
When I think about woodworking basics, I see how important wood is. Wood isn’t just a material; it supports many industries like furniture and building. Did you know in 1963, about 77% of paper materials came from wood-pulp? This shows how much wood is used in making things. Learning about wood is not just for beginners. It’s important for anyone wanting to get better at woodworking or carpentry.
If you’re new and need a complete guide or want to start woodworking, learning about wood is the first step. It’s like taking beginner classes made just for you. Read this complete guide, and you’ll understand why wood is so important.
Key Takeaways
Knowing wood types is important. Pick hardwood for strong, lasting projects. Use softwood for cheaper and lighter tasks.
The right tools make woodworking better. Get hand tools and power tools for accurate and fast work.
Safety matters in woodworking. Wear safety gear and keep your workspace clean to avoid injuries.
Plan where you get your wood. Look for good quality, fair prices, and trustworthy sellers to keep things running smoothly.
Learn about market trends. Knowing wood prices and demand helps you buy smarter.
Understanding Wood and Why It Matters in Manufacturing
What Is Wood and Why Is It Important?
Wood is more than just a material. It’s essential for making things we use every day, like furniture and buildings. But why is wood so important? It’s about finding the right type of wood, reducing risks, and protecting the environment.
Here’s a simple look at sourcing practices:
Sourcing Practice Aspect | What It Means |
---|---|
Quality of Data | |
Risk Assessment Changes | Adjusts when sourcing locations shift. |
Using Technology | Helps find and fix sourcing problems. |
Procurement teams also think about risks like cutting trees in areas with lots of wildlife. They check suppliers and make sure they follow strict rules like FSC CW and PEFC CS. This ensures the wood is good quality and responsibly sourced.
Important Features of Wood for Industry
Wood has special features that make it great for many uses. Its structure, strength, and durability make it very useful. Here are some key features:
Feature Type | What It Does |
---|---|
Structure | |
Density | Impacts strength, which is important for building. |
Heat Insulation | Keeps heat in or out, useful in different climates. |
Sound Properties | Absorbs sound, great for making musical instruments. |
Durability | Resists damage, so it lasts a long time. |
These features make wood useful for things like houses, instruments, and even utility poles. Its low ability to conduct electricity is another bonus.
Why Wood Is Still Important for Businesses
Wood is still a top choice for businesses because it’s flexible and eco-friendly. It can be reused, recycled, and shaped for many purposes. Whether it’s for furniture or homes, wood is strong and looks great.
For importers, buying wood responsibly helps follow rules and protect the planet. For manufacturers, wood’s strength and beauty make it a smart choice. Knowing about wood helps people make better decisions when buying or using it.
Types of Wood: A Guide for Manufacturers
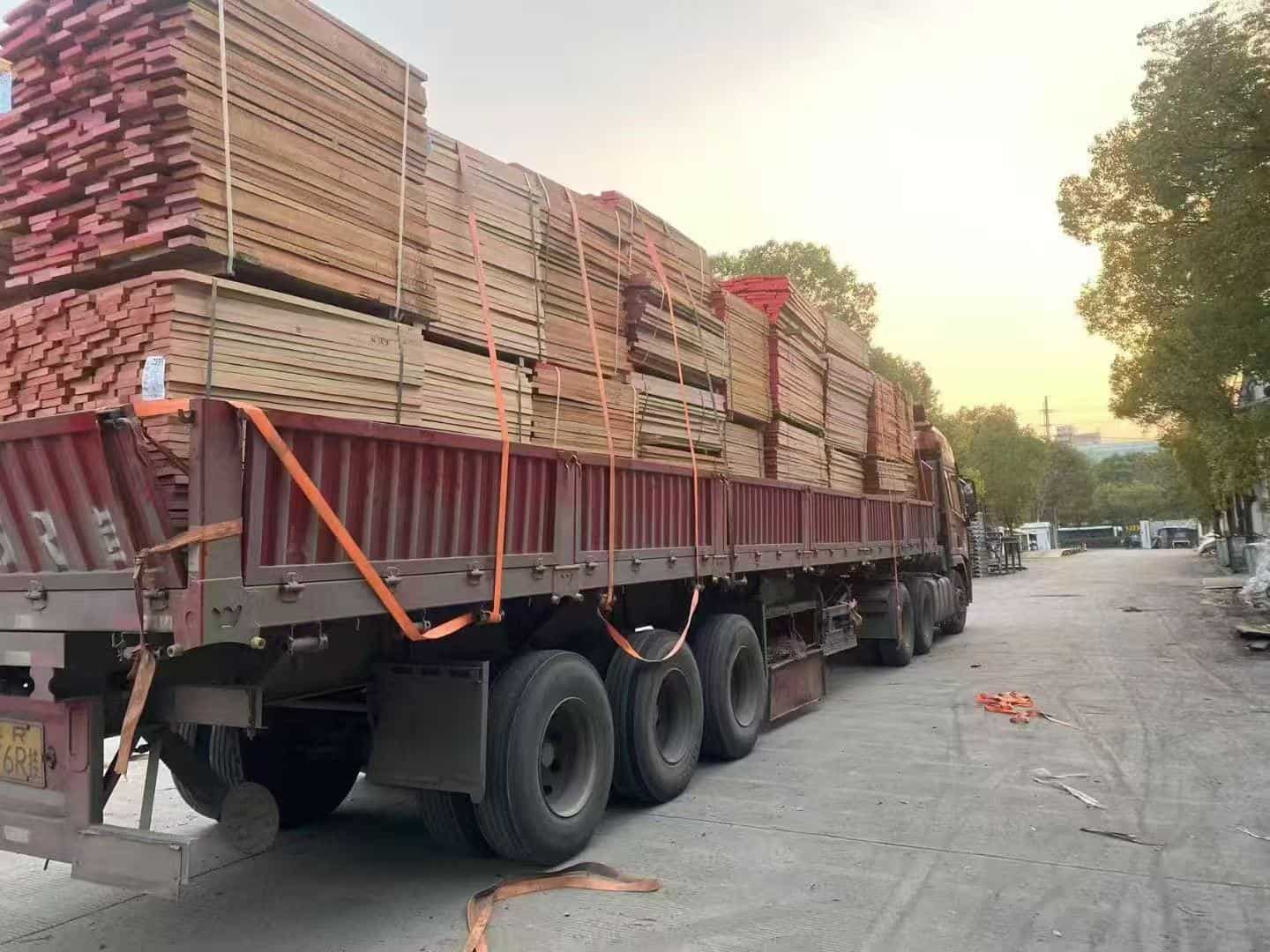
Hardwood vs. Softwood: Which One Should You Pick?
Choosing between hardwood and softwood depends on your project. Hardwood comes from trees like oak and maple. These trees grow slowly, making the wood dense and strong. It’s great for furniture and floors. Softwood, like pine or spruce, grows faster and is lighter. It’s better for construction or cheaper projects.
Here’s a cool fact: hardwoods are easier to process for some uses. They break down faster than softwoods during treatments. This makes them better for industries needing quick wood processing. But softwoods are great for big projects on a budget.
Best Hardwood Types for Industrial Use
Not all hardwoods are the same. Some are better for industries. Oak is strong, lasts long, and looks nice. Maple is smooth and works well for furniture and cabinets. Walnut is fancy with its dark color.
Each hardwood has special qualities. Oak is dense, so it’s good for heavy-duty jobs. Maple’s fine grain is great for detailed work. Always match the wood to the job for the best results.
Top Softwood Types for Affordable Sourcing
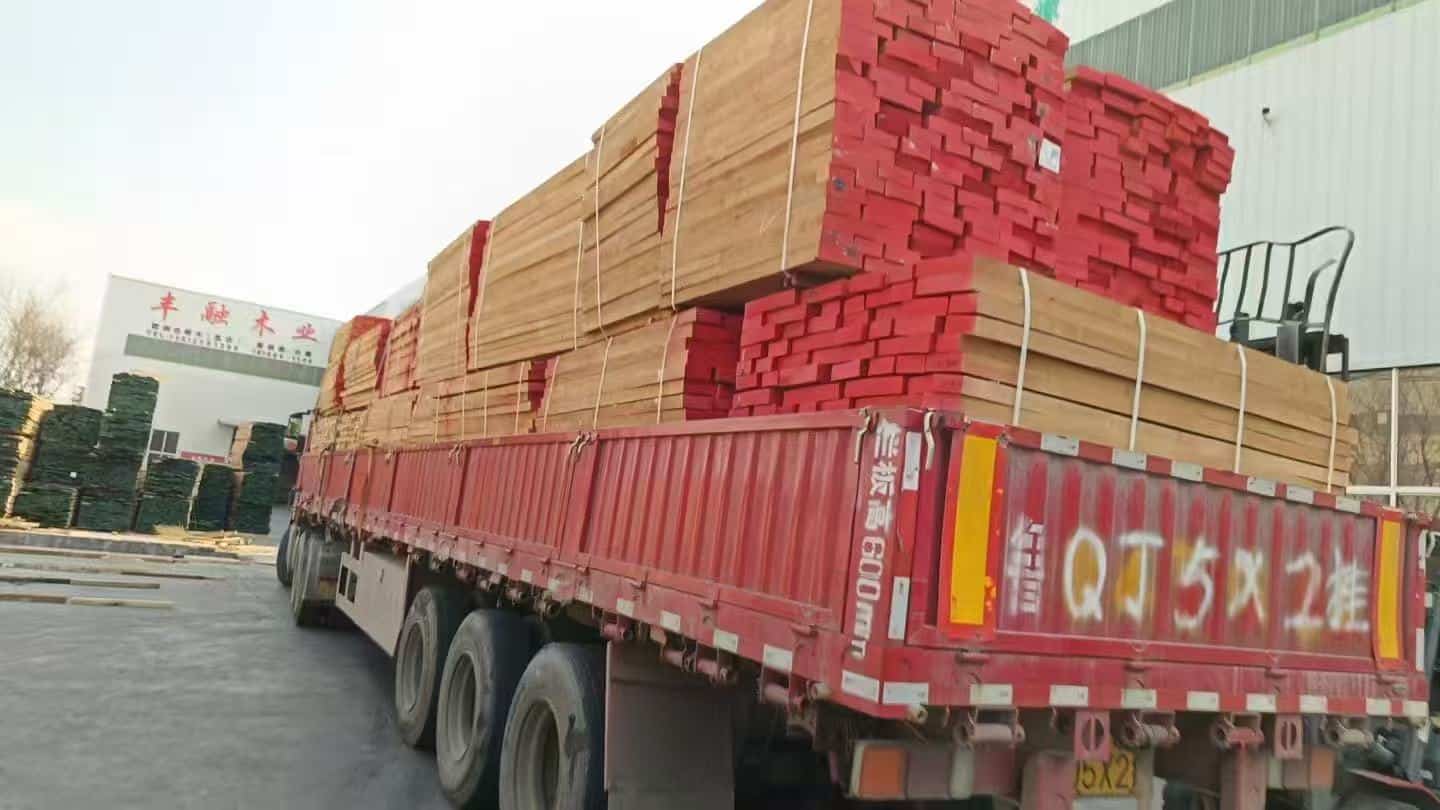
Softwoods are perfect for saving money. Pine is cheap, easy to use, and common. Spruce is light but strong, making it good for building. Cedar is special because it resists rotting, so it’s great outdoors.
Softwoods are useful and cost less. They’re perfect for manufacturers needing a lot of wood without spending too much. Picking the right softwood can save money and still give good quality.
Engineered Wood: Why It’s Great for Big Projects
Engineered wood is perfect for large projects. It makes manufacturing easier and keeps quality steady. Unlike regular wood, it’s made by mixing wood pieces with glue. This process makes it stronger, more stable, and very useful.
One big advantage is its dependability. It doesn’t bend or twist like natural wood. Imagine building something where every piece fits just right. No surprises or wasted materials—that’s what engineered wood offers.
Here’s why it works so well:
Feature | What It Means |
---|---|
Engineered wood holds more weight than regular wood. | |
Stays the Same Shape | It doesn’t bend or twist, keeping its size and shape. |
Less Waste | The way it’s made uses all the wood, so there’s no waste. |
Made from smaller trees, helping save forests. | |
Custom Sizes | Comes in long and wide pieces, saving time and effort. |
Better Performance | Works well for big spans and uses materials more efficiently. |
Manufacturers like engineered wood because it’s good for the planet. It uses smaller trees and creates less waste. That’s better for nature and saves money too.
Another great thing is its flexibility. You can get it in big sizes, so you need fewer pieces. This saves time and makes work faster. Whether for furniture or buildings, engineered wood helps projects go smoothly and costs less.
If you want something strong, steady, and eco-friendly, choose engineered wood. It’s a smart pick for making big projects easier without losing quality.
Essential Tools for Woodworking in Manufacturing
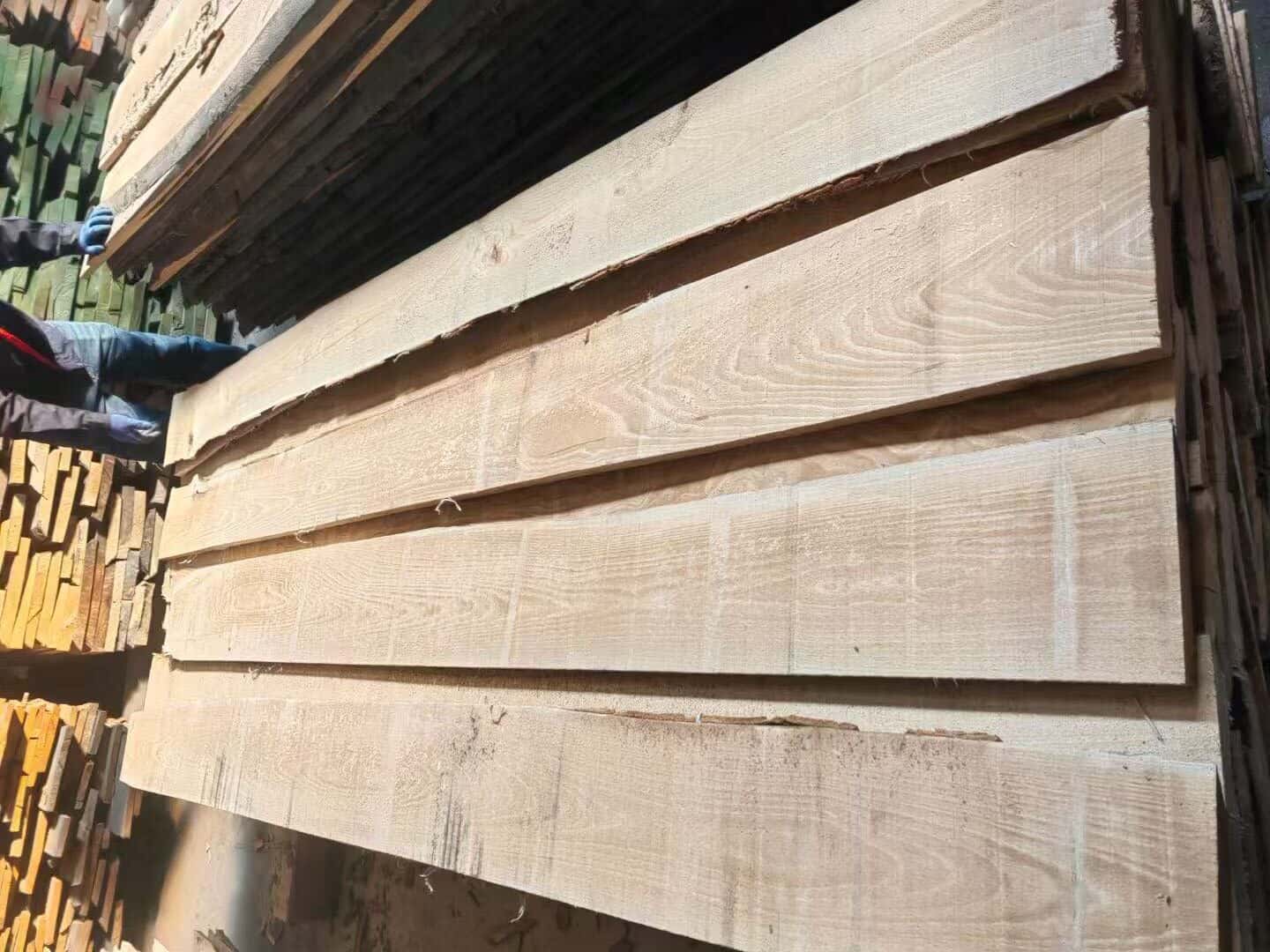
Having the right tools makes woodworking easier and better. Whether making furniture or working on big projects, good tools help with accuracy and quality. Let’s look at some must-have tools for woodworking.
Basic Hand Tools for Detailed Work
Hand tools are simple but very useful. They are great for small, precise tasks. Here are a few important ones:
Chisels: Perfect for carving and shaping wood. They help create fine details or smooth rough spots.
Hand saws: Use a crosscut saw to cut across wood grain. A rip saw is better for cutting along the grain.
Planes: These tools make wood surfaces flat and smooth. A block plane is great for trimming small areas.
Mallets: Use these to hit chisels without breaking them.
These tools may seem old-fashioned, but they’re great for detailed work. If you’re just starting, learning to use these tools is a good first step.
Power Tools for Faster Work
For big projects, power tools save time and effort. They handle large amounts of wood quickly and give consistent results. Machines like table saws, routers, and planers are very helpful.
Here’s why power tools are so useful:
They cut, shape, and process wood much faster than hand tools.
Keeping blades sharp makes them work better and last longer.
Adjusting settings for different wood types saves time and money.
For example, sharp saw blades make cutting faster and protect the machine from damage. Power tools are essential for manufacturers who need to work on a large scale.
Measuring Tools for Accurate Results
Accuracy is key in woodworking. Measuring tools help ensure every piece fits perfectly. Some important tools include:
Tape measures: Great for quick and easy measurements.
Calipers: Measure thickness and diameter with high precision.
Squares: Make sure cuts are straight and corners are perfect.
Marking gauges: Help mark straight lines for cutting or drilling.
Using these tools improves your work and reduces mistakes. Accurate measurements mean less wasted material and better results!
Clamps and Workbenches for Easy Woodworking
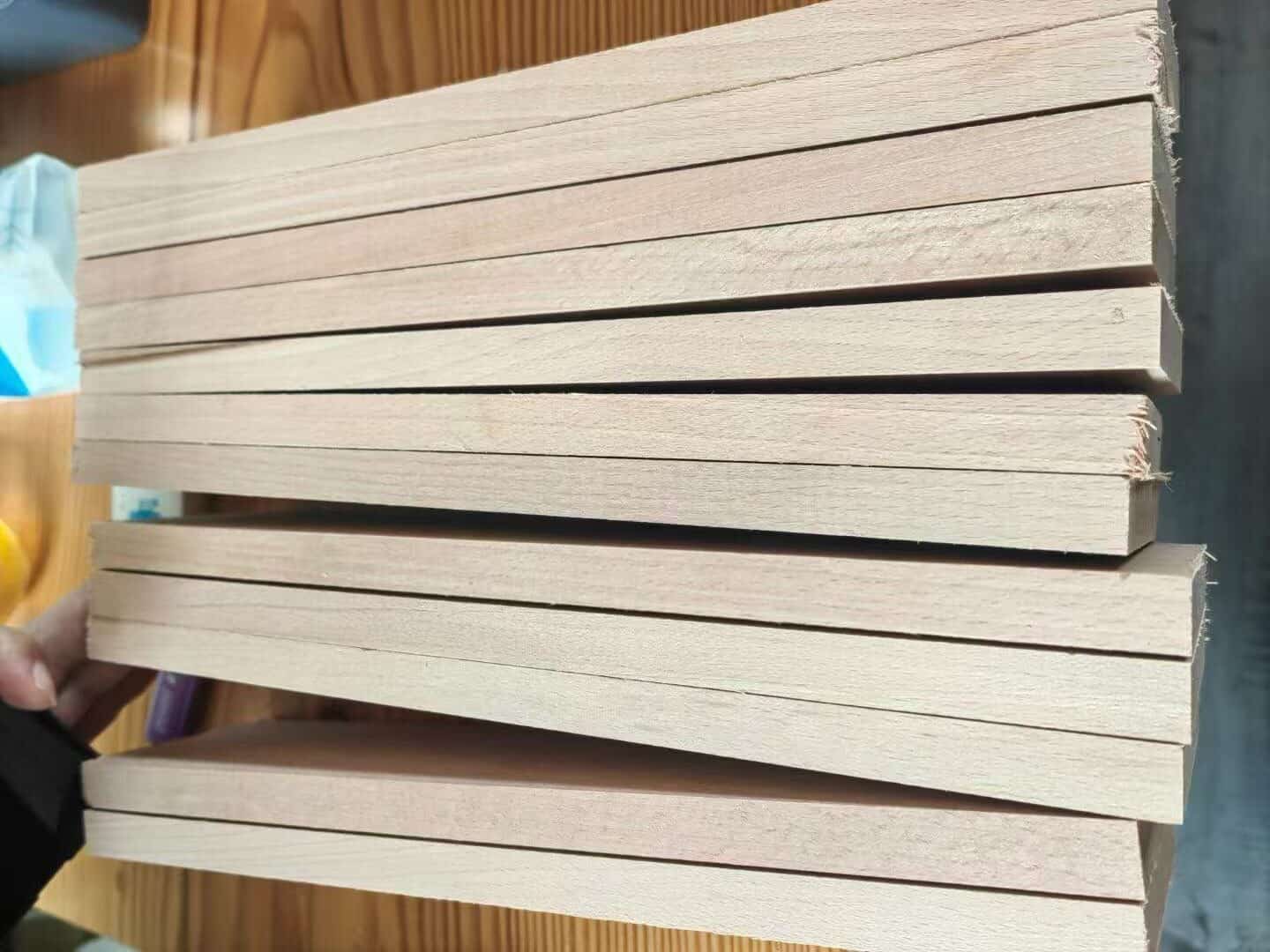
Having the right tools makes woodworking much easier. Clamps and workbenches are super helpful for putting wood projects together. They hold things steady so you can focus on doing a good job.
Let’s talk about clamps first. Clamps keep wood pieces from moving while you work. They’re great for gluing, drilling, or screwing parts together. Bar clamps work well for big projects like furniture. C-clamps are better for small, detailed tasks. Quick-release clamps are handy when you need to adjust things fast. Using good clamps saves time and stops mistakes.
Now, onto workbenches. A strong workbench gives you a flat surface to work on. This helps you assemble wood pieces accurately. Pick a bench with storage for tools to keep everything close by. Some workbenches even have built-in clamps or vises for extra help.
Tip: Secure your workbench to the floor or wall. A shaky bench can mess up your project or cause accidents.
Using clamps and a sturdy workbench makes woodworking faster and better. It’s like having a workspace made just for your needs. These tools improve your work and save time. Whether you’re new or experienced, they’re essential for any wood project.
Safety Measures for Woodworking in Industrial Settings
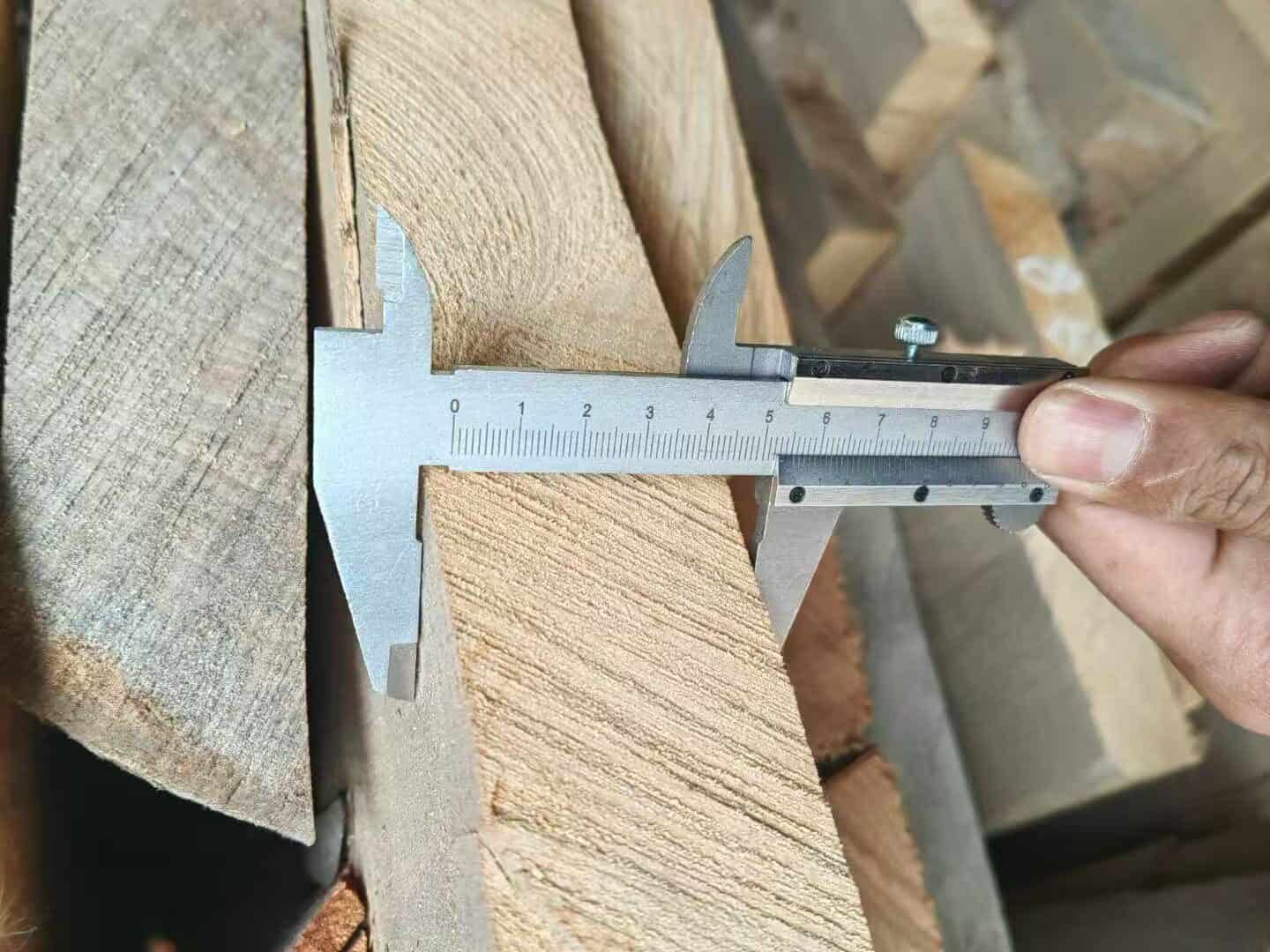
Essential Safety Gear for Factory Workers
Safety gear is very important in woodworking. The right equipment keeps workers safe. PPE like gloves, goggles, and ear protection is a must. Did you know most workplace accidents can be avoided with PPE? About 90% of incidents happen because PPE isn’t used properly. Sadly, only 64% of workers use it the right way. This shows there’s room to improve.
Here’s how PPE helps. Gloves protect hands from sharp tools and splinters. Goggles stop wood chips from hitting your eyes. Earmuffs protect your hearing from loud machines. Dust masks keep harmful particles out of your lungs. Skipping any of these can cause injuries. Make sure everyone has the right gear and knows how to use it.
Best Practices for Safe Tool Operation
Using tools safely is just as important as wearing gear. Always check tools before starting work. Loose parts or dull blades can cause accidents. For example, sharp saw blades cut better and lower the risk of kickback.
Follow the tool’s instructions carefully. They are there to keep you safe. Keep hands away from moving parts. Don’t force tools to do things they aren’t made for. Check power tool cords for damage and keep them out of the way. These simple steps can prevent many problems.
Designing a Safe and Productive Workspace

A clean workspace is safer and more efficient. Clutter can cause accidents. Tripping over wood scraps or cords is dangerous. Always keep your area neat and organized.
Good lighting helps you see clearly and avoid mistakes. Ventilation is also important. Wood dust and fumes can be harmful. Use a fan or dust collector to stay safe. Store tools in labeled spots so you can find them easily. This saves time and keeps the area safe.
Tip: Set up zones for cutting, sanding, and assembly. Keeping tasks separate reduces accidents.
By using safety gear, handling tools properly, and organizing your workspace, woodworking becomes safer and more enjoyable for everyone.
Reducing Workplace Injuries in Wood Processing
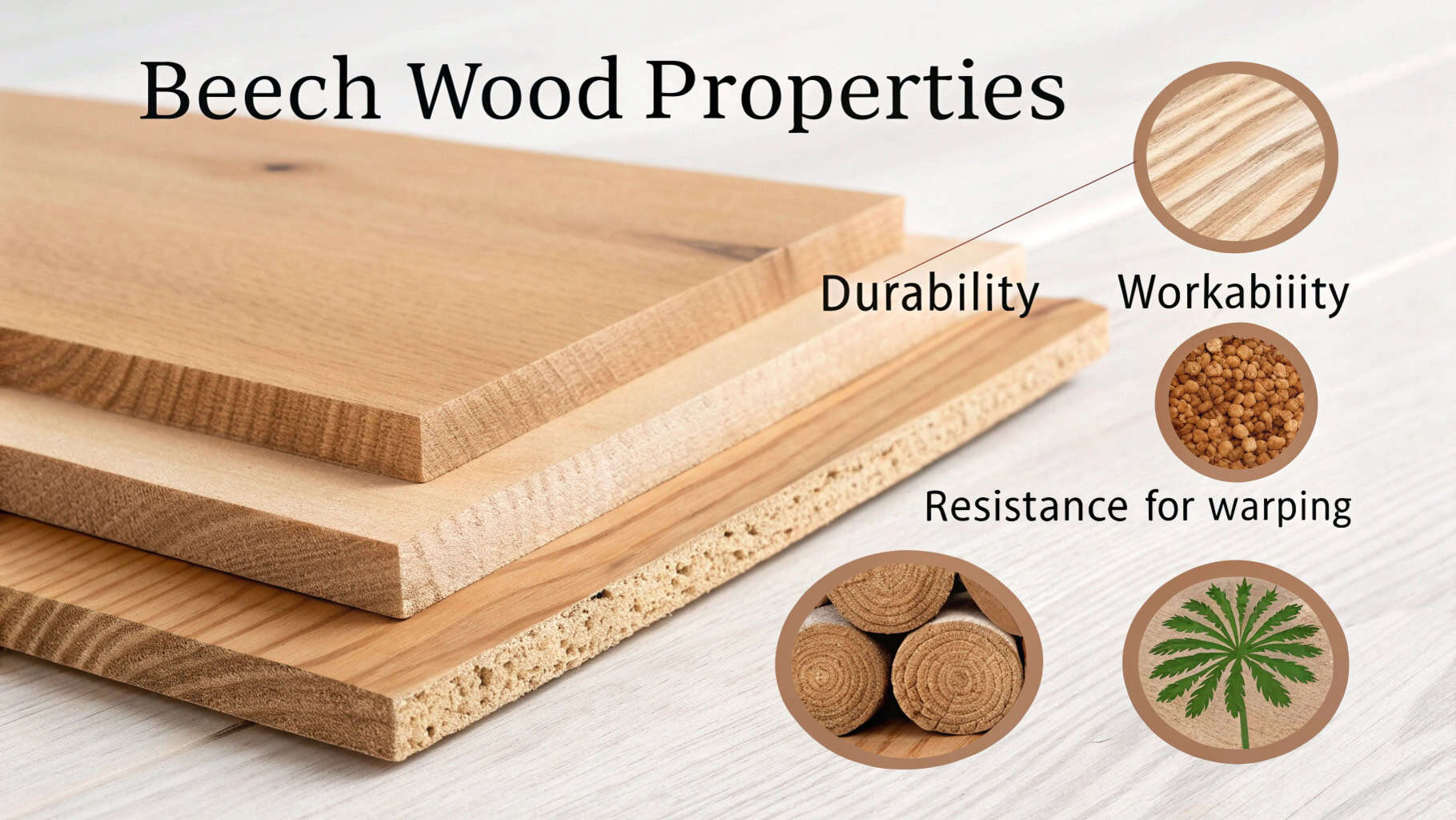
Safety is the most important thing when working with wood. Accidents can happen quickly, but we can stop most of them. Here are some simple ways to keep workers safe in a wood processing area.
1. Train Workers Often
Training helps workers stay safe and avoid mistakes. Teach them how to use tools and machines the right way. A short training session every few months is helpful. For example, showing how to safely use a saw or lift heavy wood can prevent injuries.
2. Check Tools and Machines
Broken tools can cause accidents. Always check machines before using them. Look for loose screws, dull blades, or damaged parts. Fixing tools keeps workers safe and helps them work faster.
3. Keep the Workspace Clean
A messy workspace can be dangerous. Clean up wood scraps, cords, and tools from the floor. This stops people from tripping. Label tool and material storage areas to make finding things easier.
Tip: Use anti-slip mats where workers handle heavy wood. These mats help stop slips and falls.
4. Wear Safety Gear
Wearing safety gear is very important. Workers should use gloves, goggles, and dust masks when handling wood. Ear protection is also needed near loud machines. This protects their hearing over time.
By focusing on training, tool care, cleaning, and safety gear, we can make wood processing safer. Taking these steps reduces risks and keeps everyone protected.
Woodworking Techniques for Efficient Production
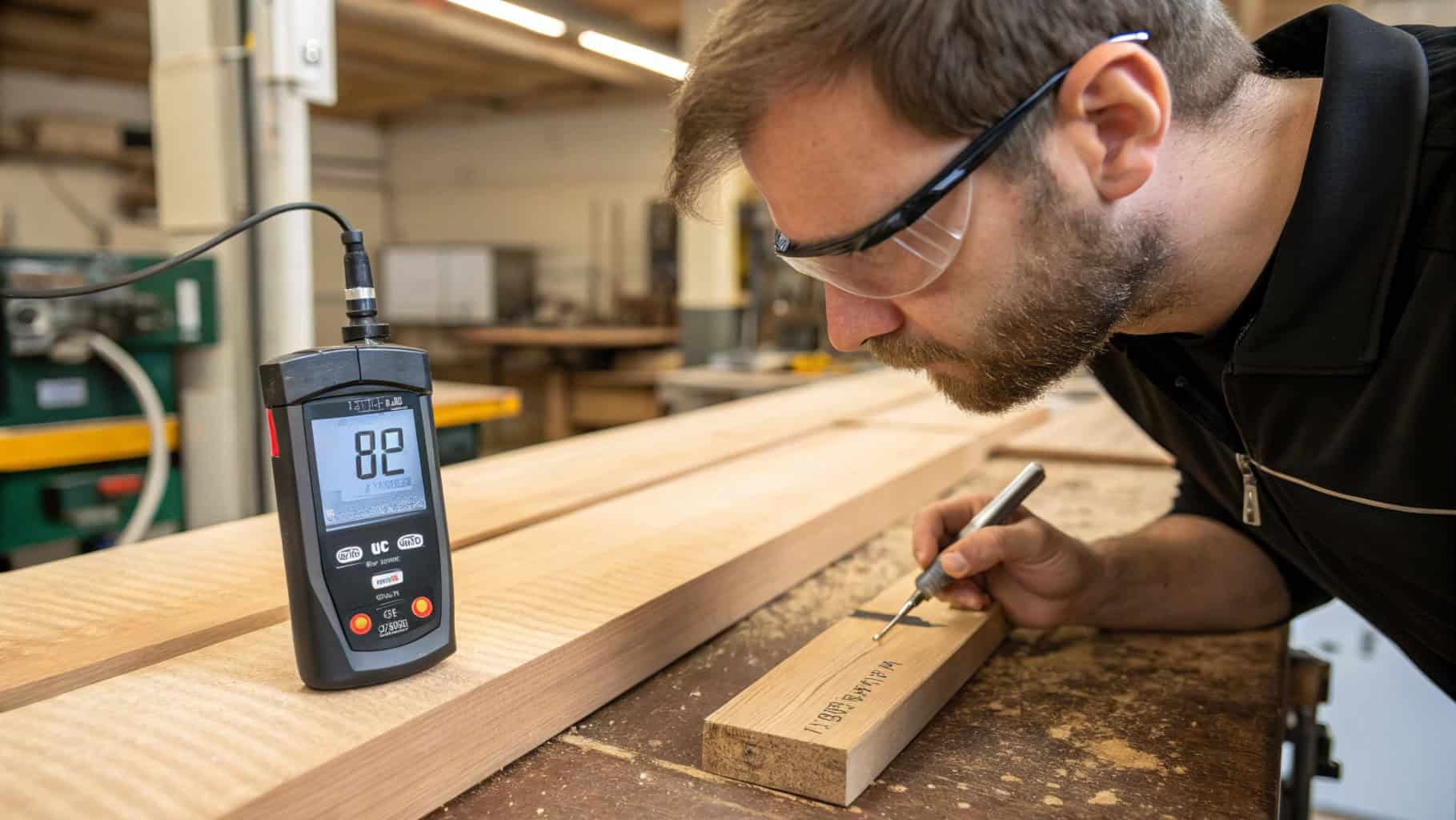
Cutting and Shaping Wood for Bulk Orders
Cutting and shaping wood quickly is important for big orders. Using advanced tools like CNC machines helps a lot. These machines cut wood automatically, saving time and reducing mistakes. They are great for making detailed shapes with accuracy. For example, CNC machines make sure every piece looks the same, which is important for large projects.
Here’s how technology improves production:
Technology | Benefits |
---|---|
CNC Machines | - Makes detailed shapes with high accuracy. |
- Cuts wood automatically, saving time and avoiding mistakes. | |
- Produces identical pieces for big projects. | |
Robotic Helpers | - Speeds up work by running non-stop. |
- Reduces mistakes with precise movements. |
Metrics like OEE (Overall Equipment Effectiveness) and scrap rate help track progress. High OEE means more work gets done, while low scrap rates show less wasted material. These numbers help improve production methods.
Joinery Methods for Durable Products
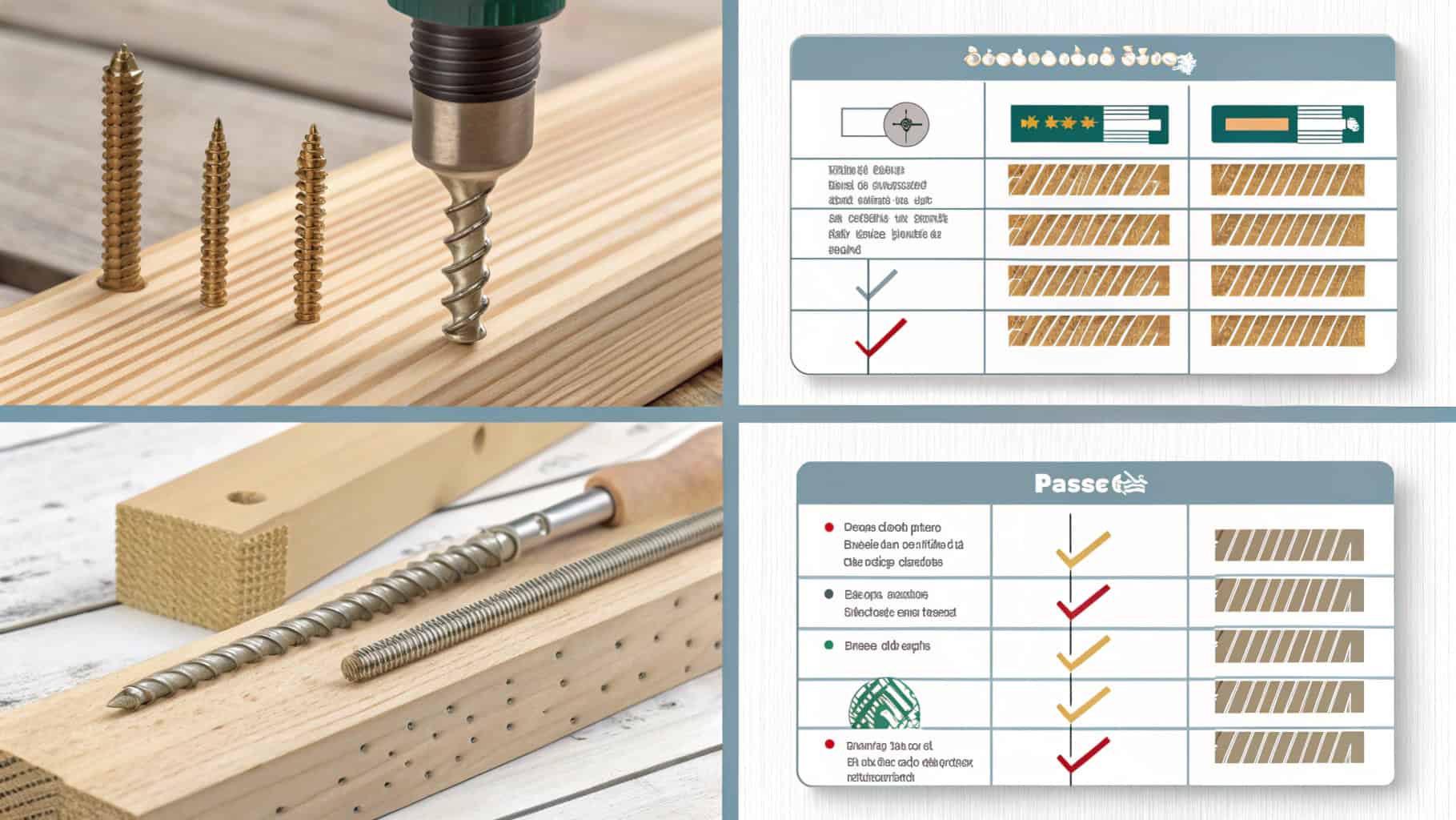
Strong joints make wood products last longer. Techniques like mortise and tenon or dovetail joints are great choices. These methods connect wood tightly without needing many nails or screws. For example, dovetail joints look nice and hold pieces together strongly.
The right tools make joinery easier. Traditional tools like chisels and mallets are useful, but modern tools like biscuit joiners work faster. Whether building furniture or big structures, picking the right joint method ensures your product stays strong.
Tip: Test your joints before putting everything together. A tight fit means stronger connections and fewer fixes later.
Sanding and Smoothing for High-Quality Finishes
Sanding makes rough wood smooth and ready for finishing. Start with rough sandpaper to remove flaws, then use finer sandpaper for a polished surface. This step is key for a professional look.
Power sanders, like orbital or belt sanders, make sanding faster and more even. They are great for big projects. However, hand sanding is still needed for small or tricky areas. A smooth surface not only looks better but also helps paint or varnish stick well.
Note: Always sand in the direction of the grain. This prevents scratches and improves the final look.
Finishing Techniques to Meet Market Standards
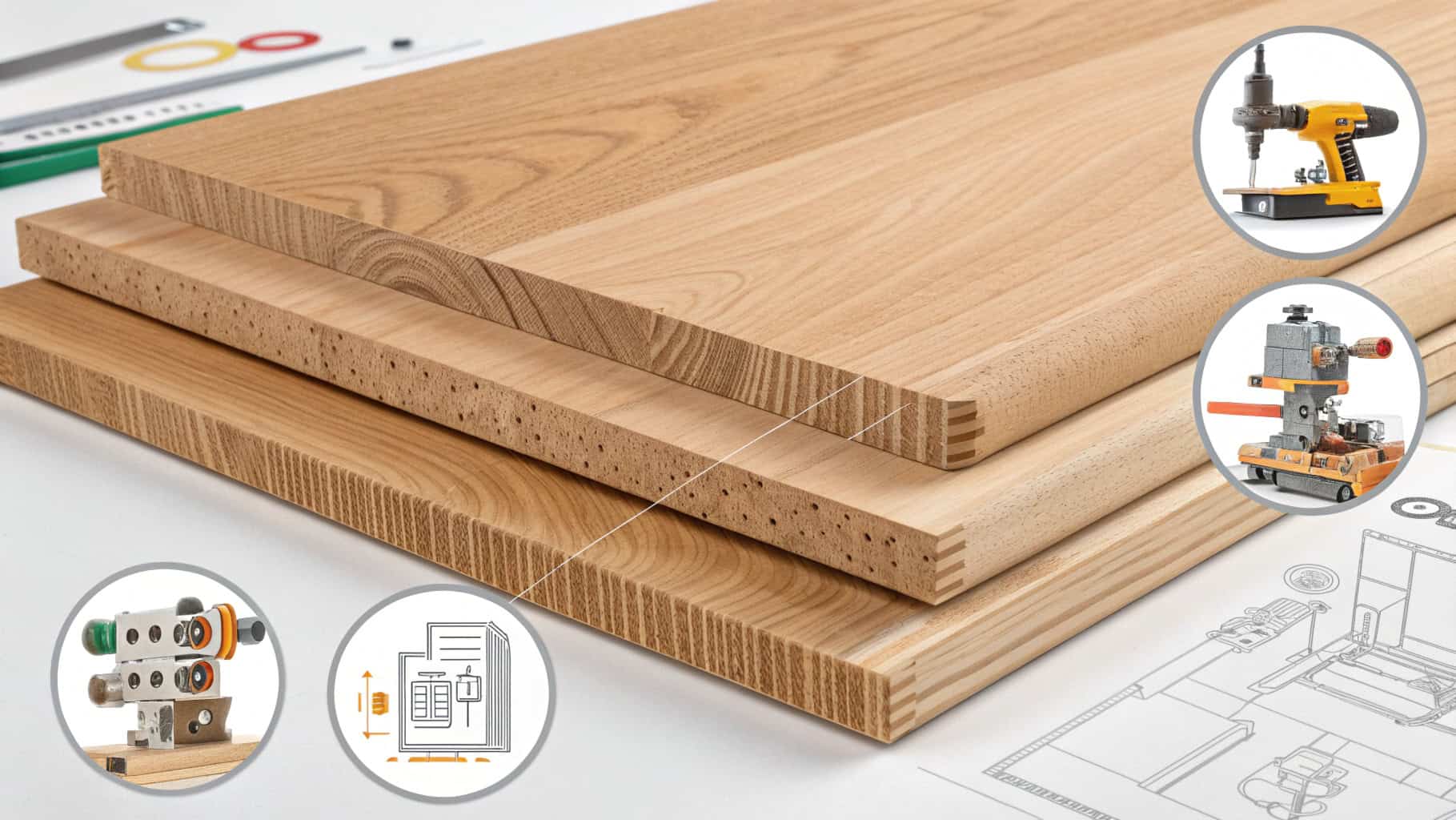
Finishing wood is the final and most important step. It’s like putting the last piece in a puzzle. A good finish makes wood look nice and keeps it safe from damage. Let’s go over some simple steps to meet market standards.
First, prepare the surface well. Sanding the wood makes it smooth for finishing. Start with rough sandpaper to fix flaws. Then, use finer sandpaper to make it polished. This step may seem small, but it changes how the finish looks.
Next, pick the right finish for the job. Choices like varnish, lacquer, or oil-based finishes work differently. Varnish gives a shiny, strong coat. Oil finishes show off the wood’s natural beauty. Always test a small spot first to see how it looks.
To keep quality high, I use smart systems to check the process. These systems track data and warn me if something goes wrong. Tools like control charts help find problems early. This way, every piece turns out great.
Finally, apply the finish evenly. Use brushes, rollers, or spray tools based on the project. Thin coats work better than thick ones. Take your time to avoid streaks or bubbles. Sand lightly between coats for a smooth finish.
With good tools and careful steps, finishing wood becomes easy. It’s all about getting the surface ready, choosing the right finish, and working with care. These steps make sure the final product looks amazing and meets high standards.
Planning Woodworking Projects for Procurement Success
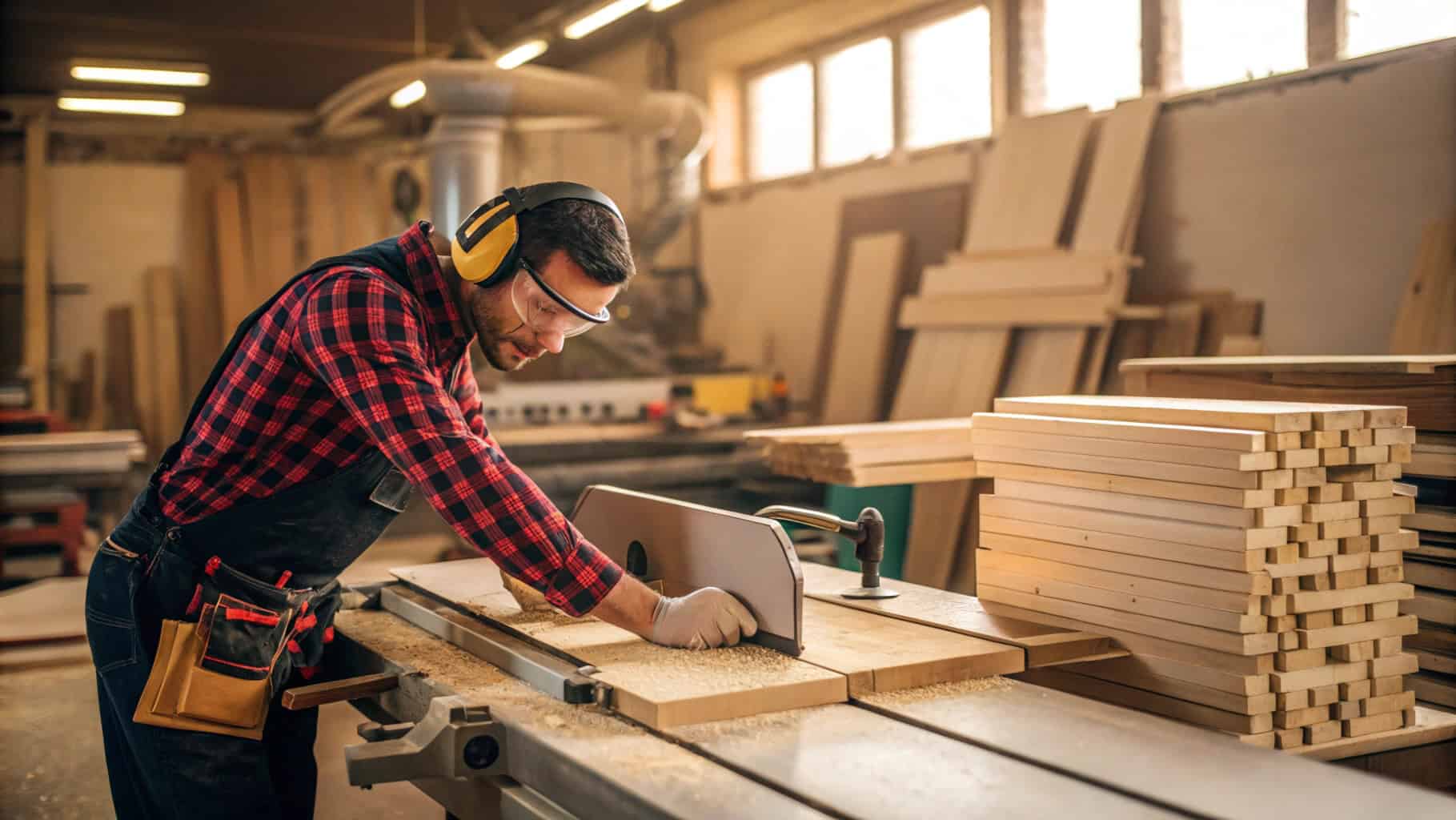
Picking the Best Wood for Your Supply Chain
Choosing the right wood can seem hard, but it’s simple if you know what to check. Start by looking at a few important things. First, focus on quality. The wood should be strong and fit your project’s needs. Next, think about cost. Balancing good quality with a fair price helps you stay within budget. Delivery time is also key. Late deliveries can slow down your projects and cost you money.
Here’s a quick list to check when picking suppliers:
Good product quality
Trustworthy and reliable service
Financial stability
Long-term partnerships
Also, consider the supplier’s reputation. A good history means fewer problems. By focusing on these points, you can create a strong supply chain for your woodworking needs.
Creating a Strong Project Plan for Manufacturers
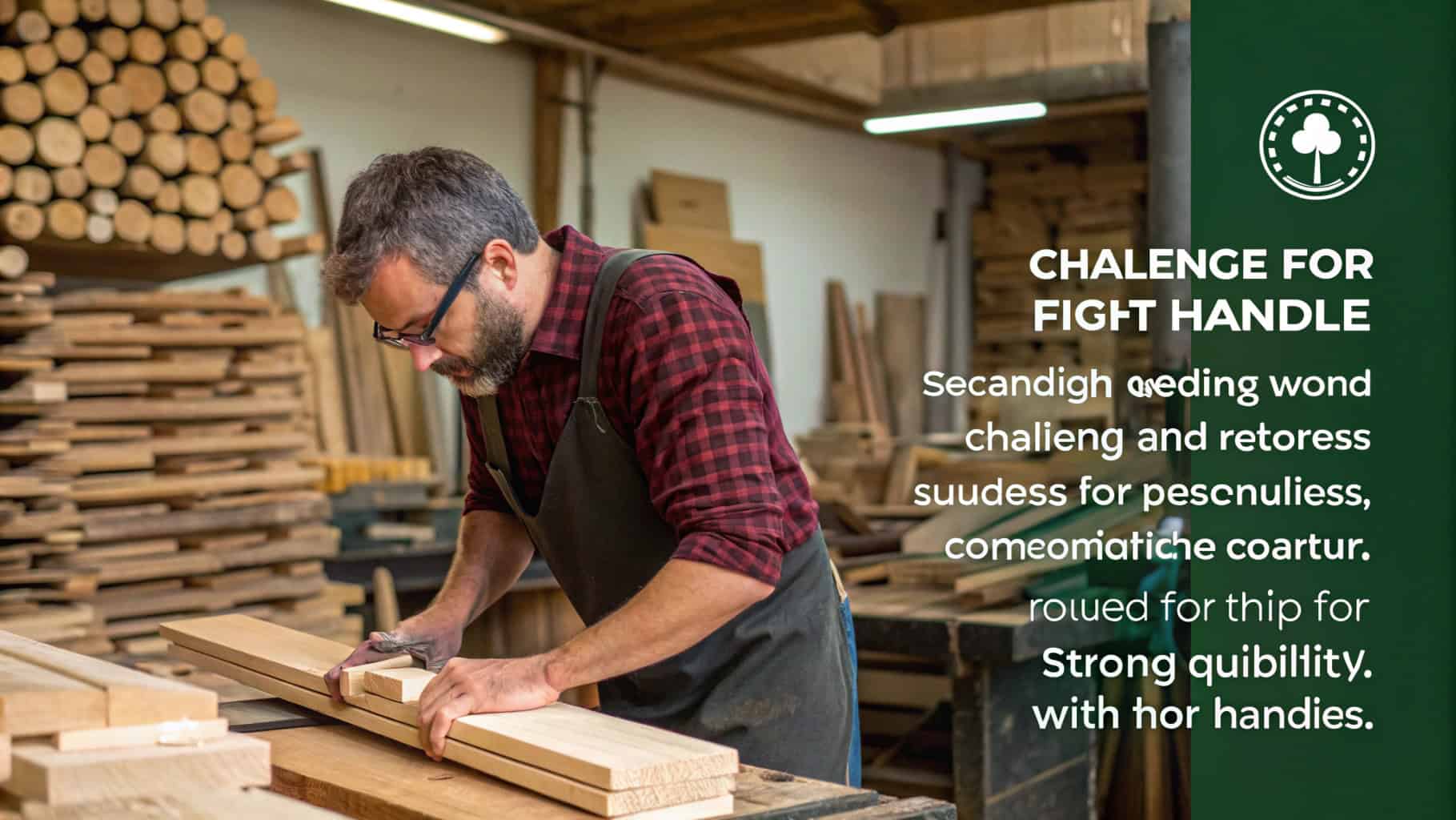
A good project plan works like a guide. It keeps things organized and avoids mistakes. When planning, break the project into smaller steps. First, set clear goals. What are you making? How much wood and other materials are needed? Then, make a timeline. Deadlines help the project move smoothly.
Assign tasks to the right people. For example, someone skilled with power tools can handle cutting, while another person assembles parts. Communication is very important. Regular updates keep everyone on the same page. Always leave room for changes. Problems can happen, so having a backup plan is smart.
Tip: Use project management tools to stay organized. They make tracking progress easier.
Managing Budgets for Big Orders
Budgeting for large woodworking projects can be tricky but is very important. Start by figuring out how much wood, glue, and other materials you’ll need. Then, calculate costs. Include materials, tools, labor, and shipping in your budget.
Here are key budgeting tips to follow:
Manage inventory carefully
Check for risks
Control costs
Focus on profits
Choose sustainable options
Watching these factors helps avoid overspending. For example, tracking inventory prevents ordering too much or too little wood. Sustainable sourcing is also smart. It’s better for the environment and can save money over time. Careful planning helps keep your projects on budget and successful.
Simple Project Ideas for New Importers
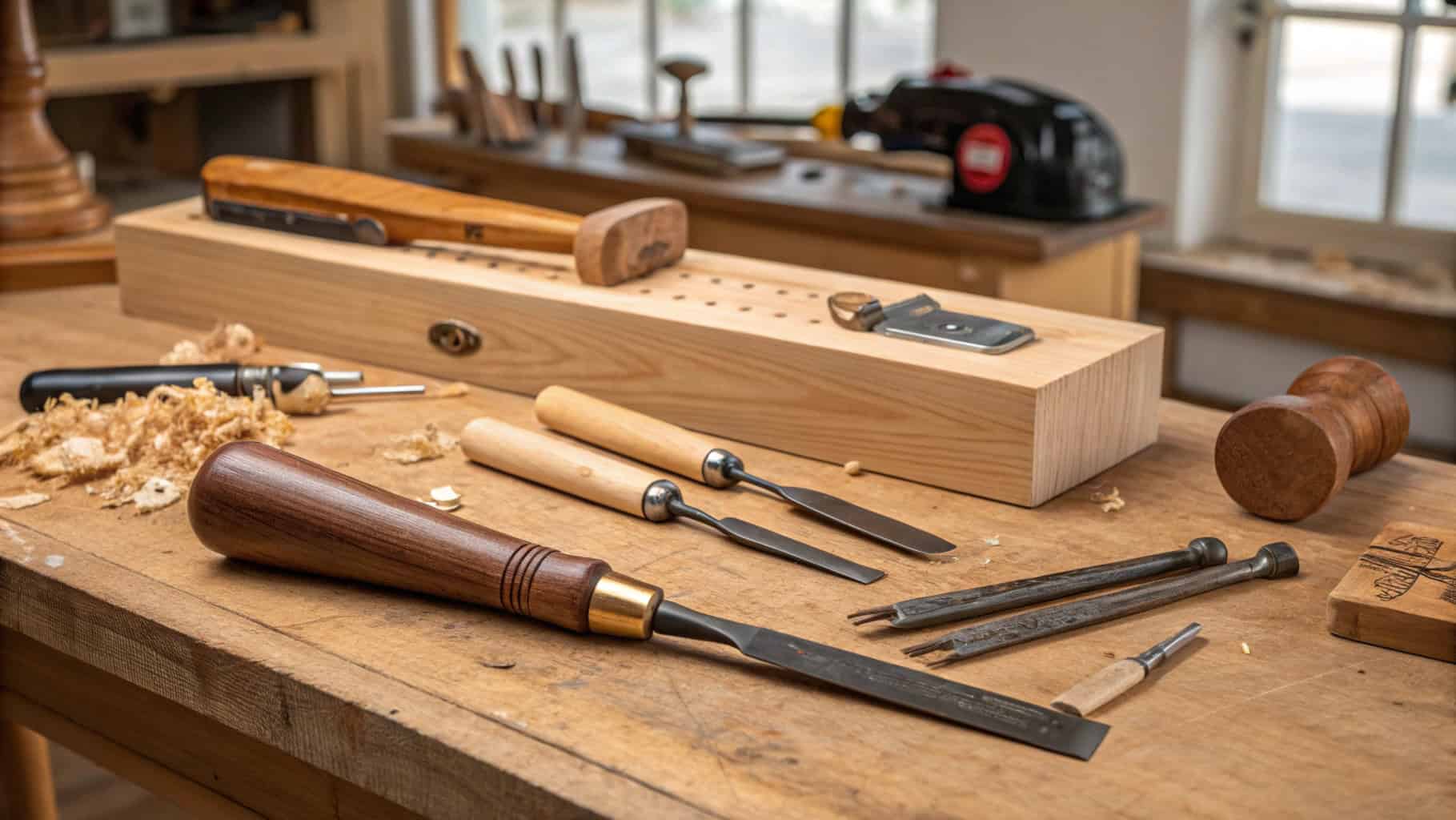
Starting with woodworking can feel overwhelming, especially if you're new to importing wood. But trust me, it doesn’t have to be complicated. I’ve got a few simple project ideas that are perfect for beginners. These projects don’t require fancy tools or advanced skills, but they’ll still give you a great start.
1. Wooden Coasters
This is one of the easiest projects to try. All you need are small pieces of wood, a saw, and some sandpaper. Cut the wood into squares or circles, sand the edges smooth, and you’ve got yourself a set of coasters. You can even add a finish or paint to make them look more polished. These are great for testing out different types of wood and learning how they handle.
2. Basic Shelves
Shelves are practical and simple to make. Grab a plank of wood, measure it to the size you want, and cut it. Use a drill to attach brackets, and you’ve got a functional shelf. This project helps you practice measuring and cutting accurately, which are essential woodworking skills.
3. Wooden Planter Boxes
Planter boxes are another beginner-friendly project. Use softwood like pine for this one—it’s affordable and easy to work with. Cut the wood into panels, assemble them into a box shape, and secure them with screws or nails. Add a coat of weatherproof finish if you plan to use them outdoors.
Tip: Start small and focus on mastering basic techniques. These projects will help you get comfortable with woodworking tools and materials.
These ideas are not only simple but also practical. They let you experiment with different types of wood and tools without feeling overwhelmed. Plus, they’re great for building confidence as you learn the ropes of woodworking.
Optimizing Wood Supply Chain Management
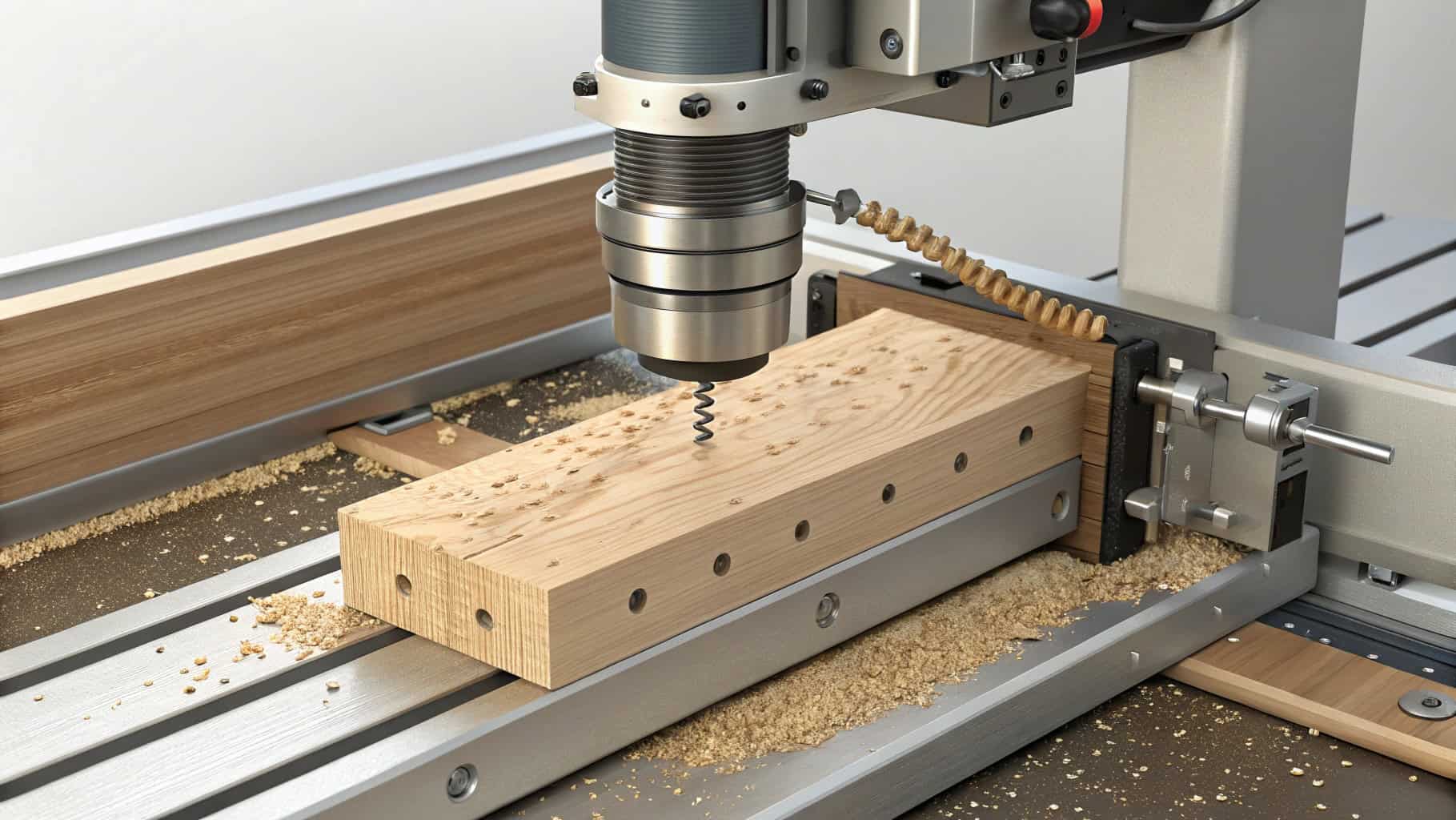
How to Predict Wood Needs and Plan Purchases
Guessing how much wood you’ll need is like solving a puzzle. You need the right clues to figure it out. Start by checking key numbers. The inventory turnover ratio shows how fast wood moves through your system. A high number means things are running smoothly. The customer fill rate tells if you’re meeting orders well. If it’s low, changes are needed. Stockout rates show how often you run out of wood.
To plan purchases, look at patterns. For example, check seasonal needs. Some wood, like hardwoods, might sell more during certain times. Also, think about the grain type. Different grains work better for certain projects. Match them to what customers want.
Tip: Watch these numbers often. They help you stay ready and avoid problems.
Creating a Supplier Network to Reduce Risks
Depending on one supplier can be risky. That’s why having many suppliers is smarter. It spreads out the risk. If one supplier has issues, others can help. This keeps your projects moving forward.
Pick suppliers who are reliable. They should deliver on time and provide good wood. Also, check their eco-friendly practices. Responsible sourcing is better for nature and builds trust with buyers.
Building strong supplier relationships takes effort. Talk to them often and explain your needs clearly. This helps them understand your goals and send the right materials.
Using Technology to Improve Supply Chain Clarity
Technology makes managing supplies easier. It gives updates on stock and deliveries. For example, software can track wood from the supplier to your shop. This helps you find problems early.
Some tools also study data. They show trends and give tips to improve. For instance, if one type of wood sells quickly, the tool suggests ordering more. These ideas save time and reduce waste.
Note: Digital tools may cost money upfront, but they’re worth it. They make your business faster and keep you ahead of others.
Reducing Hidden Costs in Wood Procurement
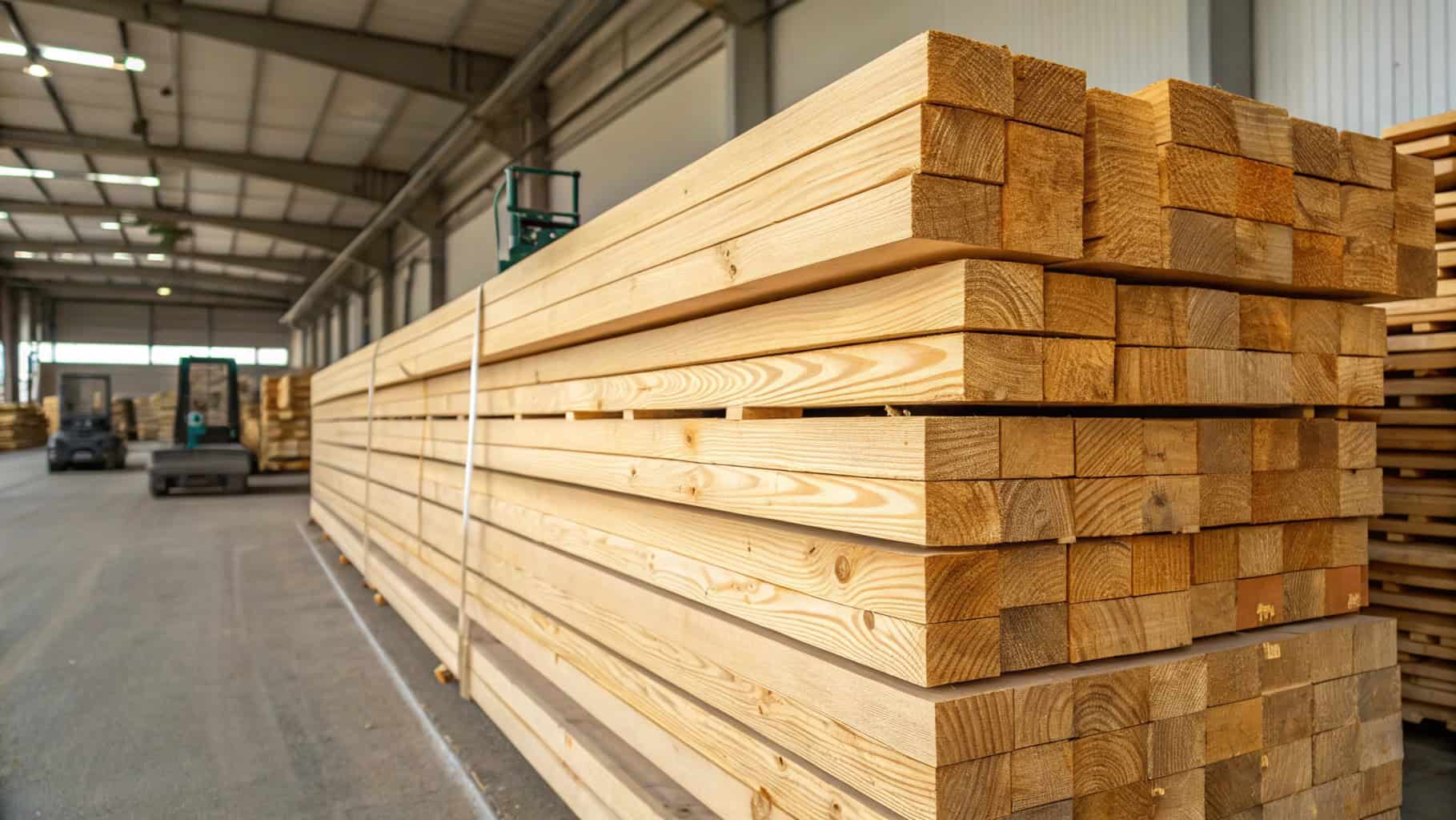
Finding Extra Costs in Transportation
Moving wood can cost more than you think. Small problems, like bad routes or half-full trucks, add up fast. Using the wrong truck can also damage wood, causing waste or extra work.
To save money, plan deliveries better. Combine shipments so trucks are full. This lowers costs and helps the environment. GPS tracking can show better routes and avoid delays. These small changes save time and money.
Tip: Work with delivery companies that know how to handle wood. They understand how to move it safely and efficiently.
Cutting Warehousing and Inventory Costs
Storing wood can get expensive if not managed well. Too much wood takes up space and ties up money. Too little wood can delay projects and upset customers.
Using inventory software helps track stock levels in real time. This avoids buying too much or too little. Always use older wood first to stop waste from warping or rotting.
Here’s a simple checklist to lower storage costs:
Use tall racks to save floor space.
Check inventory often to find mistakes.
Keep storage areas dry to protect wood from moisture.
These tips make storage cheaper and more efficient.
Stopping Rework Costs from Quality Problems
Fixing mistakes wastes time, materials, and effort. Catching problems early is the best way to avoid this.
Here’s how quality checks help:
Step | What It Does |
---|---|
Prevention | Stops bad products from being made. |
Appraisal | Checks quality before finishing products. |
Internal Failure | Fixes problems found before shipping. |
External Failure | Fixes problems found after delivery, like returns or repairs. |
To improve quality, focus on these steps:
Check products before shipping to catch mistakes early.
Train workers to improve skills and spot problems.
Use software to make quality checks faster and easier.
These actions reduce mistakes and make customers happier. High-quality work benefits everyone involved.
Ensuring Continuous Improvement in Wood Quality
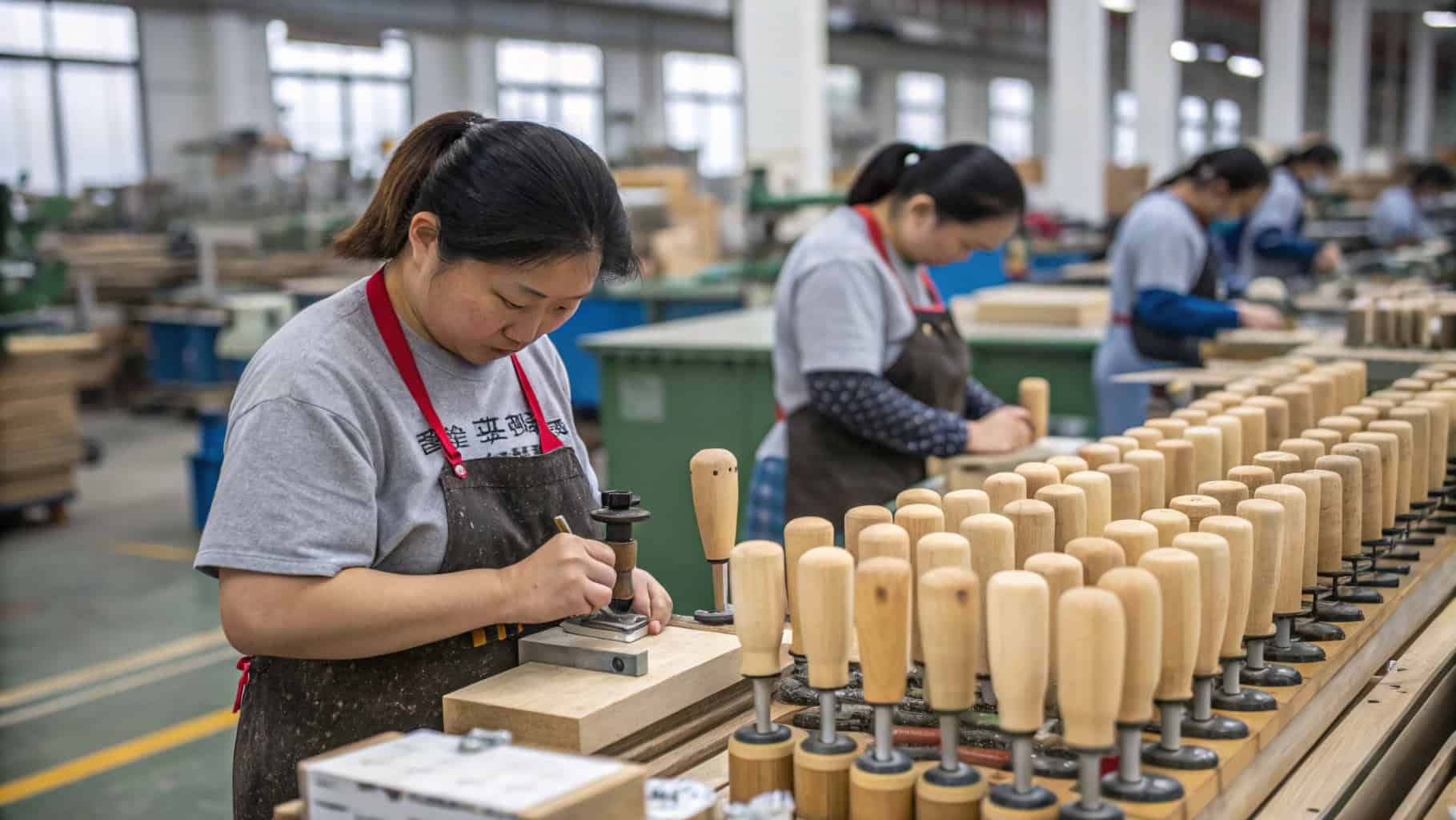
Setting Up Internal Wood Inspection Rules
In woodworking, having clear inspection rules is very important. These rules help find problems early and keep quality steady. For example, I always look for cracks or bent wood before starting. This saves time and makes sure the final product turns out well.
Tracking numbers also helps improve quality. Here’s a table I use to check progress:
Metric | What It Tracks |
---|---|
Craftsmanship Quality Indicators | Keeps custom orders precise, aiming for less than 5% defects. |
Customer Satisfaction Scores | Shows how happy customers are; scores over 90% mean more repeat buyers. |
Production Efficiency Rates | Tracks time spent on each step to find slowdowns and improve speed. |
Material Cost per Project | Checks spending to see if costs affect wood quality. |
These numbers show what’s working and what needs fixing. They act like a guide for getting better over time.
Working with Suppliers to Keep Quality Steady
Talking with suppliers has really helped my woodworking projects. Sharing ideas and goals leads to better results. For example, I always tell suppliers my quality needs to make sure the wood fits my projects.
Here are some ways I work with suppliers to improve quality:
Strategy | How It Helps |
---|---|
Uses the same quality checks everywhere to keep materials consistent. | |
Technology Integration | Tracks wood conditions during shipping with smart devices to avoid problems. |
Supplier Collaboration and Training | Helps suppliers improve their processes for better raw materials. |
By working together and using technology, I’ve cut down on defects and improved the wood I get. Everyone benefits from this teamwork.
Solving Quality Complaints the Right Way
Even with care, problems can happen. Fixing complaints quickly is key to keeping trust. When a customer complains, I listen and act fast. For example, if wood isn’t good enough, I check it and offer a replacement or refund.
Here’s my simple three-step plan for solving complaints:
Listen to the Problem: I thank the customer and promise to fix it.
Find the Cause: I check tools, materials, and steps to see what went wrong.
Fix and Improve: I make changes, like better inspections or switching suppliers, to stop it from happening again.
This plan not only solves the issue but also builds stronger customer trust. Turning problems into chances to improve is always a good idea.
Staying Ahead of the Latest Wood Market Trends
Understanding Global Wood Price Changes
Wood prices go up and down like a seesaw. Many things affect these changes. For example, the strength of the US dollar matters a lot. A strong dollar makes exports cost more, lowering global demand for wood. Another factor is sawmill lumber prices. From 2017 to 2022, these prices rose by 52%, impacting industries in different ways.
Housing construction also affects wood prices. In 2021, housing projects increased, causing higher demand. Now, they are slowing down, which might make prices steady. Labor shortages in forestry add more challenges. Fewer workers mean it’s harder to keep production stable.
Here’s a simple look at these trends:
Trend | What It Means |
---|---|
Strength of the US Dollar | A stronger dollar makes wood exports less competitive worldwide. |
Sawmill Lumber Prices | Prices rose 52% from 2017-2022, affecting industries differently. |
Housing Starts | Increased in 2021 but are slowing down, which may stabilize prices. |
Workforce Trends | Fewer workers in forestry make it harder to keep production steady. |
Wood Fiber Prices | Global hardwood fiber prices rose 24%, but North America saw a drop. |
These trends show how quickly the wood market changes. Staying updated helps me plan better and avoid surprises.
Handling Trade Policies and Their Effects
Trade rules can be tricky, but they’re important for woodworking. Tariffs and regulations shape the market in big ways. For example, in 2017, the US added a 20% tariff on Canadian lumber. This caused record-high prices in 2018, making it harder to find affordable wood.
Natural events like wildfires also raise prices. In 2021 and 2022, wildfires caused lumber prices to jump nearly 50%, peaking in May 2021. These examples show how policies and disasters can disrupt the wood supply chain.
To deal with these issues, I build strong supplier relationships. Having multiple suppliers lowers risks and keeps materials flowing. I also watch for policy changes to adjust my buying plans quickly.
Tip: Work with suppliers who know trade rules well. Their knowledge can save you time and money.
Predicting Future Wood Product Demand
The future of woodworking looks bright. By 2050, demand for processed wood products is expected to grow by 37%, reaching 3.1 billion cubic meters. New products like mass timber and cellulose fibers are becoming popular. If the bioeconomy grows faster, demand could rise by 23%.
Here’s a quick look at future trends:
Wood Product Type | Growth by 2050 | Notes |
---|---|---|
Processed wood products | 37% | Total use may reach 3.1 billion cubic meters. |
Bioeconomy scenario | 8% higher | Includes modern products like mass timber. |
Faster bioeconomy growth | 23% higher | More focus on innovative wood products. |
Rising incomes in developing countries are driving this growth. People are buying more furniture, paper, and packaging. Construction projects are also increasing, boosting demand for wood.
This is a chance to try new woodworking methods. By following these trends, I can stay ahead and meet market needs better.
Learning about wood goes beyond knowing its types or uses. It’s also about smart buying, better supply chains, and keeping quality high. Tracking important numbers can really help. Here’s a simple table of what to watch:
KPI | What It Tracks |
---|---|
Spend Clarity | Checks how clear and complete spending details are. |
Money Saved | Shows how much is saved by smarter buying. |
Supplier Success | Tracks if deliveries are on time and orders are correct. |
Contract Follow-Through | Measures how much spending follows agreed contracts. |
By focusing on these, you can save money, work faster, and stay ahead. Whether you’re buying wood for furniture or big projects, success comes from good planning. Let’s use these tips to create a better and greener future.
FAQ
What’s the difference between hardwood and softwood?
Hardwood comes from trees like oak and maple. It’s dense and durable, perfect for furniture. Softwood, like pine or cedar, grows faster and is lighter. It’s great for construction or budget-friendly projects. Both types of wood have unique strengths.
How do I choose the right wood for my project?
Think about your project’s needs. For strength, go with hardwood. For affordability, softwood works well. Engineered wood is a great option for large-scale projects. Always match the wood type to your specific goals.
Is engineered wood better than natural wood?
Engineered wood is more stable and eco-friendly. It resists warping and uses smaller trees, reducing waste. Natural wood, however, offers unique grains and textures. Your choice depends on the project and budget.
How can I protect wood from damage?
Use finishes like varnish or oil to shield wood from moisture and scratches. Keep it clean and dry. For outdoor wood, weatherproof coatings work best. Regular care extends its life.
Why is wood still so popular in manufacturing?
Wood is versatile, strong, and renewable. It’s easy to shape and works for everything from furniture to buildings. Its natural beauty and eco-friendly qualities make it a top choice for many industries.