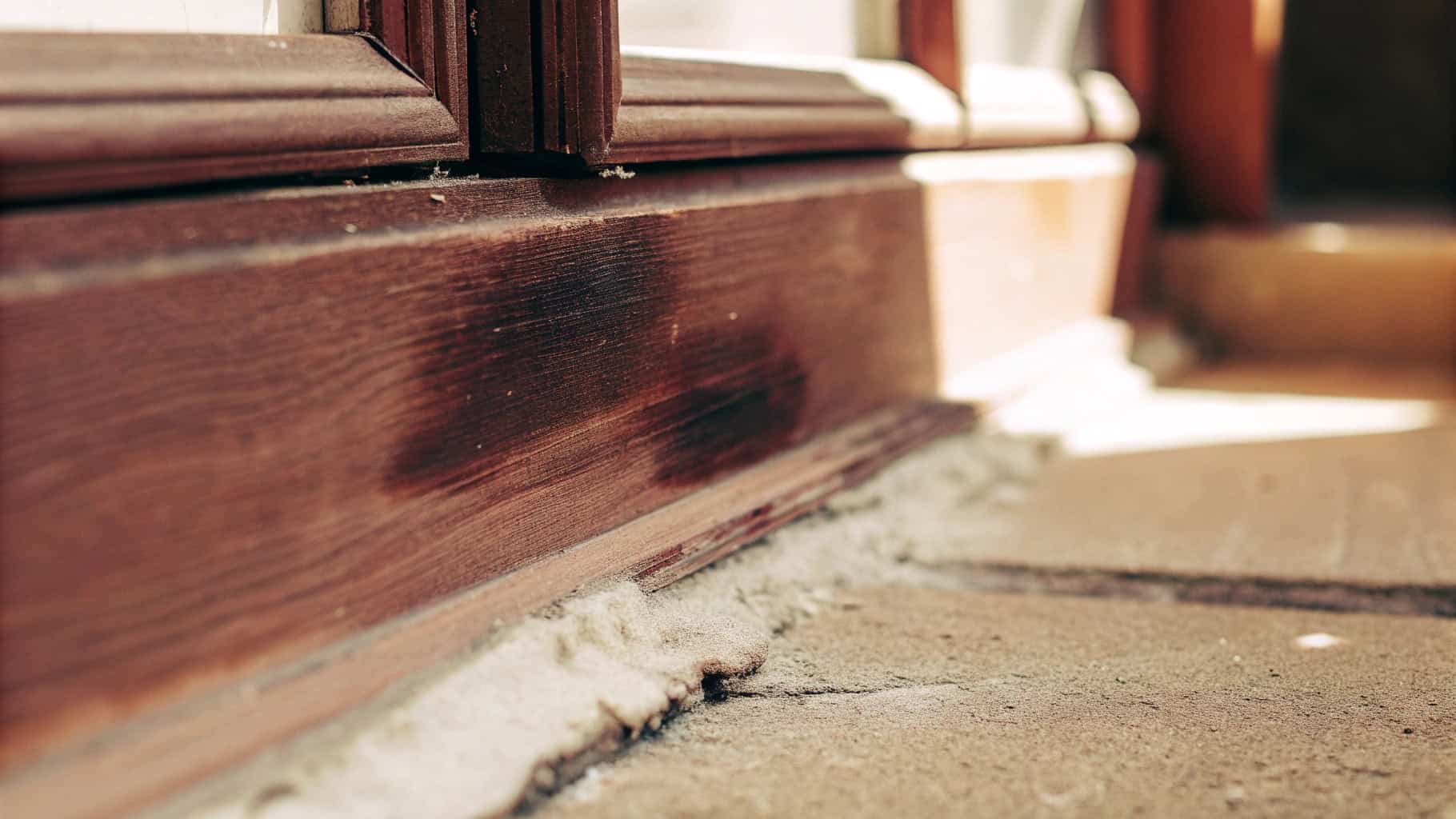
Decay is a tough defect to handle, especially in large shipments. It starts small, like a tiny discolored spot. But soon, it spreads and ruins lots of wood. Decay doesn’t just make wood look bad—it also weakens it.
Decay often happens when wood isn’t stored the right way. Moisture is usually the main reason. If wood gets wet during shipping or storage, fungi can grow. Once fungi start growing, decay begins. Even one bad piece can spread decay to others.
Tip: Always check wood moisture before shipping. Keep it under 20% to lower decay risks.
Another problem is poor airflow in storage areas. Without good air circulation, moisture stays trapped, and decay spreads faster. Using storage spaces with controlled climates can help stop this. It’s a simple way to save money over time.
Here’s an easy checklist to find and stop decay:
Look for soft spots or discoloration before shipping.
Use tools to check moisture levels under 20%.
Store wood in dry, airy places.
Rotate stock often to avoid dampness over time.
Stopping decay early can feel hard, but it’s worth it. A little effort now can save big losses later.
JDW Pro Solutions: Fixing Wood Defects for Industrial Buyers
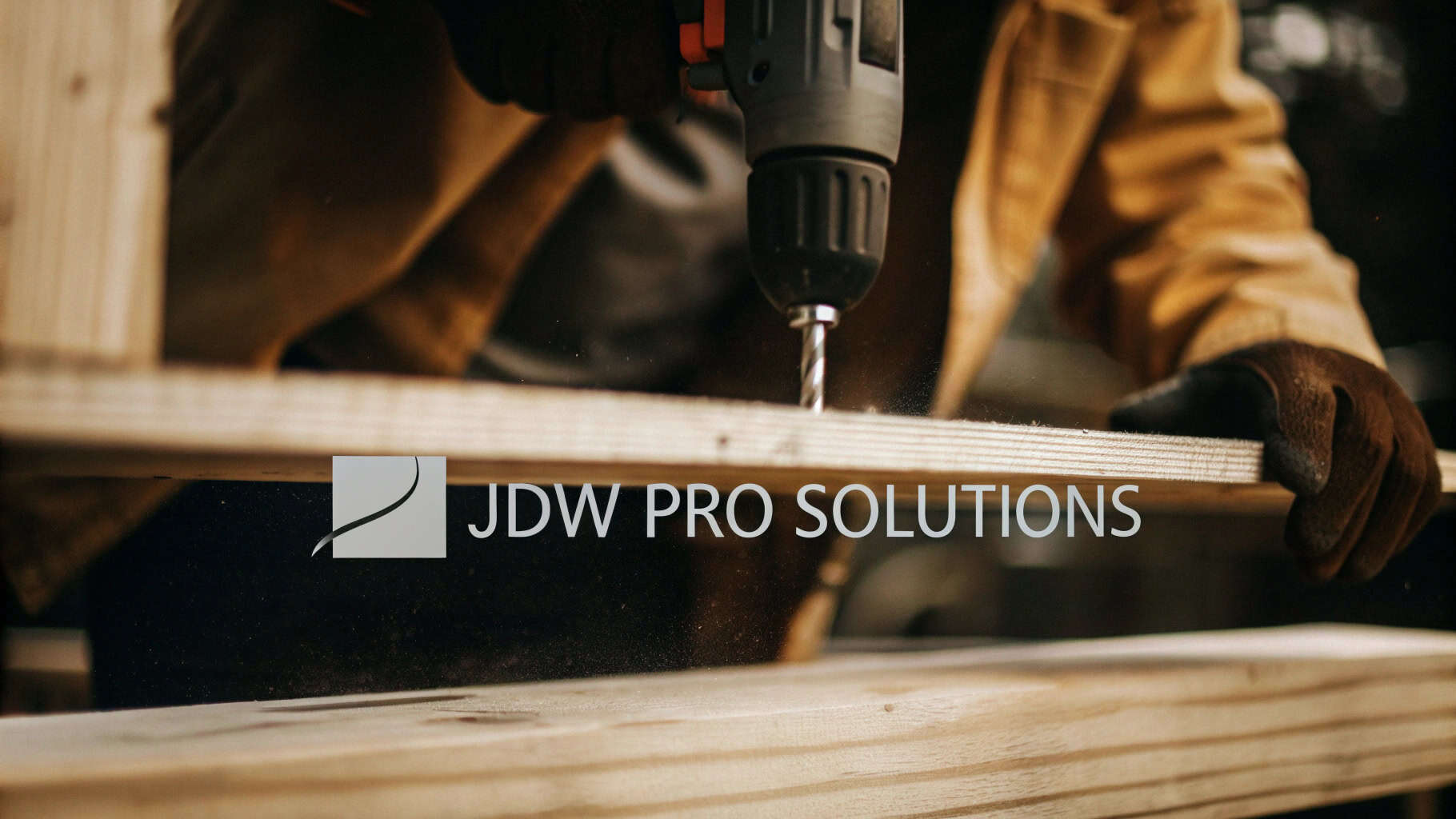
Laser Tools to Remove Knots
Knots in wood can cause big problems. They make wood weaker and harder to use. Laser grading tools help solve this issue. These tools scan the wood and find knots quickly. After spotting them, the system removes the knots neatly. This leaves the wood smooth and strong. Using this method saves time and reduces waste. It’s a great solution for handling large amounts of wood.
Steam Fixing for Warped Wood
Warped wood can mess up projects easily. Bent, cupped, or twisted boards are hard to work with. Steam fixing is a great way to solve this. It uses steam to soften the wood fibers. This helps straighten bent or twisted pieces. I’ve seen how it makes warped wood straight again. This process makes the wood usable and saves materials.
Resin Filling for Cracks
Cracks in wood start small but grow bigger over time. They can ruin the wood if not fixed. Resin filling is a smart way to repair cracks. A special resin is injected into the cracks, filling them completely. Once it hardens, the wood becomes strong again. This method works well for fixing expensive wood. It’s fast, effective, and saves money.
Heat Treatment to Kill Pests
Pests can destroy wood quickly. Tiny bugs can hide inside and ruin shipments. Heat treatment is a safe way to fix this. It heats the wood to kill pests and their eggs. This method is eco-friendly and avoids harmful chemicals. It’s perfect for shipping wood to other countries. Heat treatment keeps the wood pest-free and ready to use.
Wood Quality Control: 4-Stage Defect Prevention System
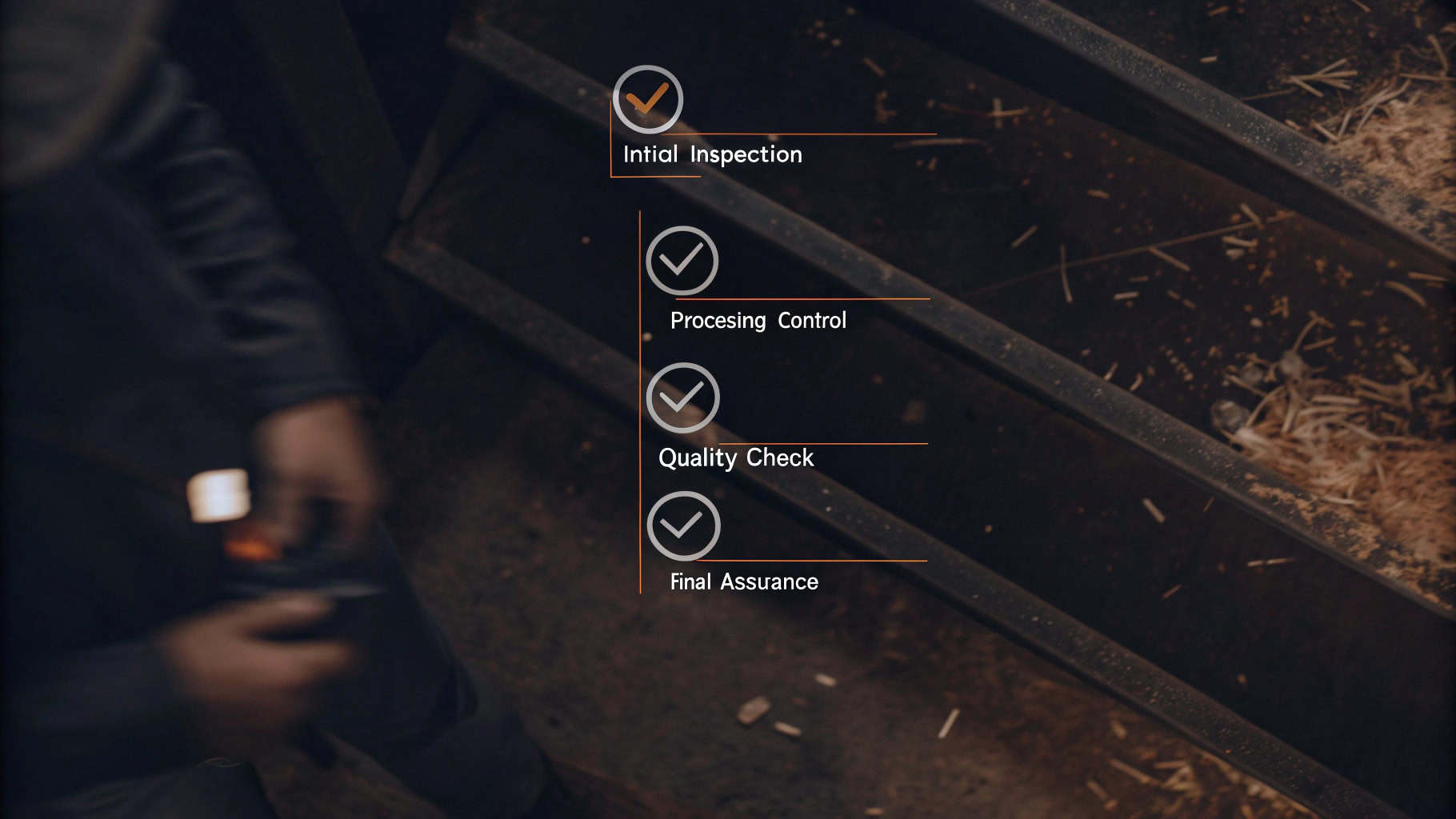
Blockchain Tracking for Raw Material Sourcing
Tracking raw materials is very important. Blockchain technology helps make tracking clear and easy. It keeps a digital record of where the wood comes from. It also shows how it’s handled and who is responsible. This ensures the wood is good before it gets to the factory.
If a shipment has problems, I can trace it back. This helps find the cause and fix it. It also builds trust with suppliers. Blockchain saves time by reducing paperwork. It’s like having a digital notebook for every piece of wood.
AI-Powered Defect Scanning at Receiving Docks
AI scanners make quality checks faster and better. These tools use smart systems to find wood defects quickly. They spot cracks, knots, or warping that are hard to see.
Here’s how these tools work:
Metric | What It Measures |
---|---|
Overall Classification Accuracy | How well defects are correctly identified. |
Pixel Accuracy | How precise the defect detection is at the smallest level. |
The percentage of real defects that are found. | |
False Alarm Rate | How often defects are wrongly identified. |
These scanners catch problems early. This saves both time and money. AI helps stop wood defects from being missed.
Climate-Controlled Storage Protocols
Storing wood properly keeps it in good shape. Climate-controlled storage is the best way to do this. These spaces keep the right temperature and humidity. This stops moisture from causing damage.
For example, wood stored in dry, airy places stays strong. But poorly stored wood often gets damaged. Using climate-controlled storage is a simple way to protect wood and avoid defects.
Pre-Shipping X-Ray Inspection
When it comes to shipping wood, I’ve learned that even the smallest defect can cause big problems. That’s why I always recommend pre-shipping X-ray inspections. This process helps catch hidden issues that might not be visible to the naked eye. It’s like giving the wood a full-body scan before it leaves the warehouse.
X-ray inspection works by scanning the wood for internal defects. It can detect cracks, voids, or even embedded foreign objects like nails. These are things that could ruin the wood’s quality or cause safety issues later. I’ve seen how this technology saves time and money by preventing defective shipments from reaching customers.
Here’s why I think X-ray inspections are a game-changer:
Accuracy: X-rays can spot defects deep inside the wood, where regular inspections can’t reach.
Speed: The process is quick, so it doesn’t slow down shipping schedules.
Reliability: It reduces the risk of sending out bad wood, which could lead to returns or complaints.
Pro Tip: Always schedule X-ray inspections as the final step before shipping. It’s the best way to ensure quality.
I’ve also noticed that X-ray inspections build trust with buyers. When customers know you’re using advanced technology to check for defects, they feel more confident in your products. It’s a small step that makes a big difference in the long run.
If you’re not using X-ray inspections yet, now’s the time to start. It’s an investment that pays off by protecting your reputation and keeping your customers happy.
Cost Analysis: Defect-Related Losses in Wood Processing
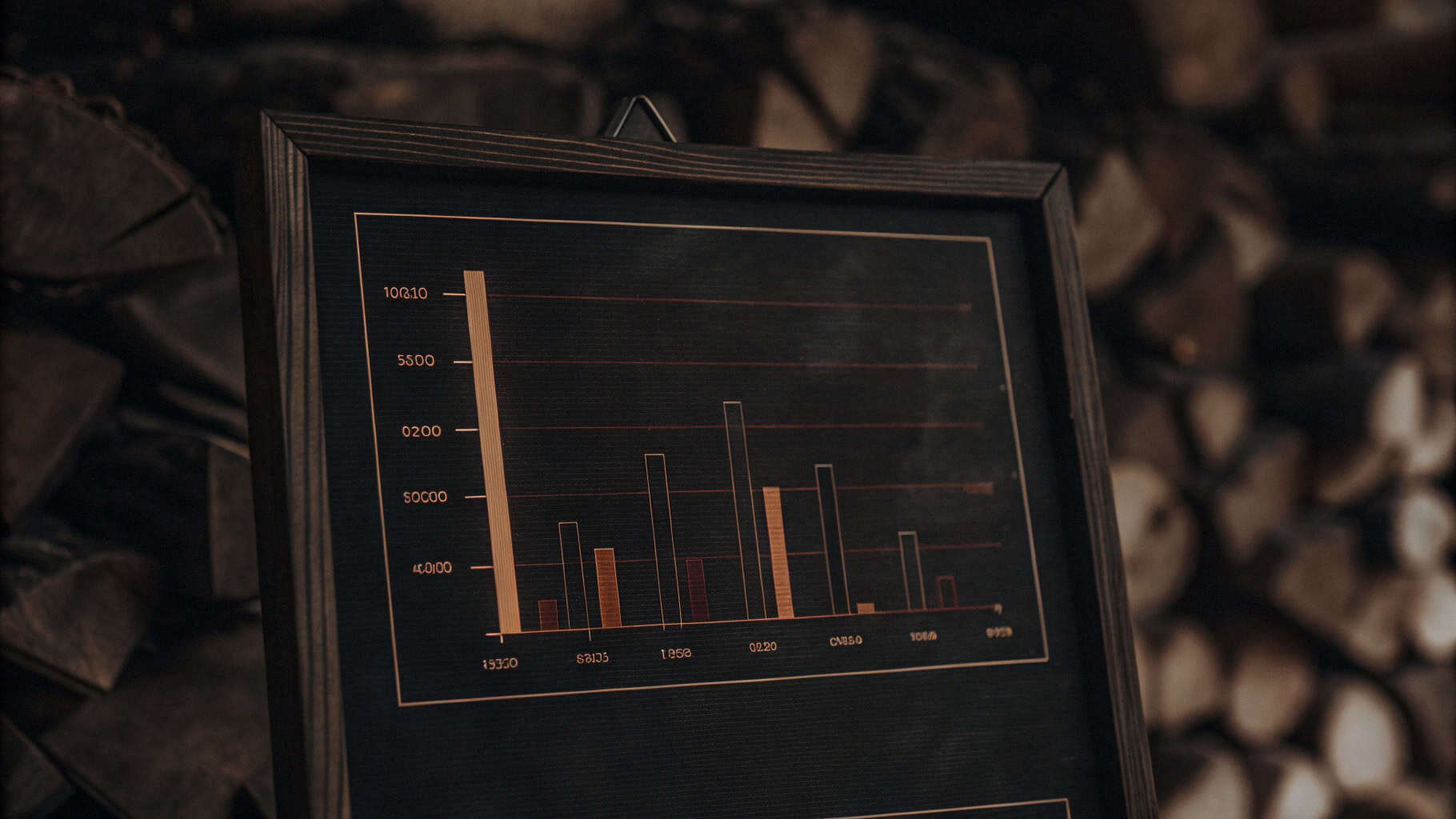
Yield Loss from Natural Defects (Examples)
Natural defects like knots, cracks, and warping can ruin wood batches. I’ve seen cases where entire shipments became useless due to these problems. For instance, one factory lost 15% of its production because of hidden cracks. These cracks weren’t spotted early but caused the wood to break during processing. This led to wasted materials and money.
Another example involved warping. A shipment stored in a damp warehouse warped so badly that only half was usable. The damage didn’t just affect the wood—it delayed the project and raised costs. These examples show how natural defects hurt both productivity and profits.
Rework Costs from Bad Drying Methods
Bad drying methods can cause big problems for wood. I’ve seen uneven drying create internal stress in wood. This often leads to cracks or warping during machining. Fixing these issues takes time and money. One company had to redo 20% of their wood because of poor drying. They had to sand, straighten, or replace damaged pieces.
Rework is expensive and wastes time. Fixing damaged wood means less time for production. That’s why I suggest using proper drying techniques. It’s better to do it right the first time than to fix costly mistakes later.
Customs Problems from Pest Infestation
Pests can ruin wood shipments and cause customs rejections. Officials often reject shipments if they find bugs or signs of infestation. I’ve heard of entire containers being sent back because of tiny pests. The financial loss can be huge. One exporter lost $50,000 on a single shipment due to pest damage.
Heat treatment and fumigation can stop these problems. I always recommend checking for pests before shipping. It’s a small step that prevents big losses. Nobody wants the cost or embarrassment of rejected shipments.
Tip: Inspect wood for pests and meet international standards before shipping.
Warranty Claims from Undetected Cracks
Warranty claims from hidden cracks can cause big problems. Small cracks that go unnoticed can lead to major issues later. For example, a customer might buy wood blocks and find cracks after starting their project. This makes them upset, and they may file a warranty claim. That’s when the real trouble starts.
These cracks often happen because inspections miss them. If not found early, cracks can grow due to stress or weather changes. For instance, wood sent to humid areas might crack during shipping. At first, the cracks are invisible but show up when the wood is used. This results in expensive warranty claims and unhappy customers.
Tip: Always check wood carefully before shipping. Use tools like X-rays or AI scanners to find hidden cracks.
Warranty claims don’t just cost money—they waste time too. Handling claims means checking the problem, replacing the wood, and sometimes paying for delays. All this work could be avoided with better inspections.
Here’s how to lower warranty claims:
Use better inspection tools: Tools like acoustic testing can find cracks early.
Train your workers: Teach them how to spot cracks and defects.
Keep records: Write down all inspections and checks to solve issues faster.
Finding cracks early saves money and keeps customers happy. A little effort now can prevent big problems later. You’ll be glad you did! 😊
JDW Certification: Industry-Standard Compliance Solutions
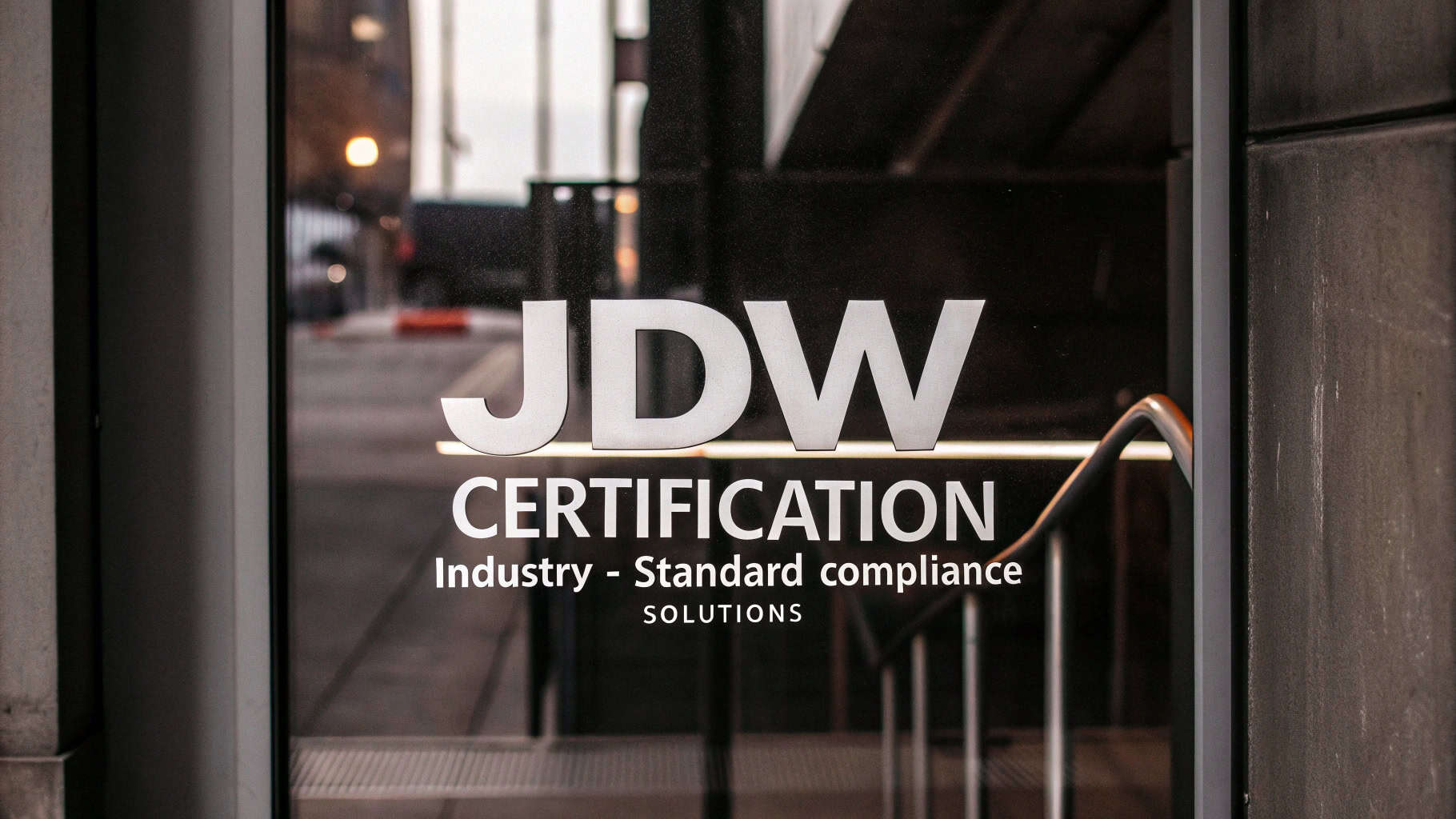
ISPM-15 Compliance for Global Shipments
Shipping wood worldwide can be challenging. Untreated wood may carry pests that harm ecosystems. That’s why ISPM-15 is important. This global rule ensures wood packaging is treated to stop pests. Over 180 countries, including the EU, follow this standard. It’s a must-know for the wood industry.
ISPM-15 requires wood to be debarked and treated. Two main methods are used: heat treatment and fumigation. Heat treatment kills pests by heating the wood to a set temperature. Fumigation uses chemicals to do the same. Both methods make wood safe for shipping.
Tip: Always confirm your wood packaging meets ISPM-15 rules before shipping. It prevents delays and customs problems.
ASTM D5456 Grading Implementation
For structural wood, ASTM D5456 is the top standard. It applies to engineered wood like laminated veneer lumber (LVL) and glued laminated timber (glulam). This standard ensures these materials meet strict safety and strength rules.
ASTM D5456 tests wood for strength, stiffness, and durability. For example, it checks if LVL can hold heavy loads without bending. This gives buyers confidence in the wood’s quality. Following this standard avoids future issues. It’s a smart choice for structural projects.
EN 350 Durability Classification
Durability is key for outdoor wood. EN 350 rates wood based on its resistance to decay and pests. This standard is helpful for picking wood for outdoor furniture or buildings. It ranks wood from “very durable” to “not durable.”
For instance, teak is rated very durable, while pine is less durable. Knowing this helps choose the right wood for the job. It also saves money by cutting down on repairs.
Pro Tip: Use EN 350 ratings to pick wood that lasts longer outdoors. It’s a smart investment!
JAS Certification for Selling Wood in Asia
Selling wood in Asia is easier with JAS Certification. This certification helps open new markets and gain buyers' trust. JAS stands for Japanese Agricultural Standard. It sets strict rules for wood quality, safety, and sustainability. Meeting these rules shows your products are reliable and meet high standards.
JAS Certification improves market acceptance. It’s not just about following rules—it shows you care about quality. Here’s why it works:
JAS India has AEO certification, trusted worldwide. This proves businesses are safe and reliable trade partners. It helps build trust in Asian markets.
JAS Japan holds IATA CEIV Pharma certification. This ensures strict safety and compliance, especially for shipping medicines. It shows JAS-certified companies stand out in Asia.
These certifications impress buyers. They show your company values safety and quality. Customers always appreciate that.
JAS Certification also makes exporting easier. Many Asian countries prefer JAS-certified products. This means fewer customs delays and less risk of rejection. It’s like a fast pass for shipments. It saves time and money.
If you want to grow in Asia, JAS Certification is a smart choice. It’s more than approval—it builds trust and helps your business grow. It’s an investment worth making. 😊
Advanced Defect Detection Technologies for Bulk Buyers
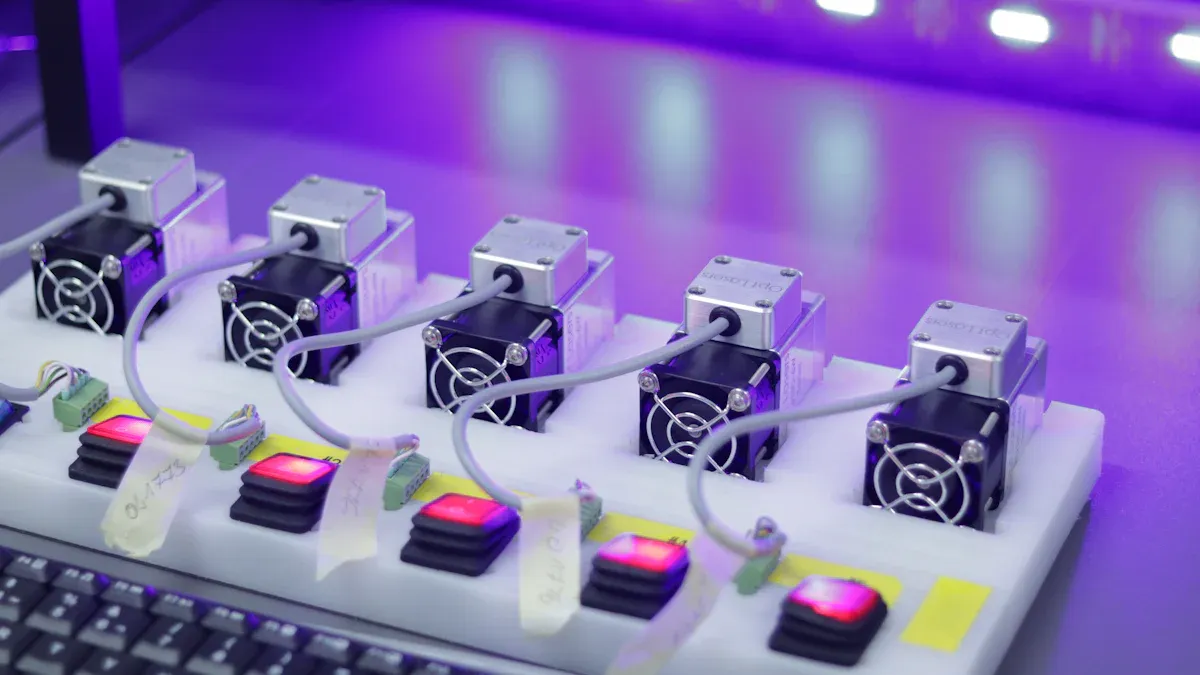
Hyperspectral Imaging for Early Decay Detection
Wouldn’t it be great to find decay early? Hyperspectral imaging makes this possible. It uses light to spot decay in wood before it spreads. Think of it as a health check for wood before it leaves the factory.
This technology is very accurate. It finds tiny surface changes that people might miss. Catching decay early saves both time and money. The best part? It doesn’t harm the wood during the process.
Tip: Use hyperspectral imaging at the start of inspections. It ensures your wood is free from decay right away.
3D Scanning for Warpage Measurement
Warped wood can ruin projects quickly. That’s why 3D scanning is so helpful. It measures wood shapes with great detail, like a perfect digital ruler.
The scanner creates a virtual model of the wood. It shows bends, twists, or curves that could cause issues. This helps remove bad pieces before production begins.
Here’s how advanced tools improve defect detection:
Evidence Description | Key Findings |
---|---|
Wood defect detection based on the CWB-YOLOv8 algorithm | Improves timber quality and reduces waste, saving money and resources. |
Advances in deep learning technology | Finds wood defects better than older methods. |
Enhanced YOLOv8 algorithm | Handles tricky defects and boosts detection accuracy with custom datasets. |
These tools don’t just find problems—they stop them from becoming costly mistakes.
Acoustic Emission Testing for Internal Cracks
Internal cracks are hard to find. They hide inside the wood and cause problems later. Acoustic emission testing solves this by “listening” for crack sounds. It’s like a stethoscope for wood.
This method is quick and precise. It finds cracks that other tools might miss. It’s especially useful for checking expensive wood where every piece matters.
Pro Tip: Use acoustic testing with X-rays for the best results. Together, they ensure your wood is crack-free.
These technologies are more than tools—they’re game-changers. They help catch problems early, save money, and improve product quality. If you’re not using them yet, now’s the time to start. 😊
IoT-Enabled Moisture Monitoring Systems
Did you know too much moisture can ruin wood? I’ve seen it happen often. When wood gets too wet, it bends, rots, or attracts pests. That’s why controlling moisture is so important. Thankfully, IoT-enabled systems make it super easy.
These systems use smart sensors to check moisture levels all the time. They send updates to your phone or computer instantly. No more guessing or checking by hand! Here’s why they’re awesome:
Real-Time Alerts: Get warnings if moisture goes too high or low.
Data Tracking: See moisture trends over time to stop future problems.
Remote Monitoring: Check moisture levels from anywhere, even on vacation.
Pro Tip: Set alerts for specific moisture levels to catch issues early.
These systems save both time and money. For example, one company I know cut wood waste by 20% after using IoT sensors. They fixed moisture problems fast and avoided big losses.
If you handle large wood shipments or need special storage, these systems are amazing. It’s like having a 24/7 helper for your wood. Once you try it, you’ll never go back. 😊
Custom Fixes for Big Wood Factories
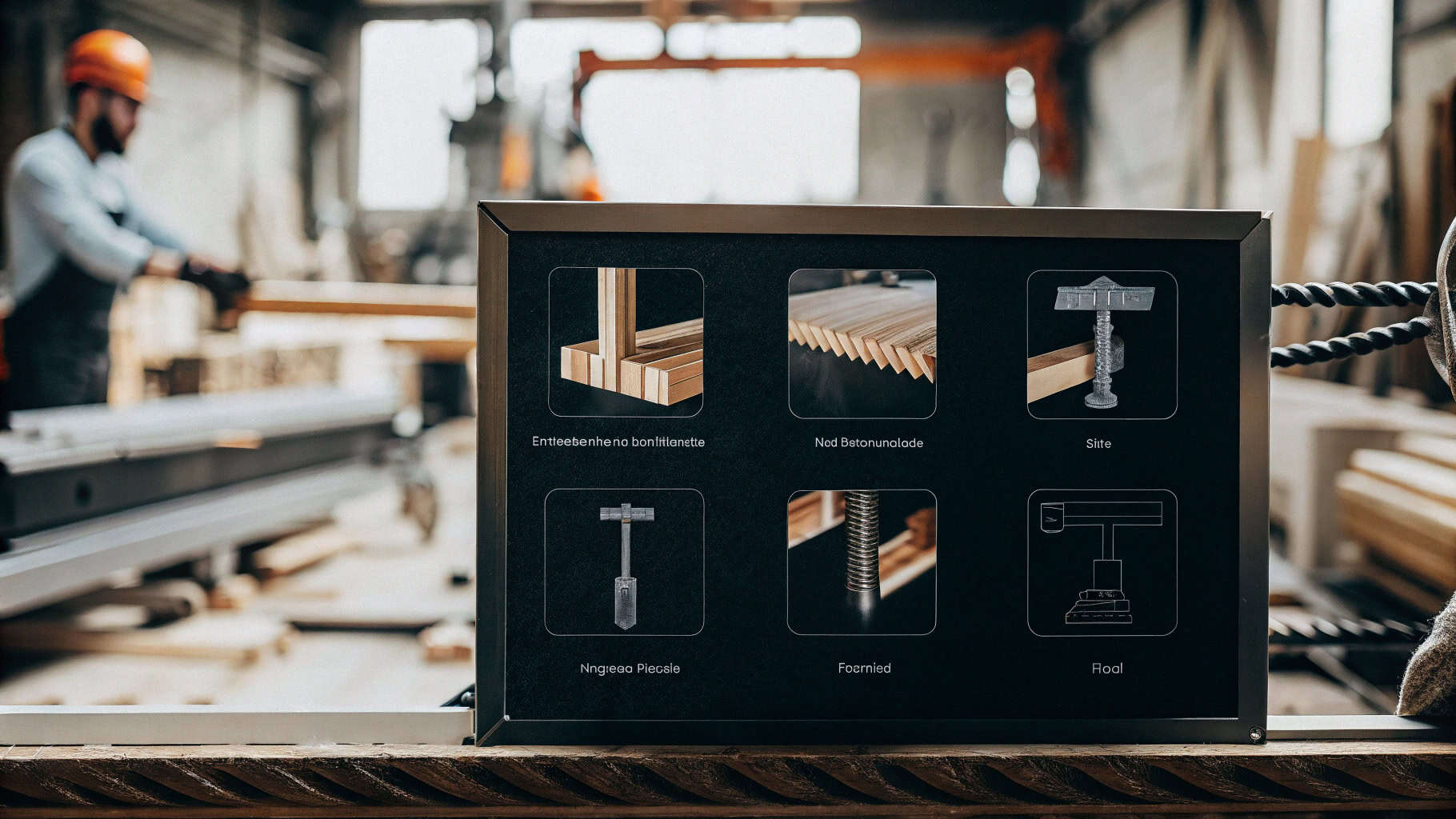
On-Site Drying Kilns for Faster Work
Drying wood can be tough for big factories. On-site drying kilns make it easier. These kilns are set up at your factory, saving time and cutting shipping costs. It’s like having your own drying machine right there.
The cool thing? These kilns can be adjusted to your needs. For example, faster drying schedules can dry wood quickly without hurting quality. This helps finish projects on time and avoids shipping delays. Everyone wins with this setup.
New ideas in wood drying have made things better. Faster drying methods save time and lower costs. Research also helps clean wastewater from wood treatments using eco-friendly methods.
If you handle lots of wood, on-site kilns are super helpful. They’re fast, save money, and fit your needs perfectly.
Smart Software to Spot Wood Problems
Wood defects can be tricky to find. They often stay hidden until it’s too late. Smart software can fix this. It scans wood for cracks, knots, or bends. Then, it makes a map showing where the problems are.
This tool saves time and reduces waste. You don’t need to check each piece by hand. The software does it for you. It’s like having a helper that never misses anything. If you want better quality and faster work, this is a great tool.
Quick Help for Bad Shipments
Bad shipments can cause big trouble. Sometimes, pests or decay ruin entire containers. That’s why having a quick action plan is so important. These plans include fast checks, treatments, or even replacements.
For example, eco-friendly methods can clean up pollution. A study showed land farming can fix problems cheaply and well. Acting fast can save shipments and cut losses.
When problems happen, being ready is key. It helps protect your business and keeps customers happy.
Annual Defect Prevention Audits
Annual defect prevention audits are like a yearly check-up for wood processing. Skipping these checks can lead to expensive mistakes. That’s why they should always be a priority. They help find small problems before they become big issues.
Here’s how audits work. A team reviews every part of your process, from getting raw materials to shipping finished wood. They search for weak points, like bad drying or poor storage. Then, they suggest fixes to improve things. It’s simple but makes a big difference.
Pro Tip: Plan audits during slow times to avoid work delays.
Audits also boost efficiency. For example, one factory had warped wood because of bad ventilation. During their audit, this issue was found and fixed. It saved them thousands of dollars in wasted wood.
A typical audit might include:
Moisture Testing: Checks if wood has the right moisture level.
Equipment Checks: Ensures machines work correctly.
Inspection Training: Teaches workers to spot defects early.
Process Reviews: Finds steps that need improvement.
Audits aren’t just about finding problems. They help create systems to stop defects from happening. Investing in audits means better quality, happy customers, and fewer problems later. It’s totally worth it! 😊
Sustainable Defect Management: JDW Eco Protocols
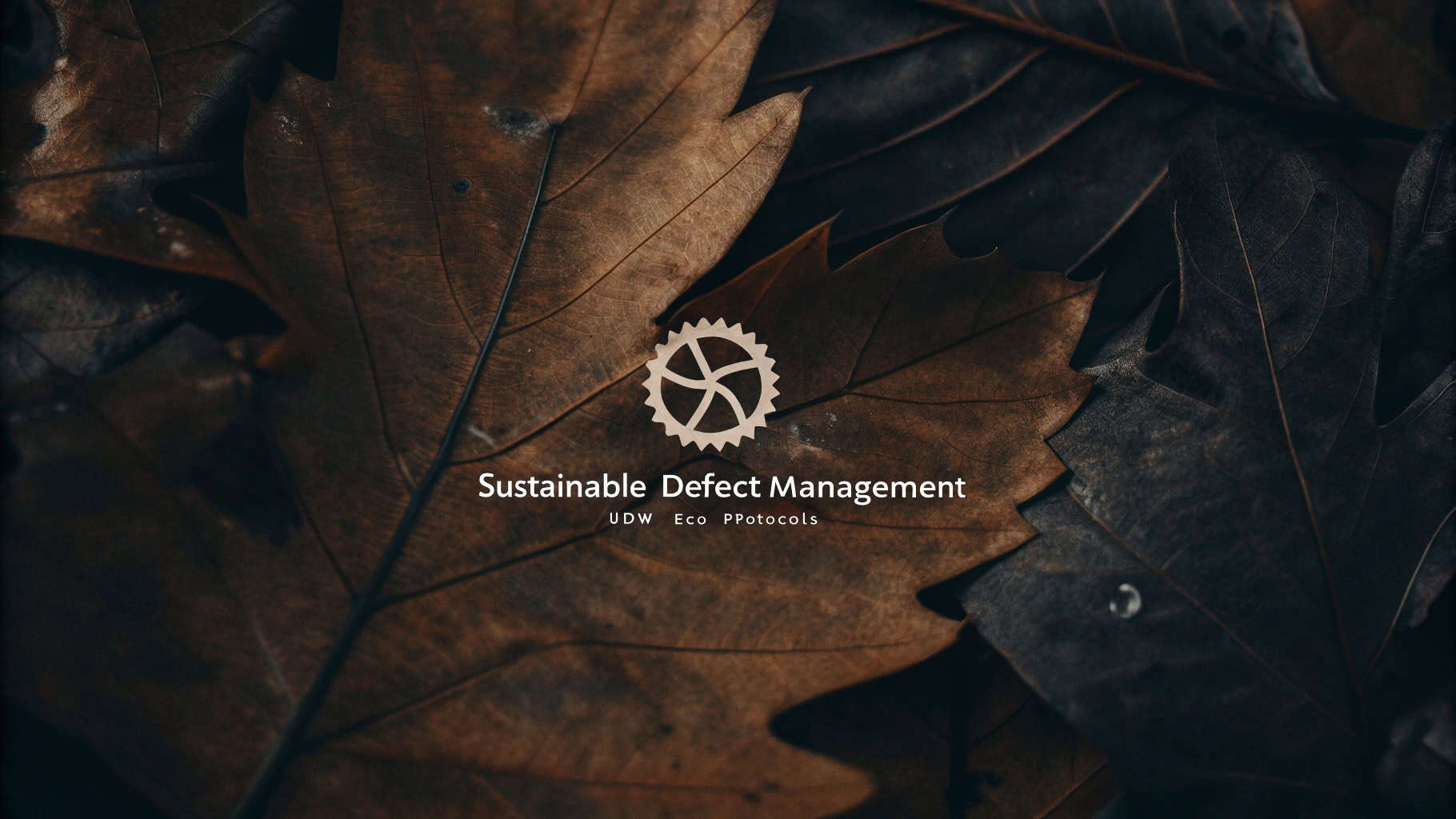
Plant-Based Resin for Cracks
Plant-based resins are changing how wood cracks are fixed. These resins come from plants, not oil, making them eco-friendly. They fill cracks well and make wood stronger.
Here’s a simple table about eco-materials:
Topic | Details |
---|---|
Green composites | How composites are made more sustainable. |
Types of eco-materials | Differences between plant-based, biodegradable, and recyclable options. |
Life cycle assessment (LCA) | Checking a product’s environmental impact for better marketing. |
New ideas for eco-building materials | Finding greener ways to make building materials. |
These resins help the planet and meet green goals. They also reduce waste and make repairs last longer. It’s good for both businesses and nature.
Eco-Friendly Heat Treatment
Heat treatment makes wood stronger but uses lots of energy. Carbon-neutral heat treatment fixes this by using solar or biomass energy. This cuts carbon emissions and keeps the process green.
This method helps the environment and improves wood quality. Treated wood lasts longer and resists pests better. It’s a smart choice for eco-conscious projects.
Reusing Water in Factories
Water is key in wood processing, but wasting it isn’t smart. Closed-loop water systems clean and reuse water in factories. This saves water and lowers costs.
These systems filter out dirt and keep water usable. They reduce the need for fresh water and show care for the planet. If you want greener operations, this is a great step forward.
Phyto-Sanitation for Organic Decay Control
Organic decay can ruin wood fast, especially in wet places. Phyto-sanitation helps stop this naturally. It uses plant-based solutions to protect wood and is eco-friendly.
This method applies plant oils or extracts to the wood. These natural ingredients fight fungi and bacteria that cause decay. Neem oil is a common choice because it works well and is safe. Tea tree oil and eucalyptus extracts are also effective options.
Here’s why phyto-sanitation is a smart choice:
Eco-Friendly: It avoids using harmful chemicals.
Cost-Effective: Plant-based treatments often cost less than chemical ones.
Safe: It’s non-toxic, great for furniture or home-use wood.
Pro Tip: Test a small spot first. Some oils might change the wood’s look.
Phyto-sanitation works better with good storage. Keep wood dry and in airy spaces to make treatments last. Regular checks help catch decay early and prevent bigger problems.
If you want a natural way to protect wood, try phyto-sanitation. It’s easy, works well, and helps the planet. Plus, it feels good to use an eco-friendly solution. 🌱
Global Import Compliance: Defect Prevention Checklist
Moisture Content Rules by Location
Different places have different rules for wood moisture. Keeping the right moisture level is very important. It stops wood from bending, rotting, or causing customs problems. For example, in the U.S., construction wood must stay under 19% moisture. In Europe, furniture wood often needs moisture levels below 12%.
Always check the rules for where you’re shipping. Missing this step can cause delays or rejected shipments. Use moisture meters to check levels. These tools are quick and accurate, helping you meet the rules before shipping.
Pro Tip: Check moisture levels twice—after drying and before shipping. This small step avoids big problems later.
Pest Control Rules and Databases
Pests are a big problem when shipping wood worldwide. Many countries have strict rules to stop harmful bugs. A pest-filled shipment can cause serious trouble. The prohibited pest species database is very helpful. It lists pests to avoid for safe shipping.
Here’s how the database helps:
Evidence Type | Description |
---|---|
Pest Interception | 95% of pests caught by APHIS inspectors are on the IPPC list. Following IPPC rules improves safety. |
Regulatory Framework | IPPC Guidelines protect forests and farms by controlling pests in wood packaging. |
This database is a great tool. It helps find risks early so you can fix them. I suggest working with pest experts to keep shipments pest-free.
Customs Paperwork for Smooth Shipping
Customs paperwork can be confusing but is very important. Missing or wrong documents can delay shipments or cause fines. Each country has its own rules, so staying organized is key.
Common documents include phytosanitary certificates, fumigation reports, and import permits. These prove your wood is safe and meets quality standards. Keep a checklist to avoid missing anything. A customs broker can also help with specific country rules.
Tip: Save all shipping documents in a digital folder. This makes them easy to find and share when needed.
Being careful with customs paperwork takes time but is worth it. It keeps shipments on track and customers happy.
Fumigation Certificate Validity Periods
Shipping wood internationally needs fumigation certificates. These prove the wood is treated to remove pests and meet safety rules. But certificates don’t last forever. Their validity depends on the country and treatment type.
Most certificates stay valid for 21 to 30 days. This ensures the wood stays pest-free during shipping. Some countries have stricter rules. For example, some certificates only last 14 days. Always check the destination’s requirements carefully.
Tip: Ask your fumigation provider about the certificate’s validity before shipping. This avoids last-minute problems.
Here’s what to check on the certificate:
Treatment Date: When the fumigation was done.
Expiration Date: The date the certificate stops being valid.
Destination Rules: Some places need extra documents, like a phytosanitary certificate.
Keep digital copies of certificates for easy access. Customs officials may ask for them. Staying organized prevents delays and stress.
If you’re unsure about the rules, ask a customs broker or fumigation provider. They can help you follow the regulations. It’s better to be safe than face issues later. 😊
Future-Proofing Strategies: Smart Factory Integration
Machine Learning for Predicting Defects
Machine learning has changed how defects are found. It works like a smart helper that spots issues early. One great tool is the LSTM (Long Short-Term Memory) model. It studies patterns over time to catch problems fast. This helps factories avoid costly delays.
Here’s a simple table comparing LSTM and Random Forest:
Metric | Random Forest | |
---|---|---|
Precision | 95% | 80% |
Sensitivity | 90% | 75% |
F1 Score | 92.5% | 77% |
Training Time | Shorter | Longer |
LSTM is faster to train and works better. It gives correct alerts 90% of the time, with only 10% mistakes. Alerts appear in 2.5 seconds, and fixes start in 5 seconds. This speed makes it perfect for smart factories.
RFID Tags to Track Defects
RFID (Radio Frequency Identification) tags are super helpful. They track each wood piece from start to finish. If a defect appears, I can find its source quickly. Each tag stores the wood’s full history, making problem-solving easier.
This system also improves quality checks. For example, I can see if a supplier often sends bad wood. It’s like having a detective to ensure shipments are top quality.
Automatic Sorting for Defective Wood
Sorting bad wood used to take a long time. Now, machines do it in seconds. These systems scan wood, find defects, and remove bad pieces automatically. It’s quick, accurate, and reduces waste.
With smart factory tools like IoT and AI, these systems work even better. They connect with other machines for smooth production. This setup saves time and ensures only good wood moves forward. It’s exciting to see how this will improve factories in the future.
Real-Time Supplier Quality Dashboards
Do you wish you could monitor suppliers easily? Real-time supplier quality dashboards make this simple. These dashboards show live updates about the materials your suppliers send. It’s like watching their work in real-time, so you know what’s happening.
Here’s how they help. The dashboard gathers data from suppliers and shows it clearly. You can check things like defect rates, delivery times, and rule compliance. For instance, if a supplier sends wood with many defects, the dashboard alerts you right away. This lets you fix problems quickly and avoid bigger issues later.
Pro Tip: Use alerts for important metrics like defects or late deliveries. This keeps you informed instantly if something goes wrong.
These dashboards are great for managing suppliers. They help you notice patterns and hold suppliers accountable. If one supplier always delivers good wood, you can give them more orders. But if another supplier keeps failing, you’ll know it’s time to talk or switch to someone else.
Here’s why these dashboards are so useful:
Clear Information: See how suppliers are performing at a glance.
Time-Saving: No need for manual checks anymore.
Quick Problem Fixing: Spot and solve issues before they grow.
If you’re not using real-time dashboards yet, you’re missing out. They save time, lower stress, and help you make better choices. Once you try them, you’ll wonder how you managed without them! 😊
Wood defects can lead to big issues, like weak wood or ruined shipments. Problems such as knots, cracks, and decay waste both time and money if ignored. The good news is that JDW remedies provide helpful fixes. Tools like lasers for knots and eco-friendly decay treatments save wood and improve quality.
Tip: Fix defects early before they get worse. Try these remedies or ask an expert now. It’s the smartest way to protect your wood and save money! 😊
FAQ
What are the most common wood defects I should watch for?
Knots, cracks, warping, and decay are the big ones. I’ve seen these cause the most trouble in wood processing. Catching them early saves time and money.
How can I prevent wood from warping during storage?
Keep the wood in a climate-controlled space. Make sure the area has good airflow and stable humidity. I always recommend stacking wood properly to avoid uneven pressure.
Is heat treatment safe for the environment?
Yes! Heat treatment is eco-friendly. It doesn’t use harmful chemicals and works by heating the wood to kill pests. I love how it’s both effective and safe for the planet. 🌍
Can I fix cracks in wood myself?
You can! Use resin to fill the cracks. Plant-based resins are a great option if you want an eco-friendly solution. Just follow the instructions, and you’ll have strong, usable wood again.
Why is moisture control so important for wood?
Too much moisture can cause warping, decay, or pest problems. I always use moisture meters to check levels before storing or shipping wood. It’s a small step that prevents big headaches later.