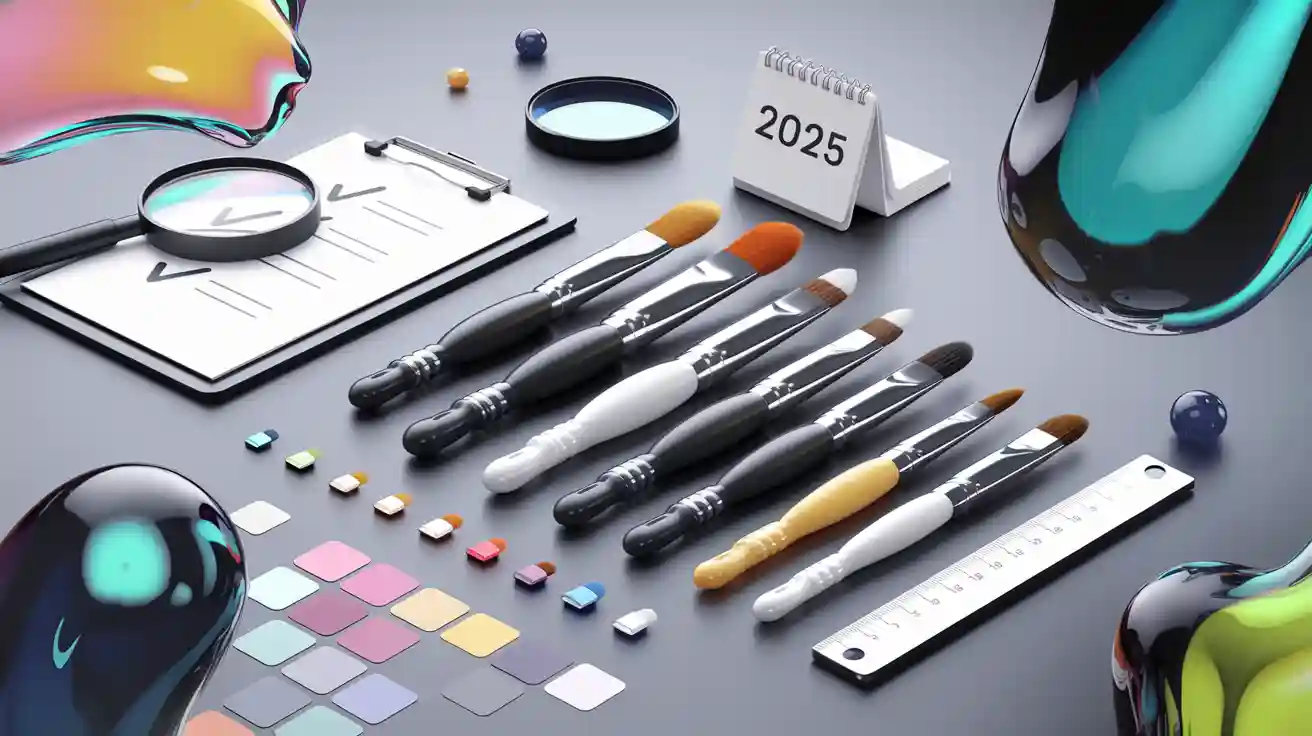
Evaluating supplier reliability is crucial for any business. Good suppliers provide consistent materials, ensuring your products maintain high quality. Reliable suppliers help you avoid delays and costly mistakes. Clear communication with suppliers facilitates smooth operations and fosters trust. By assessing how to evaluate supplier reliability, you can protect your business from potential issues and ensure everything runs efficiently. This guide offers straightforward steps to select dependable suppliers and improve communication for long-term success.
Key Takeaways
Check if suppliers are reliable. This ensures good quality and on-time delivery. It prevents expensive errors and delays.
Look at the materials used for brush handles. Strong wood or plastic makes them last longer. Always ask for proof of quality.
Review suppliers' financial health often. A supplier with steady money for three years is more dependable.
Use smart tools like AI and blockchain. These help track materials and find problems early. They make work faster and safer.
Add waste reduction goals in contracts. Keeping waste under 3% saves money and helps the environment.
Bristle-to-Handle Supply Chain Integrity
Key Checks for Brush Handle Material Suppliers
When choosing a supplier, check several important things. A good supplier gives steady quality, delivers on time, and follows rules. For wood handles, look at density and moisture levels. These affect how strong and long-lasting they are. For plastic handles, check if the material is strong and even. Trustworthy suppliers also have certifications like EN 13937:2025. These prove their materials are safe and eco-friendly. Make sure the supplier can make at least 50,000 handles each month. This keeps your supply chain running smoothly. Also, check if they’ve been financially stable for three years. This shows they are reliable and less likely to cause problems.
Problems with Bad Wood or Plastic in Brush Making
Bad materials can mess up your supply chain and hurt quality. Weak wood may crack or bend, making bad handles. Plastic that isn’t strong can break or fail during making. These problems waste materials and slow down production. A supplier with poor quality can harm your reputation. Customers might complain or return brushes that don’t work well. Checking suppliers carefully helps you avoid these problems and save money.
Example: 2025 Handle Glue Problem and Recall
In 2025, a big supplier had a recall because of bad glue. The glue didn’t hold in wet conditions, so handles fell off. This caused trouble for many brush makers. It cost money and broke trust between buyers and suppliers. The problem was poor supplier checks. The supplier didn’t test the glue well enough. This shows why checking suppliers is so important. By testing materials and processes, you can stop these issues and keep your business safe.
Brush Handle-Specific Supplier Evaluation Matrix
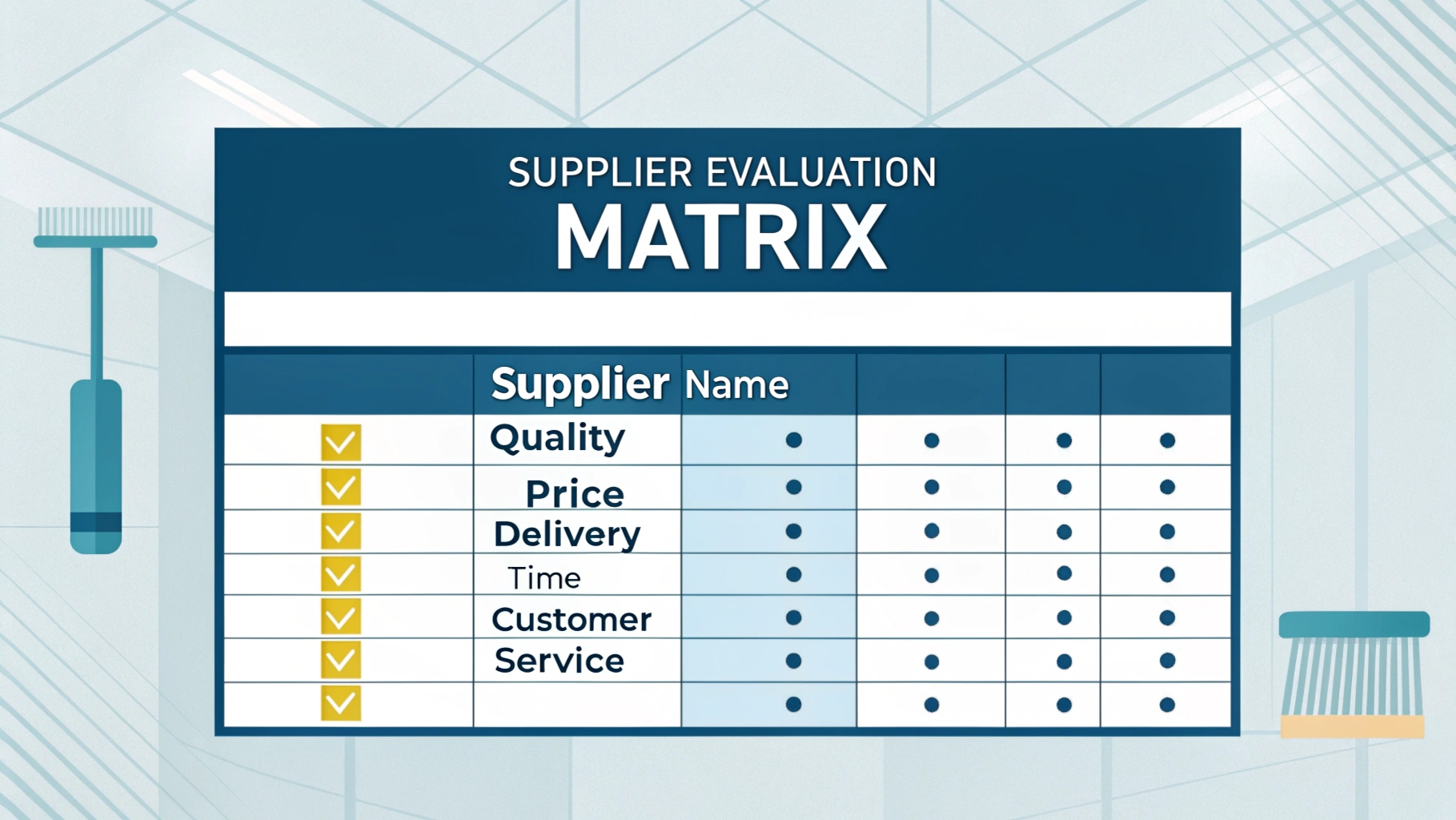
Testing Wood Strength & Plastic Quality (ASTM D6108-2025)
Checking materials is very important for brush handles. For wood, check how dense and dry it is. These things show if the handle will be strong and last long. Weak wood can break easily. For plastic, the material must stay the same every time. If it changes, it can cause problems during making. ASTM D6108-2025 gives rules to test materials properly. Ask suppliers to follow these tests to keep your supply chain steady and avoid big problems.
Handle Output: At Least 50,000 Units Each Month
How much a supplier can make affects your business. Make sure they can make 50,000 handles every month. This helps them meet your needs during busy times. Check their reports or visit their factory to see if they can do it. Good suppliers use better machines and smart systems to make more handles. By checking this, you can avoid delays and keep things running well.
Stable Finances: 3 Years of Steady Business for Long-Term Deals
A supplier’s money situation is very important. A stable supplier won’t stop your supply chain because of money problems. Look at their money records for the last three years. Here’s a simple table of what to check:
What It Shows | |
---|---|
Liquidity Ratios | Can they pay their short-term bills? |
Solvency Ratios | Are they strong enough to handle long-term debts? |
Profitability Ratios | Do they make enough profit from their sales or assets? |
Market Value Ratios | How do investors and the market see them? |
Efficiency Ratios | Are they using their resources and running their business well? |
By studying these numbers, you can find suppliers with good money habits. Working with them means fewer risks and a steady supply chain.
EN 13937:2025 Paint Brush Handle Compliance Verification
Make sure your paint brush handles follow EN 13937:2025 rules. These rules check for safety, strength, and eco-friendly materials. They ensure handles are strong, flexible, and safe to use. The materials must also be good for the environment.
Ask your supplier for proof they meet these rules. Request test results or certificates from trusted labs. These papers should explain how the handles pass the standards. If you can, visit the supplier’s factory. This lets you see if their processes match the rules.
Do regular checks to keep things on track. Plan audits to review their certificates and production steps. This helps you catch problems early before they hurt your business. Following these rules keeps your brand strong and customers happy.
VOC-Free Material Sourcing & Carbon-Neutral Manufacturing Audits
Using materials without VOCs is important for the planet. VOCs can harm people and the environment. Ask suppliers if their materials are free of VOCs. Check how they get their materials to see if they care about nature.
Carbon-neutral factories are also very important. Suppliers should lower their carbon use with green energy and smart systems. Ask for a report on their work. Look for proof they use carbon offsets or green technology. These actions show they care about the Earth.
Compare suppliers by their green certifications. Look for ISO 14001, which checks for eco-friendly practices. These certificates show the supplier works sustainably. Picking eco-friendly suppliers helps make your supply chain greener.
6-Step Handle Supplier Qualification Protocol
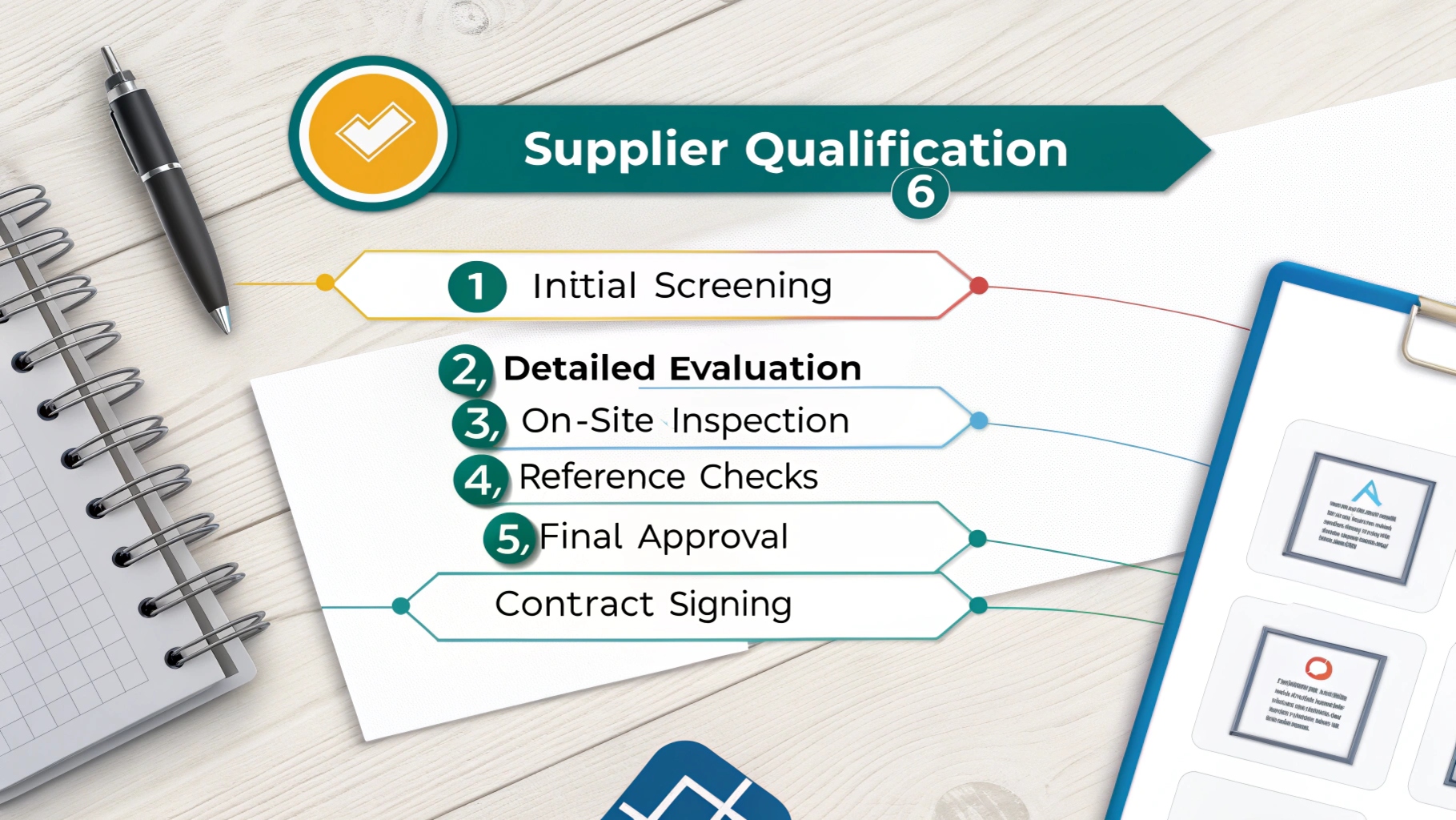
Phase 1: Picking Global Timber/Plastic Suppliers (2025 Standards)
The first step is finding trusted timber and plastic suppliers. Check their eco-friendly actions, production skills, and rule-following. Use 2025 standards to pick suppliers who meet top global practices.
Here’s a table of groups and their green efforts:
Organization | Key Practices |
---|---|
Nesma & Partners | Goes beyond green goals, building a responsible company culture. |
Trojan Construction Group (TCG) | Uses green methods, follows global building rules, and cuts waste. |
AECOM | Aims for zero carbon, boosts nature, and helps clients go green. |
Alpin | Values honesty and responsibility in eco-friendly actions. |
Damac Properties | Supports UAE Net Zero 2050 plan and fair business rules. |
Egis | Helps with green changes and follows the Paris Agreement. |
Using these standards helps you pick reliable and eco-friendly suppliers.
Phase 2: Digital Handle Supplier Scorecard v4.0 (40% Focus on Quality)
A digital scorecard makes supplier checks easier. The new Scorecard v4.0 gives 40% weight to quality. Other points include delivery, rules, and money stability.
Steps to make a good scorecard:
Give points to what matters most for your needs.
Use data from checks, feedback, and problem reports to rate suppliers.
Update the scorecard often to match new industry rules.
This method helps you find suppliers who meet your quality and business needs.
Phase 3: On-Site Handle CNC and Coating Checks
Visiting factories is key to picking good suppliers. These visits let you check CNC work and coating steps.
Requirement | Description |
---|---|
100% Inspection | Suppliers must check all parts and keep records for seven years. |
First Article Inspection | Full report with real measurements for all sizes, following AS9102 rules. |
SPC Control Charts | Suppliers must send charts showing process quality with every shipment. |
These checks ensure suppliers meet your quality needs. They also help you avoid risks and keep your supply chain strong.
Phase 4: 500-Cycle Handle Strength Test (Wet and Dry)
Testing handle strength checks if they meet quality needs. A 500-cycle test shows how handles work in wet and dry use. This test copies real-life use to find weak spots.
Ask your supplier for sample handles to test. Soak the handles in water, then dry them fully. Repeat this process 500 times. Watch for cracks, bending, or other problems during the test. Handles that pass show they can handle tough conditions.
Work with suppliers to follow ASTM D6108-2025 rules for testing. These rules give a clear way to check materials. Ask for detailed reports about how the handles did in the test. This helps you pick suppliers who meet your strength needs.
Phase 5: Checking References: Top 3 Brush Makers’ Reviews
Checking references is key to finding good suppliers. Contact the top three brush makers who worked with your suppliers. Ask about their experience with quality, delivery, and service.
Make a list of questions to ask them. For example, ask if the supplier meets deadlines or handles problems well. Also, check if their materials meet industry rules.
Write down the feedback you get and look for trends. Good reviews from trusted companies mean the supplier is reliable. Bad reviews are warnings to be careful. Use this info to choose suppliers you can trust.
Smart Supplier Management for Handle Production
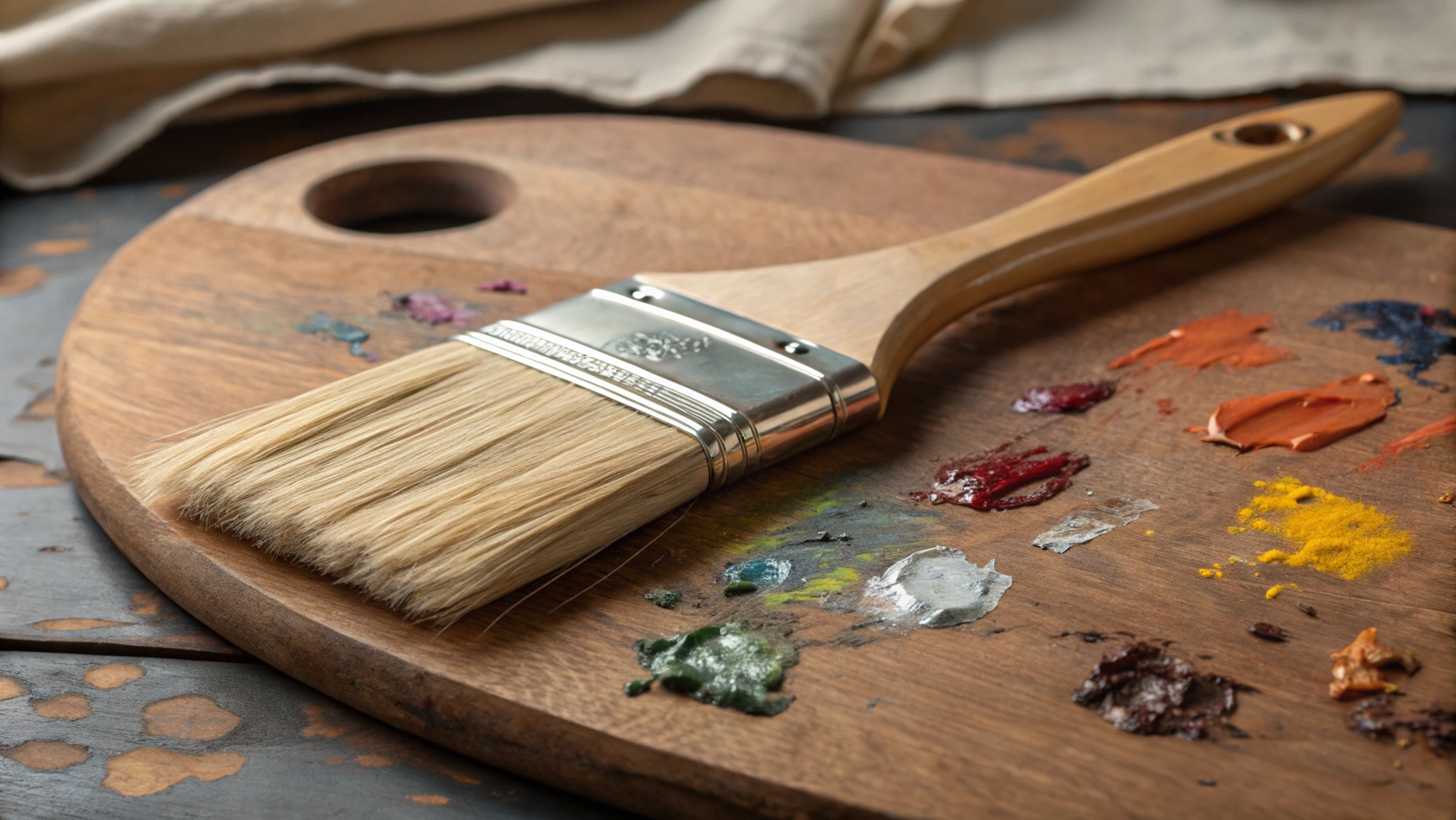
SAP Ariba Integration: Tracking Handle Materials in Real-Time
To manage your supply chain well, use helpful tools. SAP Ariba lets you track materials for brush handles as they move. It automates supplier setup and keeps compliance papers updated. Automation saves time, so your team can focus on bigger tasks.
With SAP Ariba, you can see how suppliers are doing. Check delivery times and material quality easily. If problems happen, fix them quickly to avoid delays. This keeps your supply chain steady and dependable.
AI Tools: Predicting Handle Defects Early
AI tools can change how you handle suppliers. By studying past data, AI predicts possible handle defects. This helps you fix issues before they cause trouble. For instance, if materials seem uneven, AI warns you to check them.
Using AI makes work faster and reduces waste. You can plan production better and avoid delays from bad materials. This smart method keeps your supply chain strong and ensures good quality.
Blockchain: Tracking Timber from Forest to Factory
Blockchain gives clear tracking of timber for brush handles. Every step, from cutting trees to making handles, is recorded. This proves the wood is ethical and eco-friendly.
Blockchain also checks if suppliers follow green rules. You can confirm certifications like FSC and ensure eco-safe practices. This builds trust with buyers who care about the planet.
Adding blockchain to your supply chain improves honesty and lowers risks. Suppliers become clearer, and you feel sure about your materials.
Tip: Use SAP Ariba, AI, and blockchain together for a strong system. This helps manage suppliers and keeps your supply chain reliable.
3D Collaboration Platforms: Working Together on Handle Prototypes
3D collaboration tools have changed how paint brush handles are designed. These tools let you work with suppliers and designers at the same time. Even if they are far away, you can still work together easily. Using these platforms makes creating prototypes faster and better.
Why Use 3D Collaboration Tools?
Real-Time Design Changes: Fix handle designs right away. This avoids delays caused by long discussions.
Better Visualization: See 3D models of handles from all sides. Spot problems before making them.
Teamwork Made Easy: Bring your team and suppliers together to review designs. Everyone can give feedback directly on the platform.
Tip: Try tools like Autodesk Fusion 360 or SolidWorks 3D Experience. They are simple to use and popular in manufacturing.
Steps to Use 3D Platforms for Prototypes
Upload Your Design: Add your CAD files or sketches to the platform.
Work with Others: Share the design with your team and suppliers. Ask them to suggest changes or improvements.
Test Real-Life Conditions: Use simulation tools to check if the handle is strong and comfortable.
Finish the Prototype: Once everyone agrees, save the final design for production.
Example: Quicker Prototyping with 3D Tools
Suppose you need a new ergonomic handle. You upload your design to a 3D platform and invite your supplier to check it. They suggest changing the grip angle slightly. You adjust it right away, and the updated design is ready for testing in hours. This saves a lot of time compared to older methods.
Using 3D collaboration tools helps you work faster, avoid mistakes, and make better handles. These tools keep you ahead in a tough market.
Eco-Certified Handle Sourcing Mandates
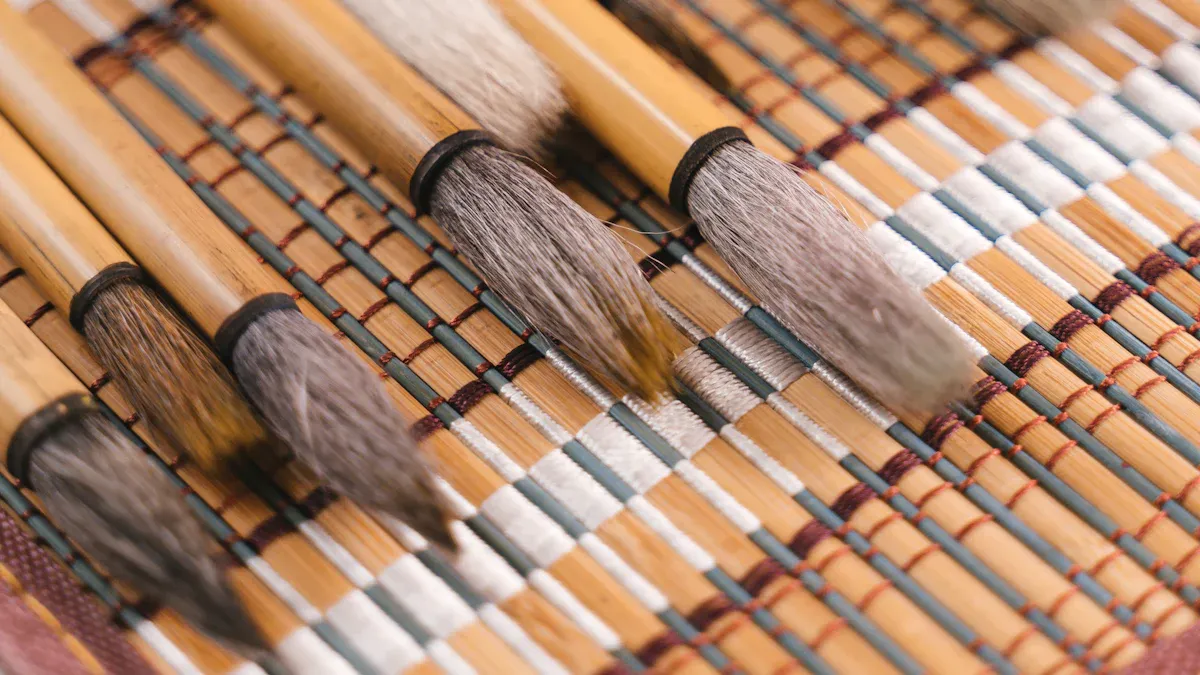
FSC-Certified Wood vs. Recycled Plastic Handle Cost-Benefit Analysis
Picking between FSC-certified wood and recycled plastic needs careful thought. FSC-certified wood comes from forests managed responsibly. It helps protect trees and stops deforestation. Recycled plastic reduces trash and supports reusing materials. Both choices make your supply chain greener.
FSC-certified wood may cost more at first. This is due to strict rules for cutting and certifying the wood. But it improves your brand image and follows rules like the European Union Deforestation Regulation (EUDR). Recycled plastic is cheaper but needs checks to ensure good quality. Both materials meet eco-friendly goals and attract green-minded buyers.
REACH SVHC Compliance: Handle Surface Coating Chemical Screening
Following REACH SVHC rules is key for safe products. These rules find and limit harmful chemicals in items. For brush handles, coatings must pass strict tests to meet these rules.
Ask suppliers for chemical test reports and certificates. Regular checks help confirm they follow the rules and avoid risks. By following REACH SVHC, you keep customers safe and protect nature. This also helps you pick responsible suppliers for your chain.
SA8000 Audit: Ethical Wood Harvesting & Handle Factory Labor Standards
Ethical sourcing means caring about workers and materials. The SA8000 standard ensures fair worker treatment and proper wood harvesting. It checks for safe workplaces, fair pay, and no child labor.
SA8000 audits help find suppliers with good practices. Look for those meeting global rules like the Ecodesign for Sustainable Products Regulation (ESPR). Ethical sourcing lowers risks and boosts your brand’s trust. Picking SA8000-certified suppliers builds a fair and green supply chain.
Tip: Use a comparison chart to weigh FSC-certified wood and recycled plastic. Include costs, rules, and eco-effects.
Handle Supplier Performance Optimization
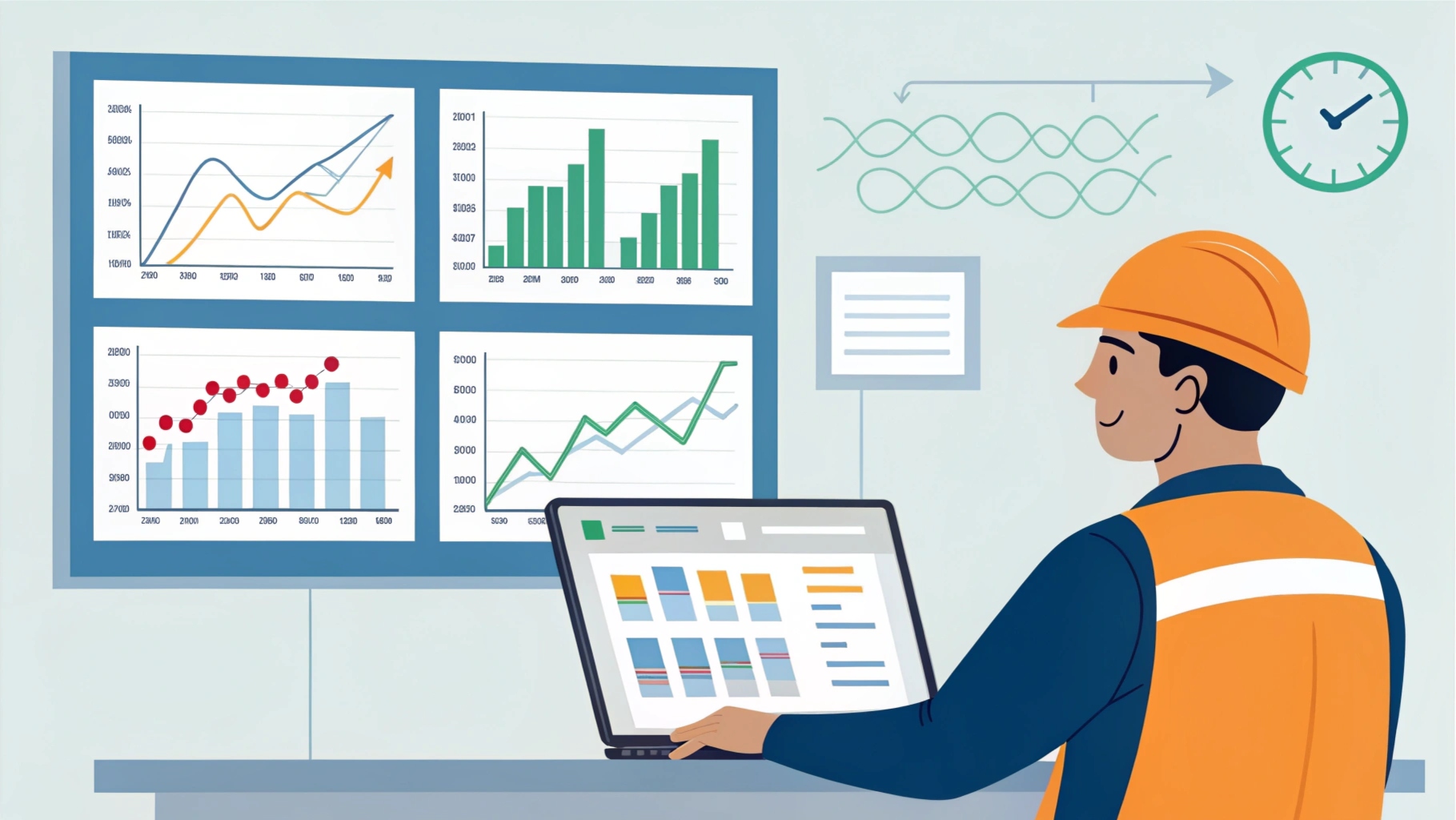
KPIs: ≤0.5% Handle Dimensional Tolerance Variance (Monthly)
Keeping handle sizes consistent is very important for quality. A size difference of ≤0.5% ensures handles fit perfectly and work well. This reduces mistakes and keeps customers happy. Work with suppliers to set clear rules for measuring handle sizes. Regular checks and reports help you track this goal.
Ask suppliers to use Statistical Process Control (SPC) charts. These charts show live data about how steady production is. By watching patterns, you can spot and fix problems early. This helps suppliers do better and keeps your supply chain strong.
Quarterly Review: On-Time Delivery Rate Optimization (Target: 98.5%)
Getting supplies on time is key to staying on schedule. Check how well suppliers deliver every three months. Aim for a 98.5% on-time delivery rate to avoid delays.
Use important numbers like service level and fill rate to check delivery. The table below explains these terms:
KPI | Description |
---|---|
Service Level | Shows how often orders are delivered on time and complete. It’s calculated as: (on-time, full orders / total orders) × 100%. |
Fill Rate | Measures how much demand is met. A higher rate, like 98.5%, means better performance. |
Talk with suppliers to fix delivery problems and improve their process. Regular updates and tracking help keep everything running smoothly.
Partnership Development: Co-Investing in Handle Automation Machinery
Working closely with suppliers can bring big benefits. Sharing costs for new machines is one way to team up. This lowers production costs, improves quality, and speeds up delivery.
Here’s why co-investing in machines is smart:
Save money by using better production methods.
Get better quality because suppliers aim to meet high standards.
Share ideas to create new and improved products.
Make the supply chain faster and keep customers happy.
Reduce risks by having backup plans and reliable suppliers.
By teaming up, you and your suppliers can build a stronger, smarter supply chain. This makes you a trusted choice in the paint tools market.
Waste Reduction: ≤3% Handle Material Scrap Rate Contract Clauses
Cutting waste helps suppliers work better and saves money. Add scrap rate rules to contracts to set clear goals. These rules ask suppliers to keep waste below ≤3% during production. This target is fair and pushes suppliers to improve their methods.
Talk to your supplier about ways to reduce waste. Ask for their current scrap rate numbers and plans to meet the ≤3% goal. If their waste is too high, request a plan to fix it. This plan could include better machines, improved techniques, or worker training.
Check how suppliers are doing often. Use monthly reports to see their scrap rates and spot patterns. Reward suppliers who meet the ≤3% goal with longer contracts or bonuses. For those who struggle, help them with audits or team problem-solving.
Tip: Add fines in contracts for suppliers who miss the scrap rate goal. This pushes them to focus on cutting waste and keeping quality high.
Waste reduction helps everyone. It lowers costs, protects the environment, and makes the supply chain stronger. By setting clear rules and working with suppliers, you can create a greener and more efficient system.
Checking how reliable a supplier is helps your business succeed. Good suppliers give steady quality, deliver on time, and follow rules. By reviewing suppliers carefully, you can avoid problems and keep things running smoothly.
To check suppliers well, do these steps: set clear goals, review them closely, use smart tools like AI and blockchain, and watch their work often. These steps help you find trustworthy suppliers and build good relationships.
Dr. Ray Carter says, "The COVID-19 crisis shows why picking suppliers with enough resources and money is so important. They need to handle demand and survive tough times."
Looking at suppliers closely brings long-term rewards:
Risk Reduction: Avoid problems with rules, contracts, and safety.
Better Compliance: Make sure they follow laws and standards.
Stronger Security: Lower risks in today’s digital world.
By focusing on supplier checks, you can make better products, avoid risks, and build strong partnerships to grow your business.
FAQ
What should you focus on when picking a supplier?
Look for quality, dependability, and rule-following. A good supplier gives steady materials, delivers on time, and meets industry rules. Check their certificates and how much they can produce to see if they fit your needs.
How can you check if a supplier is financially stable?
Ask for their money records from the last three years. Look at how well they handle short-term bills, long-term debts, and profits. Stable suppliers are less likely to cause problems for your business.
Why is testing materials important before choosing suppliers?
Testing makes sure materials are good quality. Weak wood or uneven plastic can cause bad products. Good suppliers will share test results or samples to prove their materials are reliable.
How do you check if suppliers are eco-friendly?
Ask for papers like FSC or ISO 14001 certificates. Visit their factories to check for carbon-neutral work and VOC-free materials. Green suppliers help you reach eco-friendly goals.
What tools can help you manage suppliers better?
Use tools like SAP Ariba to track materials live and blockchain to see clear records. These tools make it easier to talk with suppliers, check their work, and avoid problems in your supply chain.