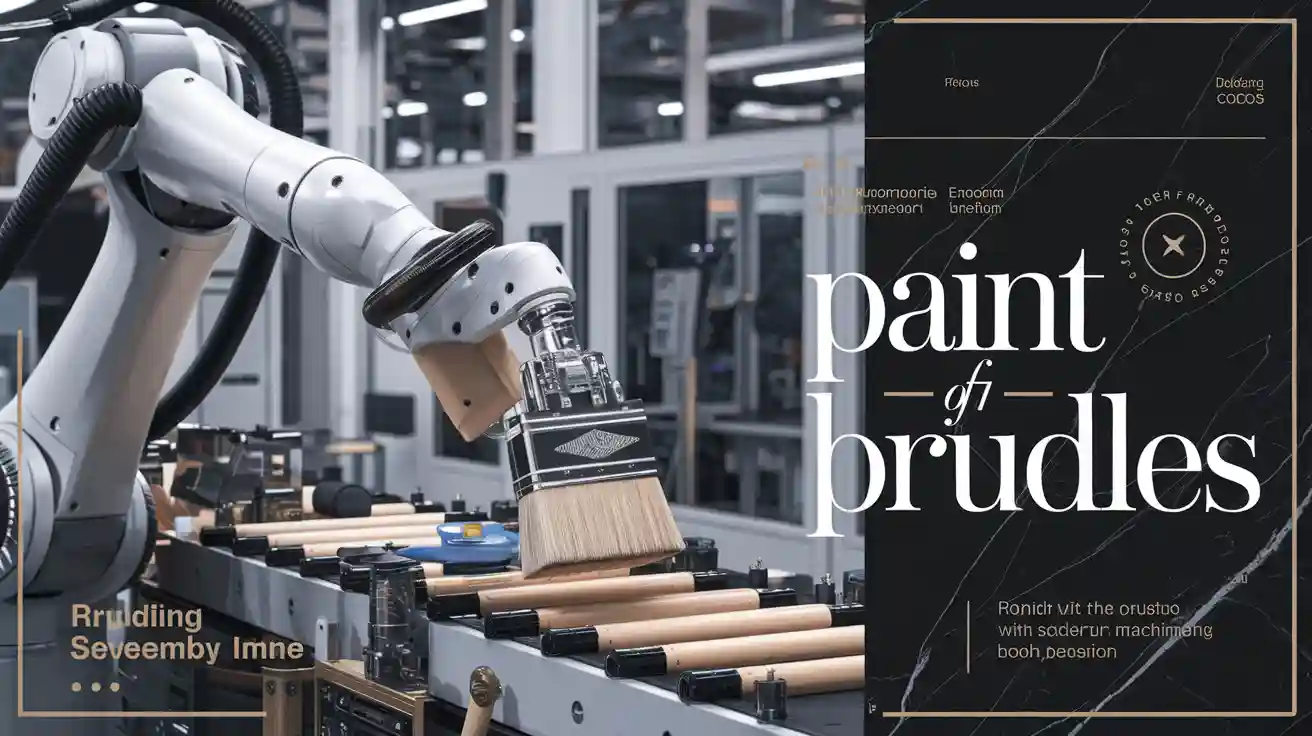
Automation has changed how things are made. Precision is key. The right tools can help or hurt efficiency. Industrial automation is growing 9.3% each year. By 2030, it may reach $307.7 billion. That’s a big number! But not all paint brush handles fit automated systems. Good handle designs make production faster and more consistent. They also make them easier to use. Since 2018, I’ve worked with Sherwin-Williams on this. We focus on making handles strong, comfortable, and precise.
Key Takeaways
Same-sized paint brush handles help machines work better and faster.
Strong materials like wood, plastic, or blends make handles last longer.
Comfortable designs, like grips with texture, make painting easier.
Careful manufacturing and checks create reliable handles for users and machines.
Green materials, like bamboo or recycled plastic, are strong and eco-friendly.
Essential Features of Automation-Ready Paint Brush Handles
Standardized Sizes for Easy Machine Use
Automation needs precision to work well. Machines rely on uniformity, so paint brush handles must have the same size and shape. If handles are different, machines can jam or misalign. Even small changes can disrupt the process. That’s why every handle must fit the machine perfectly.
Having standard sizes also makes changes simpler. For example, if you want to adjust a handle for a project, starting with a consistent size helps. It also ensures the handle works with different tools, making it more useful.
Strong Materials to Handle Machine Stress
Machines work fast and apply pressure repeatedly. Paint brush handles must survive this without breaking or wearing out. Materials like light wood and soft plastics are both strong and easy to use. They can handle stress while staying comfortable.
New technology like laser cutting makes handles stronger. These methods ensure each handle is made precisely, reducing flaws. A strong handle not only survives production but also lasts longer for users.
Comfortable Designs for Better Use
We can’t forget the people using these brushes. Comfortable designs help, especially for long painting jobs. A good handle reduces tiredness and improves grip, making strokes more accurate. Features like textured grips and balanced weight make handles easier to hold.
Comfortable designs are also practical. A handle that feels good is easier to control. This means fewer mistakes and smoother results. Whether painting a wall or doing detailed work, a comfy handle makes a big difference.
Precision Manufacturing for Reliable Performance
Making paint brush handles with precision is very important. Even tiny mistakes can mess up a whole production line. That’s why every handle must be made exactly right. Machines can’t adjust like people—they need perfect parts to work well.
One big advantage of precision manufacturing is consistency. When all handles are the same, there are fewer problems. This helps machines run smoothly and reduces waste. It also saves money and keeps production fast, which benefits everyone.
To keep things precise, manufacturers use strict quality checks. They focus on these key areas:
How efficient production is
Following safety rules
Watching systems in real time
Testing batches of handles
Cutting down on waste
These checks aren’t just numbers—they show the process works. For example, real-time monitoring finds problems early. Batch testing makes sure all handles meet standards. These steps create reliable products ready for automation.
Precision also makes customers happy. Handles that meet exact standards work better and last longer. This builds trust and gives users the quality they expect. Constant checks and improvements keep these high standards. It’s not just about making handles—it’s about making them right every time.
In the end, precision manufacturing means quality you can count on. For automation, this level of care makes all the difference.
Best Materials for Custom Paint Brush Handles in Automation
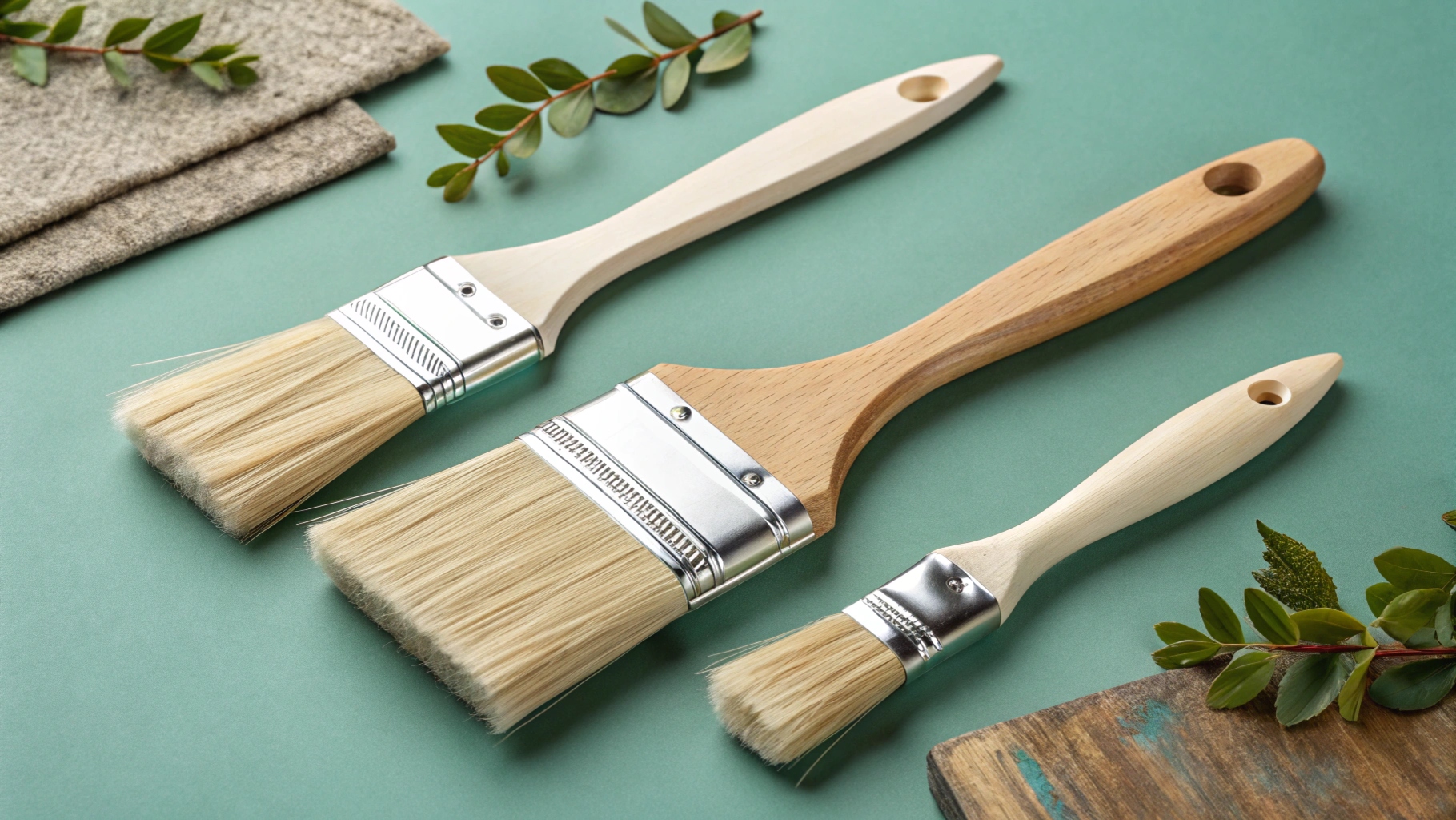
Plastic: Light and Cost-Effective
Plastic is a great material for brush handles. It’s light, cheap, and easy to shape. You can make it into many designs and sizes. Plastic handles are comfy for long painting jobs. They don’t make your hands tired. Many artists and DIYers like them for their good grip and light feel. This makes painting easier and more accurate.
New designs show how useful plastic can be. Its lightness helps you control your strokes better. This means fewer errors and smoother results. Plus, plastic is affordable. It’s perfect for making lots of handles or adjusting them for machines.
Wood: Strong, Eco-Friendly, and Comfortable
Wood is a classic choice for brush handles. It’s strong, feels nice to hold, and has a natural charm. DIY fans love wood because it’s easy to change. You can sand it, add textures, or carve designs. This makes wood great for custom handles.
Wood is also good for the planet. Many companies use wood from renewable forests. It’s tough enough for machines but still comfy to use. Whether painting walls or fine details, wood gives a mix of strength and comfort.
Metal: Tough and Long-Lasting
Metal handles are best for strength and durability. They handle heavy use and machine pressure well. Metal is heavier than plastic or wood but feels solid and reliable.
Tests prove how strong metal is. For example:
Test Type | What It Does |
---|---|
Fatigue Testing | Checks how metal holds up under repeated use. |
Finite Element Analysis (FEA) | Predicts how metal reacts to stress, vibrations, and heat. |
Electromagnetic Heating | Tests how metal handles heating and cooling cycles. |
Metal isn’t as light as plastic or as flexible as wood. But if you need something super strong, metal is the best choice.
Composite Materials: Strong, Flexible, and Reliable
Composite materials are a mix of different materials. They combine metal's strength with plastic or wood's flexibility. This makes them great for automated machines. They handle machine stress but stay light and easy to use.
Composites can be customized for specific needs. Manufacturers can adjust the mix to make handles stronger or lighter. This makes them perfect for machines needing reliable and consistent parts.
These materials are also very durable. Composite handles don’t crack like wood or dent like metal. They last longer, reducing waste and replacements. Many are designed to be ergonomic, offering a good grip and balanced weight. This helps during long painting jobs.
Composites are also eco-friendly. Some are made using recycled materials. This reduces harm to the environment while keeping quality high. It’s a smart and sustainable choice.
In summary, composites are strong, flexible, and eco-friendly. They’re ideal for making paint brush handles that work well with machines.
Key Design Factors for Automation-Compatible Paint Brush Handles
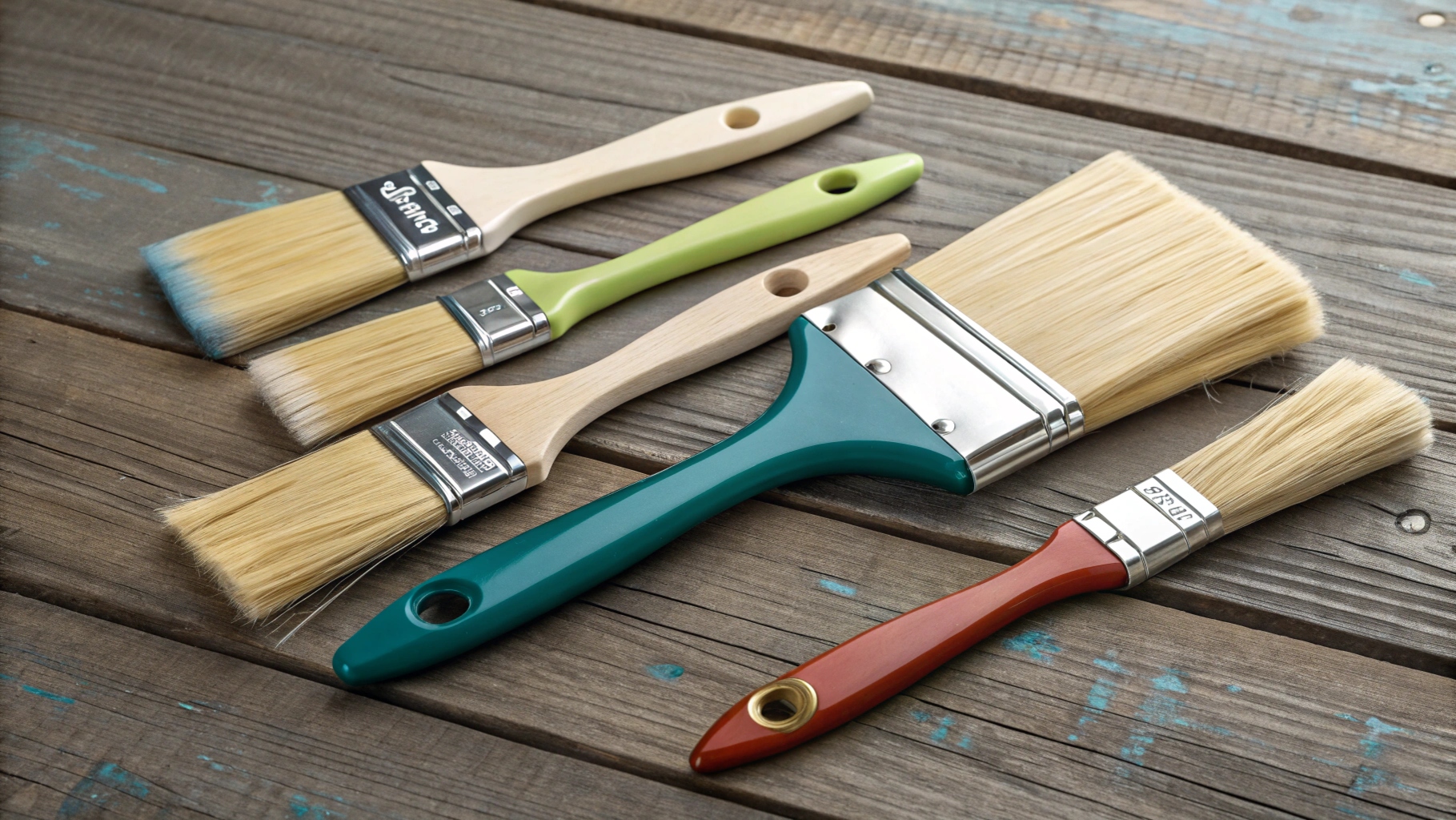
Textured Grip for Better Control
A good grip makes painting much easier. Textured grips stop slipping, even with sweaty hands. This helps people paint for hours without trouble. DIY fans love textured grips for better control and comfort.
For machines, textured grips are also important. They keep handles steady during assembly. Non-slip grips stop handles from moving or misaligning. This keeps the process smooth and efficient. Ergonomic designs with textures make brushes comfy to use. Studies show ergonomic handles improve comfort and work speed. Both machines and people benefit from these designs.
Balanced Weight for Comfort and Machine Use
The weight of a handle is very important. Heavy handles tire users, while light ones feel weak. A balanced handle is the best choice. Machines need balanced handles to avoid jams or mistakes.
Small weight changes can make a big difference. Adding weight to the base improves stability. This helps machines handle the brush better. It also gives users more control. Whether painting walls or doing detailed work, a balanced handle feels just right.
Simple Handle Shapes for Easy Use and Storage
Smooth shapes make automation faster and easier. Handles with simple designs move through machines without problems. Sharp edges or complex shapes can cause delays. That’s why smooth designs are best for automated systems.
Streamlined handles also save space and lower costs. They are easier to pack and store. Plus, they fit comfortably in your hand. These designs work well for both machines and users.
Did you know? Special sensors can check if handles meet design rules. This makes assembly more accurate and efficient.
Smooth Surface Finish for Automated System Compatibility
A smooth surface might seem small, but it’s very important. It helps paint brush handles work well with machines and users.
Smooth handles move easily on assembly lines. Rough surfaces can cause jams or misalignments. A polished finish keeps machines running smoothly. It also helps handles fit perfectly with other parts, avoiding problems during production.
Smooth finishes also make handles last longer. They reduce friction, which lowers wear and tear. This is crucial for machine parts like bearings that move fast. Less friction means fewer breakdowns and longer use.
For users, smooth handles feel better to hold. They’re comfortable and easy to grip, even for long painting jobs. When paired with non-slip grips, they give great control. Painters, both pros and DIYers, love this. It makes painting easier and less tiring.
Here’s why smooth finishes are important:
They help machines assemble handles without issues.
They lower friction, making machine parts last longer.
They improve comfort and grip for users.
In summary, smooth finishes aren’t just for looks. They improve performance, durability, and comfort. This small detail makes a big difference for machines and people.
Industry Examples of Automation-Compatible Paint Brush Handles
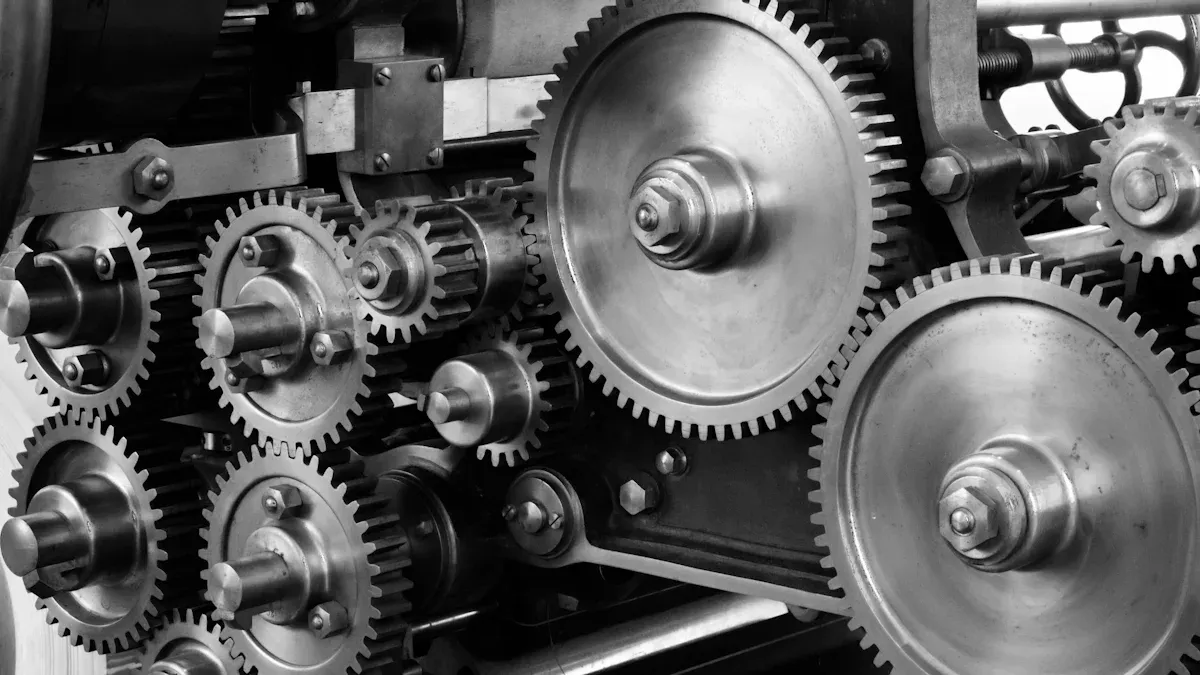
Successful Designs for Automated Assembly
Automation in making paint brush handles has come a long way. One great example is automating the process of forming brush knots. This task used to be done by hand but is now automated. Using special sensors, machines can place parts with high accuracy. This ensures every handle meets quality standards while keeping up with production speed. It shows how smart design and technology solve old problems.
Why do these designs work so well? It’s all in the details. Engineers use methods like needs analysis to make sure systems run smoothly. These approaches help figure out what’s needed and how to meet those needs. The result is faster production without losing quality.
Real-Life Examples of Automation Success
There are many interesting examples of automation in this field. Here are some key points:
One case focused on shaping brush knots, which connects to handle making. It used careful planning and problem-solving to build a reliable system.
The system worked quickly while keeping high-quality results.
Early tests showed these automated systems can handle modern production needs without issues.
These examples prove that small changes in technology can make a big difference. By improving old methods, manufacturers create faster and more reliable systems.
Lessons from Experts Like Sherwin-Williams
Since 2018, I’ve learned a lot about automation from Sherwin-Williams. They lead the way in updating their processes for today’s manufacturing needs. One key lesson is that automation must stay flexible. It’s not a one-size-fits-all solution and needs regular updates.
Sherwin-Williams also balances new ideas with practical use. They design handles that work well with machines but are still easy to use. This focus on both efficiency and comfort makes them stand out. It’s a reminder that even with advanced technology, the user experience still matters.
Advantages of Custom Paint Brush Handles Designed for Automation
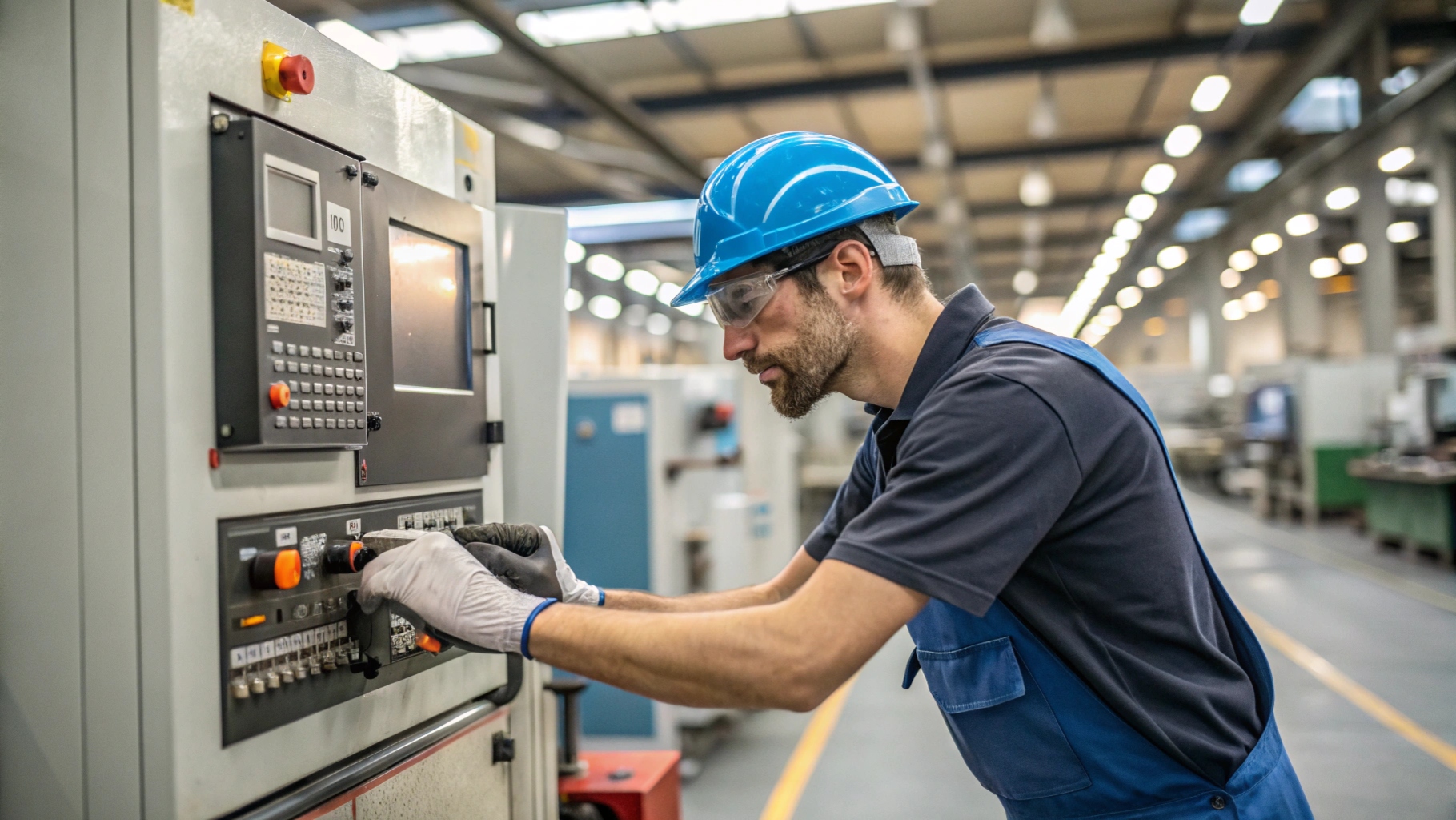
Faster and Smoother Manufacturing
Custom handles make production quicker and easier. During my work with automation, I saw how much time machines saved when handles were made to fit them. Machines don’t pause to fix mistakes—they keep working.
Handles with the same size and shape are very important. They fit perfectly into machines, avoiding jams or slowdowns. This keeps production lines moving fast and without problems.
Even small changes can improve things a lot. For example, adding a textured grip or changing the weight can help machines handle brushes better. These changes also make the brushes more comfortable for people to use.
Saving Money with Standardized Designs
Using the same design for all handles saves money. When handles are identical, they’re easier to make in big batches. This reduces waste and cuts costs.
I’ve seen how custom handles built for automation lower expenses. Companies don’t need to spend extra fixing mistakes or replacing broken parts. Plus, having a standard design makes switching projects simpler. If you need a new handle style, starting with a consistent base saves time and money.
Here’s a tip: Strong materials like wood or composites last longer. Using them means fewer replacements, saving even more money over time.
Better Comfort with Ergonomic Features
Comfort is important. A paint brush handle should feel good to hold. If it’s hard to grip, painting becomes tiring. That’s why ergonomic designs are so helpful.
Custom handles for automation often include features like textured grips and balanced weight. These details make brushes easier to hold and control. Whether painting a large wall or doing detailed work, a comfy handle makes the job better.
Painters love these designs. They say ergonomic handles reduce hand strain and improve precision. It’s not just about making handles work with machines—it’s about making them better for people, too.
Pro Tip: Think about both the machine and the user when designing handles. A handle that works well in automation and feels great to use is the best choice.
Supporting the Planet with Green Materials
Caring for the Earth is important. Using eco-friendly materials for paint brush handles helps the environment. Even small changes, like choosing sustainable materials, can reduce waste and improve products.
Many companies now use bamboo or recycled plastics. Bamboo grows fast and needs little water, making it a renewable choice. Recycled plastics help lower plastic waste. These materials are better for the planet and meet the need for greener products.
Here’s why green materials are important:
They cut down on plastic waste in landfills.
They support eco-friendly manufacturing practices.
They attract DIY fans who care about the environment.
Eco-friendly handles are strong and comfortable, just like regular ones. They work well for DIY projects, whether painting walls or crafting. These handles are durable and easy to use.
Small changes can make a big difference. For instance, adding a textured grip to a bamboo handle improves comfort without harming sustainability. These smart updates show that eco-friendly doesn’t mean less quality.
Switching to green materials helps the planet and boosts business. People love products that are useful and eco-friendly. By using sustainable handles, companies can meet customer needs and protect the Earth for the future.
Automation works best with accuracy, and good paint brush handles help a lot. Strong and comfy designs improve how machines work and make painting easier. Painting robots need exact tools to give steady results and waste less. Whether you make products or love DIY, using well-made handles makes tasks easier and results better. To stay ahead in today’s tech-focused world, start by picking the right tools.
FAQ
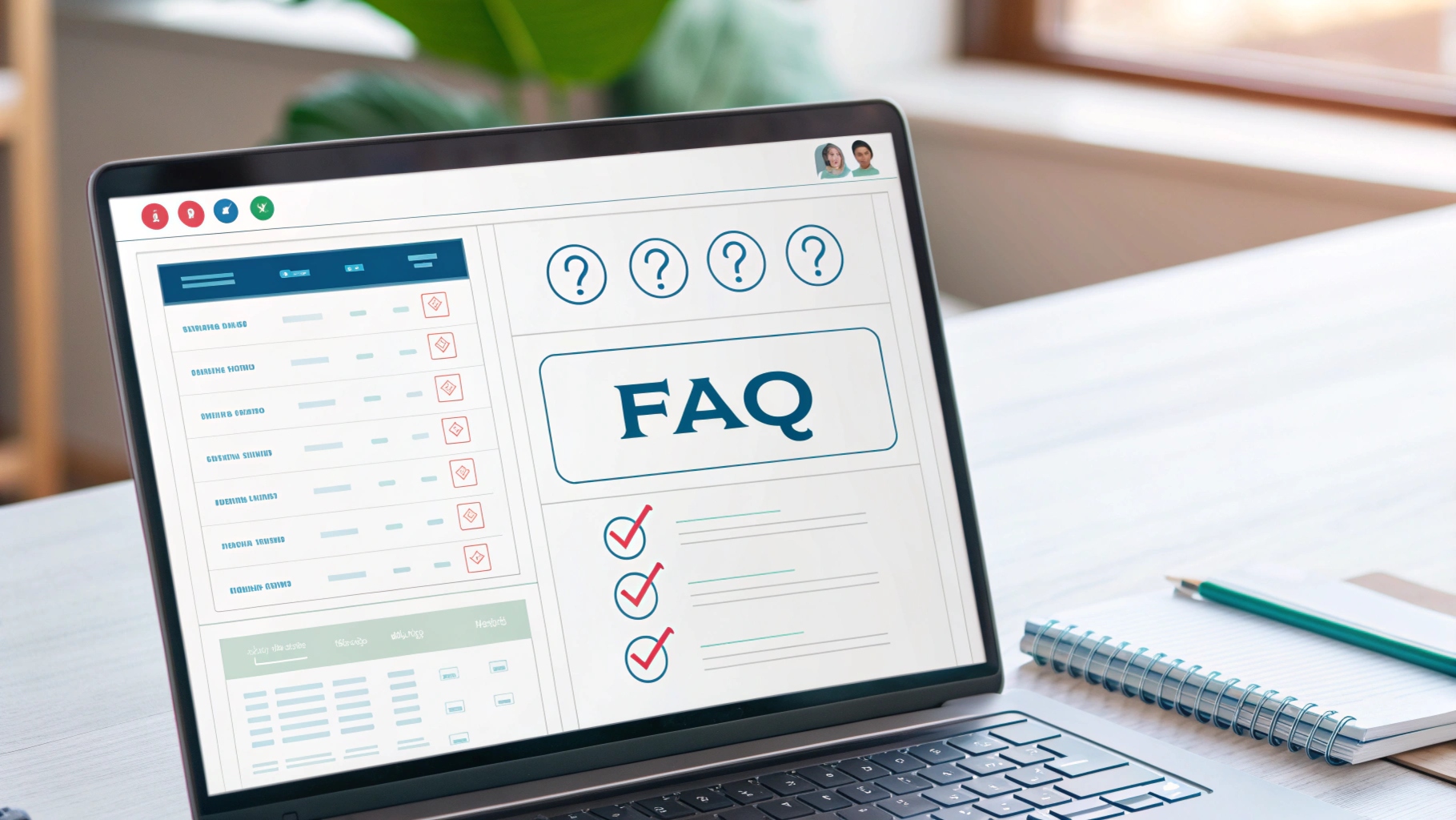
What makes a paint brush handle good for automation?
Handles need to be the same size and shape. Strong materials and smooth finishes are also important. These features help machines work smoothly. Even small changes, like adding grip texture, can improve assembly.
Can eco-friendly materials be used for automated paint brush handles?
Yes, they can! Materials like bamboo and recycled plastics are great. They are strong, eco-friendly, and work well with machines. Many DIY painters like them because they help the planet and still work well.
How do ergonomic designs make paint brush handles better?
Ergonomic designs make painting less tiring and easier to control. Balanced weight and textured grips help a lot. Whether you’re a pro or a DIY painter, comfy handles make painting better.
Are composite materials a good choice for paint brush handles?
Yes, they are! Composites mix the best parts of wood, plastic, and metal. They are strong, light, and flexible. They work well for machines and DIY projects.
Why is a smooth surface finish needed for automation?
Smooth finishes help handles move easily in machines without problems. They also make handles last longer and feel better to use. Smooth handles are great for better production and painting results.